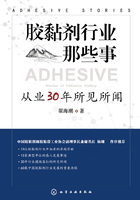
26 “自力—2、自力—4胶”研制背后的故事
20世纪60年代,我国歼击机采用的是有孔蜂窝结构。由于有孔蜂窝结构在应用中暴露出开胶、进水、增重等质量问题,20世纪60年代后期,我国开展了第二代蜂窝结构——无孔蜂窝结构的研究。1968年底至1969年初,保定550厂工程技术人员梅赛亚为了解决直升机尾桨粘接问题,带领工人一起研制成功环氧-丁腈-间苯二胺体系结构胶,并命名为自力-1胶黏剂,意思是突破西方技术封锁、消除中苏关系恶化的影响,自力更生研制出的胶黏剂,但该胶性能不够理想。为了进一步解决有关技术问题,梅赛亚来到航空部621所(北京航空材料研究所)寻求合作,促成了621所、550厂和北京航空学院三个单位的协作(研制新型航空结构胶)。项目主要负责人是621所郑瑞琪和550厂梅赛亚,参加人员有621所赖士洪、北京航空学院李凤德等。研制过程中,郑瑞琪提出了采用二氰二胺潜伏固化剂代替自力-1胶的间苯二胺固化剂,原环氧-丁腈体系不变,并且进行了温湿疲劳、湿热老化等全面性能试验。经过反复试验,环氧-丁腈-二氰二胺体系结构胶研制成功,命名为“自力-2胶”。由于研制成的“自力-2胶”是一种环氧-丁腈-双氰胺型结构胶黏剂,固化时环氧加聚反应无低分子物析出,这种胶黏剂挥发物少,固化后胶层致密无气泡,适用于制造无孔蜂窝结构旋翼,成为我国第一个实用的无孔蜂窝结构胶。
1970年初,郑瑞琪(图片中右者)去了“五七干校”,“自力-2胶”的试产和推广工作落到了621所赖士洪(图片中左者)等人头上。赖士洪首先和550厂梅赛亚、陈义及北京航空学院李凤德到哈尔滨122厂,开展自力-2胶的生产制膜工艺及应用研究工作。试验中,赖士洪发现原来确定的由两个单组分胶黏剂做成复合胶膜的配方和制膜工艺有不少缺陷,胶膜性能偏低,且不稳定,胶膜自黏性大,生产工艺复杂,不易控制,无法满足实际生产要求。在哈尔滨油漆厂转厂生产时,赖士洪对胶膜配方和制膜工艺进行了大胆的改进。当时从122厂到哈尔滨油漆厂交通极其不便,为了尽早解决胶膜技术问题,赖士洪、陈义吃住在油漆厂。他们的工作热情换来了油漆厂负责人毕吉才和吕宝华的信任,于是把原先堆放杂物的仓库安排给赖士洪与550厂陈义住宿,还把实验室的钥匙交给他们。虽然这里条件很差,没有像样的床铺,晚上还要受到不计其数臭虫的攻击,但住宿于此节省了往返两厂之间的时间,还可以日夜坚守在实验室开展试验。赖士洪从配方设计、胶液配制、胶接试片表面处理、试样制备到固化及性能测试均亲自动手。由于技术路线正确,时间也抓得紧,经过一个多月的奋战,终于研制出性能优良,可以一次流延成型制膜的自力-2胶膜。赖士洪最后编制出自力-2胶膜生产工艺说明书,该胶膜在哈尔滨油漆厂正式生产,胶膜提供给122厂开展胶接无孔蜂窝工艺试验以及直升机旋翼大梁和梳形接头粘接试验。
在122厂,为了促进自力-2胶粘接“直-5”飞机旋翼梳形接头的大梁接头能早日开展疲劳振动试验,赖士洪和陈义亲自抬着100多千克重的胶接大梁,从粘接车间送到几百米远的铆接车间厂房振动试验台上,使得试验能如期进行,赢得时间。试验结果表明,采用自力-2胶粘接和螺栓连接的旋翼梳形接头,不但胶层致密,气密性好,而且具有更高的振动疲劳性能。因此,用自力-2胶取代原来有问题的胶粘接旋翼梳形接头就顺理成章了。用自力-2胶粘接的800架“直-5”飞机旋翼比原产品可延寿一年(200飞行小时)。之后,赖士洪又协助122厂在“水轰-5”机上采用自力-2胶开展全胶接试验工作。经过各方面的努力还在运输机上和水上飞机上获得推广应用。全胶接包括运输机机身壁板、地板和整体油箱等的胶接,仅整体油箱一项可减重30kg。
1971年,课题负责人郑瑞琪从“五七干校”回所,继续带领那万才、卢华、萧静芝等从事自力-2胶的推广应用工作,解决了胶黏剂生产中出现的凝胶问题。1972年自力-2胶通过部级鉴定,三机部、石化部和六院联合批复了鉴定书和技术条件。第一副无孔蜂窝旋翼在2964部队通过了全科目飞行试验。自力-2胶在1978年获得全国科学技术大会的表扬。之后,该项成果应用于近千架直升机、运输机等五个机种并获得适航性认证。
在完成了自力-2胶研制和推广应用研究的先期工作以后,赖士洪1971年参加了“150℃无孔蜂窝结构胶黏剂研制”的探索性试验。1972年,赖士洪任课题负责人,当时胶黏剂专业组大部分同志都参与了项目的研制。1973年,赖士洪又开展了适合高温胶性能要求的潜伏固化剂研制工作。他查阅了大量资料,组织人力分头进行几种固化剂合成及相应的配方试验,但未收到预期的综合效果。1974年,通过调研和对有关专利资料进行分析对比,赖士洪确定并具体负责了环氧-聚砜-二氰二胺体系的研究路线,唐发伦和陈倩一起参加了这方面的试验工作。1976年,赖士洪带领课题组完成了自力-4胶实验室阶段研究工作,并组织编写了研制总结,同时制定了技术条件、编写了使用工艺说明书和配制工艺说明书。自力-4胶黏剂是国内第一个不需要浸胶瘤的无孔蜂窝面板胶,简化了蜂窝结构件的生产工序,可显著提高生产效率,避免了大量溶剂的污染,改善了生产条件,并可减轻结构质量。之后,在航空部主持下由601所、621所、625所和沈阳112厂共同组成了“歼-8”飞机无孔蜂窝胶接结构的研究与应用课题组。经过三年的刻苦攻关,赖士洪、唐发伦和邹贤武等在625所进行了三次基本性能和工艺性能的对比试验。最后终于选定了自力-4胶黏剂首先用于“歼-8”飞机副翼无孔蜂窝结构粘接。在此期间,七机部选用了自力-4胶粘接导弹体口盖和弹翼。
1978年,赖士洪负责自力-4胶推广应用研究,重点解决胶黏剂的韧性和制膜方法。之前采用的溶液流延法制备胶膜的工艺方法落后,存在生产效率低、消耗大量溶剂、污染环境和胶膜性能不稳定等问题。为此,他除了查阅大量国内外资料,反复探讨研制方案,还到许多生产塑料薄膜和橡胶制品的工厂及研究所进行深入调研。通过调研和对胶料混合工艺方法的探索试验,已经对挤出制膜方案有了较清晰的思路:①通过溶液共混和减压蒸馏制得无溶剂环氧-聚砜共混物,避免了热熔共混带来的物料不均匀性和烧焦问题;②采用橡胶的混炼工艺解决了坚韧固体共混物与潜伏固化剂的混合问题,克服了在反应釜制备无溶剂胶料易引起爆聚现象;③采用挤出工艺制备胶膜具有生产效率高,胶膜厚度随时可调,产品质量稳定的特点。经过艰苦的摸索,1978年下半年自力-4胶(聚砜改性环氧树脂胶膜,后来改称SY-14胶)研制成功,这是国内第一个采用无溶剂挤出机连续制膜的工艺方法。为胶黏剂在“歼-8”飞机上的推广应用打下了坚实的基础。1979年初,自力-4胶还用于长征三号运载火箭尾翼壁板的蜂窝结构粘接。
1979年,航空部召开选胶会,经过与会各方理性讨论,最终决定选用“自力-4胶”作为“歼-8”飞机无孔蜂窝结构用胶。“自力-4胶”挤出胶膜生产线于20世纪80年代初建成投产,之后赖士洪协助沈阳112厂开展无孔蜂窝结构部件的试制工作,使得无孔蜂窝结构副翼、襟翼、平尾和方向舵部件通过了试飞要求。1984年8月,航空部主持召开了“‘歼-8’飞机无孔蜂窝胶接结构的研究及应用”的鉴定会。“自力-4胶”(SY-14胶)在“歼-8”飞机无孔蜂窝结构上的应用,由于蜂窝芯不用浸胶瘤,单机节省工时172h,直接减重5.85kg,全机减重收益达20kg。这是国内首次采用“自力-4胶”(SY-14胶)成功解决了在高空高速歼击机各个活动舵面上制造无孔蜂窝结构部件的应用问题,达到了国内先进水平。1985年,“自力-4胶”(SY-14胶)荣获航空部科技进步奖二等奖。