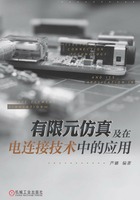
3.2 分析实例——同轴连接器簧片力学性能分析
3.2.1 问题描述
如图3-23、图3-24所示同轴连接器,其主要部件包括插头和插座两部分,插头包括内插针、绝缘体、外插针、保护螺母,插座包括内插孔、绝缘体、外插孔。分析其外圈簧片的应力应变及支反力,簧片材料为铍青铜。

图3-23 同轴连接器示意图

图3-24 同轴连接器
3.2.2 结构分析
同轴连接器外圈簧片为6片,每片之间隔有小槽,其根部可以看做不发生形变,因此可以将整个簧片结构看做6个单独的弧形悬臂梁结构,针对其中的一个进行分析。在建立模型时,单独将簧片进行约束分析,以减少网格数量,提高计算精度。
此结构是力学中的弧形悬臂梁模型,计算时可以根据其端面的挠度计算出簧片变形时的力。实际产品簧片的端部存在一个薄凸台,用悬臂梁公式进行理论计算时将其忽略。
3.2.3 理论计算
弧形悬臂梁模型如图3-25所示,由材料力学得悬臂梁最大挠度公式为


图3-25 计算模型
式中,根据插针、插座配合时簧片端部的变形量,即最大挠度ωmax为0.05mm;E为弹性模量128GPa;l为簧片长度6.9mm;I为悬臂梁相对于其中性轴的惯性矩;F为要求的未知量,因此计算的重点在于求惯性矩。要求通过中性轴的惯性矩,首先要求得截面形心,弧形的形心位置为

式中,R为界面圆环外半径(簧片相对于插头中心的外半径);r为内半径(簧片相对于插头中心的内半径)。簧片的厚度即R-r。
计算Y轴的惯性矩:

取面积微元dA=RdϕdR,则有
可得

由于是6片簧片组成圆周,每片为π/3。dϕ积分的上下限为积分π/3~2π/3,dR上下限为3.1~3.4。图3-26为积分模型。

图3-26 积分模型
根据移轴定理,计算中性轴的惯性矩Iy0为

式中,A为截面面积

由式(3-1)~ 式(3-6),计算结果见表3-1。
表3-1 簧片参数

3.2.4 仿真分析
1. DM建模
在“workbench”下新建静力学模块,点击A3(Geometry)进入DM模块(见图3-27),选择长度为mm。
在“XY Plane”上右键选择“look at”,进入草图界面,并在X轴上创建一条直线,在“Dimensions”下设置其长度为3.1mm,如图3-28所示。
重复上述操作步骤,创建图3-29所示的各条直线,结果如图3-30所示。

图3-27 DM模块

图3-28 在X轴上创建直线

图3-29 创建H2、V11、V13、V3和V4直线

图3-30 完成创建直线
创建完成所有直线后,创建凸台部分。选择Draw模块的Arc by 3 points选项,选择右侧3点,创建一个弧形曲线,如图3-31所示。至此草图截面创建完毕。

图3-31 创建凸台弧线
选择Revolve命令对截面进行旋转拉伸,设置参数如图3-32所示。

图3-32 旋转拉伸角度设置
至此模型创建完毕,如图3-33所示。但为了加载方便,需要对模型进一步完善。具体包括以下几点:

图3-33 旋转拉伸
1)创建一条线,用于加载displacement。在“YZ plane”上右键选择“look at”,进入草图界面,并创建一条直线,长度为3.6mm(见图3-34),将直线投影到体上。选择“Extrude”命令,各参数设置如图3-35所示,点击“Generate”生成。

图3-34 创建投影曲线

图3-35 参数设置
创建结果如图3-36所示,弧形面被分成两部分。
2)将被投影直线分割掉的其余面用merge命令连接起来,如图3-37所示。
3)在前端创建一中点,用于施加集中力。在create栏选择point,进入创建点界面,将各参数设置为如图3-38即可。

图3-36 分成两部分的弧形面

图3-37 merge操作

图3-38 创建中点
2. 添加材料
进入Engineering Data界面,创建一种新的材料铍青铜,并输入材料属性,如图3-39所示。

图3-39 添加材料
3. model操作
(1)赋予材料 在model界面中Geometry下,将铍青铜材料属性赋给模型,如图3-40所示。

图3-40 赋予材料
(2)建立坐标系 为了便于施加力,可以创建一个新的坐标系,如图3-41所示。

图3-41 新建坐标系
(3)网格划分 此处选择自动网格划分,将划分精度设置为100,网格及质量如图3-42所示。
4. 添加约束
需要添加的载荷有两个,一是底端的固定约束,二是弧形面外侧的位移,如图3-43、图3-44所示。

图3-42 网格划分

图3-43 底端添加固定约束

图3-44 添加弧形面外侧位移
5. 求解及结果
在solution下选择Deformation、Equivalent Elastic Stain、Equivalent Stress及Force Reaction,右键solution,选择solve,结果见图3-45、表3-2。

图3-45 仿真结果
表3-2 仿真结果

3.2.5 结果比对
为了与理论计算模型一致,以便于结果比对,新建一个不带凸台的模型,依照3.2.4节方法进行分析,结果见图3-46、表3-3。

图3-46 没有凸台的簧片
表3-3 没有凸台的簧片正向力仿真结果与理论计算比对

结果分析:从仿真结果可以看出,梁上的支反力在X方向上为10-16数量级,与Z方向上的相比可以忽略不计,在Y方向的为0。对于Z方向上的支反力(正向力),理论计算与仿真的绝对误差为0.1298N,相对误差为8.86%,在可以接受的范围内。此处误差来源主要有两个:一是在理论计算时将簧片当做了刚体进行计算,即其横截面完全不变形,但仿真根据实际情况,将簧片结构类似于一个薄片,在实际变形时截面上不同点的形变是不一样的,因此产生的支反力也会相对较大一点;二是仿真时查看的是边上中点的最大力,而在理论计算中,所用的是根据截面性质进行积分求得的平均力,因此结果会有误差。