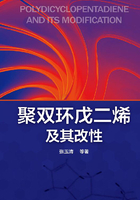
1.3 双环戊二烯聚合工艺
1.3.1 双环戊二烯反应注射成型工艺
双环戊二烯开环中降冰片烯环的张力很大,在催化剂作用下可开环易位聚合(ring-opening metathesis polymerization, ROMP)得到聚双环戊二烯。由于环张力的释放,聚合反应是一个快速的强放热过程,绝热条件下升温可达到160℃。在常温下,催化剂能迅速引发聚合反应,整个反应过程不到5min,交联的聚合物能在模具中固化,整个聚合过程中无副产物产生[8~10]。
图1-1是聚双环戊二烯反应注射成型(PDCPD-RIM)的一般工艺流程图。

图1-1 聚双环戊二烯反应注射成型(PDCPD-RIM)的一般工艺流程图
1—催化剂制备槽;2—活化槽;3—催化剂贮槽;4—混合器头
1.3.2 聚双环戊二烯成型工艺特点
① 反应速度快 DCPD的聚合是按开环易位聚合机理进行,属放热反应,即使不加热,在催化剂的作用下,反应一旦引发,聚合反应也能在瞬间完成。
② 单体黏度低 液态DCPD的黏度很低(约0.3Pa·s),可以在短时间内充满模具,使其特别适合制造大型且形状复杂的制品。
③ 引发聚合时间可调 根据制件的大小,可以控制聚合反应开始的时间,这就使得有充分的时间混合、充模。
目前工业生产中一般采用双组分催化剂。在成型过程中,将原料分为A、B两组分,A组分包括DCPD、助催化剂、调节剂、添加剂,B组分包括DCPD、主催化剂、调节剂、添加剂。精确计量后,将A、B液在混合器头中快速混合均匀,注入预热好的模具,在极短的时间内引发聚合反应,生产出大型的或形状复杂的制件。
1.3.3 聚双环戊二烯成型工艺优点
和其他成型工艺相比,PDCPD-RIM工艺有以下几个优点。
① 计量精度要求较PU-RIM低。
② 原料体系黏度低,可控制诱导期,适合做大型形状复杂制品及增强RIM制品。
③ 加工时不需要脱模剂。
④ 做增强制品时,表面质量好,涂装时无需清洗,也不必打底漆。
⑤ 制品性能优于PU-RIM制品,而设备投资和动力消耗较PU-RIM低。
⑥ 后处理简单,制品出模后无需后固化。
1.3.4 聚双环戊二烯的环境友好性
PDCPD作为一种新型的工程塑料,不仅具有优异的性能,更值得注意的是其不论是加工工艺还是最终的制品,都具有显著的环境友好性。DCPD-RIM单体体系的黏度低、流动性好,成型时不需要很高的锁模压力,而DCPD的聚合反应又属于放热反应,成型时不需要高模温,因此,PDCPD制品的加工过程能耗极低,在原材料制备和成型加工的过程中所需要的能量远远低于聚碳酸酯、ABS、聚丙烯等传统的工程塑料(见图1-2)。据统计,每生产1kg PDCPD制品所需的能量仅为生产同等质量的聚丙烯制品的1/4,聚碳酸酯的1/10。在温室气体排放方面,根据Tenele®提供的数据,2008年每生产1kg PDCPD制品,CO2的排放量约为2.4kg;2015年每生产1kg PDCPD制品,CO2的排放量仅为1kg左右。而采用注射成型工艺,在2008年每生产1kg的ABS或PC,CO2的排放量高达7.2kg,虽然在2015年降低为4.1kg左右,但是总CO2排放量仍是PDCPD制品的4倍(见图1-3)。在回收利用方面PDCPD的环境友好性也同样得以体现,PDCPD制品的废料和废弃物仍可以再次加工粉碎造粒,作为热塑性塑料如PP、PE的填料循环利用。也可以进行裂解生成油气而得到再生利用,PDCPD制品应用于交通运输等领域时,可以减轻车身重量,从而大大提高燃油经济性,节省燃油,降低排放。

图1-2 每千克聚合物生产所消耗的能量
(注:1cal=4.2J)

图1-3 不同加工工艺的温室气体排放量