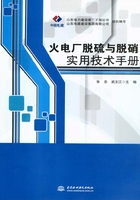
第七章 脱硫系统运行
第一节 脱硫系统设备运行
一、运行管理
脱硫设备的运行、维护及安全管理应符合国家有关规定,业主应组织编写脱硫设备的运行、维护规程。脱硫设备应在满足设计工况的条件下运行,并根据工艺要求,定期对各类设备、电气、自动仪表及(构)建筑物进行检查维护,确保设备长期稳定可靠地运行。脱硫设备在正常运行条件下,各项污染物排放应满足相关的环保规范的规定。
二、运行条件
技术人员、检修人员和运行操作人员必须经过脱硫技术基本原理和工艺流程及操作维护等专门培训,除能进行脱硫设备的正常运行操作外,还能完成脱硫设备事故或紧急状态下人工操作和事故处理。为保证脱硫设备的正常运行,每日应定时对其巡检2次以上,每次巡检人数至少为2人;脱硫剂品质合格,主体工程运行稳定,其燃煤及烟气参数符合脱硫设备的技术条件要求。
三、维护保养
脱硫设备的维护保养应纳入全厂的计划中,制定详细的维护保养规定,维护人员应按规定定期检查、更换或维修必要的部件并做好维护保养记录。
四、安全防护
严格遵守安全操作规程,防电、防火、防辐射、防毒、防滑、防冻、防堵、防腐,保证人身和设备安全。
五、FGD系统启动前工作
参加FGD系统启动时,工作人员应根据专业和岗位分工,配合安装单位做好设备的验收工作。该人员应该经过专门培训并取得相应资格。
脱硫装置在总体安装完毕后,应该对整个脱硫系统进行全面检查和调整,使其能长期安全正常运行。在FGD系统投入运行之前,应对下述系统进行检查。
1.烟气系统启动前检查
(1)烟气系统烟风道准备完毕。(2)烟气设备检查合格,送电。
(3)热控仪器仪表投入,联锁保护投入。
(4)烟道通道挡板门及其附属设备准备完毕。
(5)GGH系统准备完毕。
(6)增压风机及其附属系统准备完毕。(7)检查下述手动阀在如下位置:
1)原烟道疏水阀:关闭。
2)原烟道疏水管冲洗阀:关闭。3)净烟道疏水阀:关闭。
4)净烟道疏水管冲洗阀:关闭。5)增压风机本体排放阀:关闭。2.吸收塔系统启动前检查
(1)各相关内部已清理干净,人孔门、检查孔检查后封闭。
(2)就地仪表工作正常,初始位置正确。
(3)压力、压差、温度、液位、流量、密度、pH计等测量装置完好,并投入。
(4)手动阀、电动阀、调节阀开关灵活,指示准确,盘面显示与就地指示符合。
(5)各设备事故按钮完好。
(6)各设备周围必须清洁,无积油、积水及其他杂物。(7)现场清洁、排水沟通畅,沟盖板齐全。
(8)工艺水系统具备投入条件。(9)供浆系统具备投入条件。
(10)各地坑液位在可控范围内,不在高液位启动。3.转动机械启动前的检查
(1)机械的转动部分均装有防护罩,靠背轮连接牢固。(2)各安全装置齐全良好,事故按钮位置正常。
(3)润滑油系统正常,油标正确清楚,油位计清晰,严密无漏油现象。
(4)轴承温度表齐全良好,指示正确。(5)冷却水通畅,积水斗无堵塞。
(6)风机启动前挡板门调整机构良好,开关灵活,风机如有倒转现象必须停止启动。
(7)烟道无杂物和积水。
(8)现场必须清洁无杂物,照明充足良好。4.电机启动前的检查
(1)电机清洁,周围无妨碍运行的杂物。
(2)接地良好。
(3)靠背轮罩子安装固定。
(4)轴承润滑油色及油位正常。(5)电气系统的检查:
1)变压器声音无异常,三相绕组温度最高相不超过130℃,升温不超过80℃。风机运行方式在自动位置。
2)低压电源开关指示灯指示正确,连接片投入正确。抽屉柜无异常,停电抽屉抽出30mm左右,标识牌正确。
3)UPS柜无故障报警,输出电压220V±3V。旁路柜直
流电压在200~240V之间。
4)火灾报警系统工作正常,无报警。
六、FGD系统启停概述
脱硫装置的启停由运行人员在控制室内操作FGD装置的控制系统来自动进行。FGD装置的停运可分为短时停运(数小时)、短期停运(数日)和长期停运(机组大修);与此相应,FGD装置的启动可分为短时停运后启动、短期停运后启动和长期停运后启动。下面以某一600MW机组为例来介绍烟气脱硫系统的启动与停止。
(一)短时停运后的启动
短时停运后的启动为因故临时停运后的重新启动,停运时间在24h内,系统内所有设备处于热备用状态(各箱罐坑的液位保持正常,搅拌器处于运行状态)。FGD系统投运条件满足后可随时投入运行。
1.短时停运的操作
如果停机数小时,不必使全部FGD装置都停止工作,仅关闭部分设备,应停止运行的设备有:①FGD烟气系统;
②吸收塔循环泵;③氧化风机;④石灰石浆液供给系统。
切换至旁路运行后,FGD装置与烟气隔离,原烟气和净烟气挡板门关闭。
2.短时停运后的启动操作
为尽量缩短启动周朝,某些设备同时启动,以备用方式运行,直到启动程序达到规定步骤才取消这些设备的预备运行方式。
至少两个吸收塔循环泵投入运行后,烟气方可进入系统。为避免电机启动电流大而导致负荷过大,吸收塔循环泵依次启动。
(二)短期停运后的启动
短期停运后的启动为FGD系统因故停运24~72h的重新启动。在短期停运后的启动前,有液位容器的搅拌器处于连续运行状态,其他机械设备处于停用状态。系统启动时需要进行部分系统的恢复工作。
1.短期停运的操作
如果停运需持续数日,则除了上述设备停运外,以下设备也应停运:
(1)除雾器冲洗系统。
(2)石灰石浆液制备系统。(3)石膏脱水系统。
(4)石膏浆液排出泵及石膏溢流浆液泵。(5)工业水系统。
为防止石膏板结,必须及时将石膏仓内积料全部排空。在短时停运和短期停运期间,装置中输送浆液的管线必须
冲洗。在有浆液的容器内,搅拌器维持运行。
2.短期停运后的启动操作
短期停运后,某些停运的设备可同时启动。程控中的各回路及启停过程设有联锁,以确保启动时维持正确顺序。由于各种设备并列启动,启动时间较短。
如果是单个机组的FGD系统启动,系统的启动的步骤为:工艺水泵→工业水泵→除雾器冲洗水系统→两台吸收塔浆液循环泵→氧化风机系统→启动吸收塔石膏排出泵系统→吸收塔浆液供给系统→FGD烟气系统。
如果两台机组的FGD系统同时停运几天,则系统启动时增加石灰石浆液制备系统、石膏脱水系统、废水处理系统3个系统。
注:当两台吸收塔浆液循环泵投入运行后,应尽快将烟气引入FGD系统中。
(三)长期停运后的启动
长期停运后的启动又称为冷态启动。冷态启动为FGD系统的初次启动或FGD系统检修后的重新启动。在冷态启动前,FGD系统内的全部机械设备处于停运状态,所有的箱罐坑等处于无液位状态(无水或无浆液)。
1.长期停运的操作
脱硫系统随机组进行大修,需将吸收塔内浆液由石膏浆液排出泵及吸收塔地坑泵(石膏浆液排出泵因液位低停运后)排到事故浆液罐储存备用,除事故浆液罐搅拌器应运行外,其他浆罐均应排空,其他设备均应停运以备检修。
2.长期停运后的启动操作
FGD装置大修完毕后,应对各个设备、系统进行试运行,试验合格后方可备用。在机组启动前一天,应启动工艺水系统、工业水系统和制浆系统,石灰石浆液箱储备足够的合格的吸收剂;启动事故浆液泵及吸收塔地坑泵(事故浆液泵因液位低自动停运),将事故浆液罐内浆液返回吸收塔内,以确保机
组启动后FGD装置及时投入。有浆液的容器内的搅拌器维持运行。
下面将对长期停运后的启动过程做详细介绍。启动过程涉及的数据参数以某一600MW机组参数为例,不同电厂数据和设备结构尺寸由于设计参数不同会有所不同。
七、FGD系统启动前检查事项
(一)启动前的设备及系统检查
接到启动命令后,岗位值班员应对所属设备作全面详细检查,发现缺陷及时联系检修消除并验收合格。检修后或冷备用的FGD需按以下项目进行检查:
(1)检查全部的检修工作票是否结束,现场是否清理干净。检修工作全部结束,所有设备是否齐全、完好,设备改进后应有试运报告。
(2)现场杂物须清除干净,各通道畅通,照明充足,栏杆楼梯齐全牢固,各沟道畅通,盖板齐全。
(3)烟道、箱、罐、塔、仓及脱水系统各设备的内部清扫干净,无余留物,各人孔门检查后关闭。
(4)DCS投入,各组态参数正确,测量显示及调节动作正常。
(5)就地显示仪表、变送器、传感器工作正常,位置正确。
(6)就地控制盘及所装设备工作良好,指示灯试验合格。(7)机械、电气设备地脚螺栓齐全牢固,防护罩完整,连
接件及紧固件正常;各泵、风机状态良好。
(8)手动阀、电动阀开闭灵活,电动阀开关指示与DCS显示相符。
(9)脱硫系统及相关设备电气保护试验及热控联锁试验正常。
(10)各设备油位正常油质良好,油位计及油面镜清晰完好。
(11)工艺水系统及压缩空气系统已具备向脱硫岛供水、供气条件。
(二)辅机启动检查项目
1.辅机试转注意事项
(1)检修工作结束,具备试转条件,方可通知送上动力电源。
(2)在靠背轮连接前电机先经单独试转,旋转方向正确,试转时应有检修人员在场,运行人员配合检修进行各项操作。
(3)设备检查和试转时,发现问题,须及时提出要求检修消除,凡是增加或改进设备,应有更改报告。
(4)各主要辅机在试转前需进行单项联锁保护试验正常。(5)当接到电气人员告知设备已送电后,方可启动辅机。(6)启动前表盘上应有专人监视辅机启动电流和启动时
间,当启动电流及启动时间超过规定值时,应停止该辅机。
(7)辅机小修后试转时间不少于4h,大修后试转时间不
少于8h。
(8)辅机试转完毕后,应将结果记录于运行日志中。2.转动机械检查通则
(1)各设备的油质良好,油位计及油面镜清晰完好。各油箱油位应在正常范围以内电加热器应完好,油过滤器安装正确,切换灵活。
(2)检查并投入设备的冷却水、密封水,确认管道畅通无阻,水量正常。
(3)联轴器连接牢固,旋转灵活无卡涩,地脚螺丝紧固,保护罩安装完整、牢固。
(4)转动机械周围应清洁,无积油、积水及其他杂物。(5)电动机绝缘合格,电源线、接地线连接良好,旋转方
向正确。电流表、启/停开关指示灯应完好,电流表应标有额定电流红线。
(6)轴承及电动机线圈温度测量装置完好、可靠。
(7)各冷油器和冷却风机进、出口管路畅通,连接牢固。(8)各传动皮带轮连接牢固,皮带无打滑、跑偏现象。(9)各转动机械事故按钮完好并加盖。
(三)启动前各设备的检查
1.泵的检查
(1)各泵机械密封装置完好,无泄漏。(2)泵吸入口滤网清洁无杂物堵塞。(3)各泵轴承油杯应有足够润滑油。(4)各电源线、接地线应连接良好。
(5)离心泵启动前必须有足够的液位,其入口阀应全开。若滤网被石膏浆液或其他杂物堵塞,则滤网压降增大并有报警,此时应停止该泵运行并清洗滤网。另外泵出口阀未开不允许长时间运行水泵。
2.烟气系统及挡板密封系统的检查
(1)检查脱硫装置进、出口烟气挡板和旁路烟气挡板是否安装完好,其旁路烟气挡板应开启,净烟气挡板及原烟气挡板应严密关闭。
(2)各挡板电动执行装置应完好,连杆、拐臂连接牢固,在就地用手摇各挡板应开关灵活,无卡涩现象,挡板开关位置指示正确,并处于“远控”位置。
(3)密封风机外形完好,靠背轮连接牢固,旋转灵活,无卡涩现象,地脚螺丝牢固,保护罩完整牢固。
(4)电加热装置完好并处于停运状态。
(5)各挡板密封装置完好,密封管道畅通。(6)各膨胀节应完好,安装牢固,膨胀自由。(7)烟道内防腐层应完好无脱落。
3.箱、罐、地坑以及吸收塔的检查
(1)各箱、罐、地坑及吸收塔的外形完整无变形,各焊接处焊接牢固,各管道膨胀自由。
(2)各箱、罐、地坑及吸收塔的衬胶完整无老化、无腐蚀,且衬胶与塔壁粘结牢固无起泡处。
(3)吸收塔搅拌器、氧化空气管及冲洗水管连接完好,且其出口无结垢和异物堵塞。
(4)吸收塔各层喷嘴排列整齐,连接牢固。各喷嘴完好无损、无堵塞。各喷嘴连接管道无破裂、老化、腐蚀。
(5)石灰石浆液箱内的折流板安装牢固、无磨损、无腐蚀。
(6)对烟道及吸收塔内部检查时要确保烟气不会进入,各烟气挡板不进行操作。
(7)对各种罐体内部进行检查时要确保内部含氧量足够,检查完毕后,需关好人孔门。
4.润滑油系统的检查
(1)油循环系统所有管接头、阀门、油泵的填料盖等易漏处密封良好。
(2)导向轴承、支撑轴承润滑油油量充足,油位、油温正常。
(3)油循环系统冷油器冷却水应充足、畅通。
(4)试转支撑轴承、导向轴承、摆线减速机的油泵,要求启、停良好,转向正确,电机温度正常。
5.搅拌器的检查
(1)各箱、罐、地坑及吸收塔搅拌器叶片安装牢固、无磨损、无腐蚀。
(2)吸收塔各侧入式搅拌器安装下倾角应正确。
(3)各箱、罐、地坑顶进式搅拌器应垂直安装,连接轴连接牢固且同心。
(4)各搅拌器轴封安装完好,冲洗水管道畅通无杂物堵塞。
6.石灰石(石膏)旋流器的检查
(1)各个旋流子外形完好、安装正确,漏斗无堵塞,旋流子的手动门应关闭。
(2)各旋流器底流出口应无磨损。(3)各旋流器溢流应畅通无堵塞。7.增压风机的检查
(1)检查风机进出口烟道已经清理干净。
(2)检查轴承箱的油位应正常,油量不足时应加油。(3)检查增压风机的热工检测仪表接线完整投入。(4)用手动、DCS远方操作增压风机静叶调节机构,检
查开度与指示值是否相符,动作是否灵活。
(5)增压风机轴承冷却风机联锁跳闸试验正常。(6)紧急事故按钮正常。
8.氧化风机的检查
(1)氧化风机本体和电机外形正常,空气管道消音器、入口过滤器清洁无杂物。
(2)氧化风机隔音罩完好,排风扇启停正常。(3)润滑油系统无异常。
(4)将风机电源开关置于试验位置,合上控制电源,检查开关无异后,就地分、合闸一次,其开关动作应正常,事故按钮试验正常。
9.除雾器的检查与试验
(1)除雾器连接牢固无堵塞,且完好无老化、无腐蚀、无积浆或积灰。
(2)除雾器冲洗喷嘴安装牢固、齐全,各喷嘴喷射方向正确,无堵塞。
10.浆液制备系统的检查
(1)冷却水管应畅通,冷油器外形正常,冷却水适量,无漏油、漏水现象。
(2)减速机、传动装置、筒体螺栓及大齿轮连接螺栓牢固,进/出口导管法兰等螺栓应紧固、完整。
(3)湿磨机周围应无积浆、杂物,人孔门应严密关闭。(4)湿磨机检修完毕,筒体内应按规定补充一定量钢球。(5)大齿轮润滑油系统各油、气管道,支吊架完好,油
管、气管无堵塞、漏气、漏油等现象,大小齿轮内已加入了足够的润滑油。
(6)就地操作盘上的各表计、指示灯应完好齐全。
(7)就地盘内的各设备应整洁,油泵电机、空压机电机及电源线完好。空压机皮带完好,松紧适当,空压机出口门应开启,启动前应开启储气罐的放水门疏水,空气入口滤网应完好无堵塞。
(8)湿磨机出口格筛完好,清洁、无杂物堵塞,其杂物斗内应无杂物和积浆。
(9)湿磨机低油压保护试验正常。11.称重皮带给料机的检查
(1)称重皮带给料机进、出料口应畅通。
(2)就地称重测量装置应完好准确,并已校核,
(3)皮带主轮、尾轮应安装良好,托辊齐全。
(4)皮带无破裂、无损伤、不打滑、接头完好,皮带上应无杂物。
12.石灰石输送系统的检查(1)石灰石储仓的检查:
1)石灰石储仓的进料管应畅通、无磨损。
2)石灰石储仓除尘器的振动装置及除尘风机应完好,滤袋无破损和积灰。
3)石灰石储仓内应无水源进入。
4)石灰石储仓料位测量显示应准确。
5)检查斗式提升机的竖井内应无障碍物,底部无石灰石堆积。
6)斗与链条连接应完好、牢固。各料斗外形正常,无磨损和变形。
7)调紧装置应灵活,试转提升机应正常(无卡涩),链条无掉链现象,且接头连接牢固。
8)斗式提升机驱动装置安装牢固,链条无破裂损伤。(2)振动给料机及电磁除铁器的检查:
1)卸料斗格栅应完好,格栅上应无杂物。
2)振动给料机的机座及减振弹簧应完好、牢固,各支架、螺栓连接应无裂纹和松动。
3)振动给料机的进、出口应畅通,无严重磨损。
4)振动装置应完好,试转振动给料机应正常,给料方向正确。
(3)布袋除尘器的检查:
1)除尘器滤袋应完好、清洁、无积灰,空气管道应畅通、无堵塞。
2)检查就地盘的开关、指示灯、标志应齐全且准确。3)试投除尘器工作正常后,停止其运行。
13.石膏脱水系统的检查
(1)真空皮带脱水机滤布、驱动皮带、滑道无偏斜,各支架牢固,皮带上无剩余物,皮带张紧适当。
(2)皮带和滤布托辊转动自如,无卡涩现象。
(3)皮带主轮和尾轮完好,轮与带之间无异物。皮带和滤布应完好,无划伤或抽丝现象。
(4)真空皮带脱水机下料处滤布刮刀安装位置适当,下料口清理干净。
(5)真空皮带脱水机进浆分配管畅通、无堵塞。
(6)滤布冲洗水、滤饼冲洗水、皮带润滑水,真空室密封水管路畅通且无堵塞;真空室与皮带之间间隙适当,其管路畅通,密封严密。
(7)真空泵,滤布冲洗水泵安装完好,管路畅通。(8)工艺水至真空泵密封水管路畅通。
(9)检查纠偏气动执行机构,检查托辊的位移方向正确。(10)检查并确认真空皮带脱水机变频器工作正常,将控
制方式置远方。
(11)调整真空室高度适当,其调整装置应灵活,密封水密封良好,滑道密封水应适当。
(12)试转脱水机,检查其走带正常,张紧度适当,将走带速度逐渐增加至100%,检查运转声音正常,确认皮带及滤布位置正常后,停止其运转。
14.废水处理系统的检查(1)泵启动前的检查:
1)启动前检查确认机械及电气检修工作已结束,工作票注销。
2)检查水泵及电动机周围有无杂物,地脚螺丝连接牢固,电源接线及电动机接地线良好。
3)检修后投运应检查泵体有无油脂或污垢。4)传动箱内注入适量的机油。
5)安全补油阀组和泵腔内注入适量的变压器油。6)柱塞工作时,不得有任何卡涩阻滞现象。
7)7天未运行的电动机,启动前应测量电动机绝缘,若绝缘不合格禁止启动。
8)满足厂用电动机运行规程中启动前检查的相关条文。(2)加药系统的检查:
1)系统供电电源正常。
2)碱加药系统、酸加药系统、有机硫加药系统、混凝剂加药系统、絮凝剂加药系统无检修工作,各阀门、法兰无泄漏。
3)工业水系统运行正常。
4)各系统手动阀门均处于关闭状态。(3)废水处理系统的检查:
1)系统电源应供电正常。
2)系统应无检修工作,各阀门、法兰无泄漏。3)工业水系统运行正常。
4)各手动门均处于关闭状态。
5)各计量箱内有足够的药液,其浓度在规定范围内。
(四)启动前的配送电及试验
在以上设备及系统检查的基础上,联系有关人员将控制电源、设备电源送上,并进行启动前的相关试验。
(1)DCS投入,各系统仪用电源投入,检查各组态参数是否正确,测量显示及调节动作是否正常。
(2)就地显示仪表、变送器、传感器工作正常,位置正确。
(3)就地控制盘及所装设备工作良好,指示灯试验合格。(4)手动阀、电动阀开闭灵活,电动阀指示与DCS显示
相符。
(5)开启吸收塔通风阀。
(6)FGD出入口挡板门、旁路挡板门保护试验正常。(7)增压风机保护试验正常。
(8)氧化风机保护试验正常。
(9)脱硫岛内的仪用空气检查。
八、FGD系统启动前的准备
启动FGD系统前,先进行压缩空气系统启动、工艺水箱的注水和石灰石料仓的上料工作,启动FGD的公用设备,然后按步序启动FGD各系统。
(一)压缩空气系统启动
脱硫仪用压缩空气由仪用压缩空气系统提供。仪用压缩空气系统包括一个仪用空气罐用来对FGD的气动执行机构、CEMS吹扫等用气点供气。启动FGD前需核实仪用压缩空气系统启动,压缩空气储罐的压力达到0.75MPa。
(二)工艺水箱注水和石灰石仓上料
脱硫设备工艺水箱补水通常有两路水源:一路从机组开式冷却水管网系统引接;一路从水源地至消防服务用水母管上引接。进水总管路上设置电动调整门,检查工艺水箱正常后联系值长投入脱硫工艺水。
1.工艺水箱手动注水步骤
(1)在工艺水箱注水前,注意阀门的位置。
(2)对工艺水箱冲洗,确认出水清洁,关闭工艺水箱底部排放门。
(3)打开工艺水箱补水电动调整门。
(4)待工艺水箱液位达到正常范围后投入工艺水箱液位自动控制。
2.石灰石上料的启动允许条件
正常运行后,斗式提升机运行反馈后,才允许启动卸料振动给料机。
3.石灰石上料操作步骤
石灰石卸料斗下部的手动闸阀,在正常情况下常开,只有在卸料振动给料机需要检修时关闭。需要加料时按以下逻辑启动石灰石加料系统。
(1)开启石灰石仓顶收尘系统,则可以由中控发出仓顶收尘系统启动指令。
(2)启动斗式提升机。
(3)斗式提升机运行反馈后空载运行2min。(4)启动振动给料机皮带机。
(5)将合格的石灰石卸至卸料斗。(6)上料至正常料位。
(三)工艺水系统启动
首先对所有水泵按照启动前检查标准进行就地检查,就地检查完毕后进行水泵启动。选择一台运行泵和一台备用泵。
将工艺水箱液位自动控制系统投入,待设备启动完毕后,开启各用户阀。工艺水泵启动步骤为:
(1)开启工艺水泵入口门。(2)启动工艺水泵。
(四)吸收塔注液
1.吸收塔注液需具备的条件
(1)工艺水系统管道、支吊架完整,无异常现象。
(2)吸收塔内部已清理干净,无残留杂物,人孔门检查后关闭。
(3)吸收塔就地仪表工作正常,初始位置正确。(4)吸收塔所有冲洗水管关闭。
(5)吸收塔内部衬胶保养结束(如果需要)。(6)吸收塔底部浆液排放门关闭。
(7)吸收塔的梯子、平台完整,通道畅通。(8)吸收塔底部人孔门关闭。
(9)吸收塔液位计投入。
(10)吸收塔区排水坑防腐完毕或清理完毕,具备上水条件。
(11)工艺水系统具备投入条件。
(12)现场清洁,排水沟畅通,沟盖板齐全。(13)有临时排水措施。
2.吸收塔浆液池注水步骤
初次启动时的吸收塔注水:初次启动时,利用除雾器冲洗水进行注水,打开一期除雾器冲洗水总门,采用除雾器冲洗子程序逐层进行冲洗并对吸收塔进行注水,当吸收塔液位达到
9.3m时,停止注水。
检修完毕后的吸收塔注液:导通事故浆液箱到吸收塔的浆液输送管路,启动事故浆液泵,用事故浆液泵将事故浆液箱中的浆液通过浆液管线打入吸收塔中进行注液,当吸收塔液位达到2.8m时,按顺序启动吸收塔的3个搅拌器,检查搅拌器运行正常,当吸收塔液位达到9.3m时,停止事故浆液泵。
注:不同电厂在启动时数据略有不同。
(五)事故浆液泵启动
1.事故浆液泵启动条件
(1)事故浆液箱液位高于1.0m。
(2)事故浆液泵管道冲洗门关闭。(3)事故浆液泵入口门开启。
(4)事故浆液泵出口门关闭。
(5)事故浆液泵管道排放门关闭。(6)事故浆液泵无电气故障。
2.事故浆液泵顺控启动步序(1)关闭事故浆液泵出口门。(2)关闭事故浆液泵管道冲洗门。(3)开启事故浆液泵入口门。(4)开启事故浆液泵管道冲洗门。
(5)等待5s,关闭事故浆液泵管道冲洗门。(6)启动事故浆液泵。
(7)等待5s,开启事故浆液泵出口门。
(六)吸收塔搅拌器启动
按照搅拌器启动要求对搅拌器进行检查。在吸收塔搅拌器启动条件满足后(吸收塔液位高于2.8m),按顺序冲洗并启动吸收塔的4个搅拌器,检查搅拌器运行正常。
(七)滤布冲洗水箱、滤饼冲洗水箱注水
采用工艺水对滤布及滤饼冲洗水箱进行注水:导通工艺水泵至滤布及滤饼冲洗水箱的管路,启动工艺水泵,水箱注水至正常水位时,关闭水箱补水阀,水箱处于冷备用状态。
(八)湿磨机浆液循环箱注水
湿磨机浆液循环箱注水通过稀释水管道注入:导通工艺水至湿磨机浆液循环箱的管路,启动工艺水泵向磨机浆液循环箱注水,液位在0.6m时启动搅拌器,液位到1.2m的液位后,关闭湿磨机稀释水电动调整门,注水完毕后,系统处于冷备用状态。
(九)石灰石浆液箱注石灰石浆液
在石灰石浆液制备系统制出合格浆液后对石灰石浆液箱进行注液,石灰石浆液箱注液至0.8m以上时,启动搅拌器运行,将石灰石浆液箱注入到6.2m的液位后停止石灰石浆液制备系统,石灰石浆液箱系统处于热备用状态。
本系统状态为系统已经冲洗完毕,具备石灰石浆液进料条件。
(十)吸收塔区排水坑的启用
按要求检查吸收塔区排水坑的搅拌器及排水坑泵,检查各阀门开关状态正常,使吸收塔区排水坑内浆液能够送往吸收塔。
当吸收塔区排水坑泵满足启动条件时,需要向吸收塔排放浆液,可以由操作人员启动排水坑泵向吸收塔排放浆液,也可以在到达自启动液位后,排水坑泵自动启动。
(十一)制浆区排水坑泵的启用
按要求检查浆液制备区排水坑的搅拌器及排水坑泵,检查各阀门开关状态正常,使浆液制备区排水坑内浆液能够送往石灰石浆液箱。
石灰石浆液制备区排水坑泵满足启动条件时,可以由操作人员启动,也可以在到达自启动液位后,排水坑泵自动启动。
(十二)烟气在线监测系统的投运
投入FGD出入口的烟气在线监测系统(配合热工)。
九、FGD装置正常启动
当锅炉运行稳定,没有油枪投用,电除尘器已投运,对于600MW机组,机组负荷大于180MW,电除尘器出口的烟气
含尘浓度低于150mg/Nm3,FGD进口烟气温度低于160℃时,
FGD装置系统可投入运行。
按照以下的启动步序对FGD系统的设备进行启动。
注:FGD装置系统启动前应确认吸收塔的通气阀处于开启状态。
(一)石灰石浆液制备系统的启动
1.石灰石浆液制备系统启动前的检查
在石灰石浆液制备系统启动前应先把石灰石储仓上好料,打开称重皮带给料机给料门,程控启动石灰石浆液制备系统。启动前操作员应检查确认石灰石储仓的阀门状态。
在湿磨机启动条件具备后,启动湿磨机顺控启动程序。在湿磨机系统启动后,操作员应将称重皮带给料机的出力给定到设计值,对石灰石浆液箱进行注液;如果石灰石浆液不合格,则要对磨机系统进行调整直至石灰石浆液合格。
2.湿磨机浆液循环泵的启动
对要运行泵进行就地检查,接通泵的机械密封水,设备检查完毕后,顺控启动湿磨机浆液循环泵。
3.湿磨机浆液循环泵启动条件
(1)湿磨机浆液循环箱液位高于1.0m。(2)该泵无电气故障。
4.湿磨机浆液循环泵顺控启动步骤(1)关闭湿磨浆液泵放空阀和冲洗阀。
(2)放空阀和冲洗阀关到位打开湿磨浆液泵入口阀。
(3)湿磨浆液泵入口阀开到位反馈后延时5s,打开湿磨浆液泵。
(4)湿磨浆液泵开启反馈后,打开湿磨浆液泵出口阀。5.湿磨机的启动
湿磨机的启动步骤为:
1号低压油泵为主油泵,2号油泵为备用油泵,在球磨机开启前首先开启1号低压油泵和球磨机空压机。油站加热器和冷却器可以单独远控操作,也可以根据温度自动调节。
(1)手动启动1号低压油泵。(2)手动启动高压油泵。
(3)接收到高压油泵反馈的主轴浮起开信号后启动球磨机主电机。
(4)球磨机主电机运行信号返回后向球磨机控制箱发出球磨机运行信号,同时发出喷射风阀启动指令。
(5)磨机运行后,开启喷油装置。
(6)喷油装置运行15min后,高压油泵自动停止,由低压油泵提供润滑。
6.称重皮带给料机的启动
球磨机启动后应启动球磨机给料系统。球磨机系统运行反馈后延时2min启动皮带称重机。
(二)除雾器冲洗系统启动
1.除雾器冲洗系统启动前的检查
在除雾器冲洗系统启动前,应对系统内的阀门状态及设备仪表进行检查,确保冲洗系统内各阀门及设备仪表正常可用。
2.除雾器冲洗系统启动
(1)除雾器冲洗水泵启动程序。采用3台除雾器冲洗水泵,两用一备。只有这些水泵的入口手动门处于开启状态,并且工艺水箱液位满足要求,无电气故障,这些水泵才允许启动和投入备用状态。
除雾器冲洗水泵启动程序:
1)手动打开除雾器冲洗水泵入口阀门。2)启动除雾器冲洗水泵。
(2)吸收塔除雾器冲洗顺序控制启动。除雾器冲洗电动阀启动顺序:
1)吸收塔除雾器入口总阀开到位,开吸收塔一级除雾器
上层6号电动阀。
2)吸收塔除雾器上层6号电动阀开到位后,延时60s。3)关吸收塔除雾器上层6号电动阀,开吸收塔除雾器上
层7号电动阀。
4)吸收塔除雾器上层7号电动阀开到位,延时60s。5)关吸收塔除雾器上层7号电动阀,开吸收塔除雾器上
层8号电动阀。
6)关吸收塔除雾器上层10号电动阀。
按上述顺序运行完后,开始按上述顺序运行一级除雾器下层冲洗,一级除雾器下层运行完后按上述顺序运行二级除雾器冲洗;运行完后如果吸收塔液位没有达到9.3m,继续从头开始执行冲洗顺序。
一级除雾器下层喷淋阀门:AA001,2,3,4,5。一级除雾器上层喷淋阀门:6,7,8,9,10。
二级除雾器下层喷淋阀门:11,12,13,14,15。(三)吸收塔浆液循环泵启动
1.吸收塔浆液循环泵启动前的检查
按照吸收塔浆液循环泵启动要求对循环泵进行检查,接通吸收塔浆液循环泵的减速机油系统冷却水及机械密封水。
2.吸收塔浆液循环泵启动条件吸收塔浆液循环泵启动条件:
(1)浆液循环泵入口阀门开到位反馈延时5s。
(2)吸收塔液位高于7.6m。
(3)循环泵放空阀门关到位。(4)循环泵冲洗阀门关到位。3.吸收塔浆液循环泵的顺控启动
在吸收塔浆液循环泵启动条件满足后,依次启动两台吸收塔浆液循环泵顺控启动程序。
(1)待第一台循环泵启动完毕吸收塔液位恢复正常后,方可启动第二台循环泵。
(2)电机的启动电流相当大,两台泵同时开时,电气负荷会不够。
(3)在FGD系统启动完毕后,视吸收塔通烟气后脱硫效率的情况确定是否需要启动第三台吸收塔浆液循环泵。对于未启动的吸收塔浆液循环泵,将泵设为备用。设备启动完毕后,检查设备运行情况。
吸收塔浆液循环泵顺控启动顺序:浆液循环泵具备启动条件后,关闭放空和冲洗门,放空和冲洗门关到位后打开循环泵进口阀,循环泵进口阀全开,延时60s;启动浆液循环泵,循环泵运行有反馈信号,则启动成功,否则发出循环泵启动超时报警。
注:开启同一台泵时,应有30min间隔(6kV电机要求),来保证没有频繁启动(电机在冷态)。当电机长时间运行后,(跳泵后)可以立即启动(电机在热态)。
(四)氧化风机启动
1.氧化风机启动前的检查
按照氧化风机启动要求对氧化风机进行检查,确认各阀门启动前状态。接通氧化风机冷却水。
2.氧化风机的启动条件
氧化风机必须全部具备下列条件后,才能启动。(1)吸收塔液位大于4m。
(2)氧化风机放空阀门开到位。
(3)氧化风机电机定子温度小于105℃。(4)氧化风机电机轴承温度小于80℃。(5)氧化风机轴承温度小于85℃。
3.氧化风机的顺控启动
每台氧化风机可以满足一台吸收塔100%BMCR工况。设备启动完毕后,检查设备运行情况。
氧化风机系统具备启动条件后,按照下列程序启动氧化风机。
(1)打开氧化风机放空门。
(2)氧化风机放空门开到位后启动氧化风机。
(3)氧化风机运行反馈后延时2min,打开氧化空气入吸收塔电动阀门。
(4)氧化空气入吸收塔电动阀门开到位反馈后延时1min,关闭氧化风机放空阀。
(五)吸收塔石膏排出泵的启动
1.吸收塔石膏排出泵启动前的检查
按照石膏排出泵启动要求对石膏排出泵及管道进行检查,确认各阀门启动前状态。接通石膏排出泵的机械密封水。
2.吸收塔石膏排出泵启动条件
(1)石膏浆液排出泵入口电动阀门开到位。
(2)石膏旋流器入口电动阀门开到位且石膏旋流器入口手动门开,或石膏浆液排出泵至事故浆液槽手动阀门开到位,或石膏浆液排出泵返回吸收塔电动阀门开到位且返回吸收塔手动阀门开。
(3)备用石膏排出泵出口门关到位。
(4)以上条件全部具备石膏浆液排出泵才允许启动。3.吸收塔石膏排出泵顺控启动
石膏排放系统启动程序如下:
(1)关石膏浆液排出泵冲洗阀门、放空阀门。
(2)冲洗阀门、放空阀门关到位,打开石膏浆液排出泵入口阀门。
(3)石膏浆液排出泵入口阀门开到位反馈后,延时5s,启动石膏浆液排出泵。
(4)石膏浆液排出泵运行反馈后,延时1s,开启石膏浆液排出泵出口阀门。
(六)吸收塔浆液供给系统启动
1.吸收塔浆液供给系统启动前检查
在石灰石浆液箱浆液位正常并确认磨机系统处于热备用后,可以启动石灰石浆液供给系统。
对要运行泵进行就地检查,接通泵的机械密封水,设备检查完毕,确认各阀门启动前状态后,顺控启动石灰石浆液泵。
2.石灰石浆液泵启动条件
(1)石灰石浆液输送泵入口阀门开到位。(2)备用石灰石浆液输送泵出口门关到位。
以上条件全部具备,石灰石浆液输送泵才允许启动。3.石灰石浆液泵的顺控启动
石灰石浆液输送泵启动程序如下:
(1)关闭石灰石浆液输送泵放空阀和冲洗阀。
(2)放空阀和冲洗阀关到位反馈后,打开石灰石浆液输送泵入口阀门。
(3)入口阀门开到位反馈后,延时5s,启动石灰石浆液泵。
(4)石灰石浆液泵运行反馈后,延时1s,打开石灰石浆液泵出口阀门。
4.吸收塔浆液供给系统启动条件(1)任一石灰石浆液泵在运行。
(2)吸收塔液位小于9.3m。
(3)石灰石浆液箱液位大于0.8m。
(4)石灰石浆液浓度大于20%。
(5)吸收塔供浆系统管道冲洗门关闭。5.吸收塔浆液供给系统顺控启动
吸收塔浆液供给系统顺控启动步骤为:(1)关闭吸收塔供浆系统管道冲洗门。(2)开启吸收塔供浆系统入口电动门。
(3)等待30s,开启吸收塔供浆系统电动调整门,并投自动。
(七)FGD烟气系统启动
1.FGD烟气系统启动前检查
在烟气系统启动前,应对烟气系统的设备及阀门状态进行检查,确认各阀门启动前状态。
2.增压风机启动条件
只有全部具备以下条件时,增压风机才能启动。(1)增压风机1号或2号冷却风机运行反馈。(2)烟气出口挡板开到位反馈。
(3)烟气入口挡板开到位反馈。(4)烟气旁路挡板开到位反馈。(5)增压风机叶片关闭。
(6)三台循环泵中至少有两台循环泵运行反馈。(7)增压风机轴承温度低于80℃。
(8)增压风机电机轴承温度低于85℃。(9)增压风机电机定子温度低于110℃。3.增压风机的启动步骤
(1)检查FGD具备通烟气条件。(2)检查增压风机启动条件满足。
(3)检查增压风机润滑油泵、冷却风机已正常投入运行。(4)手动试验增压风机静叶挡板全开、全关正常。
(5)启动增压风机运行。
(6)慢关烟气旁路挡板,同时手动开大增压风机入口静叶,保持原烟气挡板前压力。
(7)当旁路挡板全关后,将增压风机入口静叶投自动,设
定压力为-100~+100Pa。
(8)检查系统运行正常后,汇报值长FGD正常投运。
(八)石膏脱水系统的启动
石膏脱水系统的运行取决于石膏浆液浓度。当石膏浆液密度不到设定值时,石膏脱水系统处于热态备用状态;当石膏浆液密度达到设定值时,并满足启动条件后,投入石膏脱水系统。按照真空皮带脱水机启动要求对真空皮带脱水机进行检查。
1.石膏旋流器的启动
在石膏旋流器启动前,对系统内阀门状态进行检查确认,投入石膏旋流器旋流子。
注意事项如下:
(1)石膏浆液排出泵任一台已启动,石膏浆液总管密度大于1150kg/m3,且真空皮带脱水系统已运行,且真空泵已运行,联锁打开去旋流器入口电动阀门,关闭石膏浆液排出泵返回吸收塔电动阀门。
(2)石膏浆液排放泵任一台已启动,石膏浆液总管密度小于1100kg/m3持续10s,或真空皮带脱水系统已停止,或真空泵已停止,联锁打开石膏浆液排出泵返回吸收塔电动阀门,联锁关闭去旋流器入口电动阀门。
2.真空皮带脱水机的启动条件
汽水分离器至滤液池连通且在液面下。
3.真空皮带脱水机的启动
真空皮带脱水机系统开启程序如下:(1)开启滤布冲洗水泵。
(2)延时5s。
(3)打开真空泵入口密封水阀门。
(4)启动皮带脱水机(以25Hz的频率运行)。
(5)延时3s。(6)延时10s。
(7)启动真空泵。
滤饼冲洗水泵在需要冲洗时启动,滤饼冲洗水泵的启停顺序为:
(1)手动打开滤饼冲洗水泵入口阀门。(2)启动滤饼冲洗水泵。
(九)废水处理系统的启动
1.脱硫废水处理系统启动条件(1)已提供稳定电源。
(2)已提供水质清洁、水量水压稳定的工艺水。(3)电气设备、仪控仪表完好。
(4)手动、电动阀门启闭正常。
(5)药剂已配制,并注入药剂罐内。
(6)使用油封或油冷却、润滑的设备油位正常。2.脱硫废水处理系统启动的准备
(1)关闭脱硫废水处理系统内的箱体储罐的全部放泄阀或排空阀。
(2)向处理系统内的中和箱、沉降箱、絮凝箱、澄清器、出水箱内注入清洁工艺水。其中向中和箱、沉降箱、絮凝箱注入清洁水,可通过开启澄清器冲洗水管线阀门,向澄清器内注入工艺水;同时利用污泥循环泵回流将三联箱内充满废水;出水箱内的清洁水来源于澄清器溢流出水。
(3)接通pH计、污泥浓度计、浊度计电源,检查就地显示与远程传输信号是否一致,确定设备可以正常工作。
3.脱硫废水处理系统的启动(1)待处理废水进入处理系统。
(2)现有自控系统设计进水流量大于等于2m3/h时系统才可以启动,此最小流量参数可根据需要在参数设定栏目中更改。手动操作时无需考虑。
按以下次序开启系统装置:中和箱搅拌器→沉降箱搅拌器→絮凝箱搅拌器→澄清器刮泥机→出水箱搅拌器。
按以下次序开启加药计量泵:NaOH计量泵→混凝剂计量泵→有机硫计量泵→絮凝剂计量泵。
计量泵的频率可以通过自控系统给定,或由手工给定。加药系统开始工作后,pH曲线会出现反复属正常现象,在大约2h内曲线会逐渐趋向平稳。
4.脱硫废水处理系统短期停运的重启(1)检查药剂是否失效。
(2)开启加药系统计量泵进出口阀门。
(3)清洁pH电极后,接通pH电极电源,污泥浓度计电源,浊度计电源。
(4)脱硫废水系统短期停运重启完成,操作参考脱硫废水处理系统的启动。
5.脱硫废水处理系统长期停运后的重启
(1)清洗污泥浓度计表面,注意保护光电触点不可刮伤;清洗完毕后安装。
(2)清洗浊度计表面,注意保护光电触点不可刮伤;清洗完毕后安装。
(3)拆卸pH电极电极罩,使用5%稀HCl溶液清洗或使用清水清洗;清洗后对pH电极进行重新校验,校验需由专业人员使用标准液完成。
(4)校验完毕后重新安装pH电极;注意pH电极不可裸露在空气中4h以上,因此pH电极的安装应在液位已接近时操作。
(5)脱硫废水长期停运后重启的其他操作与脱硫废水处理系统的启动相同。
(十)废水处理加药系统的启动
1.加药系统启动的准备工作
(1)受过专业培训的操作人员2名;相互配合,相互注意安全。
(2)完善充足的劳保用具。(3)充足的药剂供应。
(4)已提供稳定电源。
(5)电气设备、仪控仪表正常。
(6)已提供水质水量水压稳定的工艺水水源。2.加药设备的清洗(HCl加药设备不在此范畴)
(1)关闭计量泵进出水阀门,拧开Y形过滤器,取出滤网,观察滤网网眼是否有堵塞。如网眼堵塞约大于25%即需要用有压清洁水或自来水清洗滤网里外表面;如滤网少量网眼堵塞或无堵塞则不必冲洗。检查或清洗滤网完毕,安装回去。
(2)关闭加药装置罐体设备排空阀门,打开进水阀门向内注入清洁工艺水。
(3)清洁水注入液位,达到封头盖接缝位置时,关闭进水阀门,开启放空阀。
(4)罐体内清洗水放空后,关闭放空阀,开启进水阀,再次重复操作步骤(2)。
(5)清洗操作根据罐体内清洗情况通过肉眼观察确定;一般罐内清洗水与工艺水进水接近即可;如罐体内原本清洁则只需清洗2次即可。
(6)清洗完成后,关闭放空阀;打开工艺水进水阀门,注入少量清洁水,准备清洗计量泵管道。
(7)打开计量泵进出口阀门,利用重力流清洗计量泵进口管路,时间应大于3min。
(8)将检查或清洗完毕的滤网安装回去。注意滤网不能混用,原先的滤网必须安装回原先的位置。
3.HCl加药设备的清洗
HCl加药设备一般不清洗,使用时间超过1年以上,药剂使用完毕或药剂失效后方清洗。
清洗前应先使用大量清洁水稀释,并通过计量泵工作将管道内残液排出,并清洗管道后,方可按照2中的(1)进行操作。
4.NaOH药剂的配制
(1)向NaOH计量罐内注入清洁水,液位以淹没计量泵入水管道为准。
(2)将NaOH药剂槽罐车排出口与卸酸泵入口连接;连接需严密不得有泄漏。
(3)打开卸酸泵进出口阀门,开启卸酸泵。
(4)当NaOH计量罐液位达到高液位时,或药剂卸料完毕后,关闭卸酸泵。
(5)卸酸泵管道内的残液交由 NaOH药剂槽罐车回收处理。
(6)卸酸操作时应有2人在场,就地控制柜1人,现场1
第一篇
人,有通信设备。
(7)卸酸过程也可通过NaOH药剂槽罐车自带的卸酸装置排入NaOH计量罐内。
(8)卸酸现场人员必须为受过专业培训人员,就地控制柜无必须要求。
(9)NaOH计量罐内原有药剂时,则无需操作步骤(1)。
5.HCl药剂的配制
(1)向HCl计量罐内注入清洁水,液位以淹没计量泵入水管道为准。
(2)将HCl药剂槽罐车排出口与卸酸泵入口连接;连接需严密不得有泄漏。
(3)打开卸酸泵进出口阀门,开启卸酸泵。
(4)当HCl计量罐液位达到高液位时,或药剂卸料完毕后,关闭卸酸泵。
(5)卸酸泵管道内的残液交由HCl药剂槽罐车回收处理。(6)卸酸操作时应有2人在场,就地控制柜1人,现场1
人,有通信设备。
(7)卸酸过程也可通过 HCl药剂槽罐车自带的卸酸装置排入HCl计量罐内。
(8)卸酸现场人员必须为受过专业培训人员,就地控制柜无必须要求。
(9)HCl计量罐内原有药剂时,则无需操作步骤(1)。6.有机硫药剂的配制
(1)向有机硫计量罐内注入清洁水,液位达到50%时关闭进水阀门。
(2)量取 TMT—15溶液20L,注入有机硫计量罐内;
TMT—15的投加量与重金属离子浓度相关,随着重金属离子浓度的增减变化,可按照实际操作情况调整TMT—15溶液的配药浓度。
(3)打开进水阀门,当计量罐内液位达到85%~90%时,关闭进水阀门。
(4)操作时需有受过专业培训人员1人在现场,有通信设备。
7.混凝剂药剂的配制
(1)向混凝剂计量罐内注入清洁水,液位以淹没计量泵入水管道为准。
(2)将混凝剂药剂注入混凝剂计量罐内至液位70%。(3)打开进水阀门,向罐体内注入清洁水3~5min,关闭
进水阀门。
(4)继续添加混凝剂至液位达到85%~90%。
(5)操作时需有受过专业培训人员1人在现场,有通信设备。
(6)混凝剂计量罐内原有药剂时,则无需操作步骤(1)。8.助凝剂药剂的配制
(1)向助凝制备箱罐内注入清洁水,液位以淹没计量泵入水管道为准。
(2)采用其他浓度商品PAM溶液时,量取一定量的商品PAM溶液,注入制备箱内。商品PAM溶液的投加量按其浓度计算。
(3)打开进水阀门,当计量罐内液位达到85%~90%时,关闭进水阀门。
(4)向助凝剂计量箱内注入清水3min后,关闭进水阀门。(5)助凝剂制备箱、助凝剂计量箱内搅拌器为自动启动,
如现场发现未启动,应及时手工启动。如手工启动失败则停止加药工序,放空罐体并清洗,等待检查维修。
(6)操作时需有受过专业培训人员1人在现场,有通信设备。
(7)助凝剂计量罐内原有药剂时,则无需操作步骤(4)。9.加药系统短期停运后的重启
(1)检查/处理药剂;如药剂已失效,及时补充药剂。(2)拆下Y形过滤器,清洗后,重新安装。
(3)开启计量泵进出口阀门。
(4)启动加药系统计量泵电源,即变频器电源。10.加药系统长期停运后的重启
(1)关闭加药系统内罐体设备的排空阀门。(2)拆下Y形过滤器,清洗后,重新安装。
(3)配制药剂。
(4)检查/处理 HCl药剂;如药剂已失效,及时补充药剂。
(5)开启计量泵进出口阀门。
(6)启动加药系统计量泵电源,即变频器电源。
(十一)压滤机的启动
1.压滤机的启动条件
(1)电气设备、仪控仪表完好。(2)控制系统、上位机通信正常。(3)有充足水量、水压的工艺水管线。(4)澄清器底部污泥浓度达到60g/L。(5)压滤机接水盘翻板在关闭位置。2.压滤机的操作步序
(1)当澄清器底部污泥浓度达到60g/L时,启动压滤机“顶紧”按钮,油泵开始工作,顶板开始向前运动。
(2)当压滤机油缸压力达到20MPa时,油泵自动停止进油工作。
(3)开启澄清器至污泥输送泵电动门,启动污泥输送泵。(4)待污泥输送泵工作时间达到设定时间,停止污泥输送
泵,关闭冲洗电磁阀;启动“松开”按钮。
(5)启动压滤机“翻板开”按钮,打开接水盘。
(6)当顶板回复到初始位置后,启动压滤机就地控制柜“自动拉板”按钮,自动拉板机构开始拉板操作。
(7)自动拉板结束,启动“翻板关”按钮,关闭接水盘。(8)压滤机正常操作如(1)~(7)步骤,其他无需
操作。
压滤机工作时,尤其是自动拉板过程中如出现滤板偏移则启动“停止”按钮中止拉板动作。将滤板手动移正后,将自动拉板机构的复位装置打到复位状态,单击“后拉板”按钮,将自动拉板机构拉回起始位置。重新启动“自动拉板”按钮,重新开始拉板。
压滤机工作时需有专人在现场观察,防止拉板出现故障造成事故。
3.压滤机的停止操作
(1)压滤机正常工作状态为间歇式,运行期间不存在停止问题。
(2)压滤机单批次过程中出现故障需停止时,单击“停止”按钮即可。
(3)压滤机在进料过程中的停止,即污泥输送泵因故停止时,应清洗污泥输送管道10min。
(十二)因电力故障停运后的启动
如果电力中断持续时间较短(10min以内),设备和系统应当立即按照如下步骤重新启动,目的是尽快使箱罐内固体处于悬浮状态并使浆液在管道系统中流动。
(1)将所有液坑泵设为自动状态并确定液坑内有液体时所有搅拌机处于运行状态。
(2)启动压缩空气系统。(3)启动工艺水系统。(4)启动工业水系统。(5)启动除雾器冲洗水系统。(6)启动2台吸收塔浆液循环泵。(7)启动吸收塔石膏排出泵系统。(8)启动氧化风机系统。
(9)启动FGD烟气系统。
(10)启动石膏脱水系统。
(11)启动脱硫废水处理系统。(12)启动石灰石浆液制备系统。备注:
(1)严密监测系统重启的所有参数。要特别留意含固体物的管线内的流动信息及任何需加润滑油的轴承温度。如发现任何异常情形,应立即对系统进行检查。
(2)所有系统在被重启前须进行复位,然后按脱硫系统“正常启动”中的指示进行重启。
(3)确定箱罐及地坑内有液体时所有搅拌机应处于运行状态。
十、脱硫装置的运行调整
(一)FGD系统的运行调整任务和规定
1.FGD系统运行调整的主要任务
(1)在主机正常运行的情况下,满足机组烟气脱硫的需要。
(2)保证脱硫装置安全、稳定、连续运行,调整烟气脱硫
率大于95%。
(3)精心调整,保持各参数在最佳工况下运行,降低各种消耗。
(4)保证石膏品质符合要求。2.FGD系统运行监视和调整规定
(1)FGD运行时应充分利用DCS控制、程序控制及自动控制调节装置,以有利于FGD运行工况的稳定和进一步提高调节品质。应尽可能将各自动控制调节装置全部投入运行,并对各参数加强监视,使各运行参数维持在允许范围之内。发现自动失灵或不正常状态时,应立即切至手动操作,汇报值长,并联系热控人员尽快消除恢复。
(2)FGD运行期间的各项记录需完备,同时运行人员每2h正点抄表1次,并对各参数进行分析比较,如发现有参数偏离正常值,应查明原因,采取相应的措施,并汇报机组长、值长。
(3)各自动控制调节装置应经热控人员试验或调整正常后,需经热控人员同意方可投入运行。
(4)运行岗位人员应根据CRT画面显示和报警、打印记录,结合对现场设备的巡视检查情况,进行运行参数、仪表分析,以便及时发现异常、隐患和设备缺陷。
3.FGD系统主要参数的控制范围
FGD系统运行主要控制参数有吸收塔浆液密度、pH值以及浆液液位,浆液制备系统的石灰石浆液密度,石膏脱水系统的石膏品质和滤饼厚度,烟气系统的增压风机流量等。
对于600MW机组来说,主要参数的范围大致如下:吸收塔液位保持在8.5~9.5m正常范围内;吸收塔浆液的pH值保
持在5.4~5.8范围内;吸收塔浆液浓度保持在10%~15%,密度1050~1150kg/m3,相应密度最大不能超过1150kg/m3;
石膏旋流器保证底流浆液浓度为40%~50%,密度值1500~
1600kg/m3;石灰石浆液浓度保持在1240~1250kg/m3。对于
某些电厂,数值会略超出此范围。
(二)FGD系统的运行调整
1.脱硫效率的调整
脱硫装置正常运行时,烟气脱硫率应不小于95%。
吸收塔内浆液的pH值的大小和浆液密度的高低对脱硫效率影响都很大,因此,运行中必须控制其pH值在5.4~5.8,浆液的密度控制在正常值。
正常运行时,给浆量可根据pH值、吸收塔入口SO2浓度、脱硫率及石灰石浆液浓度联合进行调节。当pH值及石灰石浆液浓度降低时,可加大给浆量;当入口SO2浓度增加时,可适当开大石灰石给浆调节门的开度,增加石灰石给浆量。
若脱硫率太低,则加大给浆量,必要时可增加吸收塔浆液循环泵投运数量。
2.吸收塔液位的调整
FGD装置运行时,由于烟气蒸发、携带、废水排放和石膏结晶水而造成损失,因此,需要不断向吸收塔内补充水,以维持吸收塔内的水平衡。
吸收塔液位高度调节是通过调节FGD装置工艺水的进水量来实现的,即通过工艺水对除雾器的冲洗来实现:
(1)当液位低时,启动除雾器的冲洗程序,并增加冲洗次数。
(2)当液位高时,减少除雾器的冲洗次数,以维持吸收塔液位处于正常的工作范围。即维持吸收塔液位在8.5~9.5m的正常范围。
不允许吸收塔液位高于高报警水位。长时间运行,因为此时保护已经不允许进行除雾器的冲洗,若长期运行会造成除雾器的积灰或堵塞。
严禁吸收塔液位过高造成吸收塔的溢流,或吸收塔液位过低引起氧化风机的跳闸。
3.吸收塔浆液浓度的调整
吸收塔内浆液的浓度是通过吸收塔石膏排出泵排出的浆液流量大小来控制的,而石膏排出泵的流量又是通过调节石膏排出泵的变频来实现的。
变频输出越大,排出流量就越大;变频输出越小,排出流量就越小。
由于吸收塔反应池内的浆液有一定浓度的石膏,也有一定浓度的石灰石,如果排出量过大,会导致浆液中石灰石浓度下降,脱硫效率降低,石灰石利用率和副产品石膏品质恶化,严重时还会导致FGD装置因吸收塔液位过低而停运。
如果排出量过小,吸收塔内浆液浓度过大,会增加系统管路的磨损,严重时会造成管路堵塞。
运行中要维持吸收塔内浆液的浓度在10%~15%,相应
的密度最大不能超过1150kg/m3。
4.吸收塔浆液pH值的调整
当吸收塔入口的烟气流量、烟气中SO2浓度以及石灰石品质、石灰石浆液浓度变化时,吸收塔浆液的pH值也随之变化,为保证吸收塔内浆液pH值在规定范围内,应及时对pH值进行调节,以保证FGD装置的脱硫效率。
吸收塔浆液的pH值是通过调节新鲜石灰石浆液的流量大小来实现的。增加新鲜石灰石浆液的流量,可以提高吸收塔浆液的pH值;减少新鲜石灰石浆液的流量,吸收塔浆液的pH值随之降低。
某脱硫系统在正常运行中,应维持吸收塔浆液的pH值在
5.4~5.8。
5.石灰石浆液箱的液位和浓度的调整
石灰石浆液箱的液位是通过控制石灰石浆液制备系统的运行时间和出力来控制的;而石灰石浆液的浓度是通过控制石灰石和工艺水的流量来调节的。
为了维持石灰石浆液箱中液位和浆液浓度,应控制好石灰石浆液制备系统中石灰石的进料量和工艺水流量的比率,一般情况下,保持进入湿磨机的石灰石料量、湿磨机入口研磨水流量的比值在正常值,再通过调节进入湿磨机浆液循环箱内稀释水流量的大小来控制浆液的密度,运行中既要保证石灰石浆液的细度,又要保证石灰石浆液的浓度。
正常运行中石灰石浆液箱的浆液密度控制为1200~
1250kg/m3。
石灰石浆液箱的液位保持在正常值,严禁液位低于0.7m造成搅拌器跳闸或高于6.0m引起液位高报警,发生浆液溢流。
6.石灰石浆液制备系统的运行调整
制浆系统调整的主要任务:保证合格的石灰石浆液品质,使制浆系统在最佳出力下运行,以满足脱硫装置安全、经济运行的需要。
制浆系统出力的影响因素:给料量;球磨机给料粒径;球磨机入口研磨水量;钢球装载量及钢球大小配比;物料可磨性系数。
运行中应严格控制石灰石给料和进入湿磨机研磨水量的配比,若细度过大,应增加研磨水流量,反之则减小研磨水流量。
运行中应调整湿磨机循环箱浆液密度在1400~1500kg/m3,若密度太大,应增大湿磨机浆液循环箱的稀释水量,反之则减小磨机循环箱的稀释水量。
运行中若发现球磨机电流过小,应及时补充合格的钢球。及时调整称重皮带给料机转速,保证湿磨机内给料连续、均匀、适量。及时调整湿磨机浆液循环箱液位在正常范围内,严禁浆液循环箱溢流。进入湿磨机的石灰石粒径应小于20mm,并且石灰石料干净无杂物。运行中若石灰石浆液品质不符合要求,且通过调整仍不合格时,应及时通知化验室化验石灰石给料品质。
7.真空皮带脱水机滤饼厚度的调节
维持真空皮带脱水机上石膏滤饼的厚度是保证石膏含水量的重要条件。当吸收塔石膏排出泵排出的石膏浆液流量发生变化时,单位时间内落到皮带脱水机上的石膏浓浆液的流量随之变化。
通过调节真空皮带脱水机变频器来调整和控制其运动速度,从而达到维持真空皮带脱水机上石膏滤饼稳定的厚度。
正常运行中应保持滤饼的含水率低于10%。8.石膏品质的调整
若石膏水分含量大于10%,则应及时调整真空皮带脱水机给浆量或转速,保证真空皮带脱水机真空度和石膏厚度在合格范围内。
若石膏的颜色较深,则其含尘量过大,应及时联系值长调整电除尘器的运行情况,降低粉尘含量。
若石膏中的CaCO3过多,应及时检查脱硫系统的运行情况,分析石灰石给浆量变化的原因,化验分析石灰石浆液的品质、石灰石原料的品质及石灰石浆液中颗粒的粒度,并及时进行调整。
若石膏中CaSO3过多,应及时调整氧化空气量,以保证
吸收塔中CaSO3被充分氧化。
9.增压风机系统的操作与调整
正常运行时增压风机静叶的开度随锅炉负荷、增压风机进口烟气压力的变化应及时进行调整。增压风机运行时,冷却风机须同时运行,在增压风机启动前应做冷却风机联锁试验。当运行的冷却风机因轴承温度高或主冷却风机跳闸时,另一台会自动启动。
(三)脱硫系统设备运行控制与方法
脱硫系统主要参数的控制见表1711。表1711 脱硫系统主要参数的控制

续表

第二节 脱硫系统设备检修后的调试及运行
一、大修后的验收总则
(1)检修工作全部结束,各项工作票已注销。
(2)装置大小修后,设备变更应有设备变更报告,并交车间及班组一份,作为运行操作人员的技术依据。
(3)大小修后的设备,在进行试验和试转时,由检修人员主持和负责,运行人员负责启动。
二、大修后的检查项目
(1)检修工作全部结束,临时设施、脚手架全部拆除。(2)现场整洁,各通道照明齐全,畅通无阻。栏杆楼梯完
整牢固,各沟道盖板齐全并盖好。
(3)各烟道、管道完好,保温齐全。各设备及构架等处,油漆无脱落现象,新更换的管道油漆颜色应符合要求,各种流程标志方向正确。
(4)烟道、池、罐、仓、吸收塔等内部已清扫干净,无余留物。各人孔门、检查孔应严密关闭。
(5)DCS系统投入,系统仪表用电投入,各组态参数正确,测量显示和调节动作正常。
(6)就地显示仪表、变送器、传感器工作正常,初始位置正确。
(7)压力表、压差表、温度表、液位计、料位计、流量计、浓度计、pH计等测量装置完好并投入。
(8)就地控制盘工作良好,指示灯试验合格。
(9)所有机械、电气设备的地脚螺栓齐全牢固,防护罩完整,连接件及紧固件安装正确。
(10)各手动门、电动门、气动门开关灵活,指示正确,CRT显示应与就地显示相符。
(11)配电系统表计齐全完好,开关柜内照明充足,端子排、插接头等无异常松动和发热现象。
(12)各检查孔、人孔门完好,并确认内部无人后应关闭严密。
三、FGD运行前的试验
FGD系统的调试由分部试验和整套系统启动调试组成,FGD系统的分部试验是在系统设备核查结束后,确认试验对人身、设备都安全的条件下进行的。整个试验包括从FGD受电起,至整套启动试运开始为止的全部启动试运过程,分部试验又分为单体调试和分系统调试两个部分,两者相互衔接、相互交叉。
整套系统启动调试阶段指个体设备和子系统调试合格后,从FGD系统综合水循环开始,到完成满负荷试运移交试生产为止的启动调试过程,该过程又分为系统综合水循环、FGD启动试运、系统优化、168h满负荷试运四个阶段。燃煤机组烟气脱硫工程调试程序如图1721所示。

图1721 燃煤机组烟气脱硫工程调试程序
(一)FGD系统分部试验
1.FGD系统单体试验
单体试验是对FGD系统内的单台辅机的试运,包括其中的电气设备和热控保护装置,例如各类泵(循环浆液泵、工艺水泵等)、升压风机、FGD、搅拌器、各个阀门等设备进行开/关试验。FGD系统的单体试验,可以细分为电气系统受电调试、集散控制系统(DCS)调试和关键设备的调试(如升压风机、GGH等安装部门负责),与FGD系统分系统调试结合进行。
(1)电气系统受电调试。通过电气系统调试带电,使FGD厂用电源系统达到安全、可靠的状态。为FGD系统分部试验打下良好的基础。
1)厂用电带电的条件:6kV、380V系统的设备、直流系统设备、接地系统、照明通信系统、电气系统附属的消防系统及设施单体试验完毕,验收合格具备投入条件;电气联锁保护系统静态调试完毕;电厂侧6kV系统已经做好对FGD供电的准备,随时可以投入。
2)6kV、380V系统带电。
3)直流系统、UPS系统投入运行。
4)DCS系统供电。
(2)DCS调试。调试内容包括:
1)DCS内部调试应具备的条件如下:电控楼电子间及控制室空调运行;接线完毕,检查正确并投入;就地设备,系统调试。
2)DCS调试内容包括:DCS硬件检查;DCS内部网络检查;DCS软件安装并运行正常;DCS装置运行组态逻辑检查;仪器、仪表校验;联锁保护设备、系统调试;系统优化。
(3)关键设备的机械试运转。机械设备试运转的目的是在FGD系统正式运行前,测量机械设备的振动、温度、声音等数据,确认试运转时没有异常,如有异常缺陷,在正式启动前予以消除。在试运转的同时,对设备的启停联锁过程、次序、时间、报警定值及联锁保护定值进行检查和测试。关键设备的机械试运转用实际应用的液体来进行,皮带及给料机的机械试运转应在不输送原料的情况下完成。机械试运转原则上应持续进行1~3h。在机械试运转期间,应检查并记录电动机电流、轴承温度、轴承座振动、噪声水平、进出口压力、转动、设备联锁情况、报警定值及联锁保护定值等。
关键设备的机械试运转的项目包括烟气挡板系统(原烟气挡板门、净烟气挡板门和旁路挡板门等)、吸收塔系统(搅拌器、浆液循环泵、石膏抽出泵和氧化风机等)、升压风机、GGH、石膏脱水系统(真空皮带机、石膏旋流器和真空泵等)、石灰石制备系统(球磨机、给料机和石灰石浆液泵等)、电动阀、调节阀的检查与远方操作试验、FGD事故联锁跳闸。
现以升压风机试运转为例来说明关键设备机械试运转的一般步骤:首先对风机进行全面检查,确认升压风机叶片角度为零且调节处于手动位置,若条件允许,经锅炉班长同意可关闭FGD旁路烟道挡板,将风机电源开关置于试验位置,模拟升压风机启动进行以下试验:
1)电动机前端轴承温度高于110℃报警。2)风机推力轴承温度高于100℃报警。3)电动机前端轴承温度高于120℃报警。
4)风机轴承振动高于1.4mm/s报警。
5)电动机后端轴承温度高于110℃报警。
6)风机轴承振动高于1.4mm/s报警。
7)电动机后端轴承温度高于120℃报警。
8)FGD系统前压力最小值0Pa。
9)电动机绕组温度高于145℃报警。10)烟囱前压力大于最大值600Pa。11)风机推力轴承温度高于85℃报警。
12)升压风机转速小于50r/min,刹车装置动作。
上述试验合格后,将风机电源开关打至运行位置并合上控制电源开关,联系值班班长同意后启动“SCS(顺序组控制)升压风机”。检查风机转向正确、无异常,摩擦和撞击声、轴承温度和振动值符合规定,润滑油泵、控制油泵及各冷却风机运行良好。风机试转后,停止风机运行,关闭开启的各人孔门。
2.FGD系统分系统调试
分系统调试是指按工艺系统或功能系统等单个系统的调整试运,包括动力、测量、控制等,也就是对FGD系统的主要组成部分进行冷态模拟试运行。这些系统包括公用系统(压缩空气系统,闭式冷却水系统和工艺水系统等)、吸收塔系统、烟气系统(含升压风机、GGH及其辅助系统等)、石灰石制备系统(包括石灰石接收和储存系统、石灰石研磨系统、石灰石供浆系统等)、石膏脱水系统(含真空皮带机系统)、排空系统(含事故浆液池和地坑系统)以及取样系统。烟气系统的冷态调试是分系统调试的核心,也是全面检查该系统的设备状态并进行系统联锁和保护试验的重要环节。
现仅叙述烟气系统冷态调试的一般原则,其他分系统不予说明。
(1)烟气系统冷态启动调试前应具备的条件:安排机组停运,锅炉侧与FGD信号交换系统投入;烟气通道打通,沿程系统各设备的人孔门、检修孔等封闭,确认系统严密;烟气系统及相关的热工测点安装、校验完毕,具备投入条件;烟气系统各阀门、挡板安装调试完毕;烟气系统烟道、升压风机、GGH、吸收塔等设备和系统清理干净;挡板、密封风机分部调试合格,具备投入条件;升压风机、冷却风机分部试运合格,联锁保护正确,具备投入条件;升压风机润滑、控制油系统分部试运合格,具备投入条件;升压风机电动机试运合格,具备投入条件;GGH及其附属系统单体试运结束,具备投入条件;烟气系统DCS控制、保护调试完毕;通道畅通,现场清洁,照明投入,符合试运要求。
(2)冷态启动前的试验检查:FGD烟气系统挡板门(原烟气、净烟气、旁路挡板门)投入;升压风机与挡板门的联锁、保护静态试验合格;升压风机、GGH及其附属设备联锁保护试验合格;FGD与锅炉联锁、保护试验模拟合格;检查锅炉与FGD装置之间的交换信号;锅炉信号联锁保护试验;FGD装置设备故障跳闸及FGD装置切除保护试验联锁试验;检查烟道已封闭;检查监测信号已投入;检查关闭原烟气挡板、升压风机挡板、净烟气挡板;检在开启旁路挡板;检查锅炉烟气系统投入运行;锅炉送、引风机运行,锅炉烟气系统参数接近正常运行工况。
(3)烟气系统冷态启动试运:按烟气系统启动程序启动后,手动开启风机导叶,调至所需工况,检查烟气系统运行的平稳性及各监视仪表的显示状态,确认运行参数正常,升压风机冷态8h试运,记录各参数。烟气系统冷态试验方法如下:
1)FGD冷态变负荷运行跟踪特性试验。投入升压风机入口压力自动跟踪,改变锅炉风量,记录参数变化。
2)FGD保护对锅炉扰动试验。
3)旁路挡板门联锁对锅炉扰动影响试验。投入旁路挡板门联锁保护,手动FGD装置跳闸,记录变化。
(二)FGD系统整套启动运行操作程序
整套启动调试包括FGD系统综合水循环、FGD启动试运、系统优化和168h满负荷试运。大体分为FGD系统综合水循环、正常启动、正常运行和正常停运四部分,这里只描述前两部分。
1.FGD系统综合水循环
FGD系统综合水循环调试的目的是在用水进行模拟操作的条件下,对FGD系统的控制系统以及启动与停止顺序进行检查,并对设备进行检查,以预先发现在FGD装置启动后可能发生的故障。在进行系统综合水循环调试的同时,要检查与水循环系统相关的联锁系统。水循环调试设备的范围应为用于处理液体及浆液的设备,但不包括烟气系统、DCS冲洗水、事故浆液池搅拌器和地坑的搅拌器。
(1)FGD系统综合水循环的条件:电气系统、DCS系统、热工仪表投入,工艺水系统调试完毕,各系统设备冲洗完毕;石灰石供浆系统调试完毕;吸收塔系统单体调试完毕(包括循环泵、除雾器、氧化风机等);石膏脱水系统单体调试完毕(包括石膏排出泵、石膏旋流站、真空皮带机系统等)。
(2)FGD系统综合水循环调试程序:启动工艺水向吸收塔供水;吸收塔进入高水位后,吸收塔水位自动控制;按程序启动1~4号循环泵试运行;按程序启动1号、2号浆液排出泵;按程序启动1号、2号石膏旋流器试运行;试运行热工控制系统的仪表、仪器,作调整校验;检查系统、设备运行情况,对出现的问题及时处理,使FGD系统正常运行。初步调整FGD装置的控制系统,包括确认控制阀门的流量特性曲线,调整手动控制门,调整程序计时器等;调整各个设备系统运行状态;试运行束后,停止各个系统设备,进行系统设备完善处理。
2.FGD系统正常启动
FGD系统正常启动流程如图1722所示。

图1722 FGD系统正常启动流程图
四、FGD脱硫系统启、停操作
(一)脱硫装置投运前必须具备的条件
1.试验及验收要求
整个脱硫系统已经按验收标准及FGD装置的性能试验规范通过性能试验及设备验收。
2.环境及安全要求
FGD投运前,要求场地清理干净,道路畅通,各操作巡查平台、走道扶手完整,照明充足。灰水沟有盖板,各转动机构外面有护罩或挡板,安全标志清晰,电气安全联锁要完好,控制室具备有效的降温、防尘及防火措施。
3.运行人员的技能要求
(1)熟知FGD设备的构造、系统及工作原理,自动及保护装置的结构和正确的使用方法。
(2)掌握FGD装置的启动、停运操作、运行控制的调整操作以及各参数变化带来的影响,并能根据参数变化,熟练地进行各种异常情况的处理。
(3)了解电力工业技术管理法规、电业安全工作规程以及事故处理规程、消防规程等有关内容。
(4)掌握锅炉、汽轮发电机组、厂用电系统的运行方式。(5)熟练掌握FGD装置的投入、隔离以及FGD附属设备
各个子系统的操作方法,并能做好运行维护和保养工作。
4.技术资料及器具准备
(1)工器具的准备。运行人员应配置常规电工器具和警告牌等安全用具,以及阀门扳手等机务工具。
(2)有必需的备品、备件及消耗性材料的储备。
(3)有完整的技术资料与台账的准备。做好投运前或大修后有关技术资料的验收、整理、存放工作。应有全套的机务与电气图纸。针对常用的设备图纸、资料、说明书等应根据需要准备数份。
在安装或大修中,设计修改通知单及设备变更单要整理归类,并在图纸上反映出来。
运行部门要准备FGD装置运行规程、值班记录、运行日报表、设备巡回检查卡、开停机操作卡、工作票登记本等运行所需的台账、报表、记录表等。
(二)启、停操作的一般要求
脱硫装置的启停由运行人员在控制室内操作FGD装置的控制系统来自动进行,FGD装置的停运可分为短时停运(数小时)、短期停运(数日)和长期停运(机组大修),与此相应,FGD装置的启动可分为短时停运后启动、短期停运后启动和长期停运后启动。
1.脱硫装置的停运
(1)短时停运的操作。如果停机数小时,不必使全部FGD装置都停止工作,仅关闭部分设备。以下设备一般应停止运行:①FGD烟气系统;②吸收塔循环泵;③氧化风机;④石灰石浆液供给系统。
切换至旁路运行后,FGD装置与烟气隔离,原烟气和净烟气挡板门应关闭。
(2)短期停运的操作。如果停运需持续数日,则除了上述设备停运外,以下设备也应停运:①除雾器冲洗系统;②石灰石浆液制备系统;③石膏脱水系统;④石膏浆液排出泵及石膏溢流浆液泵;⑤工业水系统。
为防止石膏板结,必须及时将石膏仓内的积料全部排空。在短时停运和短期停运期间,装置中输送浆液的管线必须
冲洗。在有浆液的容器内,搅拌器继续维持运行。
(3)长期停运的操作。脱硫系统随着机组进行大修,需要
将吸收塔内的浆液由石膏浆液排出泵及吸收塔地坑泵(石膏浆液排出泵因液位低停运后)排到事故浆液罐,除事故浆液罐搅拌器应运行外,其他浆罐均应排空,其他设备均应停运以备检修。
2.脱硫装置的启动
(1)短时停运后的启动操作。
为尽量缩短启动周期,某些设备同时启动,以备用方式运行,直到启动程序达到规定步骤才取消这些设备的预备运行方式。按以下顺序进行开启:吸收塔循环泵→石灰石浆液供给系统→FGD烟气系统→氧化风机。
至少两个吸收塔循环泵投入运行后,烟气方可进入系统。为避免电动机启动电流高而导致负荷过大,吸收塔循环泵依次启动。
(2)短期停运后的启动操作。短期停运后,某些停运的设备可同时启动。程控中的各回路及启停过程设有联锁,以确保启动时维持正确顺序。由于各种设备并列启动,启动时间较短。
(3)长期停运后的启动操作。FGD装置大修完毕后,应对各个系统、设备进行试运行,试验合格后备用。在机组启动前一天,应启动工艺水系统、工业水系统和制浆系统,石灰石浆液箱储备足够的合格吸收剂。
启动事故浆液泵及吸收塔地坑泵(事故浆液泵因液位低自动停运),将事故浆液罐内浆液返回吸收塔内,以确保机组启动后FGD装置及时投入。有浆液的容器内的搅拌器维持运行。机组启动后,FGD装置按短期停运启动进行操作。
(三)烟气系统的启动、停运
1.启动前完成的工作
(1)烟气系统烟气通道挡板门及其附属设备准备完毕。(2)电气设备检查合格,送电。
(3)热控仪器仪表投入,联锁保护投入。
(4)GGH系统准备完毕。
(5)增压风机及其辅助系统准备完毕。2.启动前应检查并确认以下手动阀的位置(1)原烟气通道疏水阀关闭。
(2)原烟气通道疏水管冲洗阀关闭。(3)净烟气通道疏水阀关闭。
(4)净烟气通道疏水管冲洗阀关闭。(5)增压风机本体排放阀关闭。
(6)密封风手动阀关闭。3.启动、停运顺序
启动顺序:GGH系统启动→挡板门密封风机停止→FGD原烟气挡板门打开→吸收塔排空门关闭→FGD净烟气挡板门打开→增压风机子系统启动→缓慢关闭旁路挡板门,同时缓慢调大增压风机静叶开度→增压风机入口压力投自动→挡板门密封风机启动→GGH净化风机子系统启动。
停止顺序:挡板门密封风机停止→增压风机静叶开度调节手动,增压风机入口压力解自动→打开烟气旁路挡板→手动缓慢关闭增压风机静叶,使开度为最小→增压风机子系统停止→GGH空气吹扫风机子系统停止→FGD原烟气挡板门关闭→吸收塔排空门打开→FGD净烟气挡板门关闭→挡板门密封风机启动→增压风机停止,延时→手动停止 GGH子系统。
4.烟气系统涉及子系统的启动、停运顺序
(1)GGH子系统。
启动顺序:GGH密封风机启动→导向轴承油泵联锁投入、
支撑轴承油泵联锁投入、启动GGH辅助电动机→延时→GGH主电动机启动、辅助电动机停止。
停止顺序:GGH主辅电动机停止→延时→导向轴承油泵停止、支撑轴承油泵停止→GGH密封风机停止。
(2)增压风机子系统。
启动顺序:增压风机冷却风机启动、润滑油泵启动→增压风机入口压力手动、调节叶片开度最小→增压风机启动。
增压风机油站油温小于5℃,手动投入电加热器;增压风机油站油温大于30℃,手动停止电加热器;增压风机油站油温大于45℃,手动投入冷却水。
停止顺序:增压风机入口压力手动、调节叶片开度最小→增压风机停止→延时→增压风机冷却风机停止、润滑油泵停止。
(3)GGH空气吹扫风机子系统。
启动顺序:关闭空气吹扫风机入口电动阀、关闭空气吹扫风机出口电动阀→启动空气吹扫风机→延时→开空气吹扫风机出口电动阀→开空气吹扫风机入口电动阀。
停止顺序:停止空气吹扫风机→关闭空气吹扫风机出口电动阀→关闭空气吹扫风机入口电动阀。
(4)GGH蒸汽吹灰子系统。
启动顺序:开启疏水阀→关闭母管疏水阀、开启蒸汽隔离阀→延时→关闭疏水阀→下部吹灰器启动→下部吹灰器停止→上部吹灰器启动→上部吹灰器停止→关闭蒸汽隔离阀→开启疏水阀。
停止顺序:停止下部吹灰器、停止上部吹灰器→关闭蒸汽隔离阀→开启疏水阀、开启母管疏水阀。
每班需根据GGH进出口原烟气差压情况投入蒸汽吹扫,在投入蒸汽吹扫后,差压仍无法达到正常值时,需投入高压水冲洗。
(5)GGH高压水吹灰子系统。
启动条件:①GGH主电动机运行;②GGH高压水泵运行;③上部吹灰器、下部吹灰器均在关闭位。
启动顺序:关闭上部吹灰器及下部吹灰器高压供水阀→开启下部吹灰器高压供水阀→下部吹灰器启动→下部吹灰器停止→关闭上部吹灰器高压供水阀→开启上部吹灰器高压供水阀→上部吹灰器启动→上部吹灰器停止→关闭上部吹灰器高压供水阀。
停止顺序:停止上部吹灰器及下部吹灰器→关闭上部吹灰器及下部吹灰器高压供水阀。
(6)挡板门密封风机子系统。
启动顺序:密封风机出口挡板门关闭→密封风机入口挡板门关闭→密封风机启动→延时→密封风机出口挡板门开→密封风机入口挡板门开。
停止顺序:密封风机入口挡板门关闭→密封风机出口挡板门关闭→密封风机停止。
(四)吸收系统的启动、停运
1.启动前完成的系统检查工作
(1)各箱、罐内部已清理干净,人孔门、检查孔检查后封闭。
(2)就地仪表工作正常,初始位置正确。
(3)压力、压差、温度、液位、流量、密度、pH计等测量装置完好,并投入。
(4)备手动阀、电动阀、调节阀开关灵活、指示准确,盘面显示与就地指示相符。
(5)各设备事故按钮完好。
(6)各设备周围应清洁,无积油、积水及其他杂物。(7)现场清洁、排水沟畅通、沟盖板齐全。
(8)工艺水系统具备投入条件。(9)供浆系统具备投入条件。
(10)各地坑液位在可控制范围内,不在高液位启动。2.启动、停运顺序
启动顺序:工艺水泵启动→吸收塔搅拌器启动→循环泵子系统启动→除雾器冲洗程序启动→石膏浆排出泵联锁启动→吸收塔供浆子系统启动→氧化风机启动→供浆量控制自动→供浆调节阀开度自动。
停止顺序:供浆量控制手动、供浆调节阀开度手动→氧化风机停止→吸收塔供浆子系统停止→石膏浆排出泵联锁停止→除雾器冲洗程序停止→吸收塔地坑液位低于高值时循环泵子系统停止。
3.吸收系统涉及子系统的启动、停运顺序(1)循环泵子系统。
启动顺序:关闭循环泵排放阀→开启循环泵入口阀→延时→启动循环泵。
停止顺序:循环泵停止→关闭循环泵入口阀→开循环泵排放阀→延时→关闭循环泵排放阀。
循环泵停运后,需手动开启循环管冲洗阀冲洗。(2)石膏浆排出泵子系统。
启动顺序:关闭石膏浆排出泵冲洗阀、关闭pH计冲洗阀→关闭石膏浆排出泵出口阀→开pH计前隔离阀→石膏浆液分配阀开向石膏溢流浆液箱→开石膏浆液排出泵入口阀→启动石膏浆液排出泵→延时→开石膏浆液排出泵出口阀→pH计冲洗子系统启动→石膏浆液密度控制自动(真空脱水系统自动启
停)。
停止顺序:关闭石膏浆液排出泵出口阀→停止石膏浆液排出泵→开石膏浆液排出泵冲洗阀→延时→关闭石膏浆液排出泵入口阀;若另一台石膏浆液排出泵运行,则关闭石膏浆液排出泵冲洗阀;若另一台石膏浆液排出泵未运行,则继续下列工作→石膏浆液密度控制手动→石膏浆液分配阀开向石膏溢流浆液箱、真空脱水系统自动停止→pH计冲洗子系统停止→开pH计前隔离阀→开石膏浆液排出泵出口阀→延时→关闭石膏浆液排出泵出口阀→关闭石膏浆液排出泵冲洗阀。
(3)pH计冲洗子系统。
启动顺序:关闭pH计前隔离阀→开pH计冲洗阀→延时→关闭pH计冲洗阀→开pH计前隔离阀→延时,重复上述过程。
停止顺序:关闭pH计前隔离阀→开pH计冲洗阀→延时→关闭pH计冲洗阀。
(4)吸收塔供浆子系统。
启动顺序:①关闭供浆冲洗阀→②开供浆隔离阀→③供浆调节阀开度自动,供浆量控制自动→④延时→⑤供浆量控制手动,关闭供浆隔离阀,供浆调节阀自动全开并切换为手动→⑥开供浆冲洗阀,延时→⑦关闭供浆冲洗阀→③开供浆隔离阀,并重复执行上述第③~⑧步操作。
停止顺序:关闭供浆隔离阀→供浆量控制手动,关闭供浆隔离阀,供浆调节阀自动全开并切换为手动→开供浆冲洗阀→延时→关闭供浆冲洗阀→供浆调节阀自动全关。
(五)石灰石浆液制备系统的启动、停运
1.石灰石破碎系统的启动、停运
启动顺序:启动除铁器→启动输送皮带机→延时→启动斗式提升机→启动破碎机→延时→启动振动给料机→延时→除铁
器卸料。
停止顺序:停止振动给料机→延时→停止破碎机→延时→停止斗式提升机→延时→停止输送皮带机→停止除铁器。
2.制浆系统的启动、停运
启动顺序:启动湿磨子系统→再循环浆液箱液位平衡阀自动全开后置为手动控制、湿磨供水阀开度控制自动、再循环浆液箱供水阀开度控制自动→启动称重皮带给料机→石灰石浆液密度闭环控制手动→等待再循环浆液箱液位达到规定液位→联锁启动浆液箱再循环泵→再循环浆液箱液位平衡阀开度置为自动。
停止顺序:停止称重皮带给料机、湿磨供水阀开度控制置为手动、再循环箱供水阀开度控制置为手动、延时→自动关闭湿磨供水箱→自动关闭再循环箱供水阀→再循环箱液位平衡阀自动全关后置位手动控制,等待再循环箱液位降到规定液位→联锁停止再循环泵→停止湿磨子系统。
在石灰石浆液制备系统的启动、停运操作中,所涉及的各子系统启动、停运操作顺序如下:
(1)湿磨子系统的启动、停运。
启动顺序:开启湿磨用工业水阀→湿磨油站加热器根据油箱温度自动启停投入→等待油站温度达到规定值→联锁启动低压润滑油泵→延时→启动高压润滑油泵、等待高压润滑油泵出口油压低报警消除→延时→启动湿磨主电动机→延时→停止高压润滑油泵。
停止顺序:停止湿磨主电动机→启动高压润滑油泵→高压润滑油泵出口油压低报警消除→延时→停止高压润滑油泵→联锁停止低压润滑油泵→延时→联锁启动低压润滑油泵、延时→启动高压润滑油泵→高压润滑油泵出口油压低报警消除→延时→停止高压润滑油泵→联锁停止低压润滑油泵→关闭湿磨用工业水阀、停止湿磨油站加热器运行。
(2)浆液箱再循环泵子系统的启动、停运。
启动顺序:关闭泵出口阀、冲洗阀→开启泵入口阀→启动泵运行→延时→开启泵出口阀。
停止顺序:关闭泵出口阀→停止泵运行→开启冲洗阀→延时→关闭泵入口阀,若另一台泵运行,则关闭泵冲洗阀;若另一台泵未运行,则继续下列工作→开启泵出口阀→延时→关闭泵出口阀→延时→关闭冲洗阀。
(六)石膏脱水系统的启动、停运
启动顺序:空气压缩机启动→滤布冲洗水泵启动→皮带润滑水流量低信号不报警、真空箱密封水流量低信号不报警→滤饼冲洗水箱排放阀关闭、滤饼冲洗水箱补水阀自动开至满水后关闭→真空皮带机启动→开真空泵密封水气动阀→真空泵密封水流量低信号不报警→真空泵启动→滤饼冲洗水泵启动、皮带机速度控制自动→石膏浆液分配阀开向真空皮带机。
停止顺序:皮带机速度控制手动→石膏浆液分配阀开向石膏溢流浆液箱→滤饼冲洗水泵停止→滤饼冲洗水箱排放阀开启→真空泵停止→真空泵密封水启动阀关闭→延时→真空皮带机停止→滤布冲洗水泵停止。
石膏仓卸料装置为就地控制,手动按就地控制盘上的按钮进行启停操作。
(七)工艺水、工业水系统的启动、停运
(1)工艺水、工业水系统均通过手动启停。可手动预选A泵或B泵运行,并在泵间自动故障切换。
(2)工艺水补给由电动蝶阀控制。该阀在液位低于低液位设定值时自动打开,在液位高于高液位设定值时自动关闭。
(3)工业水补给由电动蝶阀控制。该阀在液位低于低液位设定值时自动打开,在液位高于高液位设定值时自动关闭。
(4)当工艺水箱液位高于启动液位设定值时允许启动工艺水泵,低于低液位设定值时保护动作停止工艺水泵运行。
(5)当工业水箱液位高于启动液位设定值时允许启动工业水泵,低于低液位设定值时保护动作停止工业水泵运行。
(八)事故浆液罐和地坑系统的启动、停运
1.事故浆液输送泵
允许启动:事故浆罐液位高于液位设定值。
保护停止:事故浆罐液位低于低液位保护设定值。2.事故浆罐搅拌器
允许启动:事故浆罐液位高于液位设定值。
保护停止:事故浆罐液位低于低液位保护设定值。3.地坑泵
自动启动:地坑液位高于自动启动液位设定值。自动停止:地坑液位低于低液位设定值。
保护停止:地坑液位低于低液位保护设定值。4.地坑搅拌器
自动启动:地坑液位高于液位设定值。
保护停止:地坑液位低于低液位保护设定值。
五、运行中异常情况处理
在FGD装置运行期间,应保护脱硫系统的所有设备免受其他设备误动作的影响。以下可能发生的故障会干扰FGD装置运行:
(1)增压风机故障。(2)锅炉侧故障。
(3)GGH停止转动。
(4)所有吸收塔浆液循环泵停止运行。
(5)原烟气挡板门和/或净烟气挡板门未打开。(6)原烟气温度超出了允许范围。
出现上述故障,旁路挡板门立即自动打开,同时关闭增压风机和原烟气挡板门,断开进入FGD装置的烟气通道。对各类泵等其他设备也采取了相应的保护措施,设置设备内部联锁保护,保证设备的安全、稳定运行。
一般情况下,当装置处于危险情况时。系统保护动作,使装置处于安全状态。
第三节 联锁保护
燃煤烟气湿法脱硫系统在保持高的脱硫效率下,设备的安全经济运行是脱硫联锁控制系统的主要实现目标。本节主要介绍脱硫系统联锁控制的总体概念、FGD及锅炉保护和脱硫系统联锁条件的应用实践。
一、联锁控制的总体概念
湿法烟气脱硫工程的控制系统一般以FGDDOS为核心,实现完整的热工测量、自动调节、控制、保护及报警功能。其自动化水平将使运行人员无需现场人员的配合,在控制室内即可实现对烟气脱硫设备及其附属系统的启动、停止和正常工况的监视、控制和调整,以及异常与事故工况的报警、联锁和保护。整个FGD设备的联锁控制包括烟气系统、石灰石浆液制备系统、吸收塔系统、石膏脱水及储存系统和水系统。
1.整个FGD设备的启动步骤(1)水系统启动。
(2)石灰石浆液制备系统启动。(3)吸收塔系统启动。
(4)石膏脱水及储存系统启动。(5)烟气系统启动。
2.整个FGD设备的停止步骤(1)烟气系统停止。
(2)石膏脱水及储存系统停止。(3)石灰石浆液制备系统停止。(4)吸收塔系统停止。
(5)水系统停止。
二、FGD设备保护
(一)原理
如果FGD设备出现危险情况,则设备必须在安全的条件下关断,以确保对人或主要设备不存在任何风险。
1.FGD设备的正常运行状态(1)FGD旁路烟气挡板关闭。(2)净烟气挡板打开。
(3)吸收塔通风阀关闭。(4)烟气换热器开启。(5)增压风机开启。(6)原烟气挡板打开。(7)浆液循环泵开启。(8)吸收塔搅拌器开启。
(9)除雾器冲洗泵3台中至少1台开启(除雾器冲洗水泵仅1台开启时,为保证设备安全,2台塔除雾器应无同步冲
洗)。
(10)氧化风机3台中至少2台开启。(11)清洁烟气温度不小于80℃。2.FGD设备的停止状态
(1)FGD旁路烟气挡板打开。(2)增压风机关闭。
(3)原烟气挡板关闭。(4)吸收塔通风阀打开。(5)净烟气挡板关闭。(6)烟气换热器关闭。(7)浆液循环泵关闭。
(二)FGD设备保护顺序
1.FGD设备从正常运行状态切换到停止状态下开启的顺序(1)旁路烟气挡板打开。
(2)增压风机关闭。(3)原烟气挡板关闭。(4)吸收塔通风阀打开。(5)净烟气挡板关闭。(6)烟气换热器关闭。(7)浆液循环泵关闭。
注:增压风机关闭后60s,浆液循环泵开始关闭。
(三)FGD保护信号的条件
FGD保护顺序将因下列任一条件而自动启动:
(1)2台以上(含2台)浆液循环泵同时出现故障。正常满负荷运行时,3台浆液循环泵均投入运行。如一台泵出现故障,FGD设备还可继续使用。如果第二台泵又出现故障,则将对吸收塔内衬和除雾器造成威胁。FGD必须按照要求切换到停止状态。
(2)2台以上(含2台)除雾器冲水泵同时出现故障。正
常满负荷运行时,2台除雾器冲水泵投入运行。如果正常运行的两台除雾器冲水泵和备用的一台除雾器冲水泵均出现故障,则将对吸收塔内衬和除雾器构成威胁。FGD必须按照要求切换到停止状态。
(3)FGD入口原烟气温度大于FGD切换旁路运行温度。原烟气的温度将通过装在FGD设备进口烟道上的3个温度传感器测量。如果进气温度(3选2)大于FGD切换旁路运行温度,则FGD设备按照要求切换到停止状态。
(4)正常运行时原烟气挡板未开或净烟气挡板未打开。按照要求,原烟气和净烟气挡板在正常运行时是打开的。这一位置将由用于每个挡板的外部限位开关来显示和检查。如果限位开关就开位出现偏差(3选2)则FGD设备按照要求切换到停止状态。
(5)FGD系统失电。如6kV失去或380V电源失去,则
按要求开始执行保护顺序。必要的紧急电源有FGD保安电源提供。
1)切换到FGD保安电源。2)旁路烟气挡板打开。3)增压风机关闭。
4)原烟气挡板关闭。5)吸收塔通风阀打开。6)净烟气挡板关闭。7)烟气换热器关闭。8)浆液循环泵关闭。
下列步骤必须由操作人员完成,即检查是否已实现:1)FGD旁路烟气挡板打开。
2)吸收塔通风阀打开。3)原烟气挡板关闭。4)净烟气挡板关闭。
5)吸收塔搅拌器:自动使用保安电源,维持运转状态。6)石灰石浆液箱搅拌器:自动使用保安电源,维持运转
状态。
7)磨机润滑油箱:自动使用保安电源,维持运转状态。8)磨机排浆罐搅拌器:自动使用保安电源,维持运转状态。9)除雾器冲水泵中的2台:自动使用保安电源,维持运
转状态2h。
10)工艺水泵:自动使用保安电源,维持运转状态。
11)增压风机冷却风机:自动使用保安电源,维持运转状
态2h。
12)增压风机电动机润滑油泵:自动使用保安电源,维持运转状态2h。
(6)烟气换热器故障运行(主、辅电机同时故障)。如果烟气换热器(GGH)主、辅电机同时故障,FGD会自动停机。按照要求切换到停止状态。
(7)增压风机故障停运。如果增压风机出现故障停运,FGD设备必须按照要求切换到停止状态。
(8)吸收塔搅拌器不少于3台或同侧2台出现故障停运。如果吸收塔搅拌器不少于3台或同侧2台出现故障停运,FGD设备必须按照要求切换到停止状态。
(9)锅炉 MFT(Main FuelTrip,主燃料跳闸)。当锅炉
MFT时,FGD设备必须按照要求切换到停止状态。
(10)烟气灰尘含量超过最高值后30min。当烟气灰尘含量超过最高值后30min时,为了保护FGD设备(对GGH有害)不受损坏,FGD设备必须按照要求切换到停止状态。
(四)设备正常停运保护
在FGD装置停机期间,装置中不同的管道系统中装有浆液,必须对这些管道系统进行冲洗,防止固体材料的沉淀。在短时间停机期间,吸收塔搅拌器、石灰石浆罐搅拌器等仍保持工作。
三、自FGD侧发出锅炉保护信号条件
由于FGD旁路挡板未能正常运行(如未能按要求打开或关闭)而引起的锅炉压力变化,由锅炉自带的压力检测进行保护动作。
为了保护整个FGD设备中的防腐衬胶、玻璃鳞片和除雾器等不能耐高温的设备和材料,当FGD入口烟道温度大于最高允许运行温度,或所有运行的吸收塔循环泵均故障停机,或除雾器冲洗水泵均故障停机时,FGD入口原烟气挡板“未打开”且旁路烟气挡板“未打开”,则请求锅炉跳机。
如果从锅炉到烟囱的烟道“未打开”,则请求锅炉跳机。必须保证一条烟道是畅通的,这意味着在锅炉正常运行过程中要么正常烟道(FGD入口原烟气挡板、FGD出口净烟气挡板)是“打开的”,要么旁路烟道(旁路挡板)是“打
开的”。
引起FGD跳机或旁路挡板门未开(拒动),即作为FGD侧发出的锅炉系统保护信号。
四、脱硫系统控制联锁条件的应用实践
某电厂机组容量2×300MW,采用2炉1塔的配置方式,石灰石制备采用来粉制浆工艺,烟气系统设GGH。
(一)烟气系统
1.烟气系统启动允许条件
具备所有以下条件,烟气系统允许启动:
(1)循环泵运行A/B/C(至少1台)。
(2)原烟气温度正常(100℃<T<160℃)。
(3)增压风机本体启动条件满足(除原烟气挡板关闭、净烟气出口挡板门开启条件外)。
(4)GGH运行(当系统设GGH时)。
(5)机组运行(机组送脱硫信号)。
(6)进口烟尘含量低于150mg/m3 (标况下)。
(7)机组负荷大于40%(机组送脱硫信号)。(8)1台石灰石浆液泵在工作。
(9)工艺水泵运行。
(10)1台氧化风机在运行。
(11)FGD烟气系统无保护跳闸信号。2.FGD烟气系统联锁保护条件
在以下情况之一发生时,FGD烟气系统保护动作,首先执行旁路挡板开启指令,同时执行FGD烟气系统顺控停止程序。
(1)3台吸收塔浆液循环泵都停止。
(2)2个相邻布置的吸收塔搅拌器同时出现故障,延时1800s(或3个以上吸收塔搅拌器同时出现故障,立即执行)。
(3)FGD入口烟气温度大于最高温度180℃,延迟30s。(4)FGD系统失电。
(5)GGH主辅电机停运(如2台电动机都跳闸延迟10s,2台电动机转速低延迟120s)。
(6)增压风机停止。
(7)锅炉 MFT。
(8)增压风机入口压力低于最低值,延时60s。(9)增压风机入口压力高于最高值,延时60s。3.旁路挡板快速打开(保护)动作触发条件当发生下列任一条件时,旁路挡板快速打开:
(1)出现FGD烟气系统联锁保护条件。(2)增压风机叶片突然关小且小于43°。
(3)增压风机入口压力小于-1000Pa或大于600Pa。
4.挡板门密封风机启动、停止
(1)启动允许:
1)挡板门密封风机无电气故障。2)挡板门密封风机停止。
3)挡板门密封风机出口门停止。
4)任一增压风机出口烟气挡板门关闭。(2)停止允许:密封垫及加热器停止。
(3)保护停止:启动后延时1min出口阀门未关。
(4)联锁保护:当2台以上密封风机联锁投入时,2台密封风机互为热备用。
(5)报警:密封温度小于75℃;或密封温度高于130℃。5.挡板门密封电加热器
(1)启动允许:
1)密封加热器无故障。2)密封加热器不运行。
3)任意一台密封风机已启动,且时间超过4min。
(2)保护停止:
1)密封加热器故障。
2)2台密封风机故障皆停或对应出口阀未开。3)密封风温度过高。
6.吸收塔顶部排气阀
(1)打开允许:原烟气挡板全关。(2)关闭允许:净烟气挡板全开。7.增压风机
(1)启动允许:
1)至少一台冷却风机正常运转。
2)前导叶电动执行机构最小角度(5%开度)。3)入口烟气挡板1关闭。
4)出口净烟气挡板开启。
5)增压风机1出口烟气挡板开启。6)增压风机主轴承温度不大于85℃。7)增压风机主电机定子温度不大于110℃。8)电动机轴承温度不大于80℃。
9)吸收塔排空电动门关闭。
10)GGH主或辅电机投送。
11)至少1台浆液循环泵在运行中。12)引风机在运行中。
(2)停止允许:旁路挡板门在全位。
(3)保护停止:
1)增压风机运行延时60s,入口原气挡板未打开。
2)增压风机轴承振动不小于4.4mm/s,延时10s。
3)风机启动1min后,增压风机出口挡板门未打开。
4)风机启动1min后,吸收塔出口净烟气挡板门未打开。5)增压风机冷却风机都停止,延时600s。
6)增压风机主轴承温度不大于100℃。
7)增压风机主电机定子温度不大于130℃。8)电动机轴承温度不大于95℃。
9)3台浆液泵全停延时20s(旁路挡路快开时间)。8.增压风系统故障报警项目
(1)增压风机回路故障。
(2)增压风机保护装置故障。
(3)增压风机主轴承温度不大于85℃。
(4)增压风机振动大于4.6mm/s。
(5)增压风机电机轴承温度大于80℃。
(6)增压风机主电机定子绕组温度大于125℃。
(二)GGH系统1.GGH本体
(1)启动允许:
1)GGH主、辅助电机停止。
2)主、辅助电机无故障(控制回路断线、脱扣器动作)。3)GGH导向轴承和推力轴承无报警。
4)吹灰器无故障报警。5)GGH密封风机无故障。6)低泄漏风机无故障。
(2)保护停止:
1)2台增压风机都停止后60min。
2)GGH吹灰器最后一次运行间隔时间不超过10min。2.低泄漏风机
(1)允许启动:
1)低泄漏风机停运。2)低泄漏风机无故障。
3)低泄漏风机轴承温度无报警。
4)低泄漏风机电机轴承温度无报警。5)低泄漏风机电机绕组温度无报警。6)低泄漏风机进口风门全关。
(2)保护停止:
1)低泄漏风机轴承温度大于100℃,延时3s。2)低泄漏风机电机轴承温度大于90℃,延时3s。3)电机定子绕组温度大于120℃,延时3s。4)增压风机停止。
3.低泄漏风机进口风门电动阀
(1)自动打开:低泄漏风机电机启动后延时5s,自动打开到20%开度(开度可调)。
(2)自动关闭:低泄漏风机停止。4.高压水泵系统
(1)启动允许:
1)GGH选择高压水冲洗,且GGH吹灰器请求启动高压水泵。
2)GGH正常运行。
3)高压水泵入口压力大于0.2MPa。4)吹灰器无故障。
(2)保护停止:
1)入口压力小于0.2MPa。
2)吹灰器故障停运。
5.GGH系统故障报警项目
(1)GGH转速预报警。(2)GGH转速主报警。
(3)吹灰器故障。
(4)GGH密封风机故障。
(5)GGH低泄漏风机故障。
(6)GGH底部和顶部轴承油温大于70℃,高温报警。(7)低泄漏风机轴承油温大于90℃,高温报警。
(8)低泄漏风机电机轴承油温大于85℃,高温报警。(9)低泄漏风机电机绕组温度大于110℃,高温报警。(10)高压水泵入口水压力地开关动作,报警。
(11)未处理烟气侧压降大于1.5倍初始启动后的降压,报警。
(12)处理烟气侧压降大于1.5倍初始启动后的降压,报警。
(三)除雾器系统
除雾器冲洗装置按程序定期冲洗两层除雾器,以防止堵塞,减小除雾器的压力损失。
1.除雾器冲洗系统启动必须满足的条件(1)至少1台除雾器运行。
(2)吸收塔液位低于最低值。2.除雾器冲洗系统的联锁保护
(1)吸收塔液位高于最高值,执行除雾器喷水阀强制关闭。(2)吸收塔液位低于最低值,保护停用的除雾器系统重新
继续执行顺控启动程序。
3.除雾器冲洗水泵的联锁控制
(1)启动允许:
1)工艺水箱液位正常大于设定值。2)除雾器冲洗水泵出口门关闭。3)除雾器冲洗水泵A停止。4)除雾器冲洗水泵A无故障。
(2)自动启动:联锁投入且另一台除雾器冲洗水泵跳闸。
(3)保护停止:
1)工艺水箱液位小于于最小值,延时10s。2)除雾器冲洗水泵A故障。
3)除雾器冲洗水泵A运行60s内,其出口门未打开。4)除雾器冲洗水泵A其运行出口压力小于200MPa,延
时30min。
4.除雾器系统故障报警
(1)除雾器用冲洗水泵故障。
(2)除雾器上下压差大于150MPa。(四)循环泵系统
1.循环泵进口电动阀打开允许条件(1)循环泵排放阀关闭。
(2)循环泵冲洗水阀关闭。
(3)循环泵A停止。
2.循环泵进口排放阀的联锁控制
(1)打开允许:
1)循环泵排放阀全关。2)循环泵进口阀全关。3)循环泵停止。
4)循环泵冲洗水阀关闭。
(2)保护关闭:排水坑液位大于最高值。3.循环泵出口冲洗阀打开允许条件
(1)循环泵冲洗阀全关。(2)循环泵进口阀全关。
(3)循环泵A停止。
(4)循环泵A排放阀全关。4.浆液循环泵
(1)启动允许:
1)吸收塔液位大于设定值。
2)浆液循环泵进口门打开延时30s。3)浆液循环泵排放门关闭。
4)浆液循环泵冲洗门关闭。
5)吸收塔循环泵电机定子温度小于110℃。
6)吸收塔循环泵减速温度小于90℃(如果有)。7)吸收塔循环泵轴承温度小于80℃。
8)吸收塔循环泵电机轴承温度小于80℃。
(2)保护停止。
1)吸收塔液位小于设定值(4m)延时60s。2)浆液循环泵进口门未打开。
3)吸收塔循环泵电机定子温度小于120℃。4)吸收塔循环泵减速温度小于100℃。
5)吸收塔循环泵轴承温度小于90℃。
6)吸收塔循环泵电机轴承温度小于90℃。5.循环泵系统故障报警项目
(1)泵故障。
(2)泵轴温度大于90℃。
(3)泵电机轴承温度大于80℃。(4)泵电机绕组温度大于115℃。
(五)吸收塔搅拌器系统
1.允许启动
(1)吸收塔液位大于低位1。(2)搅拌器无故障。
(3)搅拌器停止。2.自动启动
吸收塔液位大于低位2。3.保护停止
(1)吸收塔液位小于最低值。(2)搅拌器故障。
(六)吸收塔石膏排出泵系统
(1)满足以下条件,吸收塔石膏排出泵保护停止(以 A泵为例,且A、B泵互为联锁备用):
1)A泵和B泵均停止。
2)吸收塔排出泵A无故障。3)吸收塔液位大于最低值。4)旋流器进口阀打开。5)泵出口阀门开、关位置正确。
(2)出现以下情况,吸收塔排出泵保护停止(以A泵为例,且A、B泵互为联锁备用):
1)A泵运行,延时60s,出口阀未打开。
2)A泵运行,且出口压力小于最低值或大于最高值,延
时10s。
3)泵进口阀打开状态失去,延时1s。4)吸收塔液位小于最小值。
(七)氧化风系统
(1)满足以下条件,氧化风机允许启动(以氧化风机 A
为例):
1)氧化风机A出口卸荷阀打开。2)氧化风机A出口阀打开。
3)氧化风机A无故障。
4)氧化风机A综合保护装置无动作。5)氧化风机A轴承温度小于85℃。6)氧化风机A电机线圈温度小于120℃。7)氧化风机A电机轴承温度小于90℃。
(2)出现以下情况,氧化风机保护停止条件(以氧化风机
A为例):
1)2台炉原烟气挡板全关。2)2台炉净烟气挡板全关。3)吸收塔顶部排气阀打开。
4)氧化空气母管减温后温度高于80℃。5)氧化风机A轴承温度小于90℃。6)氧化风机A电机线圈温度小于130℃。7)氧化风机A电机轴承温度小于95℃。
8)氧化风机A出口阀门未开。(3)氧化风系统故障报警项目:1)氧化风机A轴承温度小于85℃。2)氧化风机A电机线圈温度小于120℃。3)氧化风机A电机轴承温度小于90℃。4)氧化空气母管减温后温度高于75℃。
(八)排水坑系统(含吸收塔区、制浆区、脱水区)
1.排水泵坑
(1)允许启动:
1)排水坑液位大于低位1。
2)排水泵坑相关冲洗阀液位全关。3)排水泵坑无故障。
4)排水泵坑出口阀全关。
(2)自动启动:在液位联锁投入的前提下,排水泵液位大于高位1。
(3)自动停止:在液位联锁投入的前提下,排水泵液位小于低位2。
(4)保护停止:
1)当排水泵坑运行30s后,出口阀未打开。2)当排水坑液位小于低位2。
3)排水泵坑无故障。2.排水坑搅拌器
(1)启动允许:
1)排水坑搅拌器无故障。2)排水坑搅拌器停止。3)排水坑液位大于低位1。
(2)自动启动:在液位联锁投入的前提下,排水泵液位大于低位1。
(3)自动停止。在液位联锁投入的前提下,排水泵液位小于低位2。
(4)保护停止:
1)排水坑搅拌器故障。
2)排水坑液位小于低位2,延时10s。3.排水坑系统故障报警项目
(1)排水坑泵故障。
(2)排水坑搅拌器故障。
(3)排水坑液位大于最高值。(4)排水坑液位小于低位2。
(九)事故浆液箱系统
1.事故浆液泵
(1)启动允许:
1)事故浆液箱液位大于最高值。2)事故浆液泵无故障。
(2)保护停止:
1)事故浆液箱液位小于最低值。2)事故浆液泵电动机故障。
2.事故浆液箱搅拌器
(1)启动允许:
1)事故浆液箱液位大于最高值。2)事故浆液箱搅拌器无故障。
(2)自动启动:在液位联锁投入的前提下,排水泵液位大于低位1。
(3)自动停止:在液位联锁投入的前提下,排水泵液位大于低位2。
(4)保护停止:
1)事故浆液箱液位小于低位2。2)事故浆液箱搅拌器故障。3.事故浆液箱系统故障报警项目(1)事故浆液泵故障。
(2)事故浆液罐搅拌器故障。
(十)冲洗水系统
1.工艺水箱进水阀(用于水液位控制)
(1)自动打开:在水箱补水联锁投入的前提下,当水箱水位小于最低值时。
(2)自动关闭:在水位联锁投入的前提下,当水箱水位大于最高值时。
2.工艺水泵(以A泵为例,且A、B泵互为联锁备用)
(1)启动允许:
1)工艺水箱液位大于低位1。2)工艺水泵出口关断阀关闭。
(2)自动启动。联锁投入且B泵跳闸,B泵运行后60s工艺水管压力小于最低值,延时30s。
(3)自动停止。工艺水箱液位小于低位2。
(4)保护停止:
1)当工艺水泵运行60s后,出口阀未打开时。2)工艺水箱液位小于低位2。
3.工艺水泵回流阀
(1)打开允许:任一台工艺水泵运行。
(2)自动打开:工艺水泵出口管道压力大于最高值,延
时30s。
(3)保护打开:工艺水泵A运行60s。
(4)自动关闭:工艺水泵出口管道压力小于最低值,延
时30s。
4.工艺水吸收塔补水阀
(1)打开允许:吸收塔液位小于低位1。(2)自动打开:吸收塔液位小于低位1。(3)保护打开:吸收塔液位大于高位2。(4)自动关闭:吸收塔液位大于高位2。5.工艺水系统故障报警
(1)工艺水箱水位小于最低值。(2)工艺水箱水位大于最高值。
(十一)石灰石粉储运系统
1.电动旋转阀
(1)打开允许:
1)石灰石粉仓料位计高于最低值。2)电动插板门开。
(2)保护关闭:电动插板门关。2.电动插板门
(1)保护打开:电动旋转阀开。(2)关闭允许:电动旋转阀关。(3)自动关闭:电动旋转阀延时30s。3.石灰石粉储运系统故障报警
(1)石灰石粉仓料位小于最低值。(2)石灰石粉仓料位大于最高值。
(十二)石灰石浆液箱搅拌器
1.石灰石浆液箱搅拌器
(1)启动允许:
1)浆液箱液位大于低位1。2)搅拌器停运。
3)搅拌器无故障。
(2)自动启动:制备箱液位大于低位1。
(3)保护停止:
1)浆液箱液位小于低位2。2)搅拌器故障。
2.石灰石浆液箱系统故障报警(1)石灰石浆液箱搅拌器故障。
(2)石灰石浆液箱液位高于设定值最高值。(3)石灰石浆液箱液位低于设定值最低值。
(十三)浆液制备输送系统
1.浆液供给泵启动允许条件(以A泵为例,且A、B泵互为联锁备用)
(1)A、B浆液供给泵停止,出口阀全关。(2)A浆液供给泵无故障。
(3)石灰石浆液箱液位大于低位1。
2.浆液输送泵保护停止条件(以A泵为例,且A、B泵互为联锁备用)
(1)A浆液供给泵运行,延时60s,且出口阀未打开。(2)B浆液供给泵停止且泵出口阀开启。
(3)A浆液供给泵故障。
(4)A浆液供给泵进口阀打开失去。(5)制备箱液位小于低位2。
(6)泵运行60s后,石灰石浆液供应管压力小于最低值,或大于最高值延时30s。
3.浆液至吸收塔输送系统的联锁保护逻辑
石灰石浆液给料系统停用的条件下,如果吸收塔的pH值小于低设定值,执行系统顺控程序。
4.吸收塔浆液入口调节阀的控制
(1)输入量:烟气的流量或机组的负荷、烟气中SO2的含量、调节阀的实际开度、pH测量值、石灰石浆液流量。
(2)输出量:调节阀的开度指令信号。在浆液至吸收塔输送系统自冲洗联锁投入的前提条件下,每个60min,该控制阀强制打开60s进行管路自冲洗,然后恢复到强制打开前的强度。
(十四)二级石膏脱水系统(真空皮带脱水系统)
1.满足所有以下条件,真空皮带脱水系统允许启动(以皮带机A为例)
(1)真空皮带机A无滤布跑偏报警。(2)真空皮带机A无滤布张紧报警。(3)真空皮带机A无皮带跑偏报警。
(4)真空皮带机A无气水分离器液位无高报警。(5)滤布冲洗水箱液位无低报警。
(6)真空皮带机A真空泵密封水阀全关。(7)滤布冲洗水泵A停止。
(8)真空泵A停止且无故障。
(9)真空皮带机A变频器停止且无故障。(10)至少1台工艺水泵在运行。
(11)石膏排出泵至少1台运行。
2.出现任一以下情况,真空皮带脱水机系统紧急停止(以真空皮带机A为例)
(1)真空皮带机A真空泵停止。(2)真空皮带机A变频器停止。(3)2台工艺水泵均停止。
3.出现任一以下情况,真空皮带机保护停止(以真空皮带机A为例)
(1)真空盒密封水流量低,延时20s。
(2)滤布冲洗流量低,延时20s。
(3)真空皮带机A紧急拉绳开关动作。(4)真空皮带机A无滤布跑偏报警。(5)真空皮带机A无滤布张紧报警。(6)真空皮带机A无皮带跑偏报警。
(7)滤饼厚度大于45mm,延时30s。
(8)真空泵A跳闸。
(9)2台滤布冲洗水泵停止。4.皮带脱水机速度控制
(1)被调量:滤饼厚度。
(2)调节量:皮带机变频器控制信号。5.真空泵(以皮带机A为例)
(1)启动允许:
1)真空泵A密封水阀全开。
2)真空泵A密封水无流量低报警。
3)真空皮带机A汽水分离器液位无高报警。
4)真空泵 A停运,且真空泵 A密封水阀关闭时间超
过600s。
5)真空皮带机A变频器运行。
(2)保护停止:
1)汽水分离器A液位高报警。
2)真空泵A密封水流量低报警,延时20s。3)真空泵A故障。
4)真空皮带机A变频器停止。
6.真空皮带脱水系统故障报警(以皮带机A系统为例)(1)真空皮带机A真空泵故障。
(2)真空皮带机A变频器故障。(3)滤布冲洗泵A故障。
(4)滤布冲洗水流量低。(5)滤饼冲洗水流量低。(6)密封水流量低。(7)真空泵A密封水流量低。
(8)真空皮带机A汽水分离器液位高报警。(9)滤饼厚度异常。
(十五)滤液水系统(回收水系统)
1.滤液水箱搅拌器
(1)启动允许:搅拌器无故障且滤液水箱液位大于低
位1。
(2)自动启动:滤液水箱液位大于低位1。(3)自动停止:滤液水箱液位小于低位2。
(4)保护停止:搅拌器电机故障或滤液水箱液位小于低
位2。
2.滤液水泵(以滤液水泵A为例)
(1)启动允许:
1)A、B泵均停且出口阀关闭。2)滤液水箱液位大于低位1。3)滤液水箱搅拌器运行。
4)A泵无故障。
5)滤液水泵A冲洗阀全关。
(2)自动启动:滤液水泵A联锁投入时,滤液水泵B(运行泵)停止。
(3)保护停止:
1)当滤液水泵A运行60s,该出口阀未打开时。2)水泵A运行,进口阀打开状态失去。
3)滤液水泵 A运行,且出口压力小于0.18MPa,延
时10s。
4)当滤液水箱液位小于设定值(800mm)。5)滤液水泵A故障。
6)滤液水泵B停止,且滤液水泵B出口阀打开。
7)当滤液水泵A运行60s后,滤液水泵A出口压力高或
低,延时30s。
(4)联锁保护:滤液水泵联锁投入,滤液水泵A、B互为热备用。
3.吸收塔滤液水给水控制
(1)打开允许:吸收塔水位低。
(2)自动打开:滤液水箱液位大于最高值。(3)自动关闭:滤液水箱液位小于最低值。(4)保护关闭:吸收塔水位高。
4.工艺水至滤液水箱给水
(1)打开允许:滤液水箱液位小于低位1。(2)自动打开:滤液水箱液位小于低位1。(3)自动关闭:滤液水箱液位大于最高值。5.滤液水系统故障报警
(1)滤液水箱搅拌器故障。(2)滤液水泵A故障。(3)滤液水泵B故障。(4)滤液水箱液位小于最低值。(5)滤液水箱液位大于最高值。
(十六)废水处理系统
1.废水泵(清水泵参照执行,并以A泵为例,且A、B泵互为联锁备用)
(1)打开允许:废水箱液位大于低位1。
(2)自动打开:A泵联锁投入,B泵(运行中)停止。(3)关闭允许:废水箱液位小于低位2。
(4)自动关闭:废水箱液位小于低位2。
2.污泥输送泵(以A泵为例,且A、B泵互为联锁备用)(1)打开允许:澄清/浓缩器污泥出口阀A打开。
(2)自动打开:A泵联锁投入,B泵(运行中)停止。
(3)关闭允许:澄清/浓缩器污泥出口阀A关闭。3.废水系统故障报警
(1)各溶液箱液位低。
(2)各加药泵/输送泵故障。(3)各搅拌器故障。
(4)压滤机故障。
第四节 自动调节
FGD工艺过程中的主要调节回路有:脱硫效率控制,吸收剂浆液流量控制,烟气流量控制,吸收塔反应池液位和浆液密度控制,除雾器冲洗控制,真空皮带过滤机走速控制等。下面对部分主要调节回路作简要介绍。
一、脱硫效率控制
脱硫效率(或SO2排放量)是FGD工艺过程中要监控的主要性能变量,无论机组在稳定工况下运行,还是处于变负荷或燃料含硫量变化时,脱硫效率的调节系统必须使脱硫效率满足环保法规的强制性要求,同时,还要满足运行经济性要求。
可以用来控制脱硫效率的工艺变量是有限的,以下工艺变量直接影响脱硫效率,因此可以调节这些工艺变量来控制系统的脱硫效率:
(1)处理烟量与旁路烟量。
(2)吸收塔循环浆流量(即吸收塔循环泵投运台数)。(3)吸收塔循环浆液pH值。
(4)吸收塔循环浆液中化学添加剂浓度。
(5)早期FGD系统有一炉多塔,因此投入运行的吸收塔台数也是控制脱硫效率的工艺变量。
表1741汇列了可以用来控制FGD系统脱硫效率的调节方案,对这些调节方案的优缺点进行了比较。从该表可看出,所有的方案都采用了FGD系统出口跳浓度作为主要输入参数,从位于烟囱入口的 CEMS获得此主参数的过程值。
表1741
控制SO2脱硫效率的方法

注 1.控制目标:根据SO2排放要求和尽量降低脱硫费用的原则来维持SO2的脱除。
2.工艺过程发生变化的原因:锅炉负荷和燃料含硫量。
需要指出的是,随着FGD技术的发展,污染物排放标准的日趋严格,目前的FGD系统几乎都是采用吸收塔循环浆液pH值来控制系统的脱硫效率,其他调节方案,要么已不再采用,要么仅作为辅助手段用来控制脱硫效率。
(一)调节吸收塔处理烟量控制系统脱硫效率
采用改变吸收塔处理烟气量来控制脱硫效率的方法(表1741中第一种方案)必须满足两个条件:①FGD系统的设计可以使来自锅炉的烟气部分经旁路排入烟囱;②在烟囱入口处测得的系统总脱硫效率超过规定值。例如某电厂FGD系统设计在锅炉ECR工况时,吸收塔处理锅炉额定排烟量的85%,吸收塔设计脱硫率为95%,允许15%的原烟气经旁路烟道与处理后的烟气混合后排入烟囱,规定在设计工况下系统总脱硫率不低于80%。当锅炉低于额定负荷时,如果吸收塔处理的烟气量和脱硫率保持不变,那么总脱硫率将高于规定的80%,这时可以在保持吸收塔脱硫率不变的情况下,通过减少吸收塔的进烟量来维持80%的总脱硫效率;也可以不改变吸收塔进烟量,降低吸收塔脱硫率(例如降低运行pH值,以达到提高吸收剂利用率的效果)来保待80%的总脱硫率。

图1741 调节吸收塔处理烟量控制系统脱硫率的调节方式
根据是否设置脱硫增压风机(BUF),可以有两种调节旁
路烟量的方法,如图1741所示。图1741(a)是
当采用湿烟囱工艺,不设置BUF的工艺流程,旁路烟道装有开度可调挡板,通过调节旁路挡板开度连续改变旁路烟气流量。旁路挡板通常设计成单百叶窗式或双百叶窗式。根据烟囱入口实测SO2浓度与烟囱入口SO2浓度给定值之间的差值来调节旁路挡板的开度,从而实现对旁路烟气流量的调整。当旁路烟量偏大,总脱硫效率低于规定值,则自动减小旁路挡板开度,增加进入吸收塔的烟气量,最终使总脱硫率不低于规定值。吸收塔的脱硫率则用另外的调节回路,根据吸收塔浆液pH值或吸收塔入/出口SO2浓度来控制。
在图1741(b)中,脱硫风机布置在FGD系统的出口处(也可布置在入口),旁路烟道不设置挡板,通过脱硫风机入口调节风门开度来控制吸收塔入口烟气流量,同时使旁路
烟气流量跟随变化。当锅炉排烟量发生变化时,前馈信号使风机风门的开度即时作出响应,对风门开度进行粗调,改变进入吸收塔的烟量;烟囱入口SO2浓度与烟囱入口SO2浓度给定值的偏差经烟囱入口SO2调节器输出反馈信号,对风机风门开度进行微调,并最终确定风门开度,使总脱硫率稳定在某一预期值上。同样,吸收塔脱硫效率由另外的调节回路控制。
图1741所示两种调节方式可以用于湿烟囱工艺或采用GGH的工艺流程,由于采用旁路原烟气加热已脱硫的低温湿烟气会造成烟气混合区结构材料的严重腐蚀以及排烟脱硫标准的日趋严格,这种调节方式在欧、美、日已基本不再采用了。另外,温度较高的原烟气与脱硫后的饱和湿烟气或与经再加热器加热后的清洁烟气混合时会出现分层现象,若无使烟气均匀混合的可靠措施,很难准确测定烟囱入口SO2浓度,从而会影响调节回路的准确性。
(二)调节吸收塔循环浆液流量控制脱硫效率
表1741中控制脱硫效率的第二种调节方式是通过调整吸收塔循环泵的投运台数来改变吸收塔循环浆流量,由此来提高或降低L/G比。这种方法更多地用来适应吸收塔入口烟气流量发生大幅度变化的工况,使L/G维持在一定范围内。图1742是我国某电厂FGD喷淋吸收塔的锅炉负荷、喷淋投运层数与脱硫效率的关系,从该图可看出,当锅炉负荷降
至30.2%~63%范围,维持脱硫率不低于94.7%,可减少1~
2个喷淋层。这种方式实行起来简单,通过手动操作,吸收塔脱硫效率能迅速地随L/G变化,对工艺化学过程没有明显的影响。但这种调节方式仅适合一台循环泵对应一个喷淋层的喷淋吸收塔和填料塔,不适合吸收塔循环泵出口管道采用母管制的吸收塔。对采用母管制的喷淋塔,减少循环泵投运台数将影响喷嘴的压力和流量,从而会影响喷嘴的喷雾特性,对液柱塔来说,通常会影响液柱高度并使液柱之间露出空隙,易造成烟气“短路”。液柱塔为了实现在锅炉低负荷时也可以减少循环泵投运台数,又不至于出现上述情况,近年采用增加循环泵的设计台数,并适当提高额定工况下液柱高度的方法来实现这一目的,但这样可能会明显增加循环泵的设备费用和耗电量。
另外,这种调节方式通常仅当喷淋塔有3~5个喷淋层的情况下,可减少泵的投运数1~2台,对有4~6台循环泵的液柱塔可减少1~3台。当锅炉负荷下降时,如果不减少循环泵的运行台数,也不调节其他过程变量,在大多数时间里。FGD系统脱硫率将超过规定值。
这种调节方式主要是用于锅炉低负荷时,在保证脱硫效率的前提下,节省能耗,并不作为一种控制系统脱硫效率的方法。
(三)调节吸收塔循环浆液pH值控制脱硫效率
表1741所列第三种方法是通过调节吸收塔反应罐浆液pH值来控制脱硫率,调节方式如图1743所示。在多数情况下,改变浆液pH值将改变SO2的脱除效率,但富镁石灰FGD工艺(MEL)是个例外,因为这种工艺中SO2的吸收可能受气膜控制。在本调节方式中,通过改变供入反应罐吸收剂浆液的流量来提升或降低循环浆液pH值,从而使SO2脱除效率随pH值改变。吸收塔循环泵投运台数确定后,在负荷稳定时,通过人为或自动调整pH值给定值可以达到预期的SO2脱除效率。当手动方式时人为设定pH值给定值,烟囱入口SO2浓度信号不参与调节。自动方式时,SO2调节器对烟囱入口SO2测值和预期的SO2浓度进行比较,向pH值调节器输出pH值给定值pHsp,pHsp的调节范围受某一高值和低值的限制。浆液pH值与吸收剂浆液流量构成的串级调节系统

图1742 我国某电厂喷淋塔锅炉负荷、喷淋层投运数与脱硫率的关系

图1743 通过调节吸收塔反应罐浆液pH值来控制脱硫率
的调节原理和特点在前面已作了详细介绍,在此不再复述。这种调节方式具有连续可调节性,可以使FGD装置在满足SO2排放要求的前提下,以最低pH值运行,达到节约吸收剂耗量,提高石膏品质的目的。由于采用了pH值与浆液流量的串级调节,大大减少了浆液流量波动对pH值的影响。但是,由于反应罐浆液体积庞大,浆液pH值响应相对较慢,但在锅炉负荷和燃料含硫量大幅度波动时间不超过1~2h的工况下,这种调节方式是非常有效的。
当在低pH值下运行时,调节pH值对脱硫率的改变很灵敏,而在高pH值运行时,则显得有些迟缓,也就是说pH值对脱硫率的调节是非线性的。另外,调节pH值会影响工艺过程的其他参数,如氧化效率,石灰石利用率和石膏脱水性等。
(四)调节化学添加剂浓度控制脱硫率
一个FGD系统可能在设计时考虑了或未考虑采用化学添加剂,在这两种情况下,化学添加剂的应用都可以提高脱硫率,节省吸收剂和降低循环泵的电耗(降低循环浆流量)。采用化学添加剂的经济效益取决于添加剂的价格和耗用量。由于反应罐的体积较大以及添加剂的消耗量非常低,与改变吸收塔喷淋流量或改变浆液pH值相比,改变化学添加剂的浓度是一个很慢
的过程,因此,不能随时甚至不能每天调整化学添加剂的浓度。通常使化学添加剂浓度保持在一个预先选定的范围内,以获得最佳经济效益。如果预计燃料含硫量在较长的时间内将发生明显改变,或者用其他控制手段不能满足所要求的脱硫效率时,才改变添加剂的浓度。
(五)调节吸收塔投运台数控制脱硫效率
表1741所列的最后一种方法是早期建设的FGD系统采用一炉配备多个吸收塔的情况下,根据锅炉负荷的变化来改变吸收塔模块的投运台数,以保持投运的吸收塔具有最佳烟气流速,从而提高单塔或总脱硫效率。这种方法通常在锅炉负荷大幅度变化并持续数小时以上才考虑改变投运吸收塔的台数。吸收塔投运台数的确定不是自动进行的,而是操作人员根据经验或FGD供应商提供的习惯做法来确定吸收塔最佳运行台数。
随着FGD技术的发展,现在不仅不再需一炉多塔,而且是多炉一塔,这种调节吸收塔投运台数控制脱硫效率的方法已转变成多炉一塔设计,当其中一炉停留时,调整吸收塔循环浆流量来控制脱硫效率。
二、吸收塔浆液流量控制
表1742列出了4种控制吸收剂给浆量的方法,并简单比较它们的优缺点,下面依次分析这4种方法的特点。
(一)反应罐pH值调节法
反应罐pH值调节吸收剂给浆流量的方法如同表1 74 1第三种控制脱硫率方法中的手动调动方式(见图1743),但不设SO2调节器,人为给定pH值凋节器的设定值pHSP,对pH值调节器设置高限和低限值,采用pH值反馈简单调节回路,调节吸收剂给浆量使反应罐浆液pH值达到给定的设定值。
这种pH值调节回路除了用来控制脱硫效率外,还必须将反应罐浆液pH值控制在一定范围内,使得既要达到预期的脱硫效率又要获得吸收剂最佳利用率,同时还要考虑pH值对氧化、结垢、副产品石膏品质和腐蚀环境的影响,即pH值不能太高或太低。不同的脱硫装置有自己最佳pH值限制范围,这一最佳pH值设定值范围需通过性能试验和根据运行经验来确定。
需要指出的是,反应罐pH值调节法是假定工艺过程的最佳pH值设定范围不随时间改变,但实际上其他工艺参数的变化,例如吸收剂石灰石粒度的改变和浆液中可溶物浓度的变化(特别是 Mg2+)都会逐渐改变浆液pH值与吸收剂利用率之间的相互关系。因此,需要定期进行化学监测,监控工艺的化学过程,检验pH值控制范围是否合适。
表1742
吸收剂给浆量控制方式

注 1.控制目标:按要求的脱硫效率和尽量降低脱硫费用的原则来调节吸收剂给浆量。
2.引起工艺过程变化的原因:锅炉负荷和燃料含硫量。
仅采用一个简单的pH值反馈调节系统来控制吸收剂供浆量的调节方式存在一些不足之处。在石灰石FGD工艺中,反应罐浆液中一般含有大量未反应的石灰石,改变吸收剂供浆量,浆液pH值响应较慢。而且,吸收剂给浆量与反应罐浆液pH值的关系是非线性的,在正常运行pH值范围(5.2~5.5)的较低端,改变吸收剂给浆量,反应罐浆液pH值会随之发生明显的变化。当运行pH值为6.0左右时,加入大量的吸收剂浆液,pH值提升也非常小。而且以高pH值运行时,pH值测值的一个小偏差就会造成向反应罐加入过量的吸收剂浆液。
对于石灰FGD工艺,浆液的碱度主要由可溶性亚硫酸盐来提供。浆液中未反应的过量吸收剂很少,当石灰浆给量改变时,反应罐浆液pH值会迅速做出响应。因此,一般采用pH值反馈简单调节回路就够了。
(二)入口SO2负荷和反应罐pH值调节法
1.入口SO2负荷和反应罐pH值调节法的基本原理
入口SO2负荷和反应罐pH值调节法是表1742所列的第二种调节吸收剂给浆量方法,其调节原理见图17 44。在这种调节回路中,仍以反应罐浆液pH值作为反馈控制信号,采用吸收塔入口SO2负荷信号(入口烟气流量与入口SO2浓度的乘积)作为前馈信号,这样可以改善调节回路的响应时间,防止由于pH值的测量差错造成石灰石浆液给量出现较大的偏差。pH值调节器和石灰石浆流量调节器仍构成串级调节回路。在这种调节方式中,吸收剂给浆流量的设定值与吸收塔入口SO2负荷成正比。可以用布置在FGD系统入口烟道上的、单独的SO2分析仪和烟气流量计或由锅炉给出的排烟流量信号来确定入口SO2负荷,国外还有用位于给煤机处的燃煤含硫在线连续分析仪来确定入口SO2负荷,而目前大多通过CEMS来获得这一前馈信号。根据反应罐浆液pH值来微
调吸收剂给浆量,即在较小的范围内增减给浆量。这种调节方式使吸收剂给浆流量可以迅速跟踪锅炉负荷和燃煤含硫量的变化,获得较好的响应,同时仍可使循环浆液的pH值保持在一个合适的变化范围内。由于选用了吸收剂浆液流量为副调节参数,减少了浆液流量波动对pH值的影响。如果考虑入口烟气参数对烟气流量的影响,可以根据入口烟气温度和湿度来修正入口烟气流量。同样,也可以根据吸收剂品质和密度来修正给浆流量。

图1744 吸收剂给浆量前馈(入口SO2负荷)/
反馈(反应罐pH值)调节系统
由于入口SO2负荷和反应罐pH值调节方法具有上述优点,而在FGD系统中得到了广泛的应用。目前世界上较大的FGD供应商都以这种调节方式为基础,根据各自的设计经验和习惯,考虑影响因素的不同,作了些改进。下面将介绍德国斯坦缪勒、鲁奇能捷斯和日本三菱公司设计的吸收剂给浆量调
节方式。
2.三家FGD公司吸收剂浆液流量控制方法
图1745和图1746分别是德国斯坦缪勒公司和鲁奇能捷斯公司实际采用的石灰石浆流量调节系统,这两种调节方式都属于上述前馈/反馈调节系统。在斯坦缪勒公司的前馈/反馈调节系统中,根据烟气参数对原烟气流量进行了修正,根据石灰石品质和石灰石浆液密度修正了石灰石浆液的给浆量。在鲁奇能捷斯公司的调节方式中采用了多冲量(三冲量)调节,所谓多冲量调节是指,在调节系统中有多个参数信号经过一定的运算后共同控制调节阀,以使某个被调工艺参数有较高的调节质量。图1746是石灰石浆给量的三冲量调节系统,这三个冲量信号是:脱硫量偏差信号(前馈信号)、pH值偏差信号(反馈信号)和石灰石浆流量信号。在该调节系统中,依据吸收塔循环泵投运台数来确定脱硫率给定值,脱硫率的过程值与给定值的偏差经死区环节器9限幅后送至比较器18,死区环节9的作用是避免脱硫效率大幅度波动。pH值给定值根据入口SO2负荷来确定,pH值偏差(比较器15的输出)不直接用来调节石灰石浆流量,这样可以防止系统pH值波动过大。石灰石浆流量信号参与调节,有利于克服由于供浆压力波动引起的浆液pH值变化。

图1745 德国斯坦缪勒公司为我国FGD装置
设计的石灰石浆流量调节回路概念图

图1746 德国鲁奇能捷斯公司FGD装置石灰石浆流量调节回路概念图
日本三菱公司设计的石灰石浆液流量控制方法(见图1 747)的特点是,通过一个选择器11将入口SO2荷前馈/反应罐pH值反馈调节系统与入口SO2负荷前馈/出口SO2浓度反馈调节系统组合在一起,使调节较为灵活,为操作人员提供了控制方式的选择。
这种调节方法仍然以吸收塔入口SO2负荷作为前馈信号,经选择器11可人为选择反应罐浆液pH值作为反馈信号来控制脱硫率和石灰石浆流量,这时出口SO2浓度不参与调节。或者选择出口SO2浓度(亦即脱硫率)作为反馈信号来控制。在后一种调节方式下,SO2调节器14选择串级(CAS)方式,而pH值调节器10选择自动方式,当出口SO2浓度(SPV)高于出口SO2浓度设定值(SSP)时,高选器12自动选择SO2调节器14的输出作为反馈信号,只有当SPV≤SSP时,pH值才有可能被选为反馈信号。pH值设定值pHSP需人为设定,一般
选择SPV≈SSP时的pH值过程值pHPV为pHSP。当锅炉负荷稳
定、FGD系统运行稳定时,适合选择pH值作反馈控制,在达到规定脱硫率的前提下,逐渐降低pH值设定值,以获得较高石灰石利用率和石膏品质。选择出口SO2浓度控制石灰石
浆流量时,由于采用了高选器12,可以在维持脱硫效率不低于预期值的情况下,保持浆液pH值稳定。
这种调节方式的另一个特点是,脱硫效率设定值ηSO2随锅炉负荷改变,锅炉负荷低,设定值ηSO2高,这使得在负荷变化时,可以保持浆液pH值和浆液中过剩CaCO3含量不变,从而使得石膏副产品的质量保持稳定,也使得脱硫率能很快跟踪负荷变化。从图1748可看出上述特点的基本设计思想,假
定锅炉负荷为75%时ηSO2=95.5%,浆液pH=pH1,浆液中过剩CaCO3浓度为X1;当负荷升至100%,如果仍维持ηSO2=95.5%,那么浆液pH值应提升至pH2,CaCO3浓度提高到X2,
由于反应罐浆液体积很大,注入大量石灰石浆液短时也无法达到X2,而且浆液CaCO3浓度的变化还将影响石膏质量的稳定。
如果将负荷75%时的ηSO2设定为97.5%,当负荷提升到100%时,ηSO2取95.5%,那么可以维持浆液pH值和CaCO3浓度始
终分别为pH2和X2,并且脱硫率能迅速跟踪负荷的变化。石膏质量也能保持稳定。由此,图1747中函数发生器6f(X2)的函数关系示意图如图1749所示。

图1747 三菱重工FGD系统脱硫率和石灰石浆液流量控制概念图
1—入口SO2浓度传感器;2—锅炉负荷数据收集器;3—比值设定器;4—乘法器;5—锅炉负荷与烟气流量函数发生器;
6—烟气流量与(1-ηSO2)函数发生器(ηSO2;脱硫率);7、8—pH值传感器;9—pHA/pHB选择器;10—pH值调节器;11—出口SO2/pH值控制方式选择器;12—高选器;13—出口SO2浓度传感器;
14—SO2调节器;15—加法器;16—流量调节器;17—石灰石浆流量传感器;18—调节阀

图1748 脱硫率设定值ηSO2与浆液
pH值、CaCO3浓度关系示意图

图1749 烟气流量与(1—ηSO2)关系示意图
三菱为某电厂设计的石灰石浆液流量控制方案中,不实测系统入口烟气流量,而由主机提供锅炉负荷与排烟流量关系,也不对烟气状态和石灰石品质(如石灰石浆液密度等)进行修
正,从应用情况来看,通常情况下这些因素的影响不大。但是,当石灰石浆液密度偏离控制值较多时,仍会影响调节性能。随着强制性要求应用CEMS,采用实测烟气流量,并用烟气参数和石灰石浆液密度分别修正烟气和石灰石浆液流量能进一步提高调节品质。
(三)反应罐pH值和出口SO2浓度调节法
这种调节方法即表1742所示第三种控制方式,与表1741中第三种控制SO2脱硫率的方法相同(见图1 743)。反应罐pH控制回路用来使反应罐浆液pH值为某一设定值,但pH值设定值本身受保持烟囱入口SO2浓度(亦即脱硫率)为预期值的控制。这种调节方法的优点是能获得吸收剂最高利用率,因为供入的吸收剂浆量仅足够维持所要求的脱硫效率。但这种调节方法不能即时跟踪锅炉负荷,当锅炉负荷短时间内上升时,脱硫效率往往会下降。
(四)反应罐浆液中未反应碳酸钙含量调节法
表1742列出的最后一种控制石灰石浆液流量的方法是采用一种在线浆液连续分析仪测定反应罐中过剩CaCO3含量,根据测出的过剩CaCO3含量的信号来调节石灰石浆液流量,使浆液中过剩CaCO3量为一预定值。浆液CaCO3分析仪(又称为CaCO3传感器)由以下部分组成:①采样器:以固定流量连续采集循环吸收浆样;②反应器:向样品中添加
H2SO4,产生CO2气体;③CO2气体分析仪:用以测定产生
的CO2量;④控制单元:计算、显示循环吸收浆液中CaCO3浓度并提供相关的输出信号。
采用此控制方法基于这样一种情况,当锅炉负荷和烟气SO2浓度急速度变化时,采用浆液pH值控制方法很难维持脱硫性能的稳定。这是因为在锅炉负荷变化时,即使维持循环吸收浆液的pH值不变,浆液中未反应的CaCO3含量也不相同。
脱硫负荷高时未反应的CaCO3浓度高,脱硫负荷低时未反应的CaCO3浓度低,原因主要是吸收剂在反应罐中的停留时间不同造成的。脱硫负荷高时,供给吸收剂流量大,停留时间要短些,CaCO3溶解不充分,结果未反应完的CaCO3浓度变高。脱硫负荷低时,情况正好相反,结果浆液中未反应的CaCO3浓度变低。循环浆液中未反应的CaCO3浓度反映了浆液吸收容量(或吸收能力)的大小。因此,当负荷变化时,及时测出循环浆液中未反应的CaCO3浓度,并根据要求的脱硫率(即浆液中需维持未反应CaCO3浓度)调整吸收剂浆液流量。这样,不仅能在保持脱硫率稳定的情况下跟踪锅炉负荷,还能使石膏质量稳定。而且,pH值测量差错不会造成浪费吸收剂浆液,浆液pH值与吸收剂利用率相互关系的改变也不会影响这一控制方式。
据有关资料介绍,如果配以叶距可调式循环泵,连续调节循环吸收浆液流量来维持脱硫率,就可以获得最佳控制系统。这种控制系统的优点是:①提高了脱硫调节的可靠性;②改进了对锅炉负荷的跟踪能力;③石膏副产物的纯度稳定;④节能。但是,目前这种浆液在线连续分析仪仅在个别装置中试用,仍处在研发阶段。
上面介绍的吸收剂浆液流量控制方法中都采用了吸收剂浆液流量计和流量调节器。在实际调节回路中,并不直接用pH值调节器的输出来控制调节阀的开度,而是采用串级调节方式,pH值或SO2调节器的输出作为流量调节器的流量设定值FSP,流量计将浆液流量的过程值FPV输入流量调节器,调节阀的开度受FSP与FPV的差值控制。采用这种串级调节可以改善调节系统的响应特性,当由于压力变化或阀门磨损等原因造成吸收剂浆液流量波动时,流量调节器可以迅速进行补偿,使流量稳定,而无需等到由这些原因造成反应罐浆液pH值发生变化后再调整调节阀的开度。另外操作人员还可以根据流量计显示的流量值来发现、查找控制系统的其他问题,例如pH值测量偏差,调节阀故障等。
三、烟气流量控制
烟气流量控制指对引入系统烟气流量的控制方法。对烟气流量控制方法的要求是,能将要求脱硫的烟气量引入FGD系统,而且能迅速跟踪锅炉负荷变化,BUF的启、停和运行不能影响锅炉炉膛工作压力。烟气流量控制方法与FGD系统设计处理烟气量以及旁路烟道是否设置挡板有关。
1.FGD系统处理烟气量时对烟气控制系统的影响
为了使FGD系统出现故障停机时不影响发电机组的正常运行,一般都设置了旁路烟道,显然烟气控制系统会因旁路烟道是否设置挡板,FGD系统处理锅炉全部或部分排烟而有所差别。
当FGD系统处理锅炉部分排烟时,如图1741所示的两种烟气控制方法,其中图(a)是采用调节旁路挡板开度来控制引入FGD系统的烟气流量,当锅炉引风机(ID)对FGD系统有足够压头时,可以省去BUF。图(b)旁路烟道未设置挡板,引入FGD系统的烟量通过BUF来控制,BUF的位置可以布置在系统的A位或D位置上。
当FGD系统处理锅炉全部排烟时,为避免由于FGD系统对烟气流量控制不当而引起锅炉内爆或外爆,必须使FGD烟气流量控制与锅炉燃烧自动控制系统保持协调,图174 10示出了可供采用的三种典型的烟气控制系统:
(1)旁路烟道不设挡板,要求FGD系统处理锅炉全部排烟。如图17410(a)所示,BUF需吸入锅炉全部排烟量的105%,其中5%的烟量是经旁路烟道返回至系统入口的清
洁烟气。如果没有一定量的清洁烟气返回至系统入口,很难避免部分原烟气经旁路烟气排入大气。由于旁路烟道未设置挡板,处于常开状,对锅炉运行是安全的。但是,BUF容量和电耗因有5%的烟气循环和旁路烟道的阻力而较旁路烟道关闭系统的高5%。另外,当返回至系统入口的湿烟气流量较大时,会对处于A位置的脱硫风机造成腐蚀。
(2)旁路挡板关闭、BUF控制全部待处理烟气。如图1 7 4 10(b)所示,旁路挡板关闭运行,锅炉全部排烟由BUF引入FGD系统。当旁路采用单百叶窗式挡板时,大约不超过1%的清洁烟气经旁路烟道返回系统入口,以防止原烟气经旁路挡板向清洁烟气侧泄漏,此时BUF必须受旁路挡板两侧压力差控制,并保持此压差为一恒定值。当旁路采用双百叶窗挡板、充气密封时,BUF可以不受旁路挡板两侧压差控制。这种烟气控制系统要求旁路挡板有很高的可靠性,在FGD系统事故时,能立即开启而不影响锅炉。
(3)旁路挡板关闭,ID控制全部待处理烟气流量。如图
17410(c)所示,旁路挡板关闭运行,ID对FGD系统有
足够压头,省除了BUF,ID控制锅炉全部排烟进入口系统,ID的运行仅受锅炉送风量和炉膛负压控制。当然,ID也可以布置在FGD系统的出口侧。这种控制烟气流量的方法多应用于湿烟囱工艺。

图17410 FGD系统处理全部烟气的烟气控制方式
2.烟气流量控制方法
下面介绍FGD系统处理锅炉全部排烟时的烟气流量控制方法。对这种烟气流量的控制方法可以分成两类:一类是旁路烟道不设挡板,用锅炉负荷信号来控制进入FGD系统的烟气流量,这种控制方法适合图17410(a)所示的工艺流程。锅炉负荷信号转变成锅炉烟气流量信号,为防止烟气经旁路烟道短路进入烟囱,引入FGD系统的烟气流量应在锅炉排烟量的基础上增加5%,烟气流量与BUF调节风门开度信号去控制BUF开度。显然,这种烟气流量控制方法最简单,对锅炉运行也最安全,但BUF的电耗大。另一类控制烟气流量的方法是旁路挡板关闭运行,采用烟气压力来控制烟气流量。这种控制方法适合图17410(b)所示的工艺流程,但
BUF不限于布置在A位置。在这种控制方法中,通常采用锅炉负荷信号或锅炉炉膛压力和ID开度作为烟气流量控制回路的前馈信号,采用旁路挡板两侧压差或ID出口烟道的烟气压
力为反馈信号。下面介绍这种控制方法在三个FGD系统中的应用实例。
图17411(a)所示烟气流量控制是以锅炉负荷信号

图17411 烟气压力控制FGD烟气流量的3种应用实例
为前快(F.F)控制信号,以旁路挡板两侧压差为反馈(F.B)控制信号。锅炉负荷信号经比值设定r1,函数发生器G(X)转变成烟气流量信号,后者再经比值设定器r2、函数发生器G(X)转变成BUF风门开度信号。当锅炉负荷发生变化时,BUF风门开度立即根据前馈信号作出响应,并根据旁路挡板两侧压差设定值自动调整BUF风门开度,使挡板两侧压力保持平衡。旁路挡板两侧的差压设定值为0Pa,当采用单百叶窗式挡板时,为防止原烟气经旁路泄漏至清洁烟气一侧,挡板下游侧与上游侧差压设定为0~100Pa。
BUF是在锅炉投运稳定并停止烧油助燃后启动,BUF的启动可以经选择器选择手动或自动启动方式。但为稳妥起见,主张手动启动。风机启动顺序因风机类型不同而不同,可按风机制造厂的启动步骤执行。风机带一定负荷后,逐步关闭旁路挡板,同时增加BUF负荷,待稳定后再进一步关闭旁路挡板。对于旁路挡板,有的将其设计成3组,先上后下最后关闭中间一组挡板,但目前更多是设计成1~2组,具有连续开度调节
及15~20s快开功能。
图17411(b)所示烟气流量控制系统有两个调节回路;差压调节回路和烟气压力调节回路。BUF启动时采用差压调节回路。当缓慢关闭旁路挡板时,挡板两侧压差控制BUF的导向叶片缓缓开启,维持挡板两侧为恒定压差。当挡板关闭后,自动切换成根据BUF入口烟气压力来控制BUF,并维持此烟气压力为设定值。此压力设定值一般为-500~0Pa。烟气流量控制回路中,通过高选器来选择ID导向风门开度或炉膛压力作为前馈信号。在有些控制回路设计中,也有选取控制引风机导叶开度的信号作为BUF的前馈信号。
图17411(c)所示控制回路可以完成BUF的自动启动,BUF动叶的开启和旁路挡板的关闭需手动操作,即自
动程序完成系统入口挡板开启→系统出口挡板开启→BUF动叶以最小角度启动。然后在手动逐步调大风机动叶角度的同时,逐步关小开度可调节式旁路挡板,控制BUF上游侧烟道烟气压力在0~500Pa左右,当旁路挡板关闭95%时,将调节回路切至自动控制方式,然后全关旁路挡板,BUF动叶角度将自动跟踪锅炉负荷和烟气压力变化。
上述三种控制烟气流量方法均能满足锅炉和FGD系统运行要求,连续跟踪锅炉负荷,不影响锅炉炉膛压力。
四、吸收塔反应罐液位和浆液密度控制
在石灰或石灰石FGD工艺中,吸收塔反应罐液位和浆液密度是两个重要的控制参数。在大多数FGD设计中,吸收塔的水平衡是负平衡,即吸收塔中蒸发至烟气中的水分、废水处理系统外排水量以及脱水副产物带离系统的水分超过进入吸收塔模块的固定水流量。固定水流量包括制备吸收剂浆液所消耗的工业水泵、搅拌器和水环式真空泵等的密封水,除雾器、氧化布气管和吸收塔入口干/湿界面冲洗水。控制反应罐液位实质上就是维持这一水平衡。维持反应罐液位所需要的平衡水来自回收水罐的回收水,工艺回收水则来自脱水系统的澄清溢流水,旋流器的溢流液和过滤机的滤液。
维持反应罐正常液位可以保证浆液有适当的停留时间,也有利保持浆液密度的稳定,液位过低可能造成循环泵吸入空气而降低效率和引起气蚀,液位过高对逆流塔可能造成浆液漫入吸收塔入口烟道,进入GGH。
维持反应罐浆液密度的稳定,对脱硫效率、固体物停留时间、石膏结晶、石膏纯度和防止结垢有直接影响。
表1743汇列了控制反应罐液位和浆液密度的七种方法,对这七种方法的优缺点作了简单的比较。图174 12是前六种控制方法的调节回路图。现依次作简要介绍。
表174 3
控制反应罐液位和浆液密度方法

续表

注 1.控制目标:保持反应罐正常液位和获得最佳浆液密度。
2.引起工艺过程变化的原因:锅炉负荷和燃料含硫量。
3.方法七中仅讨论液位控制方法,浆液密度控制可以采用上述任一种方法。
1.溢流控制反应罐液位和用回收水控制浆液密度
这种控制方法如图17412所示,经过溢流管将超过溢流管最高点以上的浆液从反应罐中排至溢流浆池,使罐体液位始终低于溢流高度。吸收塔出浆泵不与反应罐相连,从溢流浆池中将浆液送至脱水系统。反应罐浆液密度通过调节返回反
应罐的回收水水量来控制。反应罐液位计用于显示和报警。这种调节方式简单,回收水流量调节阀不易磨损,维护工作量少,但当液位或密度偏低时不能自动调节。由于溢流口在罐体的上部,溢流液密度偏低,反应罐中会累积大量的固体物,加大溢流管插入深度可以缓解这种情况。

图17412 通过溢流控制反应罐液位和用回收水控制浆液密度
2.回收水调节反应罐液位和用排放阀控制浆液密度
图17413示出了这种控制方法的调节回路。在这种控制方法中,回收水流量受反应罐液位控制,用溢流管来限制最高液位。由反应罐浆液密度经排浆调节阀来控制排浆量。这种方案将液位和密度分开来控制,效果较第一种好,调节较为灵敏,但也要设置排浆池,排浆调节阀易磨损,而且排浆管道易堵塞。当锅炉低负荷,浆液密度偏低时,密度提升较慢。另外,由于排浆管道装在循环泵喷淋母管上,会影响循环浆流量的稳定性。
3.回收水调节反应罐液位和变速出浆泵控制浆液密度这种方案(见图174 14)与第二种方法的区别仅在
于改用调频调速出浆泵代替排浆调节阀,只要调速泵的容量选择适当,可以经该泵将反应罐浆液直接送至脱水系统,而无需
再设置石膏浆中间罐。采用调速泵有节能效果。由于变速出浆泵具有连续浆流,较之采用调节阀能避免堵塞管道。
4.用工业水调节反应罐液位和用出浆调节阀控制浆液密度
本方案(见图174 15)类似上述第二种方法,不同的地方是在保持回收水罐正常液位的前提下将回收水返回吸收塔,维持吸收塔正常液位不足的水量由反应罐液位调节阀直接加入反应罐。为了能对反应罐液位变化提前作出反应,对回收水流量调节回路引进了入口SO2负荷量作为前馈信号,由于采用了两个独立的调节回路来调节进入反应罐的水量,反应罐的液位较稳定。在实际运行中,通过反应罐液位调节阀补入的工业水量不多。对反应罐浆液浓度的控制也引入了SO2负荷量前馈信号,使石膏的产出和排放保持平衡,减少了浆液浓度

图17413 用回收水调节反应罐液位和用排放阀控制浆液密度

图17414 用回收水调节反应罐液位和变速出浆泵控制浆液密度

图17415 用工业水调节反应罐液位和用出浆调节阀控制浆液密度
的波动。图中反应罐的溢流管仅起限制最高液位的作用,溢流浆液通过地沟进入吸收区的集水坑,再返回反应罐。当然,也可以采用调速泵代替出浆调节阀来控制排放浆流量。
5.回收水调节反应罐液位和旋流器溢流/底流液控制浆液密度
如图17416所示,本方案采用回收水控制反应罐液
位,吸收塔出浆以恒定流量将石膏浆液送至水力旋流器,分离出来的溢流稀浆进入回收水罐,也可经节流孔板将一定量的溢流液直接返回反应罐。通过控制返回反应罐的旋流器底流浓浆液,来保持罐内浆液密度,当浆液密度低至一定值时,分流器使旋流器底流浓浆全部返回反应罐,使密度逐渐提升。当浆液密度达到某一定值后,分流器将浓浆切向底流浆罐。

图17416 用回收水调节反应罐液位和通过旋流器底流控制浆液密度
在本方案中,由于吸收塔出浆流量、压力稳定,有利于旋流器的分离,减少了出浆管道的堵塞。由于底流浆浓度大,浆液密度的调节响应较快。但这种方法不是连续调节浆液密度,底流浆罐应有足够体积,延长过滤机每次运行时间,即当底流浆返回反应罐时,停止过滤机运行,当底流浆流入底流浆罐时则启动过滤机。另外,水力旋流器会增加石膏晶体的磨损,形成细小结晶,有时会堵塞真空过滤机的滤布。
6.用工业水调节反应罐液位和旋流器溢流/底流液控制浆液密度
图17417是第六种方案的工艺流程和调节回路图,其特点是:
(1)吸收塔排浆采用恒速出浆泵,水力旋流分离器工作稳定。
(2)旋流器分离出来的溢流/底流浆液同时参与反应罐密度控制,连续控制浆液密度,对密度的调节灵敏、波动小。其密度调节原理是,如果浆液密度偏高(或偏低),脱水机给浆调节阀开度增大(或减小),经底流浆溢流管返回反应罐的浓
浆减少(或增多)。与此同时,溢流浆流量调节阀开度减小(或增大),返回反应罐的稀浆量增多(或减少),使反应罐浆液密度迅速下降(或提升)至设定值。由于采用了入口SO2负荷作前馈信号,使真空皮带过滤机的进浆量随锅炉负荷变化,保持了石膏产出和排出平衡,也加快了浆液密度的调节响应。由于过滤机的进浆量是变化的,所以皮带过滤机需根据给浆量调速运行,以保证一定的滤饼厚度。
(3)皮带过滤机滤液、冲洗水返回反应罐,当反应罐液位偏低时,直接将工业水经液位调节阀加入反应罐,保持液位稳定。
(4)当过滤机故障停运时,可经切换阀将供给过滤机的底流液引入废浆池,不影响旋流器的运行,也不会影响反应罐浆液密度的控制。
(5)正常运行时,脱水系统的运行处于全自动控制,无需运行人员手动操作干预。
(6)由于排往废浆池的浆液未作回收处理,全部作废水排放。为维持废浆池液位,需耗用工业水。

图17417 用工业水调节反应罐液位、旋流器溢流/底流液控制浆液密度
7.调节除雾器冲洗水量控制反应罐液位/启停脱水设备控制浆液密度
根据反应罐液位和锅炉负荷,调节除雾器冲洗间隔时间来调整补加工业水量,从而达到控制反应罐液位的目的。这样既补加了工业水又使补加水参与了除雾器的冲洗,其控制功能如
图17418所示。
采用旋流器和石膏脱水机间断运行的方法来控制反应罐浆液密度,即当浆液密度偏低至1.044kg/L,浆液含固量为80g/L时停止脱水设备运行,吸收塔排浆泵抽出的浆液返回吸
收塔,待浆液密度回升至1.10kg/L、含固量为180g/L后,恢
复脱水设备运行。这种方法的优点是省除了浆液浓度调节设
备,缺点是操作复杂,调节不灵敏,浆液浓度变化大,当浆液浓度低反应罐液位高时会给调节带来困难。
在一些简易FGD装置中,采用手工测量浆浓密度也可以实现对浆液密度的控制。由于反应罐浆液体积大,积聚了大量的石膏固体物,只要系统水平衡保持稳定,大多数石灰石FGD系统的浆液密度随时间变化较慢,再者,浆液浓度的控
制范围(一般10%~15%,或15%~25%,或25%~35%)
比pH值或反应罐液位要宽得多。用已校准的细颈瓶,用称重方法,每台班测定1~2次浆液密度,然后手动调整回收水流量或吸收塔浆液排出流量的给定值就可以实现对浆液密度的控制。这种手工分析方法已证明对有些系统是可行的,尤其适合
锅炉负荷和燃料含硫量变化不大的系统。
五、除雾器冲洗控制
为防止除雾器流道堵塞,必须定时冲洗除雾器以防止除雾器流道堵塞,冲洗顺序、冲洗时间和间隔时间可以预先设定(见图17419和图17420)。当出现正水平衡或冲洗效果不理想时,由自动控制工程师离线调整冲洗时间和冲洗频率。由于冲洗后的水流回反应罐,成为了水平衡中的补加水,因此设计固定冲洗时间和频率时应考虑系统的水平衡。由于这种设计是按锅炉最大工况来考虑冲洗时间和频率,当低负荷时,浪费了冲洗水,还有可能造成正水平衡,影响反应罐液位和浆液密度的控制。因此,有些FGD系统设计了除雾器冲洗控制回路,用以控制反应罐液位(见图17418),这种控制回路根据锅炉负荷(即烟气流量和反应罐液位)改变冲洗间隔时间,当锅炉负荷高,吸收塔内水分蒸发量大或液位偏低时,增大冲洗频率;当负荷下降或液位偏高时则延长冲洗间隔时间,以此达到控制反应罐液位,调节补加水量的目的。
六、FGD系统总水平衡控制
总水平衡控制是FGD系统一项复杂而又重要的控制项目,也是运行管理的一项重要工作,在现有的一些装置中,总水量控制混乱成了造成许多运行问题的根源。在设计阶段应通过对系统总水平衡的计算确定不同运行工况下的平均耗水量和最大耗水量,确保FGD系统各种运行工况下的平衡水量。
一般用补水来维持回收水罐的液位以控制FGD系统的总水

图17418 除雾器冲洗及反应罐液位控制图

图17419 水平流除雾器冲洗流程图和冲洗时间表

图17420 垂直流平放除雾器冲洗流程图和冲洗时间表
(a)ME冲洗流程图;(b)ME、吸收塔干/湿界面、氧化布气管冲洗时间表
量,在低负荷期间,系统可能耗水较少而造成正水平衡,在这种情况下应将过量水贮存起来。
当系统停运或设备检修时,这种贮水池还可以用来腾空反应罐或其他浆罐的浆液。当系统重新启动或运行时,可将储水池中的水返回吸收塔。
第五节 运行优化
近年来,由于煤炭资源紧张、煤种质量下降,机组实际燃用煤种的含硫量与设计煤种含硫量存在一定的偏差,煤质的变化引起了脱硫系统入口烟气流量、SO2浓度与灰分等主要参数的变化,而且机组负荷也经常波动,导致系统与设备的实际运行状况与设计状况不符,出现系统能耗增加、脱硫效率下降、设备腐蚀、结垢、脱硫石膏品质下降等情况,系统运行经济性、稳定性显著降低,严重时甚至会导致系统停运。这就有必要通过优化运行调整,找出不同工况(不同煤种、机组负荷)下,脱硫系统的最佳运行方案,在满足系统主要功能(脱硫效率、系统投运率等)的条件下,降低脱硫系统运行故障概率,实现脱硫系统最经济运行,从而大大降低脱硫系统运行成本,以达到系统稳定、经济、安全运行的目的。
脱硫系统优化运行是对系统运行的综合性调整,主要包括以下六个方面:
(1)根据现有煤种及负荷条件,在满足脱硫效率等主要设
计参数要求的条件下,制定最经济的运行方案,包括最佳循环泵组合、石灰石浆液投入量、吸收塔浆液pH值、吸收塔液位等。
(2)根据化学分析数据,调整吸收塔浆液品质,使吸收塔浆液良性循环,保证系统运行的稳定性、连续性。
(3)控制脱硫剂(包括纯度、活性、粒径)、工艺水品质,减少浆液品质恶化、吸收塔浆液起泡等影响系统正常运行的情况出现。
(4)强化日常生产管理,保证锅炉、除尘器等脱硫前端设备的正常、高效投运,减少因机组投油、粉尘超标等异常情况对脱硫系统的不利影响。
(5)加强日常化学分析、报表统计分析工作,及时发现系统运行潜在隐患(如浆液品质恶化、在线表计失准),并予以消除。
(6)调整脱水系统真空度、石膏厚度等参数,提高脱硫石膏品质,提升石膏利用率及系统经济性。
一、优化运行理念
脱硫优化运行的最终目的是在系统稳定运行的基础上,实现系统最经济运行。因此,脱硫系统最终运行成本就成为衡量优化运行效果的标尺。
1.烟气脱硫装置的运行成本
烟气脱硫装置的运行成本主要包括电费、脱硫剂费用、水费、蒸汽费和管理费用(财务费用、折旧费、人工费、维修
费、运营管理费和保险费等)。其中,电费、脱硫剂费用、水费、蒸汽费与运行工况紧密相关;此外,FGD装置的运行方式还会影响SO2的排污缴费和石膏销售收入。将受脱硫运行方式影响的这些因素累加起来,称为相对生产成本,计算公式如下:
C=C1+C2+C3+C4-C5
式中:C为相对生产成本,元/h;C1为系统电费,元/h;C2为脱硫剂费用,元/h;C3为用水、蒸汽、压缩空气费用,元/h;C4为SO2排污缴费,元/h;C5为脱硫副产物的销售收
入,元/h。
其中,电费、脱硫剂费用、SO2排污缴费受运行方式影响明显,且所占权重较大,水、蒸汽、压缩空气费用主要取决于运行工况,脱硫副产品销售收入主要取决于石膏品质和市场需求。因此,设计脱硫系统优化运行方案及进行优化试验时,应着力通过降低系统电耗、物耗,并保证SO2达标排放,减少排污费。即在满足环保要求的前提下,使得脱硫相对生产成本(C)最低。在此原则下,针对脱硫负荷、燃料硫分变化的不同工况,实行最优的运行方式。
2.脱硫设备的性能和寿命
脱硫设备的性能和寿命受运行环境的影响特别大。结垢、堵塞、腐蚀、磨损等现象的出现都会影响脱硫设备的可用率及电耗和维护成本,因此,应重视对设备的日常维护工作,表17 5 1列举了脱硫系统主要设备对运行经济性的影响及维护措施。
3.烟气脱硫优化运行实例
以某电厂2×300MW机组配套的烟气脱硫装置为例,系统设置4台浆液循环泵,从低到高分别为A、B、C、D。入口
SO2浓度的正常变化范围为1500~4500mg/m3,优化运行前
浆液循环泵投运方式为A、B、C、D四台泵同时运行。脱硫效
表1751
影响运行经济性的主要脱硫
设备及其维护措施

率没有严格要求,以烟气SO2排放浓度满足低于400mg/m3为准,排污费按实际排放量缴纳。脱硫剂为外购石灰石粉,石膏外卖有一定的收益,无蒸汽消耗。分析得出,造成脱硫系统运行经济性差的主要原因为:①未根据脱硫系统负荷(烟气量与入口SO2浓度乘积)及SO2排放浓度情况调整循环泵投运数量和组合,造成循环泵整体电耗显著增加;②未根据实际脱硫效率和SO2排放浓度及时调整吸收塔浆液pH值,最终影响石灰石浆液投加量,造成石灰石消耗量偏大。因此,优化运行主要从调整循环泵运行组合和浆液pH值两个方面入手。
(1)机组负荷为300MW、脱硫系统入口 SO2浓度为
4000mg/m3时,循环泵运行组合试验结果见表1752。
表1752
循环泵运行组合试验结果(负荷300MW、入口SO2浓度4000rng/m3)

可以看出,在此工况条件下,ABC三台循环泵同时运行即可满足污染物达标排放,而由于较优化运行试验前少运行一台浆液循环泵,系统电耗显著降低,由1711元/h降至1493元/h,虽然由于SO2排污浓度升高,排污费增加了115元/h,但系统总的相对运行成本降低了178元/h,以脱硫系统年运行6000h计算,每年可节约运行成本106万元,经济效益显著。
此外,三台浆液循环泵运行,可以保证有一台浆液循环泵长期处于备用状态,大大提高了系统的运行可靠性,提升了系统投运率,具有潜在效益。
不同机组负荷、不同入口SO2浓度条件下,循环泵组与相对运行成本和脱硫效率、出口SO2排放浓度的关系曲线如
图1751~图1759所示。

图1751 循环泵组与运行成本、脱硫效率、出口SO2浓度关系的曲线
(负荷300MW、入口SO2浓度4000mg/m3)

图1752 循环泵组与运行成本、脱硫效率、出口SO2浓度关系的曲线
(负荷300MW、入口SO2浓度3000mg/m3)

图1753 循环泵组与运行成本、脱硫效率、出口SO2浓度关系的曲线
(负荷300MW、入口SO2浓度2000mg/m3)

图1754 循环泵组与运行成本、脱硫效率、出口SO2浓度关系的曲线
(负荷240MW、入口SO2浓度4000mg/m3)

图1755 循环泵组与运行成本、脱硫效率、出口SO2浓度关系的曲线
(负荷240MW、入口SO2浓度3000mg/m3)

图1756 循环泵组与运行成本、脱硫效率、出口SO2浓度关系的曲线
(负荷240MW、入口SO2浓度2000mg/m3)

图1757 循环泵组与运行成本、脱硫效率、出口SO2浓度关系的曲线
(负荷180MW、入口SO2浓度4000mg/m3)

图1758 循环泵组与运行成本、脱硫效率、出口SO2浓度关系的曲线
(负荷180MW、入口SO2浓度3000mg/m3)

图1759 循环泵组与运行成本、脱硫效率、出口SO2浓度关系的曲线
(负荷180MW、入口SO2浓度2000mg/m3)
可以看出,在满足环保要求的前提下,不同机组负荷、不同入口SO2浓度条件下,最经济循环泵运行组合存在很大差
异:在负荷300MW的情况下,入口SO2浓度为6000mg/m3
时,ABC泵运行可满足运行要求;而入口 SO2浓度为
2000mg/m3时,AB泵运行就可满足运行要求,相比SO2浓度为4000mg/m3时,可以少运行一台循环泵,节电690kWh左
右。根据机组负荷和烟气条件及时调整循环泵组运行情况,有利于脱硫系统的经济运行。
(2)机组负荷为300MW、脱硫系统入口 SO2浓度为4000mg/m3时,吸收塔浆液pH值优化试验结果见表17
5 3。
可以看出,在此工况条件下,吸收塔浆液pH值大于5.2
即可满足污染物达标排放,pH值进一步升高能提高脱硫效率,降低排污费,但脱硫反应所需石灰石量也随之增加,石灰石成本增加,二者存在平衡关系。pH值为5.4时,总体相对运行成本最低,相比于pH值为5.8时,相对运行成本由3773元/h降至3726元/h,虽然由于SO2排污浓度升高,排污费增加了48元/h,但系统总的相对运行成本降低了47元/h,以脱硫系统年运行6000h计算,每年可节约运行成本28万元。此外,满足运行要求的前提下,适度降低浆液pH值,还能减轻系统结垢、堵塞,防止浆液品质因过饱和而恶化。
不同机组负荷、不同入口SO2浓度条件下,吸收塔浆液pH值与相对运行成本和脱硫效率、出口SO2排放浓度的关系
曲线如图17510和图17511所示。
表1753 吸收塔浆液pH值优化试验结果(负荷300MW、入口SO2浓度4000mg/m3、ABC泵运行)


图17510 浆液pH值与运行成本、脱硫效率、出口SO2浓度关系的曲线
(负荷300MW、入口SO2浓度4000mg/m3)

图17511 浆液pH值与运行成本、脱硫效率、出口SO2浓度关系的曲线
(负荷180MW、入口SO2浓度2000mg/m3)
(3)根据烟气负荷调整吸收塔液位和氧化风机投运台数及方式,可进一步优化脱硫系统运行方式,减少电耗。根据优化试验结果,编制各种工况下最佳运行操作卡见表17
5 4。
根据优化最佳运行操作卡,运行人员可以根据烟气负荷情况,灵活准确地调整脱硫系统运行方式,最大限度地实现脱硫系统经济运行。需要指出的是,随着运行工况及设备状态的变化,运行人员应按照优化运行的思路对试验结果进行适当调整,以求实现最佳运行操作卡的及时有效性。
表1754
不同运行工况最佳运行操作卡

二、优化运行方案
实际运行过程中,锅炉燃用煤种、机组负荷、烟气量、烟气温度、烟尘浓度、吸收剂品质等参数发生变化时,都会对脱硫系统的运行控制带来影响,脱硫系统优化运行正是通过试验分析各参数变化对脱硫系统的实际影响,来提出最佳应对方案,实现系统最经济、最稳定运行。因此,脱硫系统优化运行的内容也就应涵盖上述各种影响因素。
(一)浆液循环泵优化运行
浆液循环泵是脱硫系统的主要耗电设备,其电耗约占整个系统电耗的50%,在烟气条件一定的情况下,循环泵的投运情况决定了脱硫反应的最终液气比,并直接影响脱硫效率和SO2排放浓度。因此,循环泵的投运数量和配置方式关系着系统脱硫效率和经济性。优化运行试验应针对不同负荷、不同烟气条件,试验各种循环泵投运方式下的脱硫效率,并根据电耗和出口SO2排放浓度计算系统运行成本,得出最经济运行方式。
以某电厂为例,脱硫系统设置3台浆液循环泵,自下而上
分别为A、B、C,扬程分别为24.5m、26.5m、28.5m,三台
循环浆液泵均配备6000V的电机。脱硫系统入口SO2浓度在700~1200mg/m3浮动,循环浆液泵不同运行方式(三台循环浆液泵同时运行、停运 A循环浆液泵、停运B循环浆液泵、停运C循环浆液泵)下,浆液循环泵功率和脱硫效率变化如
表1755~表1758所示。
表1755
三台泵同时运行时的电耗和脱硫效率

表1756
停运A泵时的电耗和脱硫效率

表1757
停运B泵时的电耗和脱硫效率

表1758
停运C泵时的电耗和脱硫效率

可以看出,投入循环泵数量增加或投运高层循环泵时,脱硫反应液气比增加,脱硫效率提高,出口SO2排放浓度降低。100%负荷时,投运3台浆液循环泵比投运2台浆液循环泵时,脱硫效率高出1%~2%。80%负荷时,BC泵运行组合脱硫效率也高于AB泵、AC泵运行组合。显然,投运高层浆液循环泵,烟气与脱硫浆液接触时间增加,有利于提高脱硫效率。
但是,同时可以看出,增加循环泵投运台数或投运高层循环泵时,浆液循环泵总电耗也同时显著增加。100%负荷时,3台浆液循环泵运行时,总功率高出2台泵运行时800kW左右,以年运行6000h计算,年电耗增加约4800MWh,以上网电价
0.25元/(kWh)计,年运行成本增加近120万元。
因此,实际运行中,应根据脱硫系统负荷情况,选择适当的循环泵运行方式。
(二)吸收塔浆液pH值优化运行
吸收塔浆液pH值是脱硫系统中最重要的控制参数之一,它影响到吸收塔内吸收、氧化、溶解及结垢等各个方面。由于每个过程所控制的最佳pH值区间并不相同,故以保证系统安
全运行及满足脱硫效率要求为目的,对吸收塔内不同区域的pH值进行研究与优化调整。
最佳pH值研究的理论基础为:由于吸收塔内各位置的反应情况不同而导致不同区域pH值存在一定差异,因而每一区域控制的最佳pH值也并不相同。根据不同区域的化学反应过程及工艺要求进行pH值调整,综合起来给出吸收塔浆液pH值的最优控制值。
SO2的吸收、水合和离解过程为
图17512为pH值对SO2的吸收、水合和离解过程的影响,由图可知,当pH值小于4.0时,HSO3-开始减少,而此时开始有二氧化硫与水化分子存在,这会影响SO2的吸收反应。因此,此时应控制pH值低限在4.0以上。当有大量的HSO3-存在于液相区时,从离解平衡上要求快速将 HSO3-浓度减少,以有利于二氧化硫的吸收与离解。其中,一种方式为保证一定的pH值,即有一定的OH-存在,将其中的 H+中和而增大平衡向有利于二氧化硫吸收的方向进行;另一种方式则是将HSO3氧化,成为沉淀后而有利于二氧化硫的吸收。
可以看出,较高的pH值可快速中和生成的 H+,加强了二氧化硫的吸收活性。但因为喷淋层出口浆液pH值与扰动区
pH值基本一致,由于过高的pH值不利于石灰石的溶解析出Ca2+,所以pH值的上限主要受石灰石溶解的限制。
通过动力学反应试验可知,pH值与吸收塔内亚硫酸盐氧化的关联度较小,基本为0级响应。其中主要反应为
SO23-+12O2→SO24-HSO3-+12O2→HSO4-
但是当有 Mn2+、Fe3+等催化剂存在时,发生反应式为
HSO3-+12O2→SO24-+H+
即在催化作用下,pH值在5.0~5.5时,HSO3-直接被
氧化成SO24-离子态,即为快速氧化反应过程。
研究发现,pH值对亚硫酸盐氧化过程产生影响,如图1 7513所示。若在吸收塔扰动区检测出存在亚硫酸盐,将会大大降低吸收区内二氧化硫的吸收效率,这可以从溶解平衡中得到解释:在吸收区时,由于亚硫酸盐的存在加快了其平衡,抑制了二氧化硫的吸收。也就是说,在烟气吸收区无烟气短路现象存在时,吸收区末级浆液喷淋中的亚硫酸盐浓度决定了出口二氧化硫的最终排放浓度,所以应尽量降低此处的亚硫酸盐浓度。

图17512 pH值对SO2吸收过程影响曲线

石灰石的溶解主要受pH值的影响,即浆液池中石灰石加入区及扰动区的H+浓度主要决定了石灰石的溶解。pH值对石灰石溶解速率的影响如图17514所示。

图17514 pH值对石灰石溶解速率的影响曲线
显然,石灰石溶解过程需要消耗 H+,较低的pH值有利
于Ca2+的析出,且pH值为4.0~5.5时,石灰石能较快溶解,
0.5h左右溶解趋于平衡。
从运行经济性角度考虑,降低浆液pH值,可以减少石灰石浆液消耗量,但同时脱硫效率会有所下降,SO2排放浓度升高,排污费增加,因此,对于不同运行负荷工况,存在不同的
最佳pH值。
吸收塔浆液pH值优化运行试验包括以下两个方面:
(1)在满足SO2排放浓度的前提下,降低石灰石浆液供给量,控制吸收塔浆液pH值,通过核算石灰石原料费和排污费,找出不同工况下的最经济运行点。
(2)综合考虑pH值对石灰石溶解、SO2吸收、系统结垢的影响。
(三)吸收塔液位优化运行
在浆液循环泵流量不变的情况下,较高的吸收塔液位可以增大浆液循环泵入口的压力,在一定的范围内可以降低循环泵的运行电流,起到节能的作用。同时,提高吸收塔运行液位对浆液循环泵入口负压有较明显的作用,尤其是当设计气蚀裕量不合理时,可以减小气蚀的发生。
需要注意的是,高液位运行,增加了脱硫系统溢流的风险,特别是出现浆液循环泵或氧化风机突然跳闸、塔内气液相平衡出现较大波动的情况下,这种风险概率会显著增加,运行人员必须加强监视,并准确及时地采取相应的处理操作。
(四)吸收塔浆液密度优化运行
实际运行中,吸收塔浆液密度是决定石灰石利用率和石膏品质的重要参数。运行人员需根据浓度值决定石膏脱水系统的启、停操作。通常,浆液浓度高于1150kg/m3时,启动脱水
系统;低于1080kg/m3时,停运脱水系统。
理论上认为,浆液浓度高于1150kg/m3时,吸收塔浆液
中CaCO3和 CaSO4 ·2H2O的浓度已趋于饱和,CaSO4 ·
2H2O对SO2的吸收有抑制作用,脱硫率会有所下降,同时循环泵电流也有所增加;而石膏浆液密度过低(<1085kg/m3
时),浆液中CaSO4 ·2H2O的含量较低,CaCO3的相对含量
升高,此时的浆液如果排出吸收塔,将导致石膏中CaCO3含量增高,品质降低,而且浪费了脱硫剂石灰石。因此,运行中
控制石膏浆液密度在一合适的范围内(1080~11130kg/m3),
有利于FGD的有效、经济运行。
由图17515可以看出,循环泵电流总体上随着浆液密度的上升而上升,当浆液密度从 1063kg/m3上升到
1175kg/m3过程中,A泵、B泵、C泵的电流分别升高6.86A、7.15A、7.04A。

图17515 循环泵电流与浆液密度的关系曲线
(五)增压风机优化运行
增压风机是脱硫装置烟气系统中最大的耗电设备,增压风机的运行方式对于系统电耗、脱硫效率等参数有显著影响,风机导叶开度增大,风机出力增加,风机电耗也随之增加,在有GGH的烟气脱硫系统中,GGH压差、电耗也会相应增加。以某电厂三期330MW机组为例,330MW负荷下,不同增压风机导叶开度与电耗的关系见表1759。
表1759 增压风机导叶开度与电耗的关系

但是,当增压风机导叶开度太小时,风机出力难以克服脱硫系统阻力,增压风机入口呈正压运行,系统泄漏量增加,在有旁路的脱硫系统中,旁路烟气泄漏量会有所增加,影响整体的脱硫效果;另外,为克服系统阻力,引风机导叶开度势必加大,电流升高,增压风机和引风机电流之和有升高的可能,增压风机导叶开度变化引起的引风机导叶开度及脱硫效率等相关参数的变化见表17510。
表17510 增压风机导叶开度与引风机导叶
开度及脱硫效率的关系

可以看出,当增压风机入口压力从0调整到70Pa时,引风机电流、脱硫效率基本没变,而GGH的差压及增压风机电流迅速下降。当增压风机入口压力从150Pa调到180Pa时,引风机开度有所增大,增压风机电流下降不明显,但脱硫效率迅速下降。
因此,在引风机与增压风机串联运行的系统中,应在系统安全运行的前提下,从降低引风机与增压风机电流之和来着手进行系统优化运行工作。以某电厂300MW机组为例,增压风机与引风机的优化运行结果见表17511。
表17511 增压风机、引风机导叶开度优化结果

可以看出,在脱硫效率相近的情况下,通过联合调整增压风机与引风机导叶开度,风机电流之和可以降低20A左右,系统运行经济性显著提高。增压风机与引风机串联的优化运行
曲线如图17516所示。

图17516 脱硫增压风机与引风机的优化运行曲线
需要指出的是,增压风机的主要用途是克服脱硫系统的阻力,因此脱硫系统,特别是GGH堵塞程度对增压风机的电流有很大的影响,以某电厂200MW机组配套脱硫系统为例,GGH人工冲洗前后增压风机运行参数对比见表1 7
5 12。
可以看出,通过清洗GGH,降低脱硫系统运行阻力,增压风机电耗显著下降,因此,加强日常运行中对烟气除尘设施的维护、降低脱硫系统入口粉尘浓度、加强吸收塔除雾器和GGH冲洗,是降低脱硫系统能耗、提升运行经济性的有效手段。
表17512 GGH压差对增压风机运行参数的影响

(六)氧化风机优化运行
氧化风机主要是为脱硫反应提供充足的氧化剂,保证亚硫酸盐正常氧化为硫酸盐,结晶后析出、脱水,推动脱硫反应持续进行。氧化风量是否充足对脱水系统运行效果及脱硫石膏品质有较大影响。烟气中氧含量对脱硫效率的影响如图17
5 17所示。

图17517 烟气含氧量对脱硫效率的影响曲线
可以看出,在烟气量、SO2浓度、烟温等参数基本恒定的情况下,随着烟气中O2含量的增加,CaSO4 ·2H2O的形成加快,脱硫率也呈上升趋势。当原烟气中氧量一定时,可人为地向吸收塔浆液中增加氧气,所以多投运氧化风机可提高脱硫率。当烟气中O2含量为6.0%时,运行两台氧化风机比运行一台氧化风机的脱硫率高出2%左右。
但同时需要指出,相比于一台运行,两台氧化风机运行系统电耗会大大增加,运行经济性下降,实际运行中,应结合烟气负荷情况,灵活调整氧化风机投运台数,在负荷降低时,可采取间歇停运氧化风机的运行方式。
此外,氧化风减温水量调整对于工艺水耗量和氧化风机电耗也有一定的影响,是氧化风机优化运行的另一个工作点。以某发电公司为例,脱硫系统对氧化风机出口设计有喷水减温装置,该装置投入运行时,氧化风机电流为27A左右,取消喷水减温后,氧化风机电流在20A左右。经运行实践证明,取消喷水减温后,吸收塔反应区域温度在50℃左右,而且对氧化效果基本没有影响,石膏中亚硫酸钙含量维持在0.25%左右。
(七)制浆系统优化运行
制浆系统负责脱硫系统脱硫剂的供应,制浆系统的运行不仅影响自身的物耗、电耗,而且对脱硫系统的运行效果(如脱硫效率)也有显著影响。在石灰石—石膏湿法脱硫系统中,吸收剂石灰石的颗粒度越细,其消融性能越好,反应速率越快,石灰石的利用率越高,可获得较高的脱硫效率;但石灰石的颗粒度越细,湿式球磨机的能耗就越高,从经济性角度而言,两者存在一个平衡点。
以某发电厂烟气脱硫系统为例,石灰石浆液制备系统配置2台一级旋流分离湿式球磨机,每台的额定出力为6.4t/h,设计一级旋流出口石灰石颗粒度达到325目筛通过90%以上。磨机为两套烟气脱硫的公用设备,由于石灰石用量大,要满足石灰石颗粒度达到325目筛通过90%以上,磨机达不到额定出力运行。这种运行方式下,设计平均每塔额定负荷下石灰石消耗量4.268t/h,实际在4.5t/h左右。一旦有一台湿式球磨机出现故障,制浆量就无法满足两套脱硫设备的运行需要。
为了保证脱硫系统的正常运行,经过细致分析,确定从改变石灰石旋流出口的石灰石颗粒度着手,在提高磨机出力方面进行了一系列的试验:改变两台球磨机的钢球性能曲线及钢球配比(在磨机出口加准40、准30、准20三种规格的钢球,入口加准70、准60、准50号钢球),并控制石灰石旋流器出口石灰石颗粒度(由原来的325目筛通过率达90%以上改变成
250目筛通过率达90%以上),试验数据见表17513。
表17513
制浆系统优化试验参数

从表17513可以看出,旋流出口石灰石颗粒度250目筛通过率达到90%时,在同等石灰石品质情况下磨机出力明显增大(原来最大出力为5t左右,现出力为6.5t),单台磨机运行33h的制浆量即可满足两套脱硫系统运行的需要,而且脱硫效率、石膏中石灰石的含量这两个参数均能达到设计要求。磨机优化运行后,达到了提高出力、节约电耗的目的。
(八)脱水系统优化运行
真空皮带脱水系统作为公用设备,承担着两套脱硫系统石膏浆液的脱水任务,每天的运行时间为16~20h。要降低皮带机的电耗,就要尽量减少皮带机的运行时间。某发电公司进行了改变石膏排出泵输送方式(工频、变频)及调整石膏旋流器旋流子(正常情况旋流子三运一备)的试验,并对不同工况下石膏浆液的脱水速度、石膏品质的相应变化进行了对比和监测,通过分析试验数据,确定皮带机的最佳运行状况。经过多次试验后,确定了石膏排出泵的输送方式,减少了皮带机及其附属设备的运行时间,提高了皮带机出力和设备的运行效率,从而减少了设备耗电量。目前,该公司真空皮带机运行时,石膏旋流器旋流子全部投运;石膏排出泵变频启动正常后将其频率变为工频运行方式。在运行过程中加强对皮带机
运行速度和石膏旋流器出口压力的监视,发现皮带机速度持续降低或压力降低时,及时联系维护人员检查石膏排出泵及其出口回流管路孔板的磨损情况,若磨损增大则及时更换,控制石膏浆液回流量,保证石膏排出泵出力正常,从而保持皮带机的经济运行。
(九)工艺水系统优化运行
工艺水系统负责向脱硫系统供应工艺用水和设备冷却水,是系统稳定运行的基础。脱硫系统在运行中,工艺水系统的流量变化比较大,有时可能接近零流量,有时可能接近最大流量,在工艺水系统配置中一般设有2台工艺水泵,实行一用一备;设置2台除雾器水泵,也是一用一备,这样的配置存在着水压不稳定、流量不稳定、多耗电的问题。在系统不需要水时,流量小,水压接近高限,不仅多耗了电,而且水压高会损害系统中的阀门。鉴于此问题,在有的系统中按两台泵运行一台泵备用的方式配置。在水泵出口设置了稳压阀或回流阀,这样的配置保证了系统的可靠性和安全性,但却不节能。
工艺水系统的水泵按一用一备配置,每台水泵都配置变频装置,每台水泵的流量按脱硫系统的最大流量选择,水泵的压力参数大于所需的最大水压,在水泵出口设置调压阀,这样在低流量和高流量时,变频装置根据系统压力的变化自动调节水泵的转速,不仅能满足脱硫系统所用水的流量和水压的要求,而且也达到了节约电能的效果。根据两个不同配置的系统运行对比,加装变频装置的系统要节电20%以上。
此外,以下优化运行措施也可在一定程度上减少工艺水消耗:
(1)在保证冷却效果的前提下,尽量减少设备冷却水流量。
(2)加强脱水系统运行调整,保证脱水效果,减少石膏带水量。
(3)优化除雾器冲洗周期和冲洗水压力,在保证冲洗效果的前提下,减少冲洗水耗量。
(4)避免烟气温度超标,减少烟气带水。
(十)吸收塔浆液品质优化调整
吸收塔浆液品质不仅关系着脱硫反应的正常进行与否,而且还对系统结垢、腐蚀等有着重要影响。浆液品质恶化是造成脱硫系统不能正常投运的一个重要原因,发生浆液品质恶化后,不仅脱硫反应平衡被破坏,按原有反应条件无法满足脱硫效率、SO2排放浓度等主要指标要求,而且石灰石浆液耗量、电耗均显著增加。因此,借助于化学分析数据,对吸收塔浆液品质进行优化调整就成为脱硫日常运行工作的重要组成部分。优化调整主要内容包括以下几个方面。
1.pH值控制
湿法脱硫系统中pH值是最重要的控制参数之一,其设计的理论依据不仅要满足高吸收率,而且还要兼顾石灰石的溶解率、塔内的亚硫酸盐氧化效果、石膏结晶及石膏过饱和度、控制晶体大小而引发的磨损与结垢问题。单纯从SO2的吸收角度讲,pH值越高越好,但pH过高会影响石灰石的溶解,不利于Ca2+的溶出。在系统实际运行中,应综合考虑各方面因素以确定最佳pH值。
2.浓度控制
浆液浓度较低时,单位体积内溶质较少,不利于SO2吸收;但当浓度过高时,又影响离子的扩散,也会令浆液停留时间延长,将影响吸收塔内晶体的粒径分布状况,若生成过大晶体还会导致设备磨损。设计吸收塔内质量浓度为10%~15%。
3.粒径分布控制
脱硫石膏应有较好的粒径分布特征,即粒径分布相对集中,小粒径生成较少,使新生成的晶体主要在已有石膏上生长,或在细小飞灰上生长,尽量减少石膏浆液直接生成大量细小晶体,防止因缺少晶核而在塔壁上结晶(结垢)。
4.氧化控制
应保证足够的氧化风量,并使氧化风在吸收塔内安静、均匀地鼓泡。
5.杂质控制
吸收塔内杂质情况非常复杂,影响机理也尚未完全清楚,但大部分杂质离子对脱硫系统有害,也有部分离子如 Mn2+等对氧化起到一定的催化作用。在正常条件下应尽量降低系统内的杂质。
6.浆液中Cl—、F—等主要成分的影响
浆液中Cl-浓度对石灰石的溶解有明显的抑制作用。浆液中微量的Cl-不利于石灰石的溶解。因为浆液中Cl-与Ca2+生成CaCl2,溶解的CaCl2浓度增加,同离子效应导致液相的离子强度增大,从而阻止了石灰石的溶解反应。浆液中含有微量的Cl-,即可导致石灰石消融率的明显下降。浆液中的Cl-主要来自燃煤中的氯。浆液中 Cl-与 Ca2+生成CaCl2,不仅影响石灰石的溶解率,而且还会降低脱硫剂的碱度,即通过影响H+的活性而产生作用。向浆液池鼓风可减轻CaCl2的不利影响,通过提高液气比也可弥补脱硫剂碱度的损失。
氯离子还具有较强的配位能力,能与金属离子配位形成络
合物,如(CaCl2 )+等。而飞灰中Al2O3和Fe2O3的含量是较
高的,尽管经过电除尘后,Al2O3和Fe2O3含量有所降低,但由于整个系统的水基本是闭路循环,排出去的废水是有限的,
Fe3+、Al3+、Zn2+也会因富集而使浓度不断增加,生成
(FeCl4)-、(ZnCl4)2-等络合物,这些络合物将Ca2+或CaCO3
颗粒包裹起来,使能够参与反应的Ca2+或CaCO3减少,即惰性物增加,这势必会降低脱硫效率,增加脱硫剂的消耗。
Cl-在吸收塔内除影响石灰石溶解反应外,还是系统腐蚀的最重要影响因素之一。此外,Cl-浓度较高时还会影响石膏的结晶,导致结晶缺陷,造成生成的石膏晶体不稳定,致使大石膏晶体在不饱和条件下溶解较快而生成大量的细小结晶体。
浆液中F-浓度对石灰石的溶解特性有抑制作用。随着浆液中的F-的增加,石灰石溶解率略有减小。这说明F-对石灰石的溶解率有微弱的抑制作用。这可能是因为F-形成了复杂的络合物覆盖在石灰石颗粒表面,导致石灰石堵塞,从而阻碍溶解反应的进行。浆液中的F-主要来自燃煤烟气中的氟化合
物。国外研究表明,F-主要与Al3+形成络合物(AlF4)-。
在浆液系统中,因CaF2比石膏的溶解度更小,几乎全部的F-在过量的Ca2+存在的情况下全部生成CaF2沉淀,CaF2沉淀是一种非常致密的固体,非常不易去除,若含量较大时,还会与其他沉淀物生成成片的共沉淀物,所以应重视对F-的控制。
三、优化运行案例
(一)某发电厂8号机组烟气脱硫系统优化运行案例
某发电厂8号机组于2007年6月投入商业运行,同期配套建设两套湿式石灰石—石膏法烟气脱硫装置,脱硫系统投运
时间为2007年9月。
8号机组脱硫系统设计在BMCR工况下进行全烟气脱硫,脱硫系统保证BMCR工况下锅炉燃用设计煤种和校核煤种时
脱硫效率为95%,当原烟气中SO2含量比校核煤种增加25%时,脱硫效率不低于90%。采用高效脱除SO2的石灰石—石膏湿法脱硫工艺,提供一套完整的烟气脱硫系统,一炉一塔。
在锅炉100%BMCR工况设计烟气量、入口SO2含量
1771mg/m3 (设计煤种)/2060mg/m3 (校核煤种)(标态、干
基、6.0%O2)时,脱硫效率为95%;脱硫设备年利用小时
数按6500h计。
锅炉及其辅机参数见表17514。
脱硫系统入口设计参数见表17515。设计煤种及校核煤种参数见表17516。
某发电厂8号机组燃煤设计煤种平均含硫率为0.73%,校核煤种含硫量0.82%,进入吸收塔的烟气中SO2浓度为
1770.82mg/m3(标态、干态、设计煤种)、2060mg/m3 (标
态、干态、校核煤种)。
由于煤种及实际负荷的变化,实际运行中入炉煤含硫量在
0.41~1.25范围内波动,SO2进口浓度在600~2700mg/m3范
围内波动,脱硫率也不十分稳定,当原烟气中SO2突然升高时,脱硫率会有所下降。2011年5月,8号炉入炉煤质化验报
告见表17517。
表17514 锅炉及其辅机参数

表17515
FGD入口参数

表17516 设计煤种及校核煤种参数

表17517 8号炉入炉煤煤质化验报告

脱硫系统设计烟气量为2273141m3/h(校核煤种为
297493m3/h),实际烟气量在1.5×106~2.2×106m3/h范围内
随负荷变化而波动,以此计算,即使8号机组满负荷运行,脱硫系统在现有工况下,总负荷(原烟气SO2浓度与烟气量乘积)仍在设计范围之内,因此只要运行调整合适,系统主要参数(包括脱硫效率、净烟气SO2浓度等)就可以达到设计值。
优化运行试验以实现系统主要设计参数满足设计或实际运行需要,并实现系统经济合理运行为目的,通过调整相关运行参数,实现系统最优化。根据对脱硫系统运行影响程度大小,调整参数选择吸收塔浆液pH值、浆液循环泵组合、吸收塔液位、吸收塔浆液密度、原烟气SO2浓度、石灰石浆液密度、供浆量等。其中,脱硫效率是所有调整的前提条件,调整参数以脱硫效率满足电厂实际运行控制值为准,即脱硫效率不低
于90%。
对脱硫系统经济性分析,脱硫系统运行费用主要包括运行人工费、设备折旧费、电费、石灰石原料费、水费等。其中,电费、脱硫剂费用、SO2排污缴费受运行方式影响明显,且所占权重较大;水、蒸汽、压缩空气费用主要取决于运行工况;脱硫副产品销售收入主要取决于石膏品质和市场需求。因此,设计脱硫系统优化运行方案及进行优化试验时,主要着力通过降低系统电耗、物耗,并保证SO2达标排放,减少排污费,即在满足环保要求的前提下,使脱硫相对生产成本最低。在此原则下,针对脱硫负荷、燃料硫分变化的不同工况,实行最优的运行方式。
对于某发电厂8号机组脱硫系统而言,运行人工费、设备折旧费与优化运行无关,耗水量主要取决于机组负荷,因此优化运行经济性分析主要从电费、石灰石原料费和SO2排污费三个方面考虑。
1.270MW负荷下优化试验
(1)吸收塔浆液pH值优化。
在一定范围内,pH值越高越有利于SO2的吸收,可提高脱硫率,但当pH值大于5.8时,石灰石中Ca2+的溶解速度减慢,SO2的氧化也受到抑制,不利于石膏结晶;反之,pH值越低越有利于石灰石溶解,但SO2的吸收受到抑制,脱硫效率将下降。因此在运行中保持吸收塔浆液pH值稳定,将其控制在合适范围内(一般为5.2~5.8)是有效控制SO2吸收反应、获得稳定脱硫率和石膏品质的前提。
实际操作中,pH值在5.1~5.7范围内波动,从运行效果来看,在270MW负荷下,pH值高于5.3时,脱硫效率均能达到运行要求,其他条件不变时,提高pH值,脱硫效率明显升高,浆液pH值与脱硫效率的关系曲线如图17518
所示。

图17518270MW负荷下浆液pH值
与脱硫效率的关系
但从运行经济性的角度考虑,提高pH值,亚硫酸钙的氧化和石灰石的溶解受到严重抑制,产品中出现大量难以脱水的亚硫酸钙,石灰石的利用率下降,运行成本提高,随石膏排出吸收塔未反应的过量石灰石也随之增加(从石膏分析结果来看,部分时段石膏中CaCO3含量高达3.5%,正常情况下应低于1%),同时高pH值也会增加系统结构堵塞的风险。就运行经济性而言,pH值变化会引起石灰石耗量和出口SO2浓度变化,石灰石运行成本和排污费也会随之变化,270MW负荷、入口SO2浓度1500mg/m3条件下,石灰石成本、排污费及两项合计费用变化见表17518。
表17518 270MW负荷、入口SO2浓度
1500mg/m3下不同的pH值优化

可以看出,pH值由5.1提高至5.5,石灰石浆液耗量增加0.77t/h,增幅为21.04%,石灰石成本和排污费合计增加
3.7%。在270MW负荷、入口SO2浓度1500mg/m3条件下,
pH值为5.3时,石灰石成本和SO2排污费两项费用合计最低,因此该条件下pH值应保持在5.3左右。此外,虽然pH值为5.1时与pH值为5.4时,两项费用合计相近,但低pH值运行会在入口SO2浓度较高时,存在SO2排放浓度超标的风险,因此不建议低pH值运行。为了保持运行过程中浆液pH值稳定,建议尽快完成浆液pH值自动投入工作。
(2)浆液循环泵运行组合优化。
某发电厂8号脱硫系统设置4台浆液循环泵,A~D号由低到高布置,布置如图17519所示。
负荷为270MW时,进入脱硫系统的烟气量远小于设计烟气量,因此投运较少的浆液循环泵就可以满足设计液气比,保证烟气与浆液充分接触、反应。实际运行操作中,此负荷下,投入2台浆液循环泵时,脱硫效率可满足运行要求,AC泵运行时比AB泵运行时,脱硫效率约高0.8%,但电流约高2A,

图17519 某发电厂8号脱硫系统浆液循环泵布置
计算可得系统电耗约增加0.5%;而即使是原烟气SO2浓度为此负荷下最高的1852mg/m3时,AB泵运行脱硫效率仍可达91.86%,因此此负荷下正常投运AB两台浆液循环泵即可。
(3)吸收塔液位优化。
从脱硫反应来说,吸收塔液位越高,循环泵入口浆液静压头越高,循环泵抽取的浆液量越多,母管压力越高,喷淋高度越高,浆液在塔内停留的时间越长(相当于增大了浆池容积),与气体接触的时间延长,接触界面增加,气体穿越气膜/液膜界面机会多,吸收效果更佳。同时,液位高,氧化区高度增加,氧化反应充分,会促进石膏晶体的生长,有利于形成较大颗粒的石膏晶体,有利于石膏脱水,有利于提高脱硫率。亚硫酸钙氧化不充分会导致过饱和,因亚硫酸钙溶解度大于碳酸钙,会抑制石灰石的溶解,要提高脱硫率,就得补入更多的石灰石浆液。另外,亚硫酸钙的溶解会增强浆液酸性,不利于对SO2的吸收,进而降低脱硫率。
吸收塔液位的高低对氧化风机电量的消耗有一定的影响,液位高时氧化空气压力升高,氧化风机电流增加,但影响不大。AB泵运行时不同液位下,循环泵、氧化风机电耗及两者
之和变化见表17519。
表17519 AB泵运行时吸收塔液位对电耗的影响

可以看出,循环泵流量不变的情况下,较高的工作液位可以增加循环泵入口工作压力,在一定范围内可以降低循环泵的工作电流,起到节能的作用。试验表明,AB两台浆液循环泵运行时,吸收塔液位由8.60m升至9.60m,AB泵总电流减少3.22A,循环泵与氧化风机电耗合计减少27kWh,运行成本降低8.64元/h,每年可节约5.18万元;同时,每提高1m工作液位,吸收塔浆液离子浓度约可以降低1/10,浆液饱和度降
低,有利于SO2吸收。
从实际运行操作来看,吸收塔液位对于脱硫效率有着较为明显的影响,应在运行过程中予以严格控制。270MW负荷下吸收塔液位与脱硫效率的关系如图17520所示。

图17520270MW负荷下吸收塔液位与
脱硫效率的关系
在270MW负荷下,如果入口SO2浓度为1700mg/m3,液位由9.3m升至9.8m,出口 SO2浓度由175mg/m3降至
136mg/m3,排污费约可减少22万元/年,从优化系统运行性能的角度,在保证吸收塔不出现溢流的前提下,应尽量维持吸收塔在高液位运行,此负荷下,建议液位控制在9.4~9.6m。
可以看出,随着吸收塔液位的增加,脱硫效率升高。液位低于9.3m时,脱硫效率低于90%,无法满足运行要求。
(4)吸收塔浆液密度优化。
从实际运行情况来看,吸收塔浆液密度对脱硫效率影响不大。但资料表明,当吸收塔浆液密度大于1150kg/m3时,混
合浆液中 CaCO3和 CaSO4 · 2H2O的浓度已趋于饱和,
CaSO4 ·2H2O对SO2的吸收有抑制作用,脱硫率会有所下降;而石膏浆液密度过低(小于1080kg/m3时),说明浆液中
CaSO4 ·2H2O的含量较低,CaCO3的相对含量升高,此时如
果排出吸收塔,将导致石膏中CaCO3含量增高,品质降低,而且浪费了脱硫剂石灰石。因此运行中控制石膏浆液密度在一
个合适的范围内(1080~1130kg/m3),质量浓度较高时,将
浆液打至脱水系统脱水,质量浓度较低时停运脱水系统,对于稳定脱硫效率、提高石膏品质、防止结垢和降低相关泵及管道的磨蚀是有利的,有利于FGD的有效、经济运行。综合考虑,吸收塔浆液密度在各种负荷下均应保持在1080~1130kg/m3的范围内。从实际情况来看,浆液密度过高,不仅影响SO2吸收,而且在吸收塔液位相近的情况下,循环泵的电流也会明显增加,如在液位为9.5m时,循环泵AC运行,浆液密度由
1209kg/m3升至1291kg/m3时,总电流增加约3.7A,系统电耗增加0.925%。
(5)入口SO2影响。
在其他参数不变的条件下,增大SO2浓度,相当于增大了气相主体中SO2的分压,从而增加了气液传质的推动力,增强了传质效果,提高了吸收速率。但是,SO2分压增加到一定程度,会使得气液吸收反应的增强因子减小,SO2传质速率增加的速度小于欲去除的烟气中SO2的增加速度,从而在较高SO2浓度时,其脱硫效率降低。因此,在通常情况下,烟气中SO2浓度在较低时比在较高时更容易取得较高的去除效率。
实际运行中,270MW负荷下,原烟气SO2浓度在640~
1900kg/m3范围内波动,原烟气SO2浓度与脱硫效率的关系
如图17521所示。

图17521270MW负荷下原烟气SO2浓度
与脱硫效率的关系
(6)石灰石浆液密度影响。
石灰石浆液对脱硫效率的影响最终体现在对浆液pH值和钙硫比的影响上,石灰石浆液密度与供浆量的乘积决定反应最终脱硫剂的总量,石灰石浆液浓度太低,石灰石供浆系统即使满负荷运行,也可能无法维持浆液pH值和充分反应所需的钙硫比;石灰石浆液太高,供浆泵、管道磨损,结垢加重,会增加系统运行的风险性,综合考虑,石灰石浆液密度宜控制在
1250kg/m3。
(7)氧化风机优化。
通过调整氧化风机运行方式所取得的经济效益较小。在实际运行中发现,吸收塔内长时间氧化风供给不足,会造成吸收塔内亚硫酸盐含量不断增加,石膏脱水效果变差,并最终导致脱水系统不能运行,因此为吸收塔提供适量的氧化风是保证FGD稳定运行的前提。
(8)脱水系统优化。
石膏含水率的影响因素较多,如在吸收塔内,石膏浆液中的过饱和度、浆液的pH值、氧化空气用量等化学反应条件控制不合理,都将会影响石膏晶体的形成(包括石膏晶粒的大小
和形状)。如果形成针状晶体(CaSO4 ·1/2H2O),则其晶粒
度过细就难以脱水;而理想的石膏晶体应是短柱状的,比前者颗粒大,易于脱水。现阶段某发电厂8号脱硫系统石膏化学成分分析结果见表17520。
表17520 石膏化学成分分析

对脱硫石膏二级脱水工艺运行过程控制不合理,是造成石膏含水率超标的重要因素之一。一是如果一次脱水过程中石膏旋流器效率低,则会导致石膏旋流器底流出的石膏浆液含固率偏低,将直接影响石膏二次脱水效果;二是二次脱水中石膏真空脱水皮带机效率低,也会对石膏含水率产生很大的影响。
从石膏分析结果来看,现阶段运行条件下,石膏含水量均高于10%,在13%~16%范围内波动,石膏中亚硫酸盐含量
明显偏高,最高时达8.69%(要求不大于0.2%),造成脱水困难,解决该问题应从两方面入手:①控制浆液pH值在合理范围内,防止pH值过高;②停运时检查清理氧化风管,保证脱硫反应所需的氧化风充足。此外,实际运行真空皮带脱水系统真空度明显偏低,仅为-30kPa左右(正常应为-50~-60kPa),脱水不利,应对脱水系统进行详细查漏。
(9)石灰石活性分析。
理论石灰石耗量是指脱硫系统在设计Ca/S比条件下,按照脱除SO2量计算得出的所需石灰石量,计算公式为
MCaCO3=Qsnd(Cs1-Cs2)MMCaSCO2O3F1r×St×10-6
式中 MCaCO3———理论石灰石耗量,kg/h;
Qsnd———标干烟气量,标态,6%O2,m3/h;
Cs1———原烟气SO2浓度,标态,6%O2,mg/m3;Cs2———净烟气SO2浓度,标态,6%O2,mg/m3;
MSO2———SO2摩尔质量,64.06g/mol;
Fr———石灰石纯度,试验期间为89.4%;
St———钙硫比。
实际石灰石消耗量则是通过实际脱硫反应中投加到吸收塔内的石灰石浆液量和浆液密度计算得出的,计算公式为
MCaCO3=Qsρ液ρρ石液((ρρ液石--11))×100%
式中 MCaCO3———实际石灰石耗量,kg/h;
ρ石———石灰石密度,ρ石=2.6g/cm3;ρ液———石灰石浆液密度,g/cm3;
Qs———每小时石灰石浆液量,m3/h。
理论石灰石耗量与实际石灰石耗量之差,可以在一定程度上反映石灰石在实际脱硫反应中的活性(投加过量石灰石,造成浆液过饱和,也会增加石灰石实际耗量)。270MW负荷下理论石灰石耗量与实际石灰石耗量对比见表17521。表17521270MW负荷下理论石灰石耗量
与实际石灰石耗量对比

可以看出,270MW负荷下,理论石灰石耗量均值为
3.782t/h,而实际石灰石耗量均值为4.337t/h,石灰石多耗用
量平均值为0.555t/h。每天多消耗石灰石约13t,运行成本增加2600元/天。为了合理利用石灰石,提高运行经济性,应从以下几个方面入手:
1)提高石灰石来料品质。石灰石来料品质是影响石灰石耗量的重要因素,石灰石中常含有MgO、SiO2等氧化物杂质,甚至含有大量的灰面、泥土,杂质的存在会引起磨机堵料,同时杂质带入系统中的可溶性铝和浆液中的F-可以形成AlFx络合物,AlFx络合物达到一定浓度时,会使石灰石的反应活性降
低,即所谓的“封闭”石灰石,使石灰石浆液进入“盲区”。运行中,应严格控制石灰石来料纯度,保证CaCO3含量高于
91%、MgO含量低于1.12%,严格控制石灰石浆液粒径95%
通过250目,减少石灰石料中泥土和灰面的含量。
2)优化石灰石运行环境。石灰石浆液所处的运行环境较复杂,搅拌速率、pH值、吸收塔中的离子、温度等对石灰石耗量都有一定的影响,其中pH值对石灰石耗量影响最大。运行环境中pH值不仅影响SO2的吸收和亚硫酸钙的氧化,而且也影响石灰石的溶解,因此对石灰石耗量有极重要的影响。不同pH值下石灰石溶解曲线如图17522所示。

图17522 不同pH值条件下石灰石溶解率
可以看出,pH值越低,越有利于石灰石的溶解,其中当pH值为4.5时,石灰石溶解率在30min时达到最大。但pH值越高,越有利于SO2的吸收。为了保持吸收溶液的脱离效
果,一般选择pH值控制在5.0~5.6。
3)适量添加己二酸等添加剂。在石灰石浆液中加入一定量的己二酸等添加剂,可改善化学反应传质过程,能促进Ca-CO3的溶解并缓冲浆液pH值的下降,从而提高脱硫率。从一些科研试验研究结果可知,在试验条件下,当己二酸添加浓度
为0.15%时,CaCO3利用率可提高25%;相同脱硫率要求时,
可大大降低液气比,当己二酸添加浓度为0.15%、初始pH值为6.0、脱硫率为60%时,可有效降低液气比约40%;当己二酸添加量为0.15%,控制浆液pH值约6.0时,脱硫率可达70%以上。由此可见,添加己二酸添加剂可有效提高脱硫率和吸收剂的利用率,从而进一步降低脱硫运行成本。
(10)小结。
总结上述试验结果,270MW负荷下优化运行操作卡见表
17522。
表17522 270MW负荷下优化运行操作卡

270MW负荷下,通过优化调整试验,可以实现节约石灰石0.4t/h,以脱硫系统年运行6000h计,每年可节约石灰石2400t,约48万元;通过优化循环泵组合、吸收塔液位等方式,每小时节约用电27kWh,每年可节约用电162MWh,约
5.18万元;SO2平均排放浓度降低约30mg/m3,烟气量以1.5Mm3/h计,每年可减少SO2排放270t,可减少排污费
33.48万元。
2.300MW负荷下优化试验
(1)浆液pH值优化。
300MW负荷下浆液pH值与脱硫效率的关系曲线如图
17523所示。

图17523300MW负荷下浆液pH值与
脱硫效率的关系
300MW负荷、入口SO2浓度1700mg/m3条件下,石灰
石成本、排污费及两项合计费用变化见表17523。
表17523 300MW负荷、入口SO2浓度
1700mg/m3下不同的pH值优化

可以看出,pH值由5.3提高至5.6,石灰石浆液耗量增加0.89t/h,增幅为22.0%,石灰石成本和排污费合计增加
8.90%。在300MW负荷、入口SO2浓度1700mg/m3条件下,
pH值为5.3时,石灰石成本和SO2排污费两项费用合计最低,但脱硫效率为90.65%,为防止负荷变化时,脱硫效率低于90%,建议该条件下pH值应保持在5.35左右。此外,虽然pH值为5.1时与pH值为5.5时,两项费用合计相近,但低pH值运行会在入口SO2浓度较高时,存在SO2排放浓度超标的风险,因此不建议低pH值运行。
(2)浆液循环泵优化组合。
负荷为300MW下,实际运行操作中,投入2台浆液循环泵时,脱硫效率可以满足运行要求,AC泵运行时比AB泵运行时,脱硫效率高约0.9%,但电流高约1.7A,计算可得系统电耗增加约0.438%,脱硫系统运行费用约增加0.308%;而即使是原烟气SO2浓度为此负荷下最高的2172mg/m3时,AB泵运行脱硫效率仍可达91.44%,因此负荷正常投运 AB两台浆液循环泵即可。
(3)吸收塔液位优化。
300MW负荷下,吸收塔液位与脱硫效率的关系如图
17524所示。

图17524300MW负荷下吸收塔液位与
脱硫效率的关系
可以看出,随着吸收塔液位的增加,脱硫效率升高。当液位低于9.36m时,脱硫效率低于90%,无法满足运行要求。
试验表明,AB两台浆液循环泵运行时,吸收塔液位由
9.34m升至9.90m,AB泵总电流减少2.8A,脱硫系统运行
费用减少约7.91万元/年,此负荷下,建议液位控制在
9.4~9.7m。
(4)入口SO2影响。
实际运行中,300MW负荷下,原烟气SO2浓度在670~
2180kg/m3范围内波动,原烟气SO2浓度与脱硫效率的关系
如图17525所示。

图17525300MW负荷下原烟气SO2浓度与
脱硫效率的关系
(5)石灰石活性分析。
300MW负荷下理论石灰石耗量与实际石灰石耗量的对比
见表17524。
表17524 300MW负荷下理论石灰石耗量与
实际石灰石耗量的对比

可以看出,300MW负荷下理论石灰石耗量均值为
3.905t/h,而实际石灰石耗量均值为4.737t/h,石灰石多耗用
量平均值为0.832t/h。每天多消耗石灰石约20t,运行成本增
加4000元/天。
(6)小结。
总结上述试验结果,300MW负荷下优化运行操作卡见表
17525。
表17525 300MW负荷下优化运行操作卡

300MW负荷下,通过优化调整试验,可以实现节约石灰石0.3t/h,以脱硫系统年运行6000h计,每年可节约石灰石1800t,约36万元;通过优化循环泵组合、吸收塔液位等方式,
每小时节约用电27kWh,年可节约用电162MWh,约5.18万元;SO2平均排放浓度降低约30mg/m3,烟气量以1.65mm3/h
计,每年可减少SO2排放297t,可减少排污费36.8万元。
3.330MW负荷下优化试验
(1)浆液pH值优化。
330MW负荷下浆液pH值与脱硫效率的关系曲线如图
17526所示。

图17526330MW负荷下浆液pH值与
脱硫效率的关系
330MW负荷、入口SO2浓度1800mg/m3条件下,石灰
石成本、排污费及两项合计费用变化见表17526。
表17526330MW负荷、入口SO2浓度
1800mg/m3下不同的pH值优化

可以看出,pH值由5.3提高至5.5,石灰石浆液耗量增加0.50t/h,增幅为10.9%,石灰石成本和排污费合计增加
5.92%。在330MW负荷、入口SO2浓度1800mg/m3条件下,
pH值为5.3时,石灰石成本和SO2排污费两项费用合计最低,但脱硫效率为89.05%,建议该条件下pH值应保持在
5.4左右。此外,虽然pH值为5.1时与pH值为5.4时,两
项费用合计相近,但低pH值运行会在入口SO2浓度较高时,存在SO2排放浓度超标的风险,且脱硫效率低于90%考核值,因此不建议低pH值运行。
(2)浆液循环泵优化组合。
负荷为330MW下,实际运行操作中,维持稳定合适的pH值,投入2台浆液循环泵时,脱硫效率可以满足运行要求,AC泵运行时比AB泵运行时,脱硫效率高约0.7%,但电流高约1.8A,计算可得系统电耗增加约0.45%,脱硫系统运行费用约增加0.315%;而即使是原烟气SO2浓度为此负荷下最高的 2246mg/m3时,AB泵运行脱硫效率仍可达91.15%,因此此负荷正常投运AB两台浆液循环泵即可。
(3)吸收塔液位优化。
330MW负荷下,吸收塔液位与脱硫效率的关系如图
17527所示。

图17527330MW负荷下吸收塔液位与
脱硫效率的关系
可以看出,随着吸收塔液位的增加,脱硫效率升高。当液位低于9.37m时,脱硫效率低于90%,无法满足运行要求。
试验表明,AB两台浆液循环泵运行时,吸收塔液位由
9.54m升至9.92m,AB泵总电流减少2.3A,脱硫系统运行费
用减少约0.4%,此负荷下,建议液位控制在9.5~9.8m。
(4)入口SO2影响。
实际运行中330MW负荷下,原烟气SO2浓度在750~2250kg/m3范围内波动,原烟气SO2浓度与脱硫效率的关系
如图17528所示。

图17528330MW负荷下原烟气SO2浓度与
脱硫效率的关系
(5)石灰石活性分析。
300MW负荷下理论石灰石耗量与实际石灰石耗量的对比
见表17527。
表17527 330MW负荷下理论石灰石耗量与
实际石灰石耗量的对比

可以看出,300MW负荷下理论石灰石耗量均值为
3.773t/h,而实际石灰石耗量均值为4.652t/h,石灰石多耗用
量平均值为0.879t/h。每天多消耗石灰石约2lt,运行成本增
加4200元/天。
(6)小结。
总结上述试验结果,330MW负荷下优化运行操作卡见表
17528。
表17528 330MW负荷下优化运行操作卡

330MW负荷下,通过优化调整试验,可以实现节约石灰石0.3t/h,以脱硫系统年运行6000h计,每年可节约石灰石1800t,约36万元;通过优化循环泵组合、吸收塔液位等方式,
每小时节约用电27kWh,年可节约用电162MWh,约5.18万;SO2平均排放浓度降低约34mg/m3,烟气量以1.65mm3/h计,
每年可减少SO2排放336t,可减少排污费41.7万元。
4.360MW负荷下优化试验
(1)浆液pH值优化。
360MW负荷下浆液pH值与脱硫效率的关系曲线如图
17529所示。

图17529360MW负荷下浆液pH值与脱硫效率的关系
360MW负荷、入口SO2浓度1700mg/m3条件下,石灰
石成本、排污费及两项合计费用变化见表17529。
表17529 360MW负荷、入口SO2浓度
1700mg/m3下不同的pH值优化

可以看出,pH值由5.3提高至5.5,石灰石浆液耗量增加1.00t/h,增幅为22.9%,石灰石成本和排污费合计增加
14.18%。360MW负荷、入口SO2浓度1700mg/m3条件下,
pH值为5.2时,石灰石成本和SO2排污费两项费用合计最低,但pH值低于5.5时,脱硫效率低于90%,建议该条件下pH值应保持在5.5左右。
(2)浆液循环泵优化组合。
负荷为360MW下,实际运行操作中,维持稳定合适的pH值,投入两台浆液循环泵时,脱硫效率可以满足运行要求,AC泵运行时比AB泵运行时,脱硫效率高约0.9%,但电流高约2.0A,计算可得系统电耗增加约0.525%,脱硫系统运行费用约增加0.294%;而即使是原烟气SO2浓度为此负荷下最高的2391mg/m3时,AB泵运行脱硫效率仍可达90.77%,因此此负荷正常投运AB两台浆液循环泵即可。
(3)吸收塔液位优化。
360MW负荷下,吸收塔液位与脱硫效率的关系如图
17530所示。

图17530360MW负荷下吸收塔液位与
脱硫效率的关系
可以看出,随着吸收塔液位的增加,脱硫效率升高。当液位低于9.45m时,脱硫效率低于90%,无法满足运行要求。
试验表明,AB两台浆液循环泵运行时,吸收塔液位由
9.35m升至9.95m,AB泵总电流减少3.7A,脱硫系统运行费用减少约0.625%,此负荷下,建议液位控制在9.6~9.8m。
(4)入口SO2影响。
实际运行中360MW负荷下,原烟气SO2浓度在810~2400kg/m3范围内波动,原烟气SO2浓度与脱硫效率的关系
如图17531所示。

图17531360MW负荷下原烟气SO2浓度与
脱硫效率的关系
(5)石灰石活性分析。
360MW负荷下理论石灰石耗量与实际石灰石耗量的对比
见表17530。
表17530360MW负荷下理论石灰石耗量与
实际石灰石耗量的对比

可以看出,360MW负荷下理论石灰石耗量均值为
3.957t/h,而实际石灰石耗量均值为4.682t/h,石灰石多耗用
量平均值为0.725t/h。每天多消耗石灰石约18t,运行成本增
加3600元/天。
(6)小结。
总结上述试验结果,360MW负荷下优化运行操作卡见表
17531。
表17531 360MW负荷下优化运行操作卡

360MW负荷下,通过优化调整试验,可以实现节约石灰石0.5t/h,以脱硫系统年运行6000h计,每年可节约石灰石3000t,约60万元;通过优化循环泵组合、吸收塔液位等方式,每小时节约用电27kWh,年可节约用电162MWh,约
5.18万元;SO2平均排放浓度降低约27mg/m3,烟气量以1.66mm3/h计,每年可减少SO2排放269t,可减少排污费
33.4万元。
5.400MW负荷下优化试验
(1)浆液pH值优化。
400MW负荷下浆液pH值与脱硫效率的关系曲线如图1
7532所示。

图17532400MW负荷下浆液pH值与
脱硫效率的关系
400MW负荷、入口SO2浓度1800mg/m3条件下,石灰
石成本、排污费及两项合计费用变化见表17532。
表17532 400MW负荷、入口SO2浓度
1800mg/m3下不同的pH值优化

可以看出,pH值由5.3提高至5.5,石灰石浆液耗量增加1.00t/h,增幅为21.4%,石灰石成本和排污费合计增加
12.81%。400MW负荷、入口SO2浓度1800mg/m3条件下,
pH值为5.3时,石灰石成本和SO2排污费两项费用合计最低,但pH值低于5.5时,脱硫效率低于90%,建议该条件下pH值应保持在5.5左右。
(2)浆液循环泵优化组合。
负荷为400MW下,实际运行操作中,维持稳定合适的pH值,投入2台浆液循环泵,脱硫效率可以满足运行要求,AC泵运行时比AB泵运行时,脱硫效率高约0.8,但电流高约2.1A,计算可得系统电耗增加约0.575%,脱硫系统运行费用约增加0.403%;即使是原烟气SO2浓度为此负荷下最高
的2192mg/m3时,AB泵运行脱硫效率仍可达90.95%,因此
此负荷正常投运AB两台浆液循环泵即可。如实际运行中原烟气SO2浓度进一步升高,脱硫效率略低于90%,可运行 AC两台浆液循环泵。
(3)吸收塔液位优化。
400MW负荷下,吸收塔液位与脱硫效率的关系如图
17533所示。
可以看出,随着吸收塔液位的增加,脱硫效率升高。当液位低于9.50m时,脱硫效率低于90%,无法满足运行要求。

图17533400MW负荷下吸收塔液位与脱硫效率的关系
AC泵运行时不同液位下,循环泵、氧化风机电耗及两者
之和变化见表17533。
表17533 AC泵运行时吸收塔液位对电耗的影响

可以看出,循环泵流量不变的情况下,较高的工作液位可以增加循环泵入口工作压力,在一定范围内可以降低循环泵的工作电流,起到节能的作用。试验表明,AC两台浆液循环泵运行时,吸收塔液位由8.41m升至9.41m,AC泵总电流减少2.39A,循环泵与氧化风机电耗合计减少11kWh,运行成本降低3.52元/h,每年可节约2.11万元;同时,每提高1m工作液位,吸收塔浆液离子浓度约可以降低1/10,浆液饱和度降低,有利于SO2吸收。
在400MW负荷下,如果入口SO2浓度为1800mg/m3,液位由9.0m升至9.4m,出口 SO2浓度由195mg/m3降至
165mg/m3,排污费每年可减少约35万元,从优化系统运行性能的角度,在保证吸收塔不出现溢流的前提下,应尽量维持吸收塔在高液位运行,此负荷下,建议液位控制在9.6~9.8m。
(4)入口SO2影响。
实际运行中400MW负荷下,原烟气SO2浓度在1000~
2200kg/m3范围内波动,原烟气SO2浓度与脱硫效率的关系
如图17534所示。

图17534400MW负荷下原烟气SO2浓度与脱硫效率的关系
(5)石灰石活性分析
400MW负荷下理论石灰石耗量与实际石灰石耗量的对比
见表17534。
表17534400MW负荷下理论石灰石耗量与
实际石灰石耗量的对比

可以看出,400MW负荷下理论石灰石耗量均值为
4.173t/h,而实际石灰石耗量均值为4.922t/h,石灰石多耗用
量平均值为0.749t/h。每天多消耗石灰石约18t,运行成本增
加3600元/天。
(6)小结。
总结上述试验结果,400MW负荷下优化运行操作卡见表
17535。
表17535400MW负荷下优化运行操作卡

400MW负荷下,通过优化调整试验,可以实现节约石灰石0.45t/h,以脱硫系统年运行6000h计,每年可节约石灰石2700t,约54万元;通过优化循环泵组合、吸收塔液位等方式,每小时节约用电27kWh,年可节约用电162MWh,约
5.18万元;SO2平均排放浓度降低约20mg/m3,烟气量以1.7mm3/h计,每年可减少SO2排放204t,可减少排污费
25.3万元。
6.450MW负荷下优化试验
(1)浆液pH值优化。
450MW负荷下浆液pH值与脱硫效率的关系曲线如图1
7535所示。

图17535450MW负荷下浆液pH值与脱硫效率的关系
450MW负荷、入口SO2浓度1700mg/m3条件下,石灰
石成本、排污费及两项合计费用变化见表17536。
表17536450MW负荷、入口SO2浓度
1700mg/m3下不同的pH值优化

可以看出,pH值由5.3提高至5.5,石灰石浆液耗量增加1.18t/h,增幅为25.49%,石灰石成本和排污费合计增加
16.03%。450MW负荷、入口SO2浓度1700mg/m3条件下,
pH值为5.3时,石灰石成本和SO2排污费两项费用合计最低,但pH值低于5.5时,脱硫效率低于90%,建议该条件下pH值应保持在5.5左右。
(2)浆液循环泵优化组合。
负荷为450MW下,实际运行操作中,维持稳定合适的pH值,投入2台浆液循环泵时,脱硫效率可以满足运行要求,AC泵运行时比AB泵运行时,脱硫效率高约0.9%,但电流高约1.7A,计算可得系统电耗增加约0.575%,脱硫系统运行费用约增加0.305%;而即使是原烟气SO2浓度为此负荷下最高的2729mg/m3时,AB泵运行脱硫效率仍可达90.55%,因此此负荷正常投运AB两台浆液循环泵即可。如实际运行中原烟气SO2浓度进一步升高,脱硫效率略低于90%,可运行AC两台浆液循环泵。需要指出的是,此负荷条件下,要维持两台浆液循环泵运行,必须保证吸收塔处于较高液位运行。
(3)吸收塔液位优化。
450MW负荷下,吸收塔液位与脱硫效率的关系如图1
7536所示。

图17536450MW负荷下吸收塔液位与
脱硫效率的关系
可以看出,随着吸收塔液位的增加,脱硫效率升高。当液位低于9.55m时,脱硫效率低于90%,无法满足远行要求。
AD泵运行时不同液位下,循环泵、氧化风机电耗及两者
之和变化见表17537。
表17537 AD泵运行时吸收塔液位对电耗的影响

可以看出,循环泵流量不变的情况下,较高的工作液位可以增加循环泵入口工作压力,在一定范围内可以降低循环泵的工作电流,起到节能的作用。试验表明,AD两台浆液循环泵运行时,吸收塔液位由8.90m升至9.65m,AD泵总电流减少2.92A,循环泵与氧化风机电耗合计减少34kWh,运行成本降
低10.88元/h,每年可节约6.53万元;同时,每提高1m工
作液位,吸收塔浆液离子浓度约可以降低1/10,浆液饱和度降低,有利于SO2吸收。
在450MW负荷下,如果入口SO2浓度为1700mg/m3,液位由9.0m升至9.6m,出口 SO2浓度由192mg/m3降至
160mg/m3,排污费约可减少47万元/年,从优化系统运行性能的角度,在保证吸收塔不出现溢流的前提下,应尽量维持吸收塔在高液位运行,此负荷下,建议液位控制在9.6~9.8m。
(4)入口SO2影响。
实际运行中450MW负荷下,原烟气SO2浓度在1010~
2800kg/m3范围内波动,原烟气SO2浓度与脱硫效率的关系
如图17537所示。

图17537450MW负荷下原烟气SO2浓度与
脱硫效率的关系
(5)石灰石活性分析。
450MW负荷下理论石灰石耗量与实际石灰石耗量的对比
见表17538。
可以看出,450MW负荷下理论石灰石耗量均值为
5.192t/h,而实际石灰石耗量均值为5.830t/h,石灰石多耗用
量平均值为0.638t/h。每天多消耗石灰石约15t,运行成本增
加3000元/天。
(6)小结。
总结上述试验结果,450MW负荷下优化运行操作卡见表
17539。
表17538 450MW负荷下理论石灰石耗量与
实际石灰石耗置的对比

表17539 450MW负荷下优化运行操作卡

450MW负荷下,通过优化调整试验,可以实现节约石灰石0.5t/h,以脱硫系统年运行6000h计,每年可节约石灰石3000t,约60万元;通过优化循环泵组合、吸收塔液位等方式,每小时节约用电30kWh,每年可节约用电180MWh,约
5.76万元;SO2平均排放浓度降低约32mg/m3,烟气量以1.9mm3/h计,每年可减少SO2排放365t,可减少排污费
45.2万元。
7.500MW负荷下优化试验
(1)浆液pH值优化。
500MW负荷下浆液pH值与脱硫效率的关系曲线如图1
7538所示。

图17538500MW负荷下浆液pH值与
脱硫效率的关系
500MW负荷、入口SO2浓度1700mg/m3条件下,石灰
石成本、排污费及两项合计费用变化见表17540。
可以看出,pH值由5.3提高至5.5,石灰石浆液耗量增加1.04t/h,增幅为20.7%,石灰石成本和排污费合计增加
16.72%。500MW负荷、入口SO2浓度1700mg/m3条件下,
pH值为5.3时,石灰石成本和SO2排污费两项费用合计最
低,但pH值低于5.5时,脱硫效率低于90%,建议该条件下pH值应保持在5.5左右。
表17540500MW负荷、入口SO2浓度
1700mg/m3下不同的pH值优化

(2)浆液循环泵优化组合。
500MW负荷下,实际运行操作中,维持稳定合适的pH值,投入2台浆液循环泵时,脱硫效率可以满足运行要求,AC泵运行时比AB泵运行时,脱硫效率高约0.7%,但电流高约2.5A,计算可得系统电耗增加约0.625%,脱硫系统运行费用约增加0.438%;而即使是原烟气SO2浓度为此负荷下
最高的2291mg/m3时,AB泵运行脱硫效率仍可达91.19%,
因此此负荷正常投运AB两台浆液循环泵即可。如实际运行中原烟气SO2浓度进一步升高,脱硫效率略低于90%,可运行AC或AD两台浆液循环泵。需要指出的是,此负荷条件下,要维持两台浆液循环泵运行,必须保证吸收塔处于较高液位运行。
(3)吸收塔液位优化。
500MW负荷下,吸收塔液位与脱硫效率的关系如图1
7539所示。

图17539500MW负荷下吸收塔液位与
脱硫效率的关系
可以看出,随着吸收塔液位的增加,脱硫效率升高。当液位低于9.60m时,脱硫效率低于90%,无法满足运行要求。
试验表明,AB两台浆液循环泵运行时,吸收塔液位由
9.33m升至9.91m,AB泵总电流减少3.7A,脱硫系统运行费用减少约0.675%,此负荷下,建议液位控制在9.8~10.1m。
(4)入口SO2影响。
实际运行中500MW负荷下,原烟气SO2浓度在1010~
2300kg/m3范围内波动,原烟气SO2浓度与脱硫效率的关系
如图17540所示。

图17540500MW负荷下原烟气SO2浓度与
脱硫效率的关系
(5)石灰石活性分析。
500MW负荷下理论石灰石耗量与实际石灰石耗量的对比
见表17541。
表17541500MW负荷下理论石灰石耗量与
实际石灰石耗量的对比

可以看出,500MW负荷下理论石灰石耗量均值为5.458t/h,而实际石灰石耗量均值为6.398t/h,石灰石多耗用量平均值
为0.940t/h。每天多消耗石灰石约23t,运行成本增加4600元/
天。需要指出的是,此负荷下,当原烟气 SO2浓度达到
3170mg/m3时,石灰石浆液浓度为1233kg/m3,即使石灰石浆
液按最大量加入(实际运行中可达41m3/h),此时石灰石实际
耗量达15.52t/h(理论耗量为11.00t/h),吸收塔浆液pH值仅
可维持在5.33左右,脱硫效率仍低于90%,此时应根据负荷变化情况,提前提高石灰石浆液密度(平时应保持在1250kg/m3左右),保证浆液供给,维持吸收塔浆液pH值高于5.5。
(6)小结。
总结上述试验结果,500MW负荷下优化运行操作卡见表
17542。
表17542500MW负荷下优化运行操作卡

500MW负荷下,通过优化调整试验,可以实现节约石灰石0.6t/h,以脱硫系统年运行6000h计,每年可节约石灰石3600t,约72万元;通过优化循环泵组合、吸收塔液位等方式,
每小时节约用电35kWh,每年可节约用电210MWh,约6.72万
元;SO2平均排放浓度降低约30mg/m3,烟气量以2.0mm3/h
计,每年可减少SO2排放360t,可减少排污费44.6万元。
8.550MW负荷下优化试验
与低负荷不同,550MW负荷时,pH值、吸收塔液位、循环泵组合、入口SO2浓度相互影响较大,特别是循环泵组合变得更为多样且复杂,不同循环泵运行组合下,循环泵、氧化风机电耗及两者之和变化见表175 43~表17545。表17543 CD泵运行时吸收塔液位对电耗的影响

表17544 ABD泵运行时吸收塔液位对电耗的影响

表17545 ACD泵运行时吸收塔液位对电耗的影响

CD两台浆液循环泵运行时,吸收塔液位由8.59m升至9.87m,CD泵总电流减少3.01A,循环泵与氧化风机电耗合
计减少22kWh,运行成本降低7.04元/h,每年可节约4.22
万元。ABD三台浆液循环泵运行时,吸收塔液位由8.45m升至9.80m,ABD泵总电流减少4.30A,循环泵与氧化风机电耗合计减少44kWh,运行成本降低14.08元/h,每年可节约8.45万元。ACD三台浆液循环泵运行时,吸收塔液位由
8.45m升至9.63m,ACD泵总电流减少3.73A,循环泵与氧
化风机电耗合计减少30kWh,运行成本降低9.60元/h,每年
可节约5.76万元。
550MW负荷下,如果入口SO2浓度为1800mg/m3,液位由9.0m升至9.6m,出口SO2浓度由199mg/m3降至165mg/
m3,排污费约可减少56万元/年,从优化系统运行性能的角度,在保证吸收塔不出现溢流的前提下,应尽量维持吸收塔在高液位运行,此负荷下,建议液位控制在9.5~9.9m。
试验过程中原烟气SO2浓度在1560~2240kg/m3范围内
波动,试验保证脱硫效率不小于90%,550MW负荷下优化运
行操作卡见表17546。
表17546550MW负荷下优化运行操作卡

需要指出的是,当原烟气浓度在1800mg/m3左右时,ABC泵运行比AC泵运行时的电流高出约56A,每小时电耗增加约824kWh,系统运行费用增加264元/h,而AC泵运行比ABC泵运行时的石灰石浆液耗量增加约0.6t/h,系统运行费用增加约120元/h,因此,在此条件下,尽量通过提高吸收塔液值、增加石灰石供浆量的方式来维持脱硫效率,从而大大减少系统运行费用。同理,当原烟气浓度在2000mg/m3左右时,也尽量维持ABC泵运行,提高吸收塔液位,增加供浆量,系统电耗约可减少1.33%。
550MW负荷下,通过优化调整试验,可实现节约石灰石0.6t/h,以脱硫系统年运行6000h计,每年可节约石灰石3600t,约72万元;通过优化循环泵组合、吸收塔液位等方式,
每小时节约用电40kWh,每年可节约用电240MWh,约7.68万
元;SO2平均排放浓度降低约40mg/m3,烟气量以2.2×106m3/h计,每年可减少SO2排放528t,可减少排污费65.5万元。
9.600MW负荷下优化试验
与550MW负荷时相同,pH值、吸收塔液位、循环泵组合、入口SO2浓度相互影响较大,特别是循环泵组合变得更
为多样复杂,试验过程中原烟气SO2浓度在1788~2140kg/m3
范围内波动,试验保证脱硫效率不低于90%,600MW负荷下优化运行操作卡见表17547。
表17547 600MW负荷下优化运行操作卡

需要指出的是,当原烟气浓度在1700mg/m3左右时,ABC泵运行比AC泵运行时的电流高出约56A,每小时电耗增
加824kWh,系统运行费用增加264元/h,而 AC泵运行比
ABC泵运行时的石灰石浆液耗量增加约0.7m3/h,系统运行费用增加约140元/h,因此,在此条件下,尽量通过提高吸收塔液位、增加石灰石供浆量的方式来维持脱硫效率,从而大大减少系统运行费用。同理,当原烟气浓度在2100mg/m3左右时,也尽量维持ABD泵运行,提高吸收塔液位,增加供浆量,系统电耗约可减少1.33%。
600MW负荷下,通过优化调整试验,可实现节约石灰石0.7t/h,以脱硫系统年运行6000h计,每年可节约石灰石4200t,约84万元;通过优化循环泵组合、吸收塔液位等方式,每小时节约用电45kWh,每年可节约用电270MWh,约
8.64万元;SO2平均排放浓度降低约50mg/m3,烟气量以2.3mm3/h计,每年可减少SO2排放690t,可减少排污费
85.6万元。
10.优化综合分析
以2011年5月机组负荷统计情况为例,机组负荷情况如
表17548所示。
表17548 2011年5月机组负荷情况

通过优化运行试验,可实现节约石灰石0.53t/h,每年可节约石灰石3180t,约64万元;通过优化循环泵组合、吸收塔液位等方式,每小时节约用电30.67kWh,每年可节约用电
184.020MWh,约5.89万元;每年可减少SO2排放323.67t,
可减少排污费40.14万元。通过优化运行每年可节约运行成本总计约110万元。
通过分析可以看出,要维持稳定的脱硫效率,维持稳定的钙硫比、高的液气比是关键,优化循环泵组合、降低石灰石浆液耗量则是减少脱硫系统能耗的关键,总结见表17549。表17549 主要运行参数与脱硫性能的关系

注“↑”表示增加,“↓”表示降低,“↑↑”表示显著增加,“—”
表示不显著。
11.存在问题
(1)入口粉尘超标。
某同类型机组,在吸收塔入口烟气量为1800~2000km3/
h、入口SO2浓度为1700~2000mg/m3、pH值为5.4和出口
烟气含氧量为6.7%(体积分数)左右波动的工况条件下,入口含尘量与脱硫效率的影响关系如图17541所示。
续表

图17541 入口烟尘含量与脱硫效率的关系曲线
可以看出,随着FGD系统中入口含尘量的升高,脱硫效率逐渐降低。一般脱硫系统设计值要求吸收塔入口的烟气含尘量不高于100mg/m3,有研究证实烟尘中的飞灰在一定程度上阻碍了SO2与脱硫剂的接触,降低了石灰石中Ca2+的溶解速率,同时飞灰中不断溶出的一些重金属,会抑制 Ca2+与HSO3-的反应,导致浆液pH值降低,脱硫效率下降。因此应通过控制电除尘器降低含尘量,以获得较高的脱硫效率。

可以看出,增压风机导叶开度增加,增压风机入口负压随之增加,增压风机电流大幅攀升,500MW负荷时,增压风机
入口负压由-132.65Pa变为-252.94Pa,增压风机每小时电
试验期间原烟气粉尘浓度始终高于100mg/m3,部分时段高于300mg/m3,对脱硫系统实际运行效果有所影响。
(2)GGH压差大。
耗增加331kWh,电耗增加显著,因此正常运行时增压风机入口负压应维持在-50~-100Pa。优化试验期间风机导叶为手动调整,造成负荷变化时入口压力波动较大,应尽快投入风机入口压力自动。目前满负荷运行条件下,风机导叶开度70%左右,增压风机裕量充足。
低负荷运行时,GGH压差高于400Pa,满负荷运行时GGH压差高达800Pa以上,远高于设计值,致使系统电耗(主要是增压风机电耗)明显增加,而且脱硫系统运行可靠性显著降低,应通过电除尘运行维护或改造降低烟气粉尘浓度,加强除雾器、GGH冲洗,降低烟气携带液滴量和液滴携固量。
(二)某600MW机组烟气脱硫系统优化运行案例
(3)增压风机入口负压大。
某5×600MW机组的烟气脱硫工程按单元制设计,采用一炉一塔、塔内强制氧化的石灰石—石膏湿法脱硫工艺。其系统主要由石灰石浆液制备系统、烟气系统、吸收塔系统、工艺水系统、石膏脱水系统、浆液疏排系统、废水处理系统及压缩空气系统等组成。
增压风机通常不作为脱硫系统优化的调整对象。但优化运行试验期间调整增压风机入口压力明显偏大,维持-300Pa左右,造成部分净烟气回流,增加系统电耗,正常情况应维持增压风机入口压力在-100Pa左右,并保证烟气能克服脱硫系统阻力(包括GGH在内),但应注意避开风机的失速区。
脱硫装置运行优化试验主要进行了浆液循环泵优化、氧化风机优化、pH值控制系统优化。
1.浆液循环泵运行优化
试验期间不同负荷下,增压风机入口压力与增压风机的电
流关系见表17550。
表17550 增压风机入口压力与增压风机的电流关系

脱硫系统配置3台浆液循环泵,按设计要求FGD运行时三台泵同时运行,无备用。在实际运行中,当烟气中SO2质量浓度较低、脱硫效率较高时,可停运一台浆液循环泵,达到减小电耗的目的。优化运行试验以参数的大小为指导依据,通过比较,找到较优的浆液循环泵运行方式;在此基础上,找到一个合适值,当FGD入口SO2浓度低于该值时,通过停运一台浆液循环泵来实现脱硫装置的经济运行。
吸收塔浆液pH值控制在5.3左右,液位控制在8.2m,石灰石供浆浓度控制在1250kg/m3,氧化风机两台运行。经济指标计算依据为:上网电价按0.40元/kWh计算;石灰石粉价格
为270元/t;石灰石纯度为95%;Ca/S为1.03;脱硫装置年运
行按5500h计;在燃烧该煤种时标准状态下SO2质量浓度在
2770~2973mg/m3范围内波动;SO2排污费用为0.63元/kg。
优化试验在三种不同机组负荷(350MW、400MW、
450MW)下,进行三台浆液循环泵运行与两台浆液循环泵运行的比较试验(停运的浆液循环泵均为A泵)。试验共进行了
六个不同循环泵组合的工况,分别为工况1(负荷450MW,
ABC泵运行)、工况2(负荷450MW,BC泵运行)、工况3(负荷400MW,ABC泵运行)、工况4(负荷400MW,BC泵运行)、工况5(负荷350MW,ABC泵运行)、工况6(负荷
质量流量的变化而变化。氧化风机的优化思路与浆液循环泵的优化思路一致,通过比较试验,找到最优的运行氧化风机方式,来保证FGD氧化风的合理供给,试验数据及经济指标见
表17553和表17554。
350MW,BC泵运行)。主要试验结果及经济指标见表1 7
表17553 不同负荷工况下氧化风机优化试验结果
551和表17552。
表17551 不同负荷工况下循环泵优化试验结果


注 工况1和工况3为氧化风机AB运行,工况2和工况4为氧化风
机B运行。
表17554 不同负荷工况下氧化风机
优化运行主要经济指标
表17552 不同负荷工况下循环泵优化
运行主要经济指标


注 工况1和工况3为氧化风机AB运行,工况2和工况4为氧化风
机B运行。
根据试验结果可以看出,通过调整氧化风机运行方式所取得的经济效益较小。在实际运行中发现,吸收塔内长时间氧化风供给不足,会造成吸收塔内亚硫酸盐含量的不断增加,石膏脱水效果变差,并最终导致脱水系统不能运行,因此为吸收塔提供适量的氧化风是保证FGD稳定运行的前提。
可以看出:电费占整个FGD总运行费用的60%,石灰石消耗费用约占总运行费用的40%;机组负荷越低,通过停运一台浆液循环泵的经济效益越明显;值的选取要根据实际的运行情况来确定。
3.pH值优化
烟气脱硫系统的石灰石浆液的补充由吸收塔浆液pH值进行控制,pH值的大小决定了FGD的脱硫效率。为找到吸收塔浆液运行的较佳pH值范围,进行试验对比,试验数据及经
通过上述试验分析,并结合某600MW机组脱硫装置实际运行过程中检修、电动机启动频率的要求等各种因素,制定浆液循环泵的优化运行三种工况为:
济指标计算见表17555和表17556。
表17555 不同负荷工况下pH值优化试验结果
(1)原烟气SO2质量浓度低于2100mg/m3,机组负荷小
于450MW。
(2)原烟气SO2浓度为2100~2400mg/m3,机组负荷小于400MW。
(3)原烟气SO2浓度为2400~2750mg/m3,机组负荷小于350MW。

当机组在以上三种工况下运行,并预计该负荷下连续运行8h以上时,FGD停运一台浆液循环泵运行;如果机组运行工况超出以上三个工况的范围,且脱硫效率小于90%,启动停运的浆液循环泵。
表17556 不同负荷工况下pH优化运行
主要经济指标
2.氧化风机运行优化
烟气脱硫装置配置了3台氧化风机(两运一备),提供氧化反应所需要的氧化空气。启用氧化风机过多,浪费电能;反之,启用氧化风机过少,必然会引起氧化反应不够充分,脱硫效率下降等问题。因此氧化风机的投运数量应随脱硫系统SO2

从表17555中可知,吸收塔浆液的pH值越高,脱硫率越高,石膏中CaCO3的质量分数也就越高,相应增大了Ca/S,石灰石耗量也就增加了。三种工况下各项性能指标相差不大,也可以看出工况1是最佳工况,既可以达到较高的脱硫效率,又可以实现较低的 Ca/S,并且此时 CaSO4· 1/2H2O的含量最低。工况1的脱除单位质量SO2相对成本
0.5%、pH值不同的情况下,相对运行成本差别不大,但考虑石膏品质及石灰石利用效率,应尽量低pH值运行,因此在
此工况下pH值取5.0~5.2。
表17558 机组负荷为650MW时脱硫
装置的相对运行成本
为0.347元/kg,较其他工况低。
总体来说,pH值在5.15~5.35范围内波动,对脱硫系统的经济效益影响不大,这主要是因为节省下来的石灰石成本与增加的SO2排污费用的成本相差不多。在实际的运行操作中,采用过高或过低的pH设定值运行,不利于脱硫系统的安全稳定运行,操作规程中规定pH值必须维持在5.2~5.4范围内。
4.优化运行经济效益分析

根据试验结论及得出的优化运行方案,在脱硫系统实施,表17557是根据优化运行试验结果调整后的脱硫系统运行数据。
2.浆液循环泵运行优化
(1)燃煤含硫量为0.6%、主机负荷为500MW时循环泵的运行优化。
表17557
优化运行后脱硫系统电耗
当燃煤含硫量为0.6%、主机负荷为500MW、烟气流量
占发电量比例
%
均值为1.805mm3/h、入口SO2的质量浓度均值为1362mg/

m3、循环泵投运方式不同时,脱硫装置相对运行成本见表1
7559。
由表17559可见,停运循环泵A或B,相对于三台循环浆液泵全部运行的情况,厂用电率分别降低约13.2%和
14.8%,相对运行成本分别降低8.23%和8.58%。
(2)燃煤含硫量为0.6%、主机负荷为350MW时循环泵的运行优化。
当燃煤含硫量为0.6%、主机负荷为350MW、烟气流量
均值为1.473mm3/h、入口SO2的质量浓度均值为1329mg/
从表17557中可以看出,节能运行方式的实施,使脱硫系统用电占总发电量的比例从8月的1.35%开始逐月下降到12月的1.21%,通过优化脱硫运行方式,取得了很好的经济效益。
m3、循环泵投运方式不同时,脱硫装置相对运行成本见表1
7560。
由表17 5 60可见,停运循环泵A、B、C中任意一台,相对于三台循环泵全部运行,厂用电率分别降低约
(三)某电厂660MW机组烟气脱硫系统优化运行案例
18.9%、21.1%、22.6%,相对运行成本分别降低10.58%、10.90%、11.25%。当pH值约为5.5时,即使停运最顶层的
某电厂660MW机组烟气脱硫工程设计燃煤含硫量为0.52%,由于其设计裕量较大,在满负荷工况下,燃煤的含硫量达到0.8%时,通过运行调整,脱硫效率仍可达到92%以上。在SO2排放质量浓度满足国家环保要求的前提下,如何优化运行以降低成本就成为脱硫系统运行的关键所在。
循环泵C,脱硫效率仍可达到92%以上。为降低钙硫摩尔比,可适当将pH值降至5.3左右,脱硫效率仍可在90%以上。
(3)燃煤含硫量为0.8%、主机负荷为500MW时循环泵的运行优化。
某电厂660MW杌组采用石灰石—石膏湿法烟气脱硫装置,烟气系统设有GGH,制浆系统所用石灰石粉为直接外买,设两级脱水,石膏外售。锅炉最大连续蒸发量工况下,设计参
当燃煤含硫量为0.8%、主机负荷为500MW、烟气流量
均值为 1.811mm3/h、入口 SO2的质量浓度均值为
1671mg/m3、循环泵投运方式不同时,脱硫装置相对运行成本
数为:入口烟气量2395655m3/h(实际工态)或2218279m3/h
见表17561。
(标准工态),入口SO2质量浓度1089mg/m3(标准状态,氧
气的体积分数为6%),脱硫效率不低于90%。
运行成本中,脱硫系统总的相对运行成本计为C,电费计
由表17561可见,停运循环泵A,pH值提高到近5.7时,脱硫效率仍无法达到90%,在此工况下不能停运浆液循环泵A,三台浆液循环泵需全部投入运行。
C1、脱硫剂费用计C2,水费计C3,此外,SO2排污费计C4,
石膏销售收入计C5。
(4)燃煤含硫量为0.8%、主机负荷为350MW时循环泵的运行优化。
1.pH值运行优化
当燃煤含硫量为0.8%、主机负荷为350MW、烟气流量
三台循环泵全投运、主机负荷为650MW、烟气流量均值
均值为 1.473mm3/h、入口 SO2的质量浓度均值为
为2.181×106m3/h(标准状态,下同)、入口SO2质量浓度均
1689mg/m3、循环泵投运方式不同时,脱硫装置相对运行成本
值为1076mg/m3、pH值不同时,脱硫装置相对运行成本见表
见表17562。
17558。
由表17558可见,随着pH值的增加,脱硫效率增加,同时钙硫摩尔比变大,石灰石耗量增加。综合石灰石成本、排污费及石膏收益,在满负荷工况、燃煤含硫量约
由表17 5 62可见,停运循环泵A、B、C中任何一台,相对于三台循环泵全部运行厂用电率分别降低约18.9%、
21.1%、22.6%,相对运行成本分别降低8.97%、9.64%、8.67%。
表17559
机组负荷为500MW、燃煤含硫量为0.6%时脱硫装置的相对运行成本

表17560
机组负荷为350MW、燃煤含硫量为0.6%时脱硫装置的相对运行成本

表17561
机组负荷为500MW、燃煤含硫量为0.8%时脱硫装置的相对运行成本

表17562
机组负荷为350MW、燃煤含硫量为0.8%时脱硫装置的相对运行成本

(四)某电厂烟气脱硫系统优化运行案例
某电厂脱硫系统的主要性能考核指标见表17563,针对此指标,通过试验确定一个最佳的吸收塔浆液pH值运行范围,以达到在满足脱硫效率的同时,提高石灰石利用率的目的;通过试验确定一个最佳的吸收塔浆液密度运行范围,以达到满足石膏含水率的同时,提高石灰石利用率的目的;通过试验,设计出一个合理的除雾器冲洗程序,以达到满足除雾器冲洗效果的同时,平衡脱硫系统补水和用水的目的;通过试验,研究不同负荷、不同进口SO2浓度下的最优吸收塔循环泵运行组合,以达到满足脱硫效率的同时,降低脱硫系统电耗的目的。
由于pH值采用自动控制方式,在实际运行中会有一定的波动,波动范围大致为±0.05。试验期间浆液循环泵运行3台
(BCD泵),氧化风机运行2台,浆液密度为1100~1130kg/m3,试验结果见表17564。
表17564 不同pH值下脱硫效率、石膏成分、
Ca/S试验结果
表17563
某电厂6号机组脱硫系统主要性能指标

1.pH值运行优化
在机组满负荷为1000MW,入口 SO2浓度为1489~
1635mg/m3的工况下进行试验。试验期间,分别将浆液pH值
设定在5.1、5.2、5.3、5.4、5.5、5.6六个工况进行试验,

Ca/S与浆液pH值的关系如图17542所示。


图17542 脱硫效率、Ca/S随pH值变化的曲线
图17543 石膏中CaSO4·2H2O、CaCO3含量
随浆液密度变化的曲线
从图17542中可以看出,在试验范围内,脱硫效率、钙硫比都随着吸收塔浆液pH值的升高而升高;但脱硫效率随pH值的增长率在pH值小于5.3时较大,在pH值大于5.3时较小;而钙硫比随pH值的增长率在pH值小于5.3时较小,在pH值大于5.3时较大。即在pH值大于5.3时,虽然脱硫效率也随着pH值增大而逐渐增大,但增大的幅度有限,而Ca/S却提高较多,将pH值控制在5.3以上的工况,Ca/S都超过了1.03的性能考核值。对比这六个试验工况,工况3的综合效果是最佳的,即pH值在5.25~5.35范围内,即可达到设计的脱硫效率,石膏中CaCO3的含量也较低,钙硫比也低于1.03的性能考核值,是一个理想的控制点。
2.吸收塔浆液密度运行优化
控制合理的吸收塔浆液密度,不仅有利于提高石灰石利用率和石膏品质,而且对减少浆液结垢和设备磨损都是十分有益的。

CaSO4 ·2H2O、CaCO3含量随吸收塔浆液密度的变化曲
图17544 石膏含水率和脱水皮带机真空度随
线如图17543所示。
吸收塔浆液密度变化的曲线
由图1 7 5 43可以看出,CaSO4 ·2H2O含量随着吸
收塔浆液密度的增大而升高,CaCO3含量随吸收塔浆液密度的增大而减少,吸收塔浆液密度较低时,CaCO3含量随吸收塔浆液密度的增大减少较为明显,当吸收塔浆液密度大于1130kg/·时,CaCO3含量随吸收塔浆液密度的增大变化较少,这表明当吸收塔浆液密度大于1130kg/m3时,石灰石的利用已经比较彻底。
大而减小。同时,较高的吸收塔浆液密度还会加剧设备的磨损和结垢,因此通过试验,确定吸收塔浆液密度的最佳运行区间
为1100~1130kg/m3。
3.除雾器运行优化
除雾器冲洗程序的优劣对除雾器性能和脱硫系统内水平衡至关重要。针对某发电厂机组所采用的二级屋脊式除雾器,经过优化调整试验,确定1000MW时除雾器冲洗程序,如图
石膏含水率和脱水皮带机真空度随吸收塔浆液密度变化的曲线如图175 44所示,脱水皮带机真空度随着吸收塔浆液密度的增大而增大;但是石膏含水率并没有随着吸收塔浆液密度的增大而持续减小,而是当吸收塔密度在1130kg/m3左右时达到最小,为8.7%。这表明,随着吸收塔浆液密度的增大,浆液中CaSO4 ·2H2O含量增加,石膏晶体粒径也在逐步增大,这样有利于石膏脱水;但是当石膏晶体过大时,在吸收塔搅拌器的作用下,这些大粒径的石膏晶体被破碎成针状或片状,从而导致了脱水皮带机滤布堵塞,反而不利于石膏脱水,
175 45所示。
该冲洗程序的特点是,针对雾滴主要被第一级除雾器收集的特点,加强对第一级除雾器下面的冲洗强度。同时,根据脱硫系统内的水平衡情况,机组在1000MW负荷运行时设计单个阀门的冲洗时间为1min,机组在800MW负荷运行时,单个阀门的冲洗时间为0.8min,当机组运行在更低负荷时,可适当减少单个阀门的冲洗时间,以保证脱硫系统内水平衡的要求。
如图17544所示,吸收塔浆液密度为1140kg/m3、
4.浆液循环泵运行优化
1150kg/m3的工况,脱水皮带机真空度随着吸收塔浆液密度的增大而增大,但是石膏含水率并没有随着吸收塔浆液密度的增
烟气脱硫系统设置4台浆液循环泵,各泵主要技术参数见
表17565。

图175451000MW负荷下除雾器冲洗程序
表17565
浆液循环泵主要技术参数

在满足脱硫效率要求的前提下,当不同负荷和不同进口SO2浓度时,确定的最优吸收塔循环泵运行方案如图17
5 46所示。
总之,脱硫系统优化运行是一个复杂的系统工程,优化试验的方案也需要通过不断的实践予以改进。安全性是所有优化工作的前提,经济合理性是优化工作的最终目的,通过优化运行得到的试验结论随着脱硫系统烟气特性及设备性能的改变,其适应性也会发生改变,此时就需要进一步修正更新优化运行试验结论,为运行人员提供准确的运行操作指导,确保烟气脱硫系统的安全、稳定、连续、经济运行。

图17546 吸收塔浆液循环泵最优运行组合
第六节 FGD对机组的扰动分析
本节以某电厂FGD系统为对象,详细研究了FGD系统对发电机组的影响。
一、FGD系统对锅炉运行的影响
(一)相关系统简介
FGD系统与锅炉的联系是通过FGD进、出口两个挡板及旁路(即锅炉原有引风机出口至烟囱的烟道)的两个挡板进行着烟气的切换。图1761为FGD系统与烟气系统的关系
简图,图1762、图1763为现场FGD系统进出口
烟道照片。
FGD系统的主烟道烟气挡板安装在FGD的进、出口,它是由双层烟气挡板组成的,如图1764所示。旁路烟道烟气挡板安装在旁路烟道的进、出口,是单层设计的,当烟气进入主烟道时,旁路烟道关闭,这时两个旁路烟道的烟气挡板间连接密封空气。旁路烟气挡板设有弹簧快开机构,如图1 765所示,保证在安全要求下迅速打开旁路烟道,确保锅炉的正常运行。四个烟气挡板由英国EFFOX公司生产,主要技术参数的特性列于表1761中,正常情况下,烟气系统的启停由程控操作,当满足FGD系统启停条件时,运行人员在控制屏上设定“功能组烟气系统自动”,点按键盘后,系统便按表1762的程序一步步地执行下去。挡板可手动操作,也可就地操作。

图1761 FGD系统与烟气系统的关系简图
P、T—压力、温度测点;SO2、O2—二氧化硫、氧量测点;Q—烟气流量测点;Dust—粉尘浓度测点


图1762 现场FGD系统进出口烟道
图1763 现场FGD系统出口烟道


图1764 双层烟气挡板
图1765 预拉弹簧快开机构
表1761
烟气挡板的特性
续表


表1762
烟气系统程控操作

续表
试验研究加以阐述。

(二)FGD系统对锅炉影响的冷态试验研究
1.单炉运行
在1号炉上进行了试验,试验时送、引风机的电流参照锅炉热态满负荷的数值,试验参数列于表176 4中,试验结
果见表1765。
表1764
冷态试验参数(1号炉)
但FGD保护动作时,FGD旁路挡板通过预拉弹簧在2s之内打开,保护条件及保护的相应列于表1763中。
表1763
FGD系统的保护


表1765 冷态试验结果(1号炉)
另外,在下列两种情况下,FGD系统将向锅炉控制发出请求锅炉主燃料跳闸(MFT)的申请。
(1)2台循环泵停运,并且FGD入口烟气挡板和出口烟气挡板都未关闭。

(2)FGD入口烟温高过190℃(3取2),并且FGD入口烟
气挡板和出口烟气挡板都未关闭。
当FGD启、停时,烟气进行由旁路和主路的切换,由于两路烟道的阻力不一样,此时会对锅炉的炉膛负压产生明显的影响,若设计不合理,将使锅炉 MFT,甚至危及锅炉炉膛的安全。图1766所示为一个典型FGD系统,FGD旁路挡板没有快开装置,FGD阻力由增压风机来克服。假定在运行中增压风机出现了故障,而停运或FGD进出、口挡板误关时,会发生什么样的情况呢?旁路不能快速打开,烟气无路可走,烟道阻力迅速增加,必然导致锅炉炉膛压力升高,引起 MFT。这种情况在深圳妈湾电厂海水FGD系统的运行中就发生了,另外在重庆电厂的FGD系统调试过程中,都发生过因FGD系统投运造成锅炉跳闸的事件。
从表1765可看出,冷态单炉运行FGD启停时对锅炉炉膛负压影响不大,但当烟气从FGD主路快速切换至FGD旁路(通过预拉弹簧在2s内打开旁路)时,负压的变化明显高于FGD正常启停。
2.双炉运行
双炉运行冷态试验参数列于表1766中,试验时锅炉未作任何调整,试验结果见表1767。
表1766 双炉运行冷态试验参数

图1766 典型的FGD系统
FGD不同运行状况对锅炉运行会造成不同扰动,下面通过

表1767 双炉运行冷态试验结果
序号 试验项目
1号炉试验结果
2号炉试验结果


图1769 双炉运行冷态时FGD主路快速切换
至旁路炉膛负压的变化曲线
图1767~图1769是从CRT上直接打印出的曲
FGD系统停运时负压变化正相反。
线,分别表示双炉运行冷态时FGD旁路正常切换至主路炉膛负压的变化、FGD主路正常切换至旁路炉膛负压的变化、FGD主路快速切换至旁路炉膛负压的变化。
(2)双炉运行时,FGD系统的启停对锅炉炉膛负压的影响要比单炉运行时的影响大。

(3)当烟气从FGD主路快速切换至FGD旁路(通过预拉弹簧在2s内打开旁路)时,膛负压的变化明显变大,且变化的时间很短。可以预见在热态时,FGD系统的启停将对炉有更大的影响。
(三)FGD系统对锅炉影响的热态试验研究
1.单炉运行对炉膛负压的影响
图17610为2号单炉运行、FGD系统启动时炉膛负
压的变化曲线(100MW),图1 7 6 11为FGD系统停运时
图1767 冷态双炉运行时FGD旁路正常切换至
炉膛负压的变化曲线。由图可知,FGD顺启时,压力由于烟道阻力增加而变正,波动在300Pa左右,FGD顺停时负压变化刚好相反,负压变大。1号炉的情况基本相同,图17612为1号单炉运行FGD系统停运时炉膛负压的变化曲线。由于实际运行时锅炉负压自动不投入,因此送、引风机自动时FGD系统启停对负压的影响试验未做。图17613为2号炉顺启前后只调引风机A时液力耦合器开度的变化,从图中可看出液力耦合器开度从39.5%增大至45.8%时,风机电流从60A增至70A(注:在FGD系统启、停前,人为地将锅炉负压调大或调小,在试验时不作任何调整,试验完后再调整至正常运行
主路炉膛负压的变化曲线

负压)。
图1768 双炉运行冷态时FGD主路正常切换至
旁路炉膛负压的变化曲线
从图1767~图1769可看出,冷态双炉运行FGD启停时对锅炉炉膛负压影响要比单炉运行大得多,特别是当烟气从FGD主路快速切换至FGD旁路(通过预拉弹簧在2s内打开旁路)时,负压的变化明显变大,而且变化的时间很短,可以预见在热态运行时,锅炉的负压波动将会更大,对锅炉的影响更大,运行人员必须引起足够的重视。

从上述冷态试验,可以得出以下几点结论:
图17610 单炉运行FGD顺启时炉膛
负压的变化曲线(2号炉)
(1)FGD系统启动时,锅炉炉膛负压将变小(数值变大),


图17614 引风机出口的闸板式风门
图17611 单炉运行FGD顺停时炉膛
负压的变化(2号炉)


图17615 FGD系统运行前后挡板前烟道压力的变化
图17612 单炉运行FGD系统停运时
炉膛负压的变化(1号炉)


图17616 停运锅炉在FGD运行时烟气倒灌进炉而
图176132号炉顺启前后只调引风机A时
使炉膛负压变化曲线
液力耦合器开度的变化
2.双炉运行FGD系统启停对炉膛负压的影响
从锅炉空气预热器出口到FGD进口挡板的烟道上,在电除尘器入口、引风机入口有叶片式挡板风门,在引风机出口有一闸板式风门(如图17614所示),由于积灰无法关严,试验发现,当FGD运行时,由于烟道阻力增加,FGD进口挡板前烟道压力增大,如图17615所示,这使高浓度的SO2烟气倒灌进入停运锅炉而使炉膛负压变正,如图17616所示。这不仅将对停运锅炉造成很大的腐蚀,而且使得锅炉检修工作无法进行,不得不开启一台引风机。
图17617为双炉满负荷运行FGD系统顺启时1号炉炉膛负压变化曲线。由图可知,炉膛负压波动最大在480Pa左右,比单炉运行要大。图17618为FGD顺停时1号炉负压变化曲线,炉膛负压波动最大在500Pa左右,每侧引风机电流调整约4A。
锅炉正常运行负压为±50Pa,但在FGD启、停过程中远超过此值,图176 19就反映了这种差别,图中的突出部分即是单炉运行FGD系统启、停时炉膛负压波动情况。

图17617 双炉满负荷运行FGD顺启时炉膛
负压变化曲线(1号炉)


图17620 双炉运行FGD顺启时炉膛
负压变化曲线(2号炉)
图17618 双炉运行FGD顺停时炉膛负压
变化曲线(1号炉)


图17621 双炉运行FGD顺停时炉膛
负压变化曲线(2号炉,11月29日)
图17619 单炉运行FGD系统启、停时炉膛
负压波动与正常值的比较
特别是当FGD保护动作时(如2台循环泵都故障停运、FGD系统失电等),FGD旁路挡板通过预拉弹簧在2s之内打开,造成锅炉的炉膛负压波动更大。若燃烧的无烟煤煤质差,在这么短的时间内运行人员无法将负压调整过来,极有可能造成锅炉灭火(实际运行中,锅炉都有因煤质差而造成灭火的)。从机组运行安全考虑,该试验未实际进行。
对2号炉,其负压变动情况完全与1号炉的规律相同,如

图17620、图17621所示,这是2000年11月29日
的数据。在其他时间的启、停情况再次印证了这种负压变化的
图17622 双炉运行FGD顺启时炉膛
规律,如图17622、图17623。
负压变化曲线(2号炉,12月9日)

图17623 双炉运行FGD顺停时炉膛
负压变化曲线(2号炉,11月30日)
(四)FGD烟气系统设计探讨
FGD系统的阻力可由增压风机或锅炉引风机来克服,因此烟气系统设计时应按这两种情况来考虑对锅炉运行的影响。
锅炉100%的烟气脱硫,而FGD系统无增压风机时,在正常运行状态下,锅炉负压能保持很好的稳定,如某电厂FGD系统,但当FGD系统出现异常时,就应认真考虑如何保护锅炉和
FGD系统了。
就对锅炉的影响而言,FGD系统出现异常主要有两种:①FGD系统失电,所有设备停运;②FGD进、出口挡板误关。对前一种,若旁路不快开,高温烟气直接进入FGD系统,势必破坏系统中的防腐材料,而对锅炉无大影响。解决的方法可以在FGD系统入口布置水冷装置,在旁路未开之前加水冷却烟气。加水冷却还可以除尘,提高副产品质量;另外可以将挡板的电源接入厂用电,这样一来FGD系统失电后旁路挡板也可在1min之内打开,基本可以避免对FGD系统内设备的高温损坏。对于第二种异常情况,方法是设立旁路快开装置,这也是唯一的解决方法了,当然应该避免进/出口挡板在实际运行中误差。快开的时间设定是一个关键,若弹簧在1s左右就将挡板全开,必然会引起锅炉负压的急剧波动。事实上,当旁路挡板开启50%以上时,烟气就可大部分通过,因此旁路快开可以设定50%的快开而不是全部(这里称为半快开),这样或许可以减少对锅炉的影响。
对有FGD增压风机的系统,许多设计是将旁路全开,即成了部分脱硫,这样可以避锅炉跳闸,但这实际上相当于降低了脱硫效率。对100%的烟气脱硫,旁路挡板全开时间大多设计为10~15s,这样可以减少对锅炉的影响。另外,设定50%的快开旁路挡板也应当是一个选择。
FGD系统的阻力可由增压风机或引风机来克服,比较而言,用引风机更具有优点:
(1)无需增加1台增压风机,可以较大地节省投资和减少运行成本。
(2)系统布置简单,操作也简化不少。(3)风机不需另外考虑腐蚀问题。
对于新设计的机组,已有较多的应用,例如,某电厂
600MW海水FGD系统、某电厂125MW的湿法FGD系统都只
用锅炉引风机,而未设增压风机。对于老机组,引风机的出力应有足够裕量。
二、FGD系统对汽轮机系统运行的影响
(一)相关系统简介
经FGD系统脱硫后的烟气从吸收塔出来只有50℃左右,不能直接排入烟囱,必须经过加热。本套系统采用蒸汽加热器将烟气再热至80℃以上。加热蒸汽来源于机组辅汽联箱,加热后的凝结水由凝结水泵打回至机组除氧头。
机组辅汽联箱的蒸汽主要来源于:①汽轮机三段抽汽;②汽轮机高压缸排汽;③启动锅炉;④其他,如高、中压汽门阀杆汽封等。机组正常工作时,辅汽为汽轮机三段抽汽或高压缸排汽。
(二)用汽对机组经济技术的影响
试验证明,FGD系统对汽轮机系统运行的影响如下:
(1)FGD满负荷运行时,用汽轮机三段抽汽加热FGD再
热器,蒸汽参数约为0.53MPa/350℃,用汽量约16~18t/h,
在短时间内,汽轮机本体的二抽、三抽、四抽、五抽、六抽、七抽等各压力略有降低,而在停用时各抽汽压力有所上升,但全在正常波动范围内,温度基本不变。抽汽对除氧器的正常运行影响不大。
(2)在FGD满负荷运行时,用高压缸排汽加热,由于高压缸排汽有足够的汽量,因此只用了1号炉的汽。高排参数:
2.18MPa/307℃左右,至辅汽联箱的压力设定为0.57MPa,此时调节门的开度约32%~39%,蒸汽流量大致在18~20t/h。
用汽后汽轮机各级抽汽压力都在正常范围内变动,温度变化很小。这表明FGD再热器采用二段抽汽加热对汽轮机的运行影响不大。
(3)经FGD再热器后的凝结水由凝结水泵打回至除氧头,除氧器内压力略有下降、水位略有上升,而水温基本无波动。当停用回收后,除氧器内压力略有上升、水位略有下降,而水温无波动,同回收时正好相反。因此凝结水回收对除氧器的正常运行影响不大。
(4)若凝结水质不合格未回收,将使机组的补水率增加约2%,因此在FGD投运后,运行人员应经常化验水质,合格后及时回收凝结水。
(5)脱硫用汽对机组经济性的影响是比较大的,且参数高的供汽对机组经济性的影响比低参数供汽要大得多,因此选用何种加热方式应慎重考虑。
三、FGD系统对灰渣排放系统运行的影响
(一)相关系统简介
某电厂的脱硫石膏浆液由2台浆液抛弃泵(1台使用,1台备用,如图17624所示)从石膏浆罐打入锅炉灰渣水缓冲池内(如图17625所示),直接由电厂灰渣泵打到灰场抛弃,现有3台灰渣泵,1台使用,2台备用,石膏浆液在缓冲池上分三路进入灰渣泵入口处(如图17626所示),2根灰渣

图176242台石膏浆液抛弃泵
管,1台使用,1台备用,机组正常运行时对石膏浆液只开启运行灰渣泵前的一路。系统的主要设备列于表1 76 9中。


图176272根灰渣管和1根灰水回收管现场图
图17625 锅炉灰渣水缓冲池及灰渣泵
灰场位于厂区东北面山谷,呈掌形,距厂区直线距离约

2.0km,灰坝与厂房地面高差约20m,灰场容量约为3.546×
106m3 ,可满足电厂储灰20年。灰场现场如图1 7 6 28所示,图17629为2个灰渣管出口。
图17626 石膏浆液在缓冲池上分三路
进入灰渣泵入口
表1768
系统的主要设备


图17628 灰场图

图17629 灰渣管出口
从抛弃泵至灰渣池的管道为钢骨架塑料复合管,DN1001根,冲洗水管1根为DN80,管子采用电熔连接。
2根灰渣管为铸石复合管,外套钢管φ478×6,内衬铸石管φ440×25,中间用1∶2的水泥砂浆充填,外壁防腐处理,除锈
达st3级后,涂STIC—9082底漆,再涂LK—200面漆,管道每根长约2.3km。
这种脱硫石膏浆液与机组灰渣水混排的方式在国内是首次采用,从操作观点看,有两个问题必须关注:一是会不会引起现有灰渣排放管的严重结垢;二是会不会加剧灰渣管的磨损、腐蚀。脱硫石膏浆液具有一定的酸性和磨蚀性,但石膏晶体的磨蚀性远不及粉煤灰颗粒;因此需特别关注脱硫石膏浆液被引入煤灰水后在灰渣输送管内沉积硫酸钙垢的问题,因为要清除硫酸钙垢,不仅技术难度大,而且费用很高。
1根灰水回收管为φ478×7的焊接钢管,直埋式敷设,长
(二)对灰渣排放系统运行的影响
约2.9km。三根管蜿蜒而行,如图17627所示。
1.未排石膏浆液前的灰渣管结垢情况
冲灰水主要是电厂循环水排水,另有引风机冷却水、化学水排放及灰场回收水,这水要先预处理,达到标准(悬浮物
100mg/L,pH=6~9)后方可进入清水池,由2台冲灰水泵用于
电除尘器冲灰和炉底冲渣,灰渣水一道进入缓冲池内打到灰场。
2000年11月23日—25日,选定累计已运行约6个月的2号灰渣管,从泵出口至灰场长约2300m,对其拆离进行结垢情况全面的检查(规定在FGD投运时用2号管输灰渣),检查范围如下:
(1)3号灰渣泵出口电动截止阀阀体及阀后直管段。(2)2号排灰渣管出口逆止阀阀体及阀前后直管段。(3)2号排灰渣管接近107国道公路处的弯管及弯管前直
化,但其结垢应当仍是CO23-盐为主,表17610为试验期间脱硫石膏浆液的成分分析结果,表17611为脱硫石膏浆液加入灰渣水前后灰水中pH值、Ca2+浓度及SO24-浓度的变化结果。
管段。
(4)2号排灰渣管108~109段(直管段)。
表17610 石膏浆液成分的设计值与实测值
(5)2号排灰渣管146~147段(低位直管段)。(6)2号排灰渣管335~336段(低位水平段)。(7)2号排灰渣管557~558段(上升管)。
(8)2号排灰渣管出口。
检查结果:灰渣泵房内3号灰渣泵出口阀和2号排灰渣管出口逆止阀及出口直管段检查表明,阀体及管壁圆滑,未见有结垢情况。
对厂外灰渣管的检查发现,所检查管道的侧壁均有结垢,
垢厚约1~1.2mm(结垢情况见图17630)。


表17611 石膏浆液加入灰渣水前后灰水中
pH值、Ca2+浓度及SO24—浓度的变化
图17630 厂外灰渣管的侧壁结垢
图17631为结垢厚度与相对管长关系的曲线(相对管长=离灰渣泵出口距离/灰渣管总长),表1769是垢样成分分析结果,垢样致密坚硬呈灰色,层状分布。


从表17611可看出,引起结垢的Ca2+在脱硫石膏浆液加入灰渣水后浓度增大很多,但是从灰渣管出口浓度来看,并没有减少多少,初步可表明灰水中的Ca2+与CO23-或SO24-结合成晶体沉积并吸附在管壁上的并不多,另外pH值在脱硫石膏浆液加入灰渣水后有所减小,图17632是FGD满负荷运行石膏浆液加入灰渣水后2号灰渣管出口处pH的变化过程,当时燃煤含硫分析见表17612,从图17632中可看出,灰管出口处pH值从10左右减小并最后稳定到9.07左右,两次的规律完全相同,这种变化将使结垢趋势减弱。现
图17631 灰渣管现有结垢厚度与相对管长的关系
表1769
垢样成分分析结果

从图17631和表1769中可明显看出,某电厂和其他大部分电厂一样,其结垢是典型的CaCO3垢,这主要是灰中活性的CaO与灰渣水中的CO23-在碱性条件下生成溶解度很小晶体CaCO3,沉积并吸附在管壁上所致。

2.石膏浆液混排后灰渣管的结垢情况
图17632 FGD满负荷运行石膏浆液加入灰渣水后2号
当脱硫石膏浆液加入灰渣水后,灰水中的成分有一定的变
灰渣管出口处pH值的变化过程
场拆管检查也表明了这一点,在FGD累计运行1个多月后检查灰渣管结垢情况,没有发现管壁上结垢有异常变化,灰水系统运行正常。2002年8月28日,再次对2号灰渣管进行拆管检查。
表17612 混排时锅炉燃煤含硫量分析
(收到基1号炉/2号炉,%)


图17635 水平低位处的结垢
(三)混排对灰场及灰渣利用的影响探讨
1.对灰场容量的影响
灰场容量的计算是按FGD设计值Sar=2.5%,年满负荷运行5000h。但实际上FGD含硫量不到设计的一半,并且机组常调峰,FGD的运行负荷和投用率不高,目前电厂已将一部分电除尘的干灰利用,因此可以认为电厂的灰场容量是足够的,脱硫产品不会对其造成大的影响。
2.对灰渣利用的影响
根据前两次拆管检查的经验,结垢是发生在泵出口较远的地方,故本次检查选定了3个地方:原2号灰渣管出口处(注:该管现已接长,延伸至灰坝处)、离出口约30m处的水平管道
尽管目前某电厂对灰场的灰、渣不加利用,但作为潜在的可能,分析FGD石膏对灰渣应用的影响是十分有意义的。
及原335~336低位水平段。
对于单独的灰渣和脱硫石膏已有很多的应用,如用作建材资源、填埋矿井、铺路筑坝、改良土壤、生产化肥等。对于混排,石膏浆液会产生什么影响呢?这要从石膏浆液的成分开始分析。
检查发现,管道的侧壁均结有一层硬垢,厚度在1.2mm左右,这同前两次检查的结果基本相同,垢厚没有什么增加。在管道的底部是灰渣、灰水泥层,没有任何结垢,反而被磨损许
石膏浆液成分中对灰渣有影响的主要可分为:脱硫废水、
CaSO4、CaSO3、CaCO3、MgCO3等。对脱硫废水,由于它是
多。图17633~图17635是各处的结垢照片。
酸性的,pH=4.6,将其与大量碱性的冲灰水混合,起到了中和作用。当混合液达到pH=9左右时,对于废水中超标的重金属就有吸附共沉的作用,这是脱硫废水处理的最佳pH值。

CaSO4在石膏浆液固体中占85%以上(见表17611),
在水泥生产过程中通常要用石膏(CaSO4 ·2H2O)来调节水泥的凝结时间,研究表明利用脱硫石膏来代替是可行的,关键是量的控制,应使水泥中SO3的含量不超过3.0%的国家标准。另外石膏对灰渣来说是一种良好的活性激发剂,CaCO3、MgCO3等本身就是生产水泥的材料。对FGD石膏来说,对灰
渣的影响主要是其中的CaSO3成分和Cl,在650℃下,CaSO3
会发生分解反应:CaSO3 —6—5—0℃→CaO+SO2↑,因此过多的
CaSO3自然会限制FGD石膏的应用,但从表17611看,
图17633 出口处的结垢
石膏浆液中的 CaSO3含量很少,平均不到0.2%。在欧洲,CaSO3含量超过0.5%时才不被利用,因此FGD运行时要注意吸收塔内的充分氧化。

FGD石膏的综合利用是一项大课题,对某一具体的电厂,需要许多部门合作研究。笔者认为,对于有堆放场地、石膏难以利用或利用不切实际的,将其堆放未尝不可,事实上,在欧洲的西班牙、土耳其的电厂中,由于拥有大量天然石膏,从一开始设计时就将FGD石膏与飞灰相混,堆放在灰场中。
本节将现场拆管检查和对灰渣管的结垢机理结合起来研究,表明脱硫石膏浆液与机组灰渣水混排的方式对现有排灰渣管道的影响不大,不会加剧灰渣管的结垢。对于抛弃法设计的FGD系统,可以不必单独设立脱硫石膏浆液排放管道,这样可以节约一定的投资。
图17634 近出口处的结垢
四、FGD系统对尾部烟道及烟囱的影响
电厂加装湿法FGD装置后,会使烟气温度降低、烟气含湿
量增大,按设计,脱硫前进烟囱的烟气流量为1.09×106m3/h(标准状态下),温度为135.0℃,脱硫后增加水分约6%,温度为80.0℃,有可能造成烟温低于酸露点温度,对脱硫后尾部烟道及烟囱产生不利影响。
某电厂脱硫后烟道宽4.8m,高5.0m,经约27m后进入烟囱。烟囱高180m,出口直径6.0m,为锥形单筒烟囱,如图1
7 6 36所示。烟气在标高24.0m处开孔4.81m(宽)×
6.163m(高)进入。筒身及各层牛腿混凝土采用425号以上的普通硅酸盐水泥加花岗岩碎石和河沙配制,烟囱的内衬在烟道
口处(标高在24.0~37.0m处)采用230mm厚的耐酸陶砖,
37m以上采用200mmC15页岩陶粒混凝土。隔热层采用岩棉板
材,厚90mm(24.0~37m处),37m以上厚120mm。内衬内表

面涂有OM型烟囱耐酸防腐涂料。

图17637 脱硫前后烟囱内烟气温度和
烟囱内壁温度的变化
(4)使烟囱的热应力发生变化。
(二)烟温变化的影响
1.腐蚀情况
通过理论计算,湿法脱硫后烟气酸露点温度并不比脱硫前低,脱硫前烟气温度和烟囱内壁温度基本上大于酸露点温度,故烟气不会在尾部烟道和烟囱内壁结露,且在负压区不会出现酸腐蚀问题。而脱硫后烟气温度尽管升高,但仍远低于酸露点温度,SO3将溶于水中,烟气会在尾部烟道和烟囱内壁结露,尽管烟气中SO2等酸性气体减少了,但烟气的腐蚀性并未比未脱硫前减小,加上脱硫后烟囱正压区的增大,会使烟囱的腐蚀加大,因此须定期对烟囱进行检查,发现问题及时处理。对尾部烟道应立即进行防腐保护,如加铺玻璃钢防腐材料等。
图17636 锥形单筒烟囱
(一)烟囱内烟气温度及烟囱内壁温度分布的计算
根据能量守恒原理和传热学原理,可计算出烟气温度沿烟囱高度的一维分布和烟囱内壁温度分布,这里将烟囱分为12段,每段13m,传热系数按平壁传热计算。在计算段内,有FGD装置安装前后满负荷下的工况计算结果如图17637所示,其他负荷下的结果基本相同。从图17637中可看到,脱硫前后沿烟囱高度方向上烟气温度变化都不大,但脱硫后的烟温比脱硫前要低55℃,且内壁温度低至70℃,对尾部烟道及烟囱将产生一些影响,这些影响主要有:
FGD装置进行性能试验期间发现,FGD吸收塔入口烟气为正压,温度为136~150℃,取样管法兰上未发现有结露现象。而在吸收塔出口、蒸汽再热器前以及再热器后发现,取样管和法兰在短短几天便已遭到强烈的腐蚀。测量结果表明再热器出口温度十分不均匀,明显地表现出烟道上部温度高、下部低的分布,上下温差最高达20℃,烟道中下部的烟气温度低至70℃以下,比酸露点低许多,这样腐蚀便不可避免了。
2003年7月初,某电厂2台机组停运,对FGD系统出口烟气挡板后的烟道和烟囱运行了全面检查,结果发现,烟囱入口约20m的原烟道遭到了严重腐蚀。烟道材质为A3钢,厚度原
为6mm,检查结果为4.8~5.2mm,即腐蚀了1mm左右,而
(1)由于烟温的降低出现酸结露现象,造成腐蚀。(2)烟囱正压区范围扩大。
FGD系统累计的运行时间不到1年,并且运行时燃煤含硫量
(约0.8%)大大低于设计值(2.50%)。图17638是烟道
(3)影响烟气的抬升高度,从而影响烟气的排放。
腐蚀的照片,用手可以剥下3~4层,如图17639所示。

图17638(一)FGD再热器后烟道的强烈腐蚀
(a)腐蚀原貌;(b)可见的层次分明的腐蚀层

图17638(二)FGD再热器后烟道的强烈腐蚀
(c)烟道腐蚀总览


图17639 剥离的腐蚀锈片
图17641 新的吸收塔入口非
金属膨胀节
2003年7月1—13日,由某设备防腐公司负责对引风机出口的所有烟道进行了防腐处理,用环氧树脂涂料浸透6层玻璃钢纤维布(总厚约2mm)敷满整个烟道(旁路烟道腐蚀较
蚀性更强了,在系统设计时应充分考虑防腐问题。
轻)。
另外,在某电厂,由于FGD入口挡板密封不严,FGD停运时也有烟气漏入系统,会引起烟道的腐蚀。原设计入口烟道
吸收塔入口的非金属膨胀节原设计不防腐,现已完全腐
只是在近吸收塔1m处涂有 KOROPLASTVE310防腐涂料,
烂,如图17640所示。2003年7月10日,换上了含塑
料王F4的由4层防腐材料组成的非金属膨胀节,如图17
6 41所示。
其余烟道壁就是碳钢,在FGD调试时就发现,这些烟道已锈迹斑斑,因此对吸收塔入口挡板后的烟道也应防腐。对于旁路烟道也有同样问题。某电厂对FGD系统进行全面检查时发现,吸收塔进出口烟道都有不同程度的腐蚀现象,如图176

42、图17643所示。对吸收塔出口,设计已涂有1.2~
1.5mm厚的KORRPLASTVE310防腐涂料,现已有腐蚀,可
见脱硫后烟气腐蚀性的厉害。选用更好的防腐材料(如含镍不锈钢等)固然可以延长使用寿命,但更重要的是要定期维修检查,发现问题及时处理,只有这样才能不断提高FGD系统的利用率。
图17640 吸收塔入口非金属
膨胀节完全腐烂
脱硫后的烟气更具有腐蚀性。某电厂FGD系统停运,检查FGD后的尾部烟道时发现,一些边角位置的钢板被腐蚀得如薄纸,有些部位甚至已腐蚀穿孔。某电厂FGD运行3年后尾部干、湿烟气混合处的砖砌烟道底部、两侧开始流出酸液了,FGD出口膨胀节也已损坏,这充分表明脱硫后烟气的腐

图17642 吸收塔进口烟道的腐蚀

图17643 吸收塔出口烟道的腐蚀

2.对烟囱内压力分布的影响
图17644 满负荷时脱硫前后烟囱内的静压分布情况
烟囱内是否出现正压是决定烟囱内是否会受到腐蚀的另一重要因素。如果烟囱在负压运行,则基本上不存在烟气向烟囱外壁渗透问题;如烟囱内出现正压,则烟气会通过内壁裂缝渗透到钢筋混凝土筒身表面,将导致腐蚀的增强,对烟囱的安全运行不利。
Hs———烟囱几何高度,m;
vs———烟气抬升计算风速,m/s。
脱硫后烟囱进口烟气温度从135℃降至80℃,导致烟气密度增大,烟囱的自抽吸能力降低,这样会使烟囱内压力分布改变,正压区扩大。烟囱内静压分布可由下式计算
脱硫前后烟气抬升高度的计算结果见图17645,由图17645可知,脱硫后烟气抬升高度降低约80m。地面最大浓度与污染物排放量成正比,与有效源高(烟囱几何高度加烟气抬升高度)的平方成反比,虽然脱硫后烟气抬升高度降低,但由于脱硫后烟气中的污染物已大为减少,因而不会造成更大的环境污染。
Δps=(8λi+1)×(1-D14r-4DrR-1)pve
Dr=D/D0
R=(λ+8i)pve
g(ρa-ρy)D0
式中 Δps———烟囱内静压,Pa;
λ———烟囱内衬摩擦系数,取0.05;
i———烟囱内衬坡度;
Dr———相对直径;

D———计算高度处烟囱内径;
D0———烟囱出口直径;
图17645 脱硫前后烟气抬升高度
pve———烟囱出口处动压,Pa;
4.对烟囱热应力的影响
R———里赫捷尔数,即烟囱静压准则数;
ρa———全年气温最高月份平均温度的大气密度,kg/m3;
ρy———烟气密度,kg/m3。
烟囱热应力与烟囱内外温度差成正比,脱硫后温差由脱硫前的约114℃降至约59℃,使得热应力减小,对烟囱的安全运行有利。
当R≤1.0,表明烟囱内为全负压;R>1.0时,在烟囱内将出现正压。计算得脱硫前满负荷时R=1.955,最大静压为
(三)小结
16.3Pa,出现在标高164.6m处;50%负荷时R=0.49<1.0,
烟囱内不会出现正压;脱硫后满负荷时R=3.576,最大静压
为40.5Pa,出现在标高148.9m处;50%负荷时R=0.89<
1.0,烟囱内不会出现正压;图17644给出了满负荷时脱硫前后烟囱内的静压分布情况。
从图17644可知,FGD装置运行前只在146m以上
(1)脱硫前烟气温度和烟囱内壁温度基本上大于酸露点温度,故烟气不会在尾部烟道和烟囱内壁结露,且在负压区不会出现酸腐蚀问题;而脱硫后烟气温度已低于酸露点温,烟气会在尾部烟道和烟囱内壁结露,加上脱硫后烟囱正压区的增大,会使烟囱的腐蚀加大,因此在尾部烟道和烟囱的设计时就应当考虑防腐问题。对尾部烟道、烟囱定期进行检查,发现问题及时处理。另外由于FGD入口挡板密封不严,FGD停运时也有烟气漏入系统,会引起烟道的腐蚀,因此对吸收塔入口挡板后的烟道也应防腐。
出现正压区,而脱硫后正压区扩大到99~180m的区间。虽然脱硫后SO2和其他酸性气体浓度有很大减少,但由于烟气温度已在酸露点之下,烟囱内壁必然有酸结露发生,日积月累,其腐蚀不容忽视。
(2)脱硫后烟气抬升高度的降低可通过脱硫后烟气中的污染物的减少来补偿,因而不会造成更大的环境污染。
3.对烟气抬升高度的影响烟气抬升高度计算为
(3)脱硫后温差降低使得热应力减小,对烟囱的安全运行有利。
ΔH=1.303Q1H/3Hs2/3/vs
五、FGD系统投运时机组的最优运行程序
式中 ΔH———烟气抬升高度,m;
QH———烟气热释放率,kJ/s;
本节介绍某电厂FGD系统运行前后机组的最优运行操作程序,它可有效地避免机组跳闸和设备损坏,供其他电厂运行
人员参考,同时对其他电厂类似系统的设计、运行有借鉴意义。
持炉膛一定的负压。
(二)其他
(一)FGD启、停及正常运行时锅炉运行的最优操作
在烟气脱硫系统的启、停过程中,锅炉炉膛负压将有较大波动,它有可能引起锅炉 MFT,因此对锅炉运行有一定的要求。
FGD系统的石膏浆液排入灰渣缓冲池,由灰渣泵将其与灰渣水一起打至灰场,为了跟踪这种混排对灰渣排放管结垢的影响,因此混排时注意记录灰渣泵的运行参数及灰渣管混排运行总时间。
1.FGD启、停时锅炉运行的操作
电气应保证FGD系统用电的要求,柴油发电机每2月必须启动1次。机组的其他操作按正常运行要求执行即可。
(1)单台或2台锅炉按照要求调整好负荷,稳定运行。(2)FGD启、停前锅炉调整好燃烧,每炉投1~2支油枪
稳燃。
第七节 节能措施
(3)FGD进烟气前电除尘器一定要投入运行。
(4)锅炉送、引风机全部手动运行,炉膛负压在FGD进烟气前5min左右调至比正常运行时稍大些,约-200Pa左右,在FGD停运前5min左右调至+200Pa左右,保持稳定运行。
一、脱硫系统泵和风机的节能运行
(5)FGD启、停整个过程应密切监视炉膛负压的变化,随时做好调整炉膛负压的准备,使之维持在锅炉的正常范围内运行。
2.FGD系统正常运行情况下的操作
近几年,由于发电机组装机容量的迅速增长,我国电力供应紧张的局面基本得到缓解,部分地区的电力供应甚至出现盈余,火电机组经常低负荷运行。同时,由于电网负荷结构发生较大变化,电网负荷的峰谷差加大,而电网的尖峰负荷和低谷负荷一般都要求火电机组来承担,火电机组不得不作调峰变负荷运行。作为锅炉的重要附属设备,烟气脱硫装置亦需随着机组负荷的变化而需要不断调整运行工况。
由于FGD系统对负荷有很好的适应性,锅炉的调整不会影响其运行,因此锅炉的操作完全可以按本身需要进行任意操作而不用考虑对FGD系统的影响。但需注意以下两点:
(1)锅炉投油运行。如果锅炉投油运行而电除尘器单侧有两个或以上电场(特别是1、2电场)长时间未投入,则应停
运FGD系统。
(2)电除尘器故障。FGD系统在运行,如电除尘器单侧有两个或以上电场(特别是l、2电场)故障停运,FGD系统入口、出口粉尘浓度不正常增大,烟囱冒黑烟,FGD系统应停止运行。
3.FGD系统故障情况下的操作
在锅炉石灰石—石膏湿法烟气脱硫装置中,泵与风机发挥着极其重要的作用。这些设备数量众多,而且耗电量巨大。主要是因为,通常在设计选型时,风机水泵类负载多是根据满负荷工作需用量来选型,实际应用中大部分时间并非工作于满负荷状态,因此设备运行效率低下,造成电能的大量浪费。加之这些设备都是长期连续运行和经常处于低负荷及变负荷运行状态,电耗偏大显得尤为突出。从我国提出节能降耗的政策角度出发,优化脱硫系统设备的运行状态,提高脱硫系统泵与风机的运行效率,降低脱硫设备的厂用电率已成为各个火力发电厂生产工作的一个重要目标。
(1)当FGD系统发生保护时,FGD旁路挡板通过预拉弹簧在2s之内打开,将造成锅炉的炉膛负压波动更大。若燃烧的煤质差,则在这么短的时间内运行人员无法将负压调整过来,极有可能造成锅炉灭火。如主燃料跳闸(MFT)事实发生了,则锅炉运行人员应按运行规程中关于锅炉 MFT的处理方法进行正确操作;如只是引起锅炉负压的剧烈波动,则运行人员应立即调整负压至正常范围内,并查明原因。
(一)脱硫系统各类泵的常用调节方式的比较
作为清水及浆液等各种介质的输送载具,离心泵被广泛地应用于电站锅炉烟气脱硫系统。离心泵的输出特性取决于泵的种类和管网系统的阻力特性,离心式叶轮泵的特性曲线及泵的管网阻力特性曲线如图1771和图1772所示。
(2)FGD申请 MFT。为保护FGD系统内的衬胶、防腐
涂层、玻璃钢管、石灰石浆液喷嘴等设备,在下列两种情况下,FGD系统将向锅炉控制发出请求锅炉MFT的申请:
1)2台循环泵停运并且FGD入口烟气挡板和出口烟气挡板都未关闭。
2)FGD入口烟温高过190℃(3取2)并且FGD入口烟
离心泵的工作原理是把电动机高速旋转的机械能转化为被提升液体的动能和势能,是一个能量传递和转化的过程。通常离心泵的流量、压头可能会与管路系统不一致,或由于工艺要求发生变化,需要对泵的流量进行调节,也就是改变离心泵的运行工况点。而工况点的改变由两方面引起:一是管网阻力特性改变,如阀门节流;二是泵本身的特性改变,如电动机变频调速控制等。只要改变任何一个的特性曲线都可以达到流量调节的目的。
气挡板和出口烟气挡板都未关闭。
如果FGD系统工作人员确认不能立即处理好故障,则锅
炉应立即 MFT。
(3)若FGD进、出口挡板在正常运行时发生关闭,而旁路挡板未及时打开,则锅炉毫无疑问将负压变正压引起 MFT,运行人员应按运行规程中关于锅炉 MFT的处理方法进行正确操作。
4.单炉运行FGD系统投运

某电厂是两台锅炉共用一套FGD设备,当只有一台锅炉运行时,FGD系统投运后,其入口处由负压变为正压。由于停运锅炉烟道上的挡板关不严,造成烟气倒灌入停运锅炉炉膛及烟道中,这会造成停运锅炉系统的严重腐蚀、检修工作的困难和周围环境的污染,因此应开启停运锅炉的一台引风机以维
图1771 离心泵的特性曲线
Q—流量;H—泵在一定转速下的扬程曲线;
P—泵的功率曲线;η—泵的效率曲线

当流量减小越大时,变速调节的节能效率也越大。所以,最有效的节能措施就是采用调节转速来调节流量。目前最为常用的调节转速的方式为电动机变频调速器。相关试验结果证明,应用变频器,节电率可达到20%~50%,效益显著。如一台清水泵电动机功率为55kW,当转速下降到原转速的4/5时,其
耗电量为28.16kW,省电48.8%,当转速下降到原转速的1/2时,其耗电量为6.875kW,省电87.5%。本例子说明:①使
图1772 泵的管网阻力特性曲线
DE—供水(浆液)管网的阻力曲线
用调节阀节流调节流量时,阀门将消耗其所在管路的大部分流体动力;管网阻力特性已经改变,泵的运行工况点偏移,在多数情况下将导致效率下降;②泵的能耗近似与流量变化的三次方成正比;使用变速方式调节流量时,系统阻力特性不变,泵的工况点不变,因此效率不变,泵系统均可稳定地工作;③以调整泵转速来调整流量应该是流量调节的最好手段。
大多数电厂烟气脱硫系统的各类泵,还是通过传统的节流控制方式,即调节出口阀门来调节供水量及供浆量。其实质是改变管路特性曲线的位置来改变泵的工况点,如图1773所示。泵的特性曲线N与管道性能曲线DE的交点A0,即为泵的正常使用时的工作点。当减小阀门的开度时,阀门对介质的摩擦阻力变大,阻力曲线从DE移到DE′,扬程从H0变为H1,流量由Q0减小到Q1,行工况点从A0移动到A1。在这种调节方式下,电动机的大部分输入功率都被消耗在了克服阀门的阻力上,而且流量减小量越大,阀门消耗的功率就越大。
(二)脱硫系统增压风机常用调节方式比较
轴流风机因其高效率、宽工况运行范围的优点而被广泛应用于电站燃煤锅炉。目前,国内大型火力发电机组锅炉脱硫装置基本都采用动(静)叶可调式轴流风机作为增压风机。轴流风机的特性曲线如图1774所示。


图1774 轴流风机的特性曲线
图1773 离心泵变速调节特性曲线
从改变泵自身特性的角度来分析,所谓变速调节是在管网性能曲线不变的情况下,通过改变泵的工作转速,使其性能曲线发生变化,从而改变运行工况点来实现调节。泵的特性曲线取决于电动机的转速,如图1773所示,如果把转速从n变为n′,工况点将从A0移到A2,扬程将从H0降到H2,流量将从Q0减小到Q1,流量调节时输出的流量相同。在两种不同的运行工况下,A1和A2的轴功率分别为
P1=Q1H1ρg/1000,P2=Q1H2ρg/1000
(1771)
与泵的调节方式相似,增压风机的运行工况的常用调节方式也可分为节流调节和调速调节。静叶可调轴流风机是在运行中风机依靠调节机构调节进口导叶开度,达到改变风压、风量的目的。节流调节实质就是通过改变风机系统的管网阻力特性来调节流量,其特性曲线如图1775所示。当风机入口导叶关小时,风机入口气体的压力也降低,相应的气体密度变小,风机性能曲线也发生相应的改变,于是节流后的工作点由原D1至D0。动叶可调轴流风机是在运行中依靠液压调节机构调节叶轮叶片的角度,达到改变风压、风量的目的。由于叶片的角度改变,风机的特性也将改变,其实质就是改变风机自身特性曲线来调节流量,如图1776所示。叶片角度减小时,流量由Q1至Q2,由于风机特性曲线发生变化,运行工况点由点1移至点2。
ΔP=P1-P2=(H1-H2)Q1ρg/1000
(1772)
从式(1771)和式(1772)可得出,节流调
节流量比用调速控制时多浪费了ΔP的功率,而且消耗随着阀门的开度减小而增加。根据泵的叶轮相似理论中的比例定律,流量Q与转速n的一次方成正比,压力H与转速n的平方成正比,功率P转速n的三次方成正比。如果泵的效率一定,当要求调节流量下降时,转速n可成比例的下降,而此时轴输出功率P立方关系下降。如采用改变转速方式调整流量,而轴功率将大幅度降低。当转速从n0变为n2时,Q、H、P变化关系为

Q=Q0(n2/n0),H2=H0(n2/n0)2,P2=P0(n2/n0)3
(1773)
图1775 静叶可调轴流风机
当水泵转速下降时,消耗的功率也大大下降,也就是说,
调节特性曲线

径小于20mm的石灰石磨制成粉,再将石灰石粉按照一定比例与工艺水混合,配置成浓度为25%~30%的浆液,由浆液供给泵打入脱硫塔作为吸收剂来使用。
图1776 动叶可调轴流风机特性曲线
球磨机分干式球磨机和湿式球磨机两种,两者工艺流程及原理基本相同。不同之处在于,干式球磨机使用冷/热风作为石灰石的携带介质,利用排粉风机建立的系统压力,由冷/热风将石灰石粉强制携带出磨机,经分离器分离后,合格的石灰石粉被排粉风机输送至粉仓;湿式球磨机则使用工艺水作为石灰石的携带介质,利用自然循环方式,由工艺水将石灰石粉携带出磨机,经湿磨排浆泵输送至分离器分离后,合格的浆液排入成品箱,作为吸收剂备用,过程中工艺水不仅作为石灰石粉的携带介质,而且还作为吸收剂浆液中的一部分混合水使用。
由于轴流风机同样遵守相似理论中的比例定律,流量Q与转速n的成正比,压力H与转速n的平方成正比,功率P与转速n的三次方成正比。因此,无论是动叶可调还是静叶可调轴流风机,通过调节风机转速都能使电耗大幅度下降。分析图1777可知,当所需风量从Q1小到Q2时,如果采用节流调节的方式,曲线上移,系统的运行工况点从A点变到新的运行工况点B点运行。从图1777中可看出,风机轴功率大幅度降低,并且转速越小,风机轴功率也就越小。考虑减速后效率下降和调速装置的附加损耗,通过实践的统计,风机类通过调速控制可节能30%~60%。这里举一个最简单的例子:由于风量Q和电动机的转速n是成正比关系,而所需的轴功率P与转速的立方成正比关系;所以当需要80%的额定风量时,通过调节电动机的转速至额定转速的80%,即调节频率到40Hz即可,这时理论上所需功率将为原来
的51.2%。
当吸收剂制备系统的设备配置固定以后,整个系统的出力就主要由球磨机的出力来决定。球磨机的出力分为破碎出力和研磨出力,干式球磨机还包括干燥出力。如前所述,球磨机的工作原理是通过滚筒旋转来提高钢球,利用钢球的动能来破碎、磨制石灰石粉。球磨机空载功率占总功率的90%以上,也就是说,球磨机消耗的能量主要用在提升钢球上;因此钢球装载量是决定球磨机出力的关键因素之一。试验证明,球磨机的出力与钢球装载系数的0.6次方成正比,即Bm∝φ0.6。起初球磨机的出力会随着钢球量的增加而增加,但钢球增加到一定量后,出力将不再随钢球量的增加而增加,电耗却始终会增加。这是因为球磨机筒体内各层钢球对磨制物料的有效性不同。筒内各层钢球的降落高度不同,而外层钢球的破碎能力强,所以当钢球装载量持续增加时,实际上是增加了内层的钢球量,其降落高度低,破碎物料能力就小,而提升增加的钢球又需要消耗更多的能量,电动机功率将始终会增加。根据电厂钢球磨煤机的实际运行效果,钢球装载量φ达到最大装载量φmax的85%的时候,球磨机的出力基本达到最大值。因此,并非钢球装载量越大,球磨机出力就越大。

图1777 风机调速特性曲线
相关试验研究结果表明,变频调速是一项有效的节能降耗技术,其效率很高,几乎能将因设计冗余和用量变化而浪费的电能全部节省下来。在机组变负荷运行方式下,如果脱硫岛的主要辅机采用高效可调速驱动系统取代常规的定速驱动系统,无疑可节约大量的节流损耗,节电效果显著,潜力巨大。除此之外,由于可调速驱动系统都具有软启动功能,可使脱硫岛辅机实现软启动,极大降低了电动机在运转时的机械噪声,避免了由于电动机直接启动引起的电网冲击和机械冲击,从而可以防止与此有关的一系列事故的发生,例如电动机转子笼条的疲劳断裂、定子端部绕组绝缘损坏击穿等重大事故。同时,随着变频调速技术的快速发展,变频器的保护功能越来越全面,这就更加提高了脱硫系统辅机设备运行的可靠性。
球磨机的出力除了与钢球装载量有关外,钢球的装载比例也是决定球磨机出力的一个关键因素。物料在球磨机内先被提升起的钢球击碎,落下后被底部的钢球进一步碾磨,直至磨制到合格的颗粒。在这个过程中,由于直径小的钢球具有较大的接触面,研磨出力主要由小直径钢球来完成。因此在保证钢球装载量达到最佳状态的前提下,增加小直径钢球的比例可以增大球磨机出力。这是因为小钢球量增加后,研磨出力增加,由工艺水携带出磨机的合格物料增加,球磨机的循环倍率得以降低。在吸收剂制备系统中,湿式球磨机内的钢球一般由30~70mm的几种不同直径的钢球按一定比例进行装填。在最初运行时,可由球磨机厂家提供的钢球比例及石灰石的研磨特性及成品浆液颗粒度的分析结果,适当增加小直径钢球。正常运行一段时间后,由于钢球的金属损耗,球磨机的电流将有所下降。为使出力不受到影响,应定期(如每天)向磨机内补入一定量的大直径钢球来弥补金属损耗,使得球磨机始终处于最佳运行状态。
二、脱硫岛球磨机制浆系统运行中的优化调整
电站锅炉烟气湿法脱硫装置通常采用石灰石作为吸收剂。在配置吸收剂制备系统时安装了球磨机制浆系统,考虑到原料的成本,很多电厂料磨制成合格的粉状颗粒,利用球磨机将粒
作为石灰石粉的携带介质,球磨机的工艺水进水量也是影响球磨机出力的主要因素。工艺水量偏小,携带出磨机的物料减少,磨机出力降低,严重时甚至会发生堵磨的事故;工艺水量偏大时,携带能力增强,又会将大量不合格的石灰石粉带出磨机,这部分浆液经过旋流器时又被分离出重新回到磨机,也就是说有相当一部分不合格的浆液在系统中反复循环,消耗系统的电能。因此根据物料平衡值配置好物料和工艺水的比例也是节能的一个重要环节。
通过上述优化调整,使球磨机达到最佳状态,保持磨机在
最大出力下运行将是脱硫系统节能降耗的一个重要途径。
三、浆液循环泵的优化运行
脱硫岛在正常运行当中,塔内需要有足够的浆液循环量以吸收烟气中的SO2保证脱硫效率,而浆液循环泵的配套电动机为高压电动机,电耗相当大。通常机组处于大负荷或满负荷状态时,要求脱硫岛浆液循环泵全部投入运行。若机组负荷较低,或者入炉煤含硫量低于设计值时,停止一台循环泵的运行也是能够保证脱硫岛的效率的。从理论上讲,吸收塔的汽液比基本不变,当机组低负荷运行或入炉煤含硫量较低时,烟气中的SO2相应减少,需要的浆液循环量也相应减小,因此,停止一台循环泵的运行是可行的。事实上,很多发电厂的脱硫装置都已经实现了这种运行模式,既保证了脱硫效率,又使脱硫电耗大幅度降低。
四、保证石灰石料的品质
石灰石料的品质也是保证脱硫装置节能保效运行的一个重要因素。石灰石中CaCO3含量偏低或者其他杂质含量偏高,即使脱硫塔浆液循环量足够大,也会使烟气中的硫分经过吸收塔时不被吸收而排放到大气当中,导致脱硫效率降低。同时,由于石灰石CaCO3含量偏低,脱硫岛吸收剂的需要量将大大增加,吸收剂供给泵将会增加出力,从而增加了泵的能耗,吸收剂制备系统的电耗也会随之增加。因此从原料供应的源头紧把质量关,保证石灰石原料按照设计要求供应显得十分必要。
第八节 运行故障分析
一、事故处理总原则
(1)发生事故时,脱硫值班人员应采取一切可行的方法、手段消除事故根源,防止事故的扩大,在设备确已不具备运行条件时或继续运行对人身、设备有严重危害时,应停止FGD系统的运行。
(2)发生事故时,脱硫班长应迅速向直接领导者汇报,并带领全体值班人员迅速果断地按照现场规程规定处理事故。对于直接领导者的命令,若对设备、人身有直接危害时,运行值班人员可以向直接领导者指出其明显错误之处,并向主管领导和有关部门汇报,其余的均应坚决执行。
(3)运行人员应视恢复所需时间的长短使FGD系统进入短时停运、短期停运或长期停运状态。在处理过程中应首先考虑出现浆液在管道内堵塞以及在吸收塔、箱、罐、池及泵体内沉积的可能性,尽快排放这些管道和容器中的浆液,并用工艺水冲洗干净。
(4)当发生本措施没有列举的事故情况时,脱硫运行值班人员应根据自己的经验和当时的实际情况,主动果断地采取措施。事故处理完毕后,直接领导者、值班人员应如实地把事故发生的时间、现象以及采取的措施等一一记录清楚,并向有关领导汇报。
(5)值班中发生的事故,由值长、班长召集有关人员,对事故现象的特征、经过及采取的措施认真分析,并用书面材料报有关运行部门、安监处,以便分析事故发生的原因,吸取教训,总结经验,落实责任。
(6)正确及时的设备维护工作可以延长设备寿命,减少故障的发生;预防在任何时候都是安全运行的重要保障。通过设备运行参数变化来分析故障原因,及时采取措施,把事故隐患消除在萌芽之中,可以防止事故的发生和扩大。
根据常见脱硫设备运行参数变化来分析故障原因见
表1781。
表1781
常见脱硫设备运行参数变化揭示的故障原因

二、FGD系统保护
1.FGD系统紧急停运条件
对于不同的FGD系统,有着不同的保护条件,一般当发生以下情况之一时,FGD系统将紧急停运:
(1)FGD入口烟气压力高高或低低(3取2)且旁路挡板未开。
(2)FGD入口烟气温度异常高。
(3)FGD系统进出口烟气挡板任一未开启时。(4)增压风机跳闸。
(5)GGH跳闸(GGH主、辅电机皆故障)。
(6)所有吸收塔循环泵停运。
(7)6kV电源中断。
(8)锅炉跳闸(MFT、送风机或引风机全跳闸等)。2.FGD系统关闭程序
FGD系统保护程序启动,一般按以下步骤以安全方式关
闭FGD系统:
(1)快开FGD旁路烟气挡板。(2)停增压风机。
(3)关闭FGD入口烟气挡板,打开吸收塔通风口(如有),关闭FGD出口挡板。
(4)关闭蒸汽再热器的蒸汽隔离阀门(如有)。
(5)若吸收塔入口烟温高时,打开吸收塔入口事故冷却水
门(如有)。
3.运行人员检查项目
运行人员必须去就地检查并确认(可手动执行)以下项目:
(1)确认FGD旁路烟气挡板是打开的。(2)增压风机已停运。
(3)FGD入口烟气挡板、FGD出口烟气挡板是关闭的。(4)吸收塔通风口是打开的(如有)。
(5)进蒸汽再热器的蒸汽隔离阀是关闭的(如有)。
最后可根据短时间或长时间停FGD系统的停运要求进行正常操作。
三、FGD系统申请停运
当发生以下情况之一时,脱硫运行人员应申请停止运行FGD系统,按正常停止程序操作。
(1)如果锅炉投油运行而电除尘器未投入使用,汇报值长,退出FGD系统运行。
(2)FGD系统在运行时,如电除尘器单侧有2个或以上的电场故障停运,FGD出口烟气含尘量大于某一值时(各系统有不同定值),退出FGD系统运行。
(3)GGH运行异常时,退出FGD系统运行。
(4)若石灰石浆液制备系统发生故障无法制浆,且吸收塔的pH值不断下降时,汇报值长,退出FGD系统运行。
(5)若2台吸收塔排浆泵都发生故障停运,同时吸收塔内浆液浓度超过某一高值时,汇报值长,退出FGD系统运行。
(6)石膏脱水系统故障长时间不能恢复,吸收塔内浆液浓度超过某一高值时,汇报值长,退出FGD系统运行。
(7)若所有氧化风机都故障且长时间不能恢复时,汇报值长,退出FGD系统运行。
(8)若所有工艺水泵都发生故障停运,汇报值长,退出
FGD系统运行。
(9)若FGD系统用空气压缩机都发生故障停运,或仪用空气短缺、长时间不能恢复正常时,汇报值长,退出FGD系统运行。
(10)生产现场和控制室发生如火灾等意外情况危及设备和人身安全时,退出FGD系统运行。
四、烟气系统的故障
烟气系统的关闭必须由DCS自动完成,旁路挡板必须能打开,之后增压风机停运,FGD的进、出口挡板关闭。如挡板故障则按FGD系统保护的操作进行。
(一)增压风机故障
1.故障现象
(1)“增压风机跳闸”报警发出。
(2)增压风机指示灯红灯熄,绿灯亮,电机停止转动,电流变为0。
2.发生故障的原因(1)事故按钮按下。
(2)风机失电。
(3)润滑油流量低于低设定值,且轴承温度高于某值。(4)润滑油温度高。
(5)润滑油压力低。
(6)液压油温高于设定值。
(7)风机失速。(8)风机振动。
(9)轴承温度高。
(10)密封空气压力长时间低于设定值。
(11)风机电机故障(如过负荷、过流保护、差动保护动作、电机绕组温度高等)。
(12)运行人员误操作。
(13)其他原因引起的FGD系统保护动作。3.故障处理
(1)运行人员应确认脱硫旁路挡板自动开启,进出口烟气
挡板自动关闭。
(2)检查增压风机跳闸原因,若属联锁动作造成,应待系统恢复正常后,方可重新启动。
(3)若属风机设备故障造成,应及时汇报值长联系检修人员处理。在故障未查实处理完毕之前,严禁重新启动风机。
(二)GGH停运
1.故障现象
(1)“GGH跳闸”报警发出。
(2)GCH指示灯红灯熄、绿灯亮,电机停止转动,电流
变为0。
2.发生故障的原因。
(1)电源中断。
(2)GGH电机故障。
(3)机械卡塞。
3.故障处理
(1)若备用电机联动成功,需监视预热器的运行情况,查明预热器跳闸的原因并处理,待故障消除后,迅速恢复正常运行。
(2)若备用电机联动不成功,应立即设法启动备用电机,否则需人工盘车。
(3)FGD系统保护动作,确认联锁动作正常,确认旁路挡板自动开启,增压风机跳闸,进出口烟气挡板自动关闭,否则应手动处理。
(4)查明GGH跳闸原因,并按相关规定处理。(5)必要时通知相关检修人员处理。
(三)蒸汽再热器(如有)故障
若再热器发生故障,将有报警信号显示故障原因。FGD可以运行一段时间,但出口烟温达不到设计要求时,FGD系统将自动停运。
(1)若再热器后烟温偏低,首先应检查机组来加热蒸汽的压力、温度是否满足要求,若蒸汽不满足要求,则应要求加大辅汽参数,尽量满足再热器要求;若蒸汽满足要求,则可能是换热管子结灰,应用工艺水清洗。
(2)再热器爆管。若爆管不严重,则无法判断。如有大量蒸汽进入烟道,则FGD系统出口的两个温度将不正常升高。应先检查就地温度测量是否准确,到再热器平台倾听是否有蒸汽泄漏的异常声响,如确定再热器爆管,应立即关闭来汽电动门,并按正常要求停止FGD的运行,待再热器烟道冷却后打开人孔门检查。
(3)凝结水泵故障。故障现象为CRT上有报警信号,泵停止运行,且备用泵启动。应确认备用泵已启动。如凝结水泵全故障,CRT上有报警信号,且凝结水箱将出现水位高报警。
运行人员应立即关闭机组来加热蒸汽门,对故障进行处理,尽快重新启动凝结水泵。否则,FGD出口烟气温度将达不到设计要求,FGD系统将自动关闭。
(4)加热蒸汽故障。如没有加热蒸汽,FGD出口烟气温度将达不到设计要求,FGD系统将自动关闭。应立即对故障进行处理,尽快重新恢复。
(四)挡板密封风机故障
正常运行时,烟气挡板两台风机中有一台运行,一台备用;如一台跳闸,CRT上有报警信号,且备用风机启动。运行人员应切断跳闸风机电源并立即对故障进行处理。
如两台全故障,CRT上有报警信号,风机出口压力为0,FGD系统可以正常运行,运行人员应立即对故障进行处理,尽快重新启动。
(五)烟道严重结灰
(6)若氧化空气喷嘴中长时间没有氧化空气,则管道必须清洗。
FGD系统的入口烟道和旁路烟道可能严重结灰,这取决于电除尘器的运行情况。一般的结灰不影响FGD的正常运行,当在挡板的运动部件上发生严重结灰时对挡板的正常开关有影响,因此FGD系统和锅炉停运时,要检查这些挡板并清理积灰。
(三)吸收塔搅拌系统故障
1.故障现象
CRT上报警,搅拌器或脉冲悬浮泵运行指示灯红灯熄、绿灯亮,电机停止转动。
五、吸收塔系统故障
2.故障原因
(一)循环泵(对CT—121FGD系统为烟气冷却泵)故障
(1)事故按钮动作。
1.故障现象
(2)电机故障。
(1)CRT上报警。
(2)泵运行指示灯红灯熄、绿灯亮,电机停止转动,电流
(3)吸收塔液位低,保护停。3.故障处理
变为0。
2.故障原因
(1)事故按钮动作。
(2)电机故障(如失电)。
(3)泵入口压力低,泵保护停。这可能是泵的滤网被堵塞,控制室内有报警,此时必须启动另一泵后停止该泵运行,进行滤网清洗,干净后方可再启动。
(1)对喷淋塔。①一般在塔浆液池底部有多台搅拌器,一层或二层布置,同时停运一般不会发生。如只有一二个搅拌器停运,FGD系统仍能运行;②尽快查明跳闸原因并作相应处理,再次启动前应先用工艺水(如有)冲动搅拌器,再尝试启动直至搅拌器运行正常。必要时通知相关检修人员处理。
(2)对脉冲悬浮系统。一台悬浮泵停运,应确认备用泵启动。如所有泵都长时间停运,则停运FGD系统。
(4)电机三相绕组温度高,泵保护停。(5)驱动端电机轴承温度高,泵保护停。(6)非驱动端电机轴承温度高,泵保护停。(7)吸收塔液位太低,泵保护停。
(3)对CT—121FGD系统。搅拌器为立式,如某电厂吸
收塔顶部四台搅拌器同时运行,如一台故障停运,运行人员应尽快查明跳闸原因并尽快恢复,否则申请停运FGD系统。
(8)泵入口阀门故障,显示未开。3.故障处理
(四)除雾器系统故障
(1)运行人员如发现ARP运行不正常,应立即就地查明原因并作相应处理。
若除雾器清洗不充分将引起结垢,有时可从压降升高得到判断。然而清洗水流量受吸收塔液位控制而不能随意加大,清洗程序根据FGD系统停运后肉眼观察除雾器结垢情况来设定清洗频率。假如控制室内发出除雾器报警,运行人员确认后手动对其进行清洗。
(2)若只有一台循环泵运行,FGD系统仍能运行,此时脱硫率将下降。若所有循环泵都故障,则FGD系统将保护动作。应确认联锁动作正常,旁路挡板自动开启,增压风机跳闸,进出口烟气挡板自动关闭;否则应手动处理。
1.故障现象
CRT上报警,除雾器压差大于设定值。2.故障原因
(3)查明循环泵跳闸原因,并按相关规定处理。(4)必要时通知相关检修人员处理。
表计故障或除雾器清洗不充分引起结垢、堵塞。3.故障处理
(5)视吸收塔内烟温情况,开启工艺水冲洗水或事故喷水(如有),以防止吸收塔内管道、衬胶、除雾器等内部设备的损坏。
运行人员确认后手动对其进行清洗,应加强日常运行的定期清洗维护。
(二)氧化风机故障
(五)脱硫效率低
1.故障现象
(1)CRT上报警。
影响脱硫效率的因素有很多,表1782列出了一些导致脱硫效率低的常见原因及解决方法。
(2)氧化风机运行指示灯红灯熄、绿灯亮,电机停止转动,电流变为0。
表1782 脱硫效率低的常见原因及解决方法
2.故障原因
(1)事故按钮动作。
(2)电机故障。
(3)风机出口风温高,保护停。
(4)电机三相绕组温度高,保护停。(5)任一电动机轴承温度高,保护停。3.故障处理
(1)运行人员如发现氧化风机运行不正常,应立即就地查明原因并作相应处理。
(2)一台氧化风机停运,应确认备用风机联锁启动。
(3)若所有氧化风机都故障,短时间内FGD系统能正常运行;加长时间不能恢复时,系统的脱硫率将下降,吸收塔中CaSO3含量将增大,应申请停运FGD系统。
(4)尽快查明跳闸原因,并按相关规定处理。(5)必要时通知相关检修人员处理。

续表
(2)电机故障。

(3)吸收塔液位低,保护停。3.故障处理
(1)运行人员应立即查明跳闸原因并作相应处理。
(2)正常运行时,一运一备;泵故障后应确认备用泵启动。如两台泵都故障而吸收塔浆液浓度超过高值,则FGD应停止运行。
(3)必要时通知相关检修人员处理。
(二)石膏水力旋流器故障
1.故障现象
进旋流器的浆液流量减小,旅流器底流减小。2.故障原因
有旋流子积垢、堵塞。3.故障处理
(1)用工艺水冲洗旋流器及管道。
(2)冲洗无效时,去就地投入备用旋流子。关闭并拆开堵塞的旋流子清理,干净后方可重新投入。
(三)真空脱水机跳闸
六、石膏脱水系统故障
1.故障现象
若脱水系统故障,意味着石膏固体留在吸收塔中。塔内浆液浓度不可超过某一高值,若达到此浓度,则必须用石膏浆液泵将其打到事故浆罐中。若石膏浆液不能及时输出吸收塔,则塔内浆液浓度不断增大。当吸收塔浆液浓度超过高值,而石膏浆液仍不能排出时,则FGD系统应停运。吸收塔中的液位和浓度应经常检查。运行中若石膏浆液脱水能力不足,则应立即查明原因,常见的解决方法列于表1783中。
CRT上报警,脱水机运行指示灯红灯熄、绿灯亮,电机停止转动。
2.故障原因
(1)事故按钮动作。
(2)拉绳动作。
(3)电机或气源故障。
表1783 石膏浆液脱水能力不足的原因及解决方法
(4)皮带跑偏。(5)滤布跑偏。

(6)滤布冲洗泵运行且真空箱密封水流量低。(7)滤布冲洗泵运行且皮带润滑水流量低。(8)滤布冲洗泵跳闸。
(9)真空泵跳闸。
(10)脱水机底部石膏输送系统故障。(11)石膏仓料位高。
3.故障处理
(1)确认脱水系统的联动正常,脱水机浆液供给阀门完全关闭。
(2)尽快查明跳闸原因,并按相关规定处理;必要时通知相关检修人员处理。
(3)启动并加大另一套脱水机的出力。
(4)若脱水机都不能运行,视吸收塔内浆液密度情况决定是否停运FGD系统。
(四)脱水机真空泵跳闸
1.故障现象
(1)CRT上报警,真空泵运行指示灯红灯熄、绿灯亮,电机停止转动,电流变为0。
(2)若无备用泵,则相应的脱水机跳闸。2.故障原因
(1)事故按钮动作。
(一)吸收塔石膏排浆泵故障
(2)电机故障。
1.故障现象
(1)CRT上报警,泵运行指示灯红灯熄、绿灯亮,电机停止转动。
(3)相应的脱水机跳闸。(4)泵密封水流量低。3.故障处理
(2)石膏水力旋流器进口压力指示为0。2.故障原因
(1)确认系统的联动正常,备用真空泵启动;若无备用泵,则相应的脱水机跳闸。
(1)事故按钮动作。
(2)尽快查明跳闸原因,并按相关规定处理;必要时通知
相关检修人员处理。
七、石灰石制浆系统故障
(一)石灰石浆液泵故障
1.故障现象
CRT上报警,泵适行指示灯红灯熄、绿灯亮;泵出口流量指示为0。
2.故障原因
(1)事故按钮动作。
(2)泵保护停(石灰石浆液罐液位低、失电等)。3.故障处理
(1)运行人员应立即查明具体原因并作相应处理。
(2)正常运行时,石灰石浆液泵一运一备;泵故障后应确认备用泵启动。如两台泵都故障而吸收塔内pH不断降低,则FGD系统应停止运行。
(二)石灰石浆罐搅拌器故障
1.故障现象
CRT上报警,搅拌器停。2.故障原因
保护停,事故按钮动作。3.故障处理
(1)运行人员应立即查明具体原因并作相应处理。
(2)如石灰石浆罐搅拌器长时间故障,则吸收塔无法正常供浆,吸收塔内pH不断降低,则FGD系统应停止运行。
(三)湿式球磨机故障
1.故障现象
CRT上报警,湿磨机运行指示灯红灯熄、绿灯亮,电流
变为0。
2.故障原因
(1)事故按钮动作。
(2)电机故障。
(3)磨轴承温度高。
(4)小齿轮轴承温度高。(5)磨轴承润滑油流量低。(6)磨轴承高压顶轴油油压低。(7)磨轴承高压顶轴油油压高。(8)齿轮喷射系统就地控制故障。(9)压缩空气储罐压力低。
3.故障处理
(1)确定系统联锁动作正常,石灰石给料机停止运行。(2)运行人员应立即去查明具体原因并作相应处理。(3)一般设计有两套湿磨系统,一套湿磨系统故障后可根
据石灰石浆液罐液位情况启动,另一套系统。如两套湿磨系统都故障而吸收塔内pH不断降低,则FGD系统应停止运行。
(四)石灰石给料机故障
1.故障现象
CRT上报警,给料机运行指示灯红灯熄、绿灯亮。2.故障原因
(1)事故按钮动作。
(2)电机故障。
(3)变频器故障。
(4)皮带跑偏。
(5)石灰石堵料。(6)石灰石断料。3.故障处理
(1)运行人员应立即去查明具体原因并作相应处理。
(2)停运相应的湿磨机。
(五)湿磨的循环浆液泵故障
1.故障现象
CRT上报警,泵运行指示灯红灯熄、绿灯亮;泵出口流量指示为0。
2.故障原因
(1)事故按钮动作。
(2)泵保护停(循环浆液罐液位低、失电等)。3.故障处理
(1)运行人员应立即去查明具体原因并作相应处理。
(2)正常运行时,循环浆液泵一运一备;泵故障后应确认备用泵启动。如两台泵都故障,则磨系统停止运行。
(六)给粉机故障(对于粉制浆系统)
1.故障现象
CRT上报警,相应给粉机运行指示灯红灯熄、绿灯亮。2.故障原因
(1)事故按钮动作。
(2)电机故障。(3)给粉机卡。
(4)其他保护停。3.故障处理
(1)运行人员应立即查明具体原因并作相应处理。
(2)正常运行时,一运一备;一台给粉机故障后应确认备用给粉机启动。如两台给粉机长时间故障,则系统无法制浆,吸收塔内pH不断降低,FGD系统应停止运行。
(七)粉仓流化风机系统故障
1.故障现象
CRT上报警,相应风机运行指示灯红灯熄、绿灯亮。2.故障原因
(1)事故按钮动作。
(2)电机故障。
(3)流化风机干燥器故障。(4)其他保护停。
3.故障处理
(1)运行人员应立即查明具体原因并作相应处理。
(2)正常运行时,一运一备,一台流化风机故障后应确认备用风机启动。如两台风机保护停,短时间内对FGD系统运行不造成影响,但长时间将造成系统无法制浆,吸收塔内pH不断降低,则FGD系统应停止运行。
八、公用系统故障
(一)仪用空压机故障
1.故障现象
CRT上报警,相应空气压缩机运行指示灯红灯熄、绿灯亮。
2.故障原因
(1)事故按钮动作。
(2)电机故障。
(3)其他保护停。3.故障处理
(1)运行人员应立即查明具体原因,及时排除故障并投入备用。
(2)正常运行时,有备用空气压缩机,运行时应经常检查所有的油分离器及其压差;一台空气压缩机故障后应确认备用空气压缩机启动。如所有空气压缩机都故障,则FGD系统应停止运行。
(二)工艺水泵故障
1.故障现象
(1)CRT上报警,相应水泵运行指示灯红灯熄、绿灯亮。(2)水泵出口压力低。
2.故障原因
(1)事故按钮动作。
(2)电机故障。
(3)其他保护停(水箱液位低等)。3.故障处理
(1)运行人员应立即查明具体原因,及时排除故障并投入备用。
(2)正常运行时,有备用工艺水泵;一台水泵故障后应确认备用泵启动。如所有水泵都故障,则停止FGD系统运行。
(三)工艺水中断
1.故障现象
(1)相关工艺水压力低报警。(2)相关浆液箱液位下降。(3)生产现场各处用水中断。(4)脱水机及真空泵跳闸。2.故障原因
(1)运行工艺水泵故障,备用水泵联动不成功。(2)工艺、工业水箱液位太低,水泵跳闸。
(3)工艺水管破裂或某处法兰大量泄漏等。3.故障处理
(1)确认脱水机及真空泵联动正常。(2)停止石膏排出泵运行。
(3)立即停止球磨机运行,并相应停止给料,同时关闭滤液至球磨机及磨机浆液箱相应阀门,并停止滤液泵运行。
(4)查明水中断原因,及时汇报值长,尽快恢复供水。(5)根据滤布冲洗永箱、滤饼冲洗水箱液位情况,停止相
应泵运行。
在处理过程中,密切监视吸收塔内温度、液位及石灰石浆液箱液位变化情况,必要时停运FGD系统。
(四)石膏抛弃泵(如有)故障
1.故障现象
CRT上报警,相应抛弃泵运行指示灯红灯熄、绿灯亮。2.故障原因
(1)事故按钮动作。
(2)电机故障。
(3)其他保护停(石膏浆液箱液位低等)。3.故障处理
(1)运行人员应立即查明具体原因并作相应处理。
(2)正常运行时,有备用泵;一台泵故障后应确认备用泵启动。应立即查明故障原因,及时排除故障并投运备用泵。如所有抛弃泵都故障,将导致石膏浆液箱液位不断上升,最终致使FGD系统无法运行。
(五)废水处理系统故障
当废水处理系统中某一设备故障导致废水不能正常处理时(如石灰乳给料泵故障、反应池搅拌器故障、pH计故障等),废水可以暂时走旁路,不影响FGD系统的正常运行。但运行人员应尽快查明故障原因,及时恢复系统的运行。
九、电气系统故障
(一)6kV失电
1.故障现象
(1)CRT上报警,6kV母线电压消失。
(2)运行中的脱硫设备跳闸,对应母线所带的6kV电机停运。
(3)该段所对应的380V母线自动投入备用电源,否则对应的380V负荷失电跳闸。
2.故障原因
不同的电气系统设计有不同的原因,主要有:
(1)全厂停电。
(2)6kV脱硫段母线或电缆故障。
(3)电气保护误动作或电气人员误操作。(4)发电机跳闸,备用电源未投入。
(5)脱硫变压器故障,备用电源未能投入。3.故障处理
(1)运行人员应立即确认FGD系统联锁跳闸动作是否完成,确认烟气旁路打开,FGD进、出口板关闭,吸收塔通风口打开。若旁路挡板动作不良应立即将其手动操作打开;确认FGD系统处于安全状态。
(2)确认脱硫保安段、UPS电源、仪控电源正常,工作电源开关和备用电源开关在断开位置,并断开各负荷开关。
(3)尽快联系值长及电气检修人员,查明故障原因,争取尽快恢复供电。
(4)若给料系统联锁未动作时,应手动停止给料。
(5)注意监视烟气系统内各点温度的变化,必要时应手动开启冲洗水门。
(6)将增压风机调节挡板关到最小位置,做好重新启动FGD装置的准备。
(7)若6kV电源短时间不能恢复,按停机相关规定处理,并尽快将管道和泵体内浆液排出以免沉积。
(8)若造成380V电源中断,按相关规定处理。
(二)380V失电
1.故障现象
(1)“380V电源中断”报警信号发出。
(2)380V电压指示到零。
(3)低压电机跳闸。
(4)工作照明跳闸,事故照明自动投入。2.故障原因
(1)相应的6kV母线故障,备用电源未能投入。
(2)380V母线故障。
(3)脱硫低压变压器跳闸,备用电源未能投入。3.故障处理
(1)若属6kV电源故障引起,按短停机处理。
(2)若380V单段故障,应检查故障原因及设备动作情况,并断开该段电源开关及各负荷开关,及时向上级领导汇报。
(3)当380V电源全部中断,且电源在8h内不能恢复,应利用备用设备将所有泵、管道的浆液排尽并及时冲洗。
(4)电气保护动作引起的失电,严禁盲目强行送电。
十、测量仪表故障
1.pH计故障
一般地,吸收塔浆液设有2个pH计,若某个pH计的测量值变化太快或明显有偏差,则自动调节不选该pH计。此时需对该pH计进行冲洗和校验。若2个pH计都故障,则必须人工每小时化验一次,然后根据实际的pH值和烟气脱硫率来控制石灰石浆液的加入量。pH计须立即修复,校准后尽快投入使用。
2.密度测量故障
若密度计的流量变小,先冲洗密度计;密度计故障,需人
工实验室测量各浆液密度;密度计须尽快修复,校准后尽快投入使用。
时,应立即手动按下就近的火警手动报警按钮,同时利用就近的电话向119报警台报警并尽快向班长报告火灾情况。
3.液体流量测量故障
用工艺水清洗或重新校验。4.液位测量故障
(2)班长在接到有关火灾的报告或发现火灾报警时,应立即向119报警台报警并迅速调配人员查实火情,尽快将情况向值长和部门领导汇报。
用工艺水清洗或人工清洗测量管子或重新校验液位计。
5.CEMS故障
(3)正确判断灭火工作是否具有危险性,根据火灾的地点及性质选用正确的灭火器材迅速灭火,必要时应停止设备或母线的工作电源和控制电源。
运行人员应立即查明原因并修复尽快投入,同时做好FGD泵统各运行参数的控制。
6.烟道压力测量故障
(4)控制室内发生火灾时应立即紧急停止FGD系统运行,然后根据情况使用灭火器或启动灭火系统灭火。
用压缩空气吹扫或机械清理。7.烟气流量测量故障
用压缩空气进行吹扫。8.称重设备不准确重新校验。
(5)在整个灭火过程中,运行班长(或主值班员)应积极主动配合消防人员和检修人员,进行灭火工作并按其要求执行有关必要的操作,必要时停止FGD系统运行。运行人员有责任向消防人员说明哪些部位有人孔、检查孔、通风孔以及哪些地方可以取水、取电等。
9.料位计故障重新校验。
(6)灭火工作结束后,运行人员应对有关设备进行详细检查确认,以免死灰复燃。同时对设备的受损情况进行确认并向有关领导汇报。
所有FGD系统的测量仪表应定期维护和校验,必要时更换。
十一、火灾
1.发生火灾时的现象
(7)及时总结火灾原因和教训,并制订相应防范措施。在密闭的室内以及通风不良的地方灭火时,应注意有毒气
(1)火警系统发出声、光报警信号。
(2)运行现场发现有设备冒烟、着火或有焦臭味。
体及缺氧,严防发生人身事故。在火灾有可能引起上空落物的地方应特别注意安全。
(3)若动力电缆或控制信号电缆着火时,相关设备可能跳闸,参数发生急剧变化。
十二、FGD系统的安全性故障
(一)吸收塔内设备(如除雾器)的损坏
(4)控制室出现火灾时,若灭火系统处于“自动”状态,火警发生几秒钟后灭火系统将动作。
2.火灾处理
在某电厂,2002年8月份检查发现,吸收塔内的除雾器已严重损坏,上层除雾器后部(靠吸收塔出口侧)全部塌落,尤其是第二、三区域,已完全塌下,如图1781所示。
(1)运行人员在生产现场检查发现有设备或其他物品着火

图1781(一)上层除雾器塌落现象

图1781(二)上层除雾器塌落现象
下层除雾器的塌落现象没有上层严重,第二、四区靠后部
塌下比较明显,图1782(c)、(d)显示了这点。
从上述各图看,除雾器的损坏不是机械碰撞、磨损或腐蚀,而是变形塌下,因此只能是高温烟气所致,那么高温烟气又是如何进入的?首先来看一下FGD烟气系统的设计,图1 783是烟气系统的示意图。
从锅炉电除尘器后出来的烟气,经FGD入口挡板进入吸收塔,经2层石灰石浆液喷淋洗涤后流经2个卧式除雾器。脱硫后的烟气被蒸汽再热器加热到80℃以上,经出口烟气挡板进入烟囱。FGD系统设有旁路烟道,上有2个旁路挡板。当FGD系统保护动作时,2个旁路挡板通过预拉弹簧在2s之内打开,使热烟气走旁路。

图1781(三)上层除雾器后部各区未有塌落现象

图1782 下层除雾器的塌落现象

图1783 FGD烟气系统示意图
除雾器采用聚丙烯材料制成,其最高耐温为120℃,由意
大利KOCH-CLITSCH公司制造,每层高203mm,由许多块
改变鳞片树脂防腐层的结构。前者欧美国家应用较多,国内某些FGD装置中也有应用,但价格昂贵;后者在我国许多电厂检修中应用,并取得了良好的效果。
组成,按支撑分四大区域。其作用是将经过脱硫后的烟气携带的浆液微滴除去,使烟气带水量大大减少,除雾器按照某种程序不时地进行冲洗,以保持清洁和维持吸收塔水位。正常运行情况下,FGD系统入口的烟气温度为145℃左右,流经除雾器的烟气温度为50℃上下,不会对其造成任何损坏。
然而在FGD系统的实际运行过程中,最易发生的是FGD失电事故。查运行记录,在2002年8月28日之前有4次失电发生,按设计,此时FGD旁路的弹簧应动作,使烟气走旁路;但是四次之中,保护没有一次正确动作,有时只有前或后的一个弹簧正确动作。从运行室至尾部烟道有很长一段距离,旁路烟道挡板手动打开又需几分钟,这样高温烟气便进入吸收塔,流经时间每次长达10~15min,造成了除雾器的严重损坏,并且对系统中的其他设施(如防腐衬胶、涂层、喷淋层等)也有很大伤害。

图1784 太原第一热电厂FGD入口烟道
腐蚀及鳞片更换(2002年7月30日)
在调试时,弹簧都能正确动作,但由于实际运行时烟道上有许多积灰,加上长时间不用,弹簧卡涩,会造成弹力不够打开烟气挡板,这说明在FGD系统设计上考虑不周。并且即使弹簧正确动作了,也有可能使锅炉负压波动而使锅炉灭火跳闸,严重威胁着机组的运行安全,因此必须予以改进。
在吸收塔入口的烟道上,烟道的钢板已有腐蚀,有的已掉落下一层,露出新的锈面,如图1785所示。在吸收塔出口的烟道也开始有腐蚀了,如前图1786所示。再热器管子出现了严重的变色现象,如图1787所示。
为防止热烟气对FGD系统设备的损害,有的电厂在FGD入口烟道处加装一排冲洗水喷嘴,这是可行的。某电厂的改进方法是将原烟气挡板、洁净烟气挡板及两个旁路挡板的电源由FGD系统380V开关柜改在主厂房380V工作段或公用段,这样一来即使当FGD系统完全失电时,烟气挡板仍然可以正常操作,旁路挡板在47s内即可全部打开使热烟气流过,从而保护了FGD系统内的防腐衬胶、鳞片涂层、除雾器等其他吸收塔内部设备。
(二)FGD系统内的腐蚀

防腐的重点是吸收塔入口干湿交界面处、吸收塔内部及吸收塔出口后的烟道、再热器等部件。在吸收塔入口的区域,面积虽不大,但却极易出现涂层开裂等失效行为。一方面,碳钢基体与鳞片树脂防腐层的膨胀系数不同,且在涂层及基体钢板的厚度方向温度梯度较大,受热时二者界面会产生热应力;另一方面,干湿界面涂层的受热温度从烟气介质的高温状态急剧下降到经浆液及喷淋水冷却的低温状态,温度的陡降使涂层产生相当大的热应力。热应力和其他残余应力的叠加使得涂层处在非常大的内应力状态,进而导致涂层开裂。虽然鳞片树脂具有一定的松弛应力能力,但当内应力达到一定程度且超过涂层的抗拉强度时,开裂就是必然的。太原第一热电厂在2002年水平流FGD系统大修时就发现开裂等现象,造成烟道腐蚀,于是将鳞片全部打掉,重新涂抹,如图1784所示。解决这一问题的办法是:用高耐蚀的合金材料制作该区域,或者
图1785 吸收塔入口处烟道的腐蚀

图1786 吸收塔出口烟道的腐蚀

①原烟气尽管有140℃,但仍具有一定的腐蚀性;②锅炉的燃烧工况是多变的;③当FGD停运时,尽管有密封风,但烟气泄漏不可避免,其总量很大,会在烟道上冷凝。在某电厂,当2台锅炉都运行时,可以明显地感到停运FGD吸收塔内有浓烈的刺鼻的热烟气味,人不能进入其中。在重庆电厂的FGD系统上,再热器同连州电厂的基本相同,2000年11月初,FGD装置通烟气1个月左右,检查发现了类似连州电厂的再热器管子严重变色现象,其中有三根已经破裂泄漏,德国有关
专家认为是属于“静态腐蚀”(standstillcorrosion)。对再热器
后烟气携带的水分化验,其pH值低至1.7,呈严重的酸性,对尾部烟道和烟囱的安全构成了严重的威胁。因此必须有良好的防腐措施并定期检查,发现问题及时解决。
图1787 再热器管子严重变色现象
2002年8月,某电厂FGD系统检查发现,吸收塔内的搅拌器的叶片顶部都不同程度地损坏,如图1788、图
对于原烟气挡板至吸收塔入口前2m的烟道,设计材料采用碳钢,但实际却有很大的腐蚀,初步原因分析有以下几点:
1789所示。

图1788 吸收塔搅拌器的损坏

图1789(一)吸收塔搅拌器叶片的损坏

图1789(二)吸收塔搅拌器叶片的损坏
从上述各图看,搅拌器叶片的损坏不是机械碰撞、磨损,而是腐蚀所致。上图中的叶片明显是局部腐蚀,其形态多样,可以发生孔腐蚀、缝隙腐蚀、晶间腐蚀、应力腐蚀开裂等。表1784为某电厂FGD吸收塔内的浆液成分,主要是喷淋
为25.4mm×1.4mm。
液(石膏晶体、石灰石浆液、SO24-、SO23-盐、Cl-、F-等),
降温换热器管束组件的框架、顶板和底板以及支撑管束的梳形板均为SS41(一般结构用轧钢),而再加热器的这些部件的材质均为SUS316L(奥氏体不锈钢)。这种选材是三菱开发的GGH典型设计。
其pH=4~6.5,呈酸性,由于有循环泵的运行和搅拌器的扰动,必然有颗粒物的摩擦、冲刷。这是FGD系统中腐蚀环境最为恶劣的区域之一,必须有严格的防腐措施。运行不到2年,搅拌器叶片就损坏严重,这表明设计时考虑不周,选择叶片材料不当(材料为不锈钢,钢号1.4529),应当选用更好的防腐衬料,如镍基耐蚀合金等。
1号FGD降温换热器仅运行约3400h,第一级A组迎风面正中宽约500mm范围内的翅片厚度明显减薄并开始脱落,这种情况越靠烟道的下方越严重。运行到5000h左右,迎风面的翅片已大面积脱落。运行约10000h后,翅片已基本全部脱落,几乎成光管,但管壁厚的减薄并不突出。管束组件框架的顶板和底板以及梳形支撑板均严重腐蚀和磨蚀。
表1784 吸收塔内浆液的成分

由于降温换热器处于高温区,烟道用6mm厚的碳钢板制作,未做防腐衬覆。运行约4600h烟道底板已出现腐蚀穿孔,运行到7400h左右,底板已多处腐蚀穿孔。酸腐蚀严重的地方是换热器出口侧的底板。
在国内最早运行的珞璜电厂一期湿式石灰石/石膏FGD系统内,腐蚀现象也很严重。腐蚀现象主要发生在气—气热交换器和气—气再加热器。它们均为翅片管式换热器,由三菱设计、生产供货。换热器管内是闭式循环的除盐水,并添加有联氨和磷酸三钠以调整pH值防腐,所以管内腐蚀较小。
2号FGD再加热器在运行约20000h后首次出现管束腐蚀穿孔、漏泄,运行到25000h左右已频繁漏管,约30000h后更换了第一级的四组(A~D)和第二级最下层的E组。被更换的换热器的翅片均明显减薄,严重的部位翅片已呈参差不齐的锯齿状,厚仅0.2mm左右。个别部位也有翅片脱落现象。但管束腐蚀穿孔较严重,据不完全统计至少有30余处腐蚀穿孔,且部位的分布无明显规律。总的来说,腐蚀情况第一级较后一级严重,下层的较上层的突出。采用SUS316L的部件未出现明显腐蚀。
降温换热器和再加热器的基管、肋片的材质相同。基管:
JISSTB35(锅炉换热器用碳钢钢管),管壁厚3.5mm。肋片
FGD系统中的防腐非常重要,在设计时针对不同的腐蚀环境选用合适得当的材料,对于保证FGD系统的正常运行、减少维修、提高系统的安全性都有重要意义。连州电厂吸收塔内搅拌器的损坏是一个很好的教训。
为JISSPCC(一般用冷轧碳钢薄板及带材)3片,肋距×肋厚
另外在运行中应建立一套有效的制度来防止或减少腐蚀的
发生,保证设备长期无故障地运行,例如:
(1)监测氯化物含量和pH值范围。监测氯化物含量本身并不能防止腐蚀,但可以发现潜在的问题。控制pH值对脱硫效率和防止氧化皮有重大作用,不适当地降低pH值会加速腐蚀。
(2)防止氯化物的浓缩,及时排走高浓度氯化物的浆液。(3)保持表面无污泥沉积或氧化皮,沉积物和氧化皮的聚
积会增加点蚀和缝隙腐蚀的危险,因此在有条件时应及时清洗。
对吸收塔入口的烟道,设计时除提高烟气挡板的密封性能外,可以增大密封风的压力和流量。但在连州电厂,目前已无法作大的改动,只有加设防腐材料如玻璃钢等,并定期检查。对吸收塔出口,设计已涂有武汉KCH公司提供的1.2~1.5mm

厚的KORROPLASTVE310防腐涂料,现已有腐蚀,可见脱硫
后烟气腐蚀性的厉害。选用更好的防腐材料如含镍不锈钢等,固然可以延长使用寿命,但更重要的是要定期维修检查,发现问题及时处理,只有这样才能不断提高FGD系统的安全性。
图17810(二)吸收塔入口处的积灰、结垢
(三)FGD系统内的结垢与固体沉积
FGD系统中有三种结垢形式:
过饱和度越大,结垢形成的速度就越快,仅当α<1.4时才能获得无垢运行。要使α<1.4,需适当地设计吸收塔内石膏浆液浓度、液气比和提高氧化率。日本三菱的试验认为液气比越小,α越高,使α<1.4的最低液气比为11。石膏浆液浓度与α的关系亦是如此,浓度越低,α越大。
(1)灰垢,这在吸收塔入口干/湿交界处十分明显。高温烟气中的灰分在遇到喷淋液的阻力后,与喷淋的石膏浆液一起堆积在入口,越积越多,在连州电厂FGD系统吸收塔的入口处冷、热交界的1m左右区域,结垢、积灰现象十分严重,烟道底部垢层厚20~30cm,人可踩在上面。入口处两侧壁面、中间支柱上都积有垢山,如图17810所示,其主要成分
吸收塔壁面及循环泵入口、石膏泵入口滤网的两侧就是此
类石膏垢,如图17811、图17812所示,吸收塔壁
面在浆液层下(约10m)均匀地结了一层松散的垢层,约1.5mm厚,可以很容易的剥落下来。另外,在上层除雾器的叶片上以及再热器管壁上,由于冲洗不能完全彻底,都有明显
是CaSO4和灰分。
的浆液黏积现象,如图17813、图17814所示。在
(2)石膏垢,当吸收塔的石膏浆液中的CaSO4过饱和度大于或等于1.4时,溶液中的CaSO4就会在吸收塔内各组件表面析出结晶形成石膏垢。
水力旋流溢流的盖子上以及底部分流器管子上,均有结垢发
生,如图17815,图17816所示。
石膏过饱和度 α=[Ca2+][SO24-]/Ksp
式中,[Ca2+]、[SO24-]分别为溶液中Ca2+、SO24-离子
的浓度(mol/L);Ksp为CaSO4 ·2H2O的浓度积(mol2/L2 )。


图17811 吸收塔壁面的垢层

图17810(一)吸收塔入口处的积灰、结垢
图17812 循环泵入口滤网的垢层


图17813 下层除雾器上部的浆液黏积现象
图17816 分流器的结垢

在吸收塔底,尽管均布有四台搅拌器,但仍存在“死区”,沉积的石膏便堆积在此处高达0.5m,如图17817所示,有的硬如石块。在泵的入口,沉积的石膏浆液达到了滤网的高
度,图17818、图17819显示了这一点。
图17814 再热器管壁上的浆液黏积现象


图17817 吸收塔底沉积的石膏
图17815 水力旋流器溢流盖子的结垢
(3)当浆液中亚硫酸钙浓度偏高时就会与硫酸钙同时结晶
析出,形成这两种物质的混合结晶[Ca(SO3)x·(SO4)x·

1/2H2O],即CSS垢(Calcium Sulfateand Sulfite),CSS在
吸收塔内各组件表面逐渐长大形成片状的垢层,其生长速度低于石膏垢,当充分氧化时,这种垢就较少发生。
图17818 循环泵入口沉积的石膏

图178192台石膏浆液泵前沉积的石膏
珞璜电厂一期FGD的吸收塔是填料塔,结垢主要发生在格栅床及吸收塔内的构件表面,特别是不易被浆液湿化的死角,如吸收塔罐体内壁,吸收塔干、湿交界处以及非动力输送的石膏浆回流管道。填料塔塔内有两层每层高4m的格栅床,相距1.5m2号吸收塔下部的罐体在运行不到2000h已出
力不稳定,各泵相互负荷,泵出口流量不稳定并低于设计值的情况。达到额定流量时单台泵的电流应达到1A,实际电流为38~50A,各泵电流波动达2~14A。根据泵的性能曲线,按电流降低来估算,循环泵流量降低是相当大的,实测下降13.1%,液气比的下降是不容忽视的。
现0.3mm厚的壁垢。1号FGD运行5000h吸收塔罐壁最厚
(10)由于泵的吸入侧护板的磨损,使护板与叶轮的间隙增大,泵的总效率下降。
的垢已达10mm。其下层格栅床结垢较少,塔中间的格栅基本无垢。而上层格栅床靠塔壁四周1~2m范围内的格栅结垢较多。同一格栅一床中越下层的垢越严重,格栅几乎全部被垢堵塞,大部分垢呈灰黑色略带浅棕色,坚硬,断面呈针状结晶。
FGD系统内的结垢和沉积将引起管道的阻塞、磨损、腐蚀以及系统阻力的增加,应尽量减少。解决的方法应从FGD系统的设计和运行两方面考虑。
1号、2号FGD投运3年后更换了约50%的格栅,并对其余格栅进行了除垢清洗。逐渐生长的垢将496mm×496mm×104mm的单块格栅块相互勃结成一个整体,拆开十分困难,需用钢钎破坏性地拆除。
在设计时应选择合理的工艺,如在吸收塔入口烟道增加冲洗水喷嘴,定期冲洗结尘,选择合适的材料等,减少结垢的发生。在运行时可以从以下几方面来预防结垢的发生:
(1)提高锅炉电除尘器的效率和可靠性,使FGD入口烟尘在设计范围内。
吸收塔罐体内壁的垢呈片状、坚硬、表面粗糙,断面亦呈针状结晶。罐内壁脱落的垢块在石膏浆液中会逐渐长大,曾发现重约25kg的垢块。
(2)运行控制吸收塔浆液中石膏过饱和度最大不超
过140%。
(3)选择合理的pH值运行,尤其避免pH值的急剧变化。
三菱有关专家认为,填料塔结垢较为严重的主要原因是氧化不充分,具体原因分析如下:
(4)保证吸收塔浆液的充分氧化。
(1)烟尘含量较高,在干、湿交界处,冲洗管与塔壁上缩积成较大的灰垢,坠落的灰垢卡在格栅孔中成为垢生长的
“中心”。
(2)格栅床与塔壁之间有150mm左右的间隙(防止格栅擦伤塔内壁防腐层),造成烟“短路”,使局部液气比偏小。
(5)可以向吸收剂中加入添加剂,如镁离子、乙二酸等。乙二酸可以起到缓冲pH值作用,抑制SO2的溶解,加速液相传质,提高石灰石的利用率。镁离子的加入生成了溶度大的MgCO3,增加了亚硫酸根离子的活度,降低了钙离子的浓度,使系统在未饱和状态下运行,以防结垢。
(3)循环喷淋管被异物(施工遗留物、脱落的垢片等)堵塞,造成个别部位喷液减少甚至无浆。吸收塔循环泵出口压力波动,使各喷头喷出的浆液量不稳定、不均衡。
(6)对接触浆液的管道在停运时及时冲洗干净。(7)定期检查,及时发现潜在的问题。
(四)FGD系统内的磨损和堵塞
(4)由于未设计事故储浆罐,长时间停机后再启动时,重配的石膏浆浓度偏低,达不到不低于15%(质量)的设计要求。
(5)格栅填料、塔内繁多的支撑构件使塔内表面积大、死角多,增加了结垢的可能性。因此二期采用了液柱塔,这大大减轻了结垢的发生。
(6)保持格栅表面光滑清洁是减缓结垢的措施之一,因此有些工艺设计中在格栅上方布置有事故喷水装置,正常停机时则用来冲洗格栅。
由于FGD装置运行系统内循环流动的主要是石灰石和石膏浆液及其他一些杂质,一些流体既具有磨损性又有一定的酸性,对浆液泵和管道产生严重的磨损。在珞璜电厂一期FGD系统内,浆液泵、内衬、管道等均出现有磨损。珞璜电厂除石灰石浆输送泵和GGH热媒水循环泵为金属泵外,其余大量采用美国BGA公司生产的内衬橡胶、卧式离心泵和立式液下泵。这种泵的蜗壳、前后护板、叶轮、副叶轮(干密封式)以及吸入口套管均采用美国500号橡胶衬覆。容量最大的是吸收塔循
环泵,橡胶叶轮直径为1041.4mm,额定流量达4670m3/h。
(7)珞璜电厂FGD吸收塔罐体直径达20m,垂直布置的搅拌器叶片直径为4.5m,但偏心布置。除紧靠循环浆出口管一侧外,其他各方罐体内侧边缘均有石膏沉淀缩积“死区”,严重的“死区”在搅拌器偏离的一侧,该处沉积的石膏超过1m。由于氧化空气喷嘴距罐底仅300mm,“死区”的氧化空气喷嘴被堵,被堵的喷嘴占全部喷嘴数的10%~15%左右,造成氧化不充分。
所有的衬胶灰浆泵的过流件,除泵蜗壳的衬胶和驱动侧护板外,寿命均不超过10000h。吸收塔循环泵前护板运行仅6500h已严重磨蚀,大部分过流件的寿命在7000h左右。磨蚀最严重的部位是吸入侧护板和叶轮,护板磨蚀的外观是密集的蜂窝状半圆凹坑。闭式叶轮蚀、磨损的部位主要在叶片的进、出浆处以及叶轮吸入侧边缘和轮毂。吸收塔循环泵吸入侧护板和叶轮磨蚀是典型的气蚀、冲刷磨损的结果。出现蜂窝状圆坑后磨蚀速度增加很快,如不能及时发现可能将护板磨穿,侵蚀泵的蜗壳,造成严重损坏。
(8)三菱传统设计的氧化配气管是固定布置在罐体的下部,在直径20m的罐体中布了856个φ16.7、口朝下的喷嘴管,喷嘴密度达2.74个/㎡,采用的是一槽系统。从罐抽出的循环浆量设计为28000m3/h,大量空气随浆液进人循环泵内,不仅造成气蚀,而降低了泵的出力,使液气比下降。为缓解此情况,只好取消紧靠循环浆出口管的一排氧空气管,带来的副作用是又减少了12%的喷管。
气蚀主要是由于泵和系统设计不当,包括泵的进口管道设计不合理,出现涡流和浆液发生扰动。进入泵内的气泡过多以及浆液中的含气量较大,也会加剧气蚀。磨损速度主要取决于材质和泵的转速。1996年将吸收塔循环泵的橡胶叶轮改为高铬合金铸造件,石家庄水泵厂采用沃曼(WARMAN)
(9)7台吸收塔循环泵的入口是通过母联管与罐体相连,母联管设计成变径管,其目的是使各泵的出力平衡,但实际上不仅每台泵的出力极不稳定,而且各泵的出力也相差较大。反映在泵电动机电流波动大,各泵电流相差较大。出现泵入口压
泵的技术,选用 A49合金,成分为Cr27.5%、Ni1.8%、Mo1.8%,硬度达到430HB,可以使用6年左右。这种合
金由于含Cr、Mo以及高硬度,使其具有良好的抗点蚀性和耐冲刷磨损。
综上所述,泵与系统的合理设计,选用耐磨材料,减少进入泵内的空气量,调整好吸入侧护板与叶轮之间的间隙是减少气蚀、磨损,提高寿命的关键措施。
淀,多次发生此种事故后会造成风机喘振。
珞璜电厂一期FGD系统采用的防腐措施主要是日本富士富利克的6H、6R玻璃鳞片树脂内衬,防腐的范围是从吸收塔的干—湿界面至再加热器出口的内壁和内部所有的固定支撑梁柱,所有浆池、罐体以及相互联络的地沟。这两种树脂的耐温、防腐、附着力和抗渗透等性能均较好,运行3年未出现剥落、龟裂、脱层和化学变质现象。但耐磨性不理想,不如橡胶。使用10400h后,吸收塔内壁凡被大量浆液流淌冲刷部位(约占塔壁65%的面积)的表面层树脂已被冲刷掉,裸露出玻璃鳞片,须覆盖一层树脂。两层格栅床的支撑横梁与塔壁连接的端头约100mm处由于没有格栅遮挡缓冲,在下落浆液的冲刷下,约
18900(2FGD)~22500h(1FGD)后,两层玻璃纤维布增强
在连州电厂FGD系统中,出现过多处堵塞现象。2002年8月,检查发现吸收塔喷淋管有2个喷嘴内有橡胶片堵塞,如图17820所示。同样的橡胶片堵塞多次出现在石膏浆液抛弃泵中,估计是施工不小心留下的。在FGD系统调试时,石灰石粉采用临时上粉系统,通过输粉罐车自带的空压机直接将石灰石粉送入粉仓。由于石灰石粉中杂质较多,造成石灰石浆液密度计前后手动门的损坏,如图17821所示。按厂家要求要保持密度计浆液流量为1.4~2.3m3/h,但实际的石灰石浆液中常夹带有细沙之类的硬物,造成阀门堵塞和损坏,密度计不准便无法制浆。另外,曾发生石灰石浆液至吸收塔的管道堵塞。要避免这类情况的发生,一是保证石灰石粉的质量,尽量不带杂物,对石灰石粉的输送过程进行监控,在临时上粉管入口加装滤网;二是少调阀门,出现堵塞时及时手动冲洗阀门。
的树脂层被磨损,方形钢梁被腐蚀穿孔。随后,横梁的其他部位也相继发现有多处类似情况。每层格栅的上面用不锈钢管作成的框架通过四周的顶盘与塔壁顶紧,以达到向下压紧格栅床的目的,防止在烟气和浆液作用下格栅晃动。衬有橡胶的顶盘可通过顶杆的丝杆调节顶紧的程度,当顶盘松动,顶盘与壁面摩擦,树脂层磨损,进而腐蚀钢板造成穿孔。当格栅床未压紧,或格栅在整齐堆放时离塔壁过近,运行中晃动的格栅摩擦塔壁也会损坏树脂层。同样,安装检修中遗留的机械杂物以及从干—湿界面落入的垢块卡在塔壁和格栅床之间也会磨损树脂层,最终使塔壁穿孔漏浆。涂敷树脂施工时留下的针眼,以及检修时脚手架等碰伤树脂也是造成结构腐蚀的原因之一。

FGD系统橡胶内衬主要用于石膏浆液输送管道,橡胶种类是丁基橡胶(ⅡR)。衬胶弯管和直管的设计寿命分别为3年和5年。从实际运行情况来看,一般都能达到。磨损部位主要发生在管道法兰连接处和多通道管件、装有节流孔板的出口侧管道,特别是当节流孔磨损后。衬胶管道中的蝶阀只能全关或全开,当未关到位或运行中用来调节流量,阀门处于非全开时,阀体内衬和阀门出口侧的衬胶管道很快将磨损。浆液流速越大,磨损越快。
图17820 喷嘴上的橡胶片
在重庆电厂FGD系统中,制浆系统采用了湿式球磨机,各级再循环箱返回球磨机的浆液管采用了玻璃钢管,在实际运行不到9个月的时间里,管道局部已被磨穿。
石膏浆液的磨蚀性强,沉淀快,沉淀有自密实的倾向。因此,管道设计中首先要考虑的是防止发生石膏浆液沉淀。管径和管道的倾斜度(0°~20°)对沉淀的形成影响不大,主要是石膏浆液的浓度和流速。提高流速对防止沉淀有利,但会使管

道磨损增加。浆液浓度10%~14%(质量),流速0.67m/s是
图17821 石灰石浆液密度计前后手动门的损坏
沉淀形成的临界值。此外,在布置设计中要力求避免管道下凹,否则应在管道的最低点安装排空阀,停运时用水冲洗。对于斜度不大、较长的管道,也应设置停运自动冲洗装置。
装有调节阀的管道要在阀门入口端的管道上安装回流管。当阀门全关时,回流浆流速不低于引起沉淀的最低流速;否则调节阀要设定最小开度。
连州电厂FGD试运过程中2台给粉机均发生过堵塞现象。拆开检查,发现下粉制浆系统因石灰石粉上粉用压缩空气未经干燥,潮湿空气中水分为石灰石粉所吸收,致使石灰石粉存放过久后易受潮、结块,堵塞下粉管道。现电厂已在粉仓旁新建一个空气压缩机房,专门制备上粉用冷干压缩空气。另外,在FGD系统长时间停用时,运行人员定期运行给粉机也可起到防堵作用。
因设计不合理引起堵塞的现象不突出,更多的原因包括:(1)浆液中有机械异物(包括衬橡胶管损坏后的胶片)或
垢片,最易在阀门或大、小头处造成堵塞。
(2)泵的出力严重下降,使向高位输送的管道堵塞。
(3)阀门内漏。
(4)未及时排空停机后管道中的剩余浆液。
水力旋流器漏斗底部(图17822)出现过堵塞事故,使得脱水系统一度中断。堵塞原因是漏斗底部因结构特殊,长久运行后,石膏黏附、堆积日益严重所致。只要运行人员勤加检查,每班在水力旋流器漏斗底部用工艺水反冲几次,保持畅通,即可避免堵塞情况的再次发生。
(5)管内结垢。
日本2002年修订的JEAG3603—2002《排烟处理设备指
(6)氧化风机故障停运,浆液进入氧化配气母管并很快沉
南》(以下简称《指南》)对FGD系统内的防腐蚀、磨损及堵

塔液室容量以控制石膏的饱和度,并确保石膏晶种的生成。
2)防止喷雾嘴结垢。采用构造简洁的喷嘴(如旋转叶片式),设置过滤器去除循环液中的夹杂物。
3)防止吸收塔除雾器结垢。采用构造简单的部件(如波形板等);用工业用水或过滤液进行有效冲洗;选择合适的烟气流速。
4)防止浆液配管内的圆形物沉积。选择合适的管内流速,以适应负荷的变化;配管设计要保持合适的倾斜度,避免过度弯曲及积留浆液;对于长管道,液流停滞部位(集管末端等处)设置可拆卸的排水管(停止运转时能排除滞留的液体);设置停运时配管内更换清水的装置。
图17822 水力旋流器底部漏斗的堵塞
塞提供了指导性的对策,介绍如下:
5)防止CCH堵塞。对于回转式GGH,设置吹灰装置和运行中的冲洗设备;对于热媒式GGH,设置清洗装置,简洁配置传热管。
(1)防腐蚀对策。脱硫设备处理的流体除SO2外,还有SO3、HCl、HF等腐蚀性物质;因此,必须根据流体的组成、温度、浓度等使用耐腐蚀材料,并考虑防腐内衬的施工等,同时必须在结构设计上采取相应的对策。
《指南》还对FGD系统的设备设计、保护装置提出了要求。如紧急停止装置,在运行中,若发生脱硫装置的本体温度超过最高允许值、脱硫风机跳闸、停电、运行人员判断必须紧急停止的其他情况时,应有操作装置使脱硫设备全部或部分迅速而安全地停下来。
(2)防磨损对策。除使用耐磨损材料外,为了避免流体的流速过大而导致局部湍流或撞击,必须选定合适的流速,排除极端的节流机构等,特别是对浆液,必须充分考虑其浓度及特性。要明确区分腐蚀和磨损,并讨论其对策,以石灰石/石膏法为例,要解决的问题主要有三个方面:①腐蚀与磨损的因素分析;②掌握选择耐腐蚀与耐磨损材料的要领;③正确采取防腐蚀及磨损的对策。
针对脱硫设备必须紧急停止的异常情况,在设计上应考虑:①不能对锅炉产生影响;②停运时对脱硫设备没有损伤。为了在脱硫设备紧急停运时锅炉仍能继续运转,宜设置旁路烟道,使全部烟气能从这里通过;同时,根据环境标准要求,脱硫设备停运时,锅炉要改燃低硫分的燃料。脱硫装置本体温度超过最高允许值时,为保护装置本体内的材料,必须切断高温烟气,故应设置强制冷却脱硫装置本体入口烟气的装置。
1)除尘塔及吸收塔的防腐、防磨。对于高温烟气与喷淋接触的地方(即干—湿反复接触部位),除选定适合两种流体的材料、采用可润湿性的塔壁构造外,有些部位还需采用耐酸、耐热和耐磨损的保护层。运行开始时喷向塔入口烟道的液体反向流动会引起腐蚀,要在喷液一开始就立即通风或采取前项保护措施。在喷液冲撞的塔壁面和搅拌机周边粘贴内衬和不锈钢等保护层。同时,为防止损伤壁面,液体的喷射角应对着塔的内侧。强化塑料(FRP)喷嘴的集管、喷嘴根部和顶端附近易磨损,故可在喷嘴上安装聚丙烯套管等。
在采用回转式GGH的脱硫设备中,设计中可考虑备用驱动电机。在采用补燃器作为烟气再加热装置的脱硫设备中,应考虑设计在脱硫风机停止、燃料油的压力低于允许值以及运行人员认为需要时,能使燃烧器紧急灭火的装置。
2)罐类的防腐、防磨。在带高浓度泥浆搅拌机的石膏浆槽等处,因搅拌槽内壁易磨损,要在内贴的硬质橡胶上再贴上软质橡胶。罐、塔内设置的管道、喷嘴等内部部件上使用的螺母等,由于间隙腐蚀容易松动,可填以间隙充填材料并拧紧螺栓、螺母。
在石灰石/膏法脱硫设备中,应考虑设计联锁装置,在脱硫装置本体温度超过最高允许值时采取保护措施。在脱硫装置本体入口设置紧急冷却喷雾喷嘴并采用2段联锁,尽可能不造成紧急停运。2段联锁即当锅炉一侧空气预热器故障,脱硫装置本体温度及同侧比,设备入口烟气温度升高到规定值时,紧急冷却喷雾喷嘴动作。当采用了上述方法,温度仍然继续上升而超过最高允许值时,迅速将此设备停运。当除尘塔循环泵全跳闸时,脱硫装置本体的温度将明显超过最高允许值,应迅速停运。
3)配管类的防腐、防磨。泵与配管的接合部因湍流急易产生磨损,泵和配管之间可用陶瓷等耐磨材料的短管(变径管)连接。在使用浆液配管、尤其是有内衬的配管时,要采用合适的流速(小于3m/s),避免流速大时,配管弯曲部位的内衬产生剥离和磨损。
4)其他。为防止腐蚀,应定期用清水冲洗除雾器等接触腐蚀性流体的金属部位,此举还有效地防止堵塞。
针对运行中可能发生有关安全障碍及性能降低的情况,在设计中要考虑报警装置。其情况主要有:脱硫装置本体温度高或本体入口烟温高;除尘塔循环泵出口压力或循环管道流量忽高忽低;吸收塔内液体pH值忽高忽低;脱硫设备出口(烟囱入口)SOx浓度高;脱硫设备出口(烟囱入口)温度低;脱硫风机停运;旁路烟道风门压差忽高忽低;回转式GGH的电机停运;锅炉停运;脱硫设备停运;电源丧失;控制用空气压力降低等。
(3)堵塞对策。设计时要选择合适的流体流速、浓度,或者采用不致引起堵塞和浓缩的内部结构及填料。特别是对于烟尘的堆积、浆液中固形物的沉积以及结垢等造成的堵塞,除采用好的结构外,还应在设计上充分考虑采用水洗、调节pH以及在脱硫设备停运时进行搅拌等处理对策。
(五)其他
对于石灰石/膏法的防堵塞,要考虑:
1)防止吸收塔结垢。对于由物理原因形成的结垢,在设计上要注意选用适当的液气比,采用憎水性好的材质作填料,配置喷雾液滴均匀分散的喷嘴,采用无浆液停滞的塔结构等措施。对于化学原因引起的结垢,要设计合适的循环液量及吸收
为提高FGD系统的安全性,在设计方面要充分考虑各装置内部不可泄漏液体、烟气,万一泄漏时,也不能危害人体及周围的设备,特别是对法令规定的有毒及危险物成分的液体及气体,要有防止其流出及飞散的措施。为防止脱硫风机、烟道及GGH泄漏,对于转轴贯通外壳处用空气密封。为防止泵的液体泄漏,在泵的叶轮上安装内叶片,在轴封部注入密封水或采用机械密封等方式。
在连州电厂FGD系统调试制浆时,石灰石粉通过浆液罐
的溢流管冒出,严重污染周围环境。起初是用仪用空气密封,但效果不佳,并且造成仪用空气压力降低、备用空压机频繁启动的现象。后改用流化风机的风来密封,但也不行,仍有石灰石粉外冒。又临时用一皮管引至循环泵房的排污池中,以为可将冒出的粉溶入水中,然而皮管不久就浮在水面上,喷出的粉弥漫在泵房内,造成更大的污染。更为严重的是,这一改动引起溢流管内浆液沉淀结块而导致堵塞,而运行人员没有及时发现,最终导致石灰石浆罐液位过高(液位计稍有不
准)、罐内憋压将玻璃钢结构的石灰石浆罐顶鼓起,受损变形,并导致搅拌器支架附着部位多处断裂的事故。后再次改造,将溢流管直接导到一个特制水罐底部,但因水罐水量少,而溢出气流大,罐内储水很快飞溅出去,露出溢流管口,使水封及过滤作用失效。
最后将水罐上部也密封,制浆时开启少量浆罐取样工艺水将溢流粉溶于罐中,通过小水罐底部的管子流入排污池,彻底解决了这一问题(如图17823所示)。

图17823 石灰石浆液罐溢流管水封的改造
同样,在某电厂FGD石灰石破碎系统中,两级给料机均是敞开式结构,粉尘随着给料机的振动四处飞扬,造成对环境的严重污染,必须改造。
作为吸收剂原料使用的化学药品,其品质必须满足有关工业标准,或者具有同等或以上质量。另外,化学药品的贮藏及使用必须充分考虑其性质,特别是对于被指定为剧毒及危险品的药品,必须遵守有关法规。对于回收的副产品,如需再利用,则应根据用途充分考虑其品质。当采用抛弃法时,要充分考虑安全性及对周围环境的影响,同时必须遵守有关废物处理的法律及水质污染防止法规。
安全,也给脱硫装置的稳定运行带来巨大影响。一方面,当进入吸收塔的烟气量不变而烟气中SO2含量增大时,受气/液接触面积和传质速率的限制,脱硫效率将会显著下降;另一方面,进入浆液中的SO2摩尔数增加使得浆液池中的吸收反应和氧化结晶的时间和空间不足,浆液的pH值将下降,对设备的安全性带来影响。同时,浆液中亚硫酸钙质量浓度增高,影响石膏脱水系统的正常运行。当进入吸收塔的SO2质量数增大到一定数值后,整个吸收塔的动态平衡将被破坏,脱硫系统将无法维持运行。例如,某电厂 10日内 SO2浓度低至
1300mg/m3以下,高到5000mg/m3以上,而设计在3000mg/
要有完善的监测系统设计,监测项目主要有:处理烟气量,脱硫设备出口的SO2浓度,脱硫设备入口及出口的烟气温度(根据有无GGH,出口烟气温度监测设在GGH出口或吸收塔出口),吸收塔内液体的pH值以及为确保安全的其他必须监测的项目,如除尘塔/吸收塔循环泵的出口压力或循环管道内的流量,脱硫设备各通风系统的压力等。
m3,可见煤值变化之剧烈。又如烟尘浓度高时,造成吸收塔内惰性物质、镁、氟等影响石灰石吸收的化学成分增加,石灰石溶解能力开始下降,逐渐失去吸收SO2的能力,使pH值异常下降,即使长时间的补充石灰石浆液也无效,最终导致系统操作恶化等。具体典型案例简述如下。
某电厂2×300MW机组建成后,随着煤炭市场的变化,燃煤含硫量大大超过脱硫装置的设计值,入厂煤低位发热量
监测设备的设计要注意三个方面:①根据不同用途,并考虑耐腐蚀、耐磨损及防堵塞对策来选定型式和材料;②防止排烟中的烟尘和雾滴堵塞;③由于监测用配管管径小,为防止堵塞,配管要尽可能短,并考虑设置冲洗装置。
经常低于设计值(23.5MJ/kg),最低至7MJ/kg;燃煤折算
第九节 脱硫外部条件变化分析及处理
硫分经常超出3%的设计范围,最高达到8%;原烟气SO2浓度实际值也经常大于脱硫装置设计最大的浓度8000mg/m3,最高达到14000mg/m3。由此给脱硫装置带来了下述一系列问题:
一、脱硫各种外部条件变化分析
脱硫系统入口烟气参数有烟气量、SO2浓度、烟尘浓度、烟气温度等,这些参数是脱硫装置的重要设计参数,它们决定了脱硫装置各主要设备的主要技术参数和主要辅助系统设备的容量。
(1)脱硫装置出口SO2浓度升高,脱硫效率下降。由于入口原烟气SO2浓度大大增加,超出脱硫装置处理能力,在未采取措施以前,脱硫装置出口净烟气SO2浓度增加,机组满负荷时脱硫装置出口SO2浓度经常大于设计值(400mg/m3),脱硫效率低于设计的95%。
大多数脱硫项目都规定了脱硫装置应在锅炉燃用设计煤种时脱硫效率能够达到保证值,但由于近年来我国电煤供需矛盾突出,电煤质量下降严重,一些电厂实际燃用煤种已与原设计煤种有较大差异,加之褐煤、泥煤等劣质煤的掺烧,入炉煤中硫含量和灰分明显增加,造成了脱硫系统烟气量、SO2浓度、烟尘浓度等严重超过设计要求。这不但严重影响了锅炉运行的
(2)石膏浆液及副产品石膏品质下降。石膏浆液品质随脱硫装置入口SO2浓度的增加而下降,导致脱水效果的降低和脱硫副产品石膏品质的下降,石膏中的氯离子含量、石膏含水量均有升高,石膏纯度下降;同时也造成吸收塔内石膏浆液浓度增加,石膏排出泵、吸收塔再循环泵电流增加、电机线圈温度升高,浆液泵、搅拌器、管道磨损加剧,危及设备安全运行。
(3)辅助系统运行时间大大增加,腐蚀、磨损、泄漏、结垢加剧。脱硫装置入口烟气SO2浓度增加,引起石灰石消耗量增加,因而产生的石膏量相应增加,石灰石预破碎系统、制浆系统、脱水系统运行时间大大增加。系统及设备的高投入率使脱硫装置的腐蚀、磨损、泄漏、结垢等问题增多。由于亚硫酸盐含量增加,一些浆液管道出现明显结垢,最严重之处内径
由原来的65mm变为20mm。
(4)发电成本伴随着脱硫装置入口SO2浓度的增加而增加,脱硫的各种消耗指标大大增加。石灰石消耗量、电耗、水耗、钢球消耗等基本与原烟气SO2浓度同比增加。最终导致发电成本相应增加。
(5)装置检修维护困难。燃用高硫煤使脱硫辅助设备的故障率增加,且因系统出力不足,而导致备用系统投运,导致部分脱硫装置主要设备无法停运,更增加了装置检修的难度。
二、外部条件调整应对措施
为减少脱硫烟气量、SO2浓度、烟尘浓度等严重超标问题,以下措施可供同类情况参考借鉴:
(1)加强燃煤掺混工作。从入厂煤看,电厂的燃煤含硫量虽然普遍偏高,但并不是每批煤都高,其中也有含硫量低的煤种。因此,加强燃煤掺混,使入炉煤含硫量保持相对平稳,尽量降低其含疏量是解决高硫煤对脱硫装置影响的有效途径之一。为此在煤场将洗煤和高硫煤分开卸车,分开堆储,按比例掺混,并根据电网负荷计划随时调整掺混比例。
(2)更换部分石灰石。石灰石的品质是指其化学成分和石灰石活性。鉴于燃用高硫煤的实际情况,可采用提高石灰石品质来改善吸收塔内的反应,以降低高硫煤给装置带来的影响,使脱硫装置运行参数得到改善和提高。
(3)加强运行调整。在烟气含硫量有限增加时可通过调整运行控制参数的方法,尽量维持脱硫系统稳定运行。主要可采用的手段有:
1)尽量保持较高的液气比。一般说来,相对较高的液气比有利于脱硫反应。实际运行中,液气比通常维持设计值,当机组负荷降低时停运1台吸收塔再循环泵以降低脱硫电耗。煤质改变后为了提高装置的适应能力,在低负荷或1台炉运行阶段不再停运再循环泵,以保持较高的液气比。
2)尽量保持浆液为低密度。调整浆液密度,将原来的下
限1080kg/m3下调为1060kg/m3,低负荷或1台炉运行阶段尽
量降低吸收塔浆液密度。
3)增大石膏旋流器出力。电厂石膏旋流器共14个旋流子,按设计运行12个,备用2个。当石膏浆液密度上涨较快时,12个旋流子运行往往出力不够,不能降低浆液密度。将备用旋流子投入运行后,其出力能在一定程度上满足要求。
4)调整氧化空气量。脱硫装置入口烟气SO2浓度增加后石膏浆液的产量随之增加,因此需要的氧化空气量相应加大。运行中根据入口烟气SO2浓度随时调整氧化空气量,必要时启动备用氧化风机。并增加1台氧化风机,以实现备用。但氧化空气量的增加受到氧化空间和时间的限制,因此,脱硫装置对烟气含硫量增大的适应性是有限的。
5)加强检修维护工作,及时处理缺陷,提高设备可靠性。另外当烟气参数大幅度和较长时间偏离设计值时,脱硫装
置的运行平衡将被破坏,最终导致脱硫装置被迫退出运行。为了避免这种情况,可采取人为限制脱硫装置的进烟量,以保持脱硫装置在设计的含硫负荷下运行。这种方法可有效避免由于脱硫运行参数恶化对设备寿命带来的严重影响,也避免了由于
脱硫设备被迫退出运行给环境带来的更大污染。
第十节 影响脱硫效率的主要因素
石灰石湿法烟气脱硫工艺涉及一系列的物理和化学过程,脱硫效率取决于多种因素。主要的影响因素包括:①吸收塔入口烟气参数,如烟气温度、SO2浓度、氧量;②石灰石粉的品质、消融特性、纯度和粒度分布等;③运行因素,如浆液浓度、浆液的pH值、吸收液的过饱和度、液气比L/G等。
一、吸收塔入口烟气参数的影响
1.烟气温度的影响
烟气温度对脱硫效率的影响如图17101所示。脱硫效率随吸收塔进口烟气温度的降低而增加,这是因为脱硫反应是放热反应,温度升高不利于脱除SO2化学反应的进行。实际的石灰石湿法烟气脱硫系统中,通常采用GGH装置,或在吸收塔前布置喷水装置,降低吸收塔进口的烟气温度,以提高脱硫效率。

图17101 烟气温度对脱硫效率的影响
2.烟气中SO2浓度的影响
一般认为,当烟气中SO2浓度增加时,有利于SO2通过液浆表面向液浆内部扩散,加快反应速度,脱硫效率随之提高。事实上,烟气中SO2浓度的增加对脱硫效率的影响在不同浓度范围内是不同的。
在钙硫比一定的条件下,当烟气中SO2浓度较低时,根据化学反应动力学,其吸收速率较低,吸收塔出口SO2浓度与入口SO2浓度相比降低幅度不大。由于吸收过程是可逆的,各组分浓度受平衡浓度制约。当烟气中SO2浓度很低时,由于吸收塔出口SO2浓度不会低于其平衡浓度,所以不可能获得很高的脱硫效率。因此,工程上普遍共识为,烟气中SO2浓度低则不易获得很高的脱硫效率,浓度较高时容易获得较高的脱硫效率。实际上,按某一入口SO2浓度设计的FGD装置,当烟气中SO2浓度很高时,脱硫效率会有所下降。
因此,、在FGD装置和钙硫比一定的情况下,随着SO2浓度的增大,脱硫效率存在一个峰值,亦即在某一SO2浓度值下脱硫效率达到最高。图17102是在实验室条件下烟气中SO2浓度对脱硫效率影响的试验结果。当烟气中SO2浓度低于这个值时,脱硫效率随SO2浓度的增加而增加;超过此值时,脱硫效率随SO2浓度的增加而减小。
3.烟气中O2浓度的影响
在吸收剂与SO2反应过程中,O2参与其化学过程,使

系统中Cl-含量(一般制在20000μg/g以内)。F-会形成氟化
物而包裹吸收剂,阻止其进一步溶解,降低吸收剂利用率及脱硫效率。
二、石灰石粉的品质、纯度和粒度的影响
1.石灰石粉品质和纯度的影响
石灰石中的杂质对石灰石颗粒的消溶起阻碍作用,并且杂质含量越高,这种阻碍作用强。石灰石粉中 Mg、Al等杂质对提高脱硫效率虽有有利的一面,但更不利的是,当吸收塔pH值降至5.1时(运行控制要求在5.5左右),烟气中的F-与Al3+化合成氟化铝络合物,形成包膜覆盖在石灰石颗粒表面。Mg2+的存在对包膜的形成有很强的促进作用。一方面,这种包膜的包裹引起石灰石的活性降低,也就降低了石灰石的利用
率;另一方面,杂质 MgCO3、Fe2O3、Al2O3均为酸易溶物,
图17102 烟气中SO2浓度对脱硫效率的影响
HSO3-氧化成SO24-。图17103是在烟气量、SO2浓度、
烟气温度等参数一定的情况下,烟气中O2浓度对脱硫效率的影响。随着烟气中O2含量的增加,脱硫效率有增大的趋势;当烟气中O2含量增加到一定程度后,脱硫效率的增加逐渐减缓。随着烟气中O2含量的增加,吸收浆液滴中O2含量增大,
它们进入吸收塔浆液体系后均能生成易溶的镁、铁、铝盐类。由于浆液的循环,这些盐类将会逐步富集起来,浆液中大量增加的非Ca2+离子,将弱化CaCO3在溶液体系中的溶解和电离。所以,石灰石中这些杂质含量较高,会影响脱硫效果。此外,石灰石中的杂质SiO2难以研磨,若含量高会导致研磨设备功率消耗大、系统磨损严重。石灰石中的杂质含量高,必然导致脱硫副产品石膏品质的下降。
加快了SO2+H2O—→HSO3-—O→2 SO24-的正向反应进程,有
因此,石灰石品质高,则其消溶性能好,浆液吸收SO2等相关反应速率快,这对提高脱硫效率和石灰石的利用率是有利的。
利于SO2的吸收,脱硫效率呈上升趋势。但是,并非烟气中O2浓度越高越好;因为烟气中O2浓度很高则意味着系统漏风严重,进入吸收塔的烟气量大幅度增加,烟气在塔内的停留时间减少,导致脱硫效率下降。
由于石灰石纯度越高价格也越高,因此,采用高纯度石灰石做脱硫剂将使成本增加,但这可以通过出售高品位石膏加以弥补。

2.石灰石粉粒度的影响
石灰石粉颗粒的粒度越小,质量比表面积就越大。由于石灰石的消溶反应是固相反应,其反应速率与石灰石粉颗粒比表面积成正相关,因此,较细的石灰石颗粒性能好,各种相关反应速率较高,脱硫效率及石灰石利用率较高,同时由于副产品膏中石灰石含量低,有利于提高石膏的品质。但石灰石的粒度越小,破碎的能耗越高。通常要求的石灰石粉通过325目筛
(44μm)的过筛率达到95%。
石灰石粉的粒度与石灰石的品质有关。为保证脱硫效率和石灰石利用率达到一定水平,当石灰石中杂质含量较高时,石灰石粉要磨制得更细一些。
图17103 烟气中O2浓度对脱硫效率的影响
三、运行因素的影响
1.浆液pH值的影响
4.烟气含尘浓度的影响
锅炉烟气经过高效静电除尘器后,烟气中飞灰浓度仍然较
高,一般在100~300mg/m3(标准状态下)。经过吸收塔洗涤
后,烟气中绝大部分飞灰留在了浆液中。浆液中的飞灰在一定程度上阻碍了石灰石的消溶,降低了石灰石的消溶速率,导致浆液pH值降低,脱硫效率下降。同时飞灰中溶出的一些重金
属如Hg、Mg、Cd、Zn等离子会抑制Ca2+与 HSO3-的反应,
浆液pH值是石灰石湿法烟气脱硫系统的重要运行参数。浆液pH值升高,一方面由于液相传质系数增大,SO2的吸收速率增大;另一方面,由于在pH值较高(大于6.2)的情况下脱硫产物主要是CaSO3 ·1/2H2O,其溶解度很低,极易达到过饱和而结晶在塔壁和部件表面上,形成很厚的垢层,造成系统严重结垢。浆液pH值低,则SO2的吸收速率减小,但结垢倾向减弱。当pH低于6时,SO2的吸收速率下降幅度减缓;当pH值降到4.0以下时,浆液几乎不再吸收SO2。
进而影响脱硫效果。例如,某燃煤电站由于电除尘器故障,导致含尘浓度很高的烟气进入FGD,脱硫效率由95%降低至73%。此外,飞灰还会降低副产品石膏的白度和纯度,增加脱水系统管路堵塞、结垢的可能性。
浆液pH值不仅影响 SO2的吸收,而且影响石灰石、
CaSO3·1/2H2O和CaSO4·2H2O的溶解度,如表1 7 10 1
所示。随着pH值的升高,CaSO3 ·1/2H2O的溶解度显著下
5.入口烟气中Cl—、F—含量高
降,CaSO4 ·2H2O的溶解度增加,但增加的幅度较小。因此,
如入口烟气中HF、HCl含量高,将导致进入脱硫浆液的Cl-、F-含量高。因为氯在系统中主要以氯化钙形式存在,去除困难,因此会影响脱硫效率,导致后续处理工艺复杂。在运行中应严格控制工艺水中的Cl-含量,及时排放废水,以保证
随着SO2的吸收,浆液pH值降低,CaSO3 ·1/2H2O的量增
加,并在石灰石颗粒表面形成一层液膜,而液膜内部CaCO3的溶解又使pH值升高,溶解度的变化使液膜中的CaSO3·1/2H2O析出并沉积在石灰石颗粒表面,形成一层外壳,使石灰
石颗粒表面钝化。钝化的外壳阻碍了石灰石的继续溶解,抑制了吸收反应的进行,导致脱硫效率和石灰石利用率下降。
的脱硫效率的前提下,可以适当降低L/G,从而降低初投资和运行费用。
表17101 50℃时不同pH值下石灰石、
目前,脱硫系统运行过程中,引起运行有效液气比降低而导致脱硫效率下降的主要原因有以下三种情况:
CaSO3·1/2H2O和CaSO4·2H2O的溶解度
单位:mg/L

(1)煤质变差。2008年以来,国内许多脱硫系统因机组燃煤变化、掺烧等原因,燃料热值、硫分发生变化,以致脱硫系统入口烟气量和SO2浓度增加,导致实际液气比降低,脱硫效率下降。
(2)循环泵实际出力不足。因循环泵选型缺陷或运行叶轮磨蚀等原因造成出力不足,循环浆液流量不够,实际液气比下降,脱硫效率下降。
(3)喷淋层、喷嘴设计选型缺陷。部分吸收塔喷嘴设计不合理,尤其是吸收塔近塔壁一圈的喷嘴设计选型不当,导致吸收塔壁流现象严重,实际液气比下降。此外,也有喷淋层管路设计不合理,到达各个喷嘴的流量和压力不均匀,雾化效果不一致,吸收塔断面各处烟气流速差别较大,局部液气比差别大,以致影响脱硫效果。
对应的调整措施主要有:
由此可见,低pH值有利于石灰石的溶解和CaSO3·1/2H2O的氧化,而高pH值则有利于SO2的吸收,二者互相对立。因此,选择一合适的pH值对烟气脱硫反应至关重要。新鲜石灰石浆液的pH值通常控制在8~9,但也有人认为,石灰石浆液的pH值应控制在6.9~8.9。实际的吸收塔的浆液pH值通常选择在5~6之间。
(1)如果机组低负荷长期投运,则对其脱硫设施可采取对应于高位喷淋层的循环泵,这样有利于烟气和脱硫剂充分反应,相应的脱硫效率也高。而当SO2浓度或烟气量增加时,为保证较高的脱硫效率,可加开一台循环泵以保证足够的液气比,实现高效率脱硫。
2.液气比L/G的影响液气比L/G的定义如下
LG=再循吸环收吸塔收出浆口液烟或气溶流液量的(流m3量/m(iLn/)min)L/Nm3
液气比决定吸收酸性气体所需要的吸收表面。在其他参数值一定的情况下,提高液气比相当于增大了吸收塔内的喷淋密度,使液气间的接触面积增大,吸收过程的推动力增大,脱硫效率也将增大。但液气比超过一定程度,吸收率将不会有显著提高,而吸收剂及动力的消耗将急剧增大。L/G对脱硫效率的影响如图17104所示。
(2)如果机组运行负荷较高,硫分或烟气量增加不是很多,加之提高液气比会使设备的投资和运行能耗增加,吸收塔内阻力增大,增加风机能耗。因此,应在尽可能保证脱硫效率的前提下尽量降低液气比。可以通过加入脱硫添加剂如镁盐、钠盐、己二酸的浆液等,这样既可以弥补吸收剂活性较弱的缺点,适当降低液气比,同时还可以提高脱硫效率,也可以通过运行调整适当提高或补充吸收塔石灰石浆液含量,适度控制吸收塔高密度运行等方式来达到提高脱硫效率的目的。
(3)如果硫分或烟气量的增加超过了吸收塔调整范围,则只能进行系统增容。
3.浆液循环量的影响

新鲜的石灰石浆液喷淋下来与烟气接触后,SO2等气体与吸收剂的反应并不完全,需要不断地循环反应,以提高石灰石的利用率。增加浆液循环量,提高L/G的同时,也就增加了浆液与SO2的接触反应时间,从而提高了脱硫效率。此外,增加浆液循环量,将促进混合液中的 HSO3-氧化成 HSO24-,有利于石膏的形成。但是,过高的浆液循环量将导致初期投资和运行费用增加。
4.浆液停留时间的影响
图17104 L/G对脱硫效率的影响
从图17104中可以看到,在浆液pH=7的条件下,
浆液在反应池内停留时间长将有助于浆液中石灰石与SO2完全反应,并能使反应生成物CaSO3有足够的时间完全氧化成CaSO4,形成粒度均匀、纯度高的优质脱硫石膏。但是,延长浆液在反应池内停留时间会导致反应池的容积增大,氧化空气量和搅拌机的容量增大,土建和设备费用以及运行成本增加。
液气比L/G<15L/m3时,随L/G的增大,脱硫效率显著增大。L/G>15L/m3后,随L/G的增大,脱硫效率增加幅度
5.吸收液过饱和度的影响
很小。
对于实际运行的石灰石湿法FGD系统,提高L/G将使浆液循环泵的流量增大,设备初投资和运行成本相应增大;提高L/G还会使吸收塔内压力损失增大,风机能耗提高。研究表明,在浆液中加入添加剂(如钠碱、己二酸等),在保证较高
石灰石浆液吸收SO2后生成CaSO3和CaSO4。石膏结晶速度依赖于石膏的过饱和度,在循环操作中,当超过某一相对饱和度值后,石膏晶体就会在悬浊液内已经存在的石膏晶体上生长。当相对饱和度达到某一更高值时,就会形成晶核,同时石膏晶体会在其他物质表面上生长,导致吸收塔浆液池表面结垢。此外,晶体还会覆盖那些还未及反应的石灰石颗粒表面,
造成石灰石利用率和脱硫效率下降。正常运行的脱硫系统过饱
和度一般应控制在120%~130%。
化空气的分配与搅拌设计配合不好,导致氧化空气分配不均匀,氧化效果差,这就需要结合吸收塔浆液池结构箱点、氧化风配置形式、搅拌方式等综合考虑,通过优化设计加以解决。
由于CaSO3和CaSO4溶解度随温度变化不大,所以用降温的办法难以使两者从溶液中结晶出来。因为溶解的盐类在同一盐的晶体上结晶比在异类粒子上结晶要快得多,故在循环母
9.仪表不准
液中添加CaSO4 ·2H2O作为晶种,使CaSO4过饱和度降低至
SO2测量仪、pH计等仪表测量不准确,数据漂移,对脱硫设施的运行调整起不到监控和参考作用。
正常浓度,可以减少因CaSO4而引起的结垢。CaSO3晶种的作用较小,通常是在脱硫系统中设置充气槽将CaSO3氧化成
CaSO4 ,从而不致干扰CaSO4 ·2H2O结晶。
石灰石浆液的供浆量由吸收塔入口、出口烟气中SO2的含量来确定。若SO2测量仪不准确会导致供浆量过多或不足,最终引起脱硫效率下降,石膏碳酸钙含量高等问题。
向吸收液添加含有 Mg2+、CaCl2或己二酸等添加剂,也可降低CaSO3和CaSO4的过饱和度。不仅可以防止结垢,而且可以提高石灰石的活性,从而提高脱硫效率。己二酸可起缓冲溶液pH值的作用,抑制气液界面上由于SO2溶解而导致的pH值降低,使液面处的SO2浓度提高,加速液相传质,可大大提高石灰石的利用率,从而提高SO2的吸收率。
烟气中SO2与吸收塔浆液接触后发生如下一些化学反应:
SO2+H2O→HSO3-+H+
CaCO3+H+→HCO3-+Ca2+HSO3-+1/2O2→SO24-+H+
SO24-+Ca2++2H2O→CaSO4 ·2H2O
6.Ca/S的影响
在石灰石湿法烟气脱硫中,钙硫摩尔比(Ca/S)定义为
加入CaCO3的摩尔数
Ca/S=
吸收塔进口烟气中SO2的摩尔数
在保持液气比不变的情况下,Ca/S增大,注入吸收塔内吸收剂的量相应增大,引起浆液pH值上升,可增大中和反应的速率,增加反应的表面积,使SO2吸收量增加,提高脱硫效率。但是,由于石灰石的溶解度较低,其供给量的增加将导致浆液浓度的提高,会引起石灰石的过饱和凝聚,最终使反应的表面积减小,脱硫效率降低。对于石灰石湿法FGD,吸收
从以上反应过程不难发现,高pH值的浆液环境有利于SO2的吸收,而低pH值则有助于Ca2+的析出,二者互相对立。pH值为6时,二氧化硫吸收效果最佳,但此时易发生结垢、堵塞现象。低的pH值有利于亚硫酸钙的氧化,石灰石溶解度增加,却使二氧化硫的吸收受到抑制,脱硫效率大大降低,当pH=4时,二氧化硫的吸收几乎无法进行,且吸收液呈酸性,对设备也有腐蚀。一般pH控制在5~6之间,最合适的pH值应在调试后得出。如果pH计测量不准,会导致供浆量过多或不足,引起脱硫效率下降。
塔的浆液浓度一般在20wt%~30wt%,Ca/S在1.02~1.05
之间。
因此,计量仪表在使用时要保证校正准确,平时要加强维护,冲洗干净,以保证测量值准确。此外,电厂应加强化学分析工作管理,通过化学分析对脱硫设施的运行及表计进行监督。
7.吸收塔内烟气流速的影响
在其他参数维持不变的情况下,提高吸收塔内烟气流速,一方面可以提高气液两相的湍动,降低烟气与液滴间的膜厚度,提高传质系数;另一方面,喷淋液滴的下降速度将相对降低,使单位体积内持液量增大,增大了传质面积,增加了脱硫效率。但是,烟气流速增大,则烟气在吸收塔内的停留时间减小,脱硫效率下降。因此,从脱硫效率的角度来讲,吸收塔内烟气流速有一最佳值,高于或低于此气速,脱硫效率都会降低。
第十一节 吸收塔内溢流及水平衡分析及处理
在脱硫运行中,吸收塔的水平衡是一个很重要的因素,如果在运行中掌握不好水平衡,会造成一些设备不能正常停运和吸收塔溢流等情况出现。吸收塔溢流装置是为保证塔内水平衡、防止液位过高倒流进烟道而设置的。
一、吸收塔内溢流水平衡失控原因分析
1.液位计显示偏低
在实际工程中,烟气流速的增加无疑将减小吸收塔的塔径,减小吸收塔的体积,对降低造价有益。然而,烟气流速的增加将对吸收塔内除雾器的性能提出更高要求,同时还会使吸收塔内的压力损失增大,能耗增加。目前,将吸收塔内烟气流
速控制在3.5~4.5m/s较合理。
针对压力液位计不准现象,首先应尽量避免高液位运行;其次是经常用水冲洗检查校验液位计。在发现液位计不准确时,应及时找检修人员维修,保证其准确性,从而通免液位计出现较大偏差。
8.石膏氧化不好
2.阀门内漏
在烟气脱硫的化学反应过程中,O2使 HSO3-氧化为
SO24-,随着烟气中O2含量的增加CaSO4 ·2H2O的形成加快,
脱硫效率也呈上升趋势。脱硫运行时多投运氧化风机可提高脱硫效率。考虑到脱硫的经济性,一般脱硫系统氧化空气倍率为
阀门内漏是由于除雾器冲洗水阀关闭不严而造成塔内液位不断升高,或进入吸收塔地坑的冲洗水量过大,地坑泵频繁往吸收塔注水引起,包括因吸收塔附近泵的机械密封冲洗水量过大,或部分设备冷却水也进入吸收塔地坑等。
2~3,设计一般取2.5。
3.吸收塔带浆,除雾器冲洗频繁
脱硫运行中,如果实际参与氧化反应的空气量不足,则浆液中大量的亚硫酸钙不能转化成硫酸钙,以及SO2向液相的溶解扩散速度减缓,导致脱硫效率下降。另外,如果硫分波动大,则部分时间内处理的硫总量增高较多将导致氧化倍率偏低,风量不够,这种情况在许多电厂普遍存在。一般可以通过增开备用氧化风机,或增设氧化风机来解决。也有部分电厂存在风机运行一段时间后效率下降,出力不够的问题。
因工况变化或设计原因,吸收塔带浆,导致除雾器频繁堵塞,因此需对其进行频繁冲洗。
4.吸收塔起泡
此外,也有设计上不合理导致氧化效果不好的情况,如氧
吸收塔起泡也是多数脱硫设施会发生的问题,锅炉投油、劣质燃煤、入口粉尘超标吸收剂品质不合格、工艺水水质差、氧化风机搅拌方式等都可能会造成吸收塔内起泡问题。若吸收塔内起泡,泡沫容易溢流,有的甚至倒流进入口烟道,会严重危害设备安全运行。泡沫也会造成虚假液位,一般可以通过添
加消泡剂解决。
氧化风机风量是根据设计煤种将HSO3-充分氧化为SO42-所需要的空气量,再考虑一定的裕量而确定的,扬程则是由氧化区的高度来选定的。进入吸收塔的氧化风量大大超过实际需要,这些富余的空气都以气泡的形式从氧化区底部溢至浆液的表面,从而助长了浆液动态液位的虚假值,导致吸收塔溢流。
需要特别指出的是泡沫多时,启动第三台浆液循环泵以及停止氧化风机运行时极易造成浆液溢流。
5.浆液在溢流管道处形成虹吸现象
如果浆液在溢流管道处形成虹吸现象,可采用在溢流管最高点加装对大气的排放直管来解决。
总之,在脱硫系统设备仪器正常的情况下,运行中为了避免溢流,可用的手段大致有:适当降低浆液静态液位;坚持正常排放废水,减少塔内杂质浓度;在保证脱硫效率的前提下,停用一台浆液循环泵,以减弱液面的波动;加消泡剂(此方式的效果最好)等方式。
二、吸收塔水平衡
当脱硫装置运行时,由于水分蒸发进入烟气、生成的石膏浆液排出及反应等造成吸收塔系统的水损失,因此需要不断地向吸收塔补充水,以维持吸收塔的水平衡。
为了保证脱硫装置的正常运行,达到预期的脱硫效率,吸收塔内要维持一定的液位高度。当吸收塔浆液池的液位高度低于最低的设定值时,设置的控制系统实施联锁保护,使浆液循环泵和搅拌系统等停运;液位高于最高设定值时,石灰石浆液将产生溢流。
进入脱硫系统的水源主要有除雾器冲洗水、进入吸收塔的石灰石浆液中所含的水、其他各系统冲洗水、氧化空气冷却水等;脱硫系统的水损失主要是废水系统带走的、吸收塔内蒸发掉的和生成最终产物石膏所带走的水分。脱硫系统的水平衡即指二者之间的平衡。水平衡的直接体现就是吸收塔液位及浆液回收箱液位的稳定。吸收塔液位主要靠除雾器冲洗来维持,通过调整除雾器每一层冲洗的等待时间,来达到维持吸收塔液位的目的。而等待时间是由进入脱硫系统的烟气量与吸收塔液位共同决定的,虽然有经验计算公式,但还需要在实践中针对不同的系统进行修正、优化。
加强脱硫系统设备的运行管理,及时消除设备缺陷,提高运行及检修人员的操作及维护水平是维持脱硫系统设备安全、正常运行的保证。同时,加强脱硫化学监测分析表单的管理,建立监测数据与运行操作的紧密联系,使监测数据真正起到监测、监督、指导运行的作用,可为脱硫运行问题的解决提供宝贵的经验。
第十二节 吸收塔内浆液pH值异常分析及处理
在FGD系统正常运行时,系统根据锅炉烟气量和SO2浓度的变化,通过石灰石供浆量进行在线动态调整,将pH值控制在指定范围内,一般为5.0~5.6,以保证设计钙硫摩尔比下的脱硫效率以及合格的石膏副产品。但在实际运行过程中,会出现吸收塔内浆液pH值持续下降甚至低于4.0,即使长时间增供石灰石浆液后仍难以升高的现象,脱硫效率也维持不住,最终导致系统操作恶化。当出现该种情况时,可判定为出现了“石灰石盲区”现象,其原因大致有下述以下几种。
1.FGD进口SO2浓度突变
由于烟气量或FGD进口原烟气中SO2含量突变,造成吸
收塔内反应加剧,CaCO3含量减少,pH值下降。此时若石灰石供浆流量自动投入,为保证脱硫效率则自动增加石灰石供浆量以提高吸收塔的pH值,但由于反应加剧,吸收塔浆液中的CaSO3 ·1/2H2O含量大量增加,若此时不增加氧量使之迅速
反应成为CaSO4 ·2H2O,则由于CaSO3 ·1/2H2O可溶性强
先溶于水中,而CaCO3溶解较慢,过饱和后形成固体沉积,即出现“石灰石盲区”,这是亚硫酸盐致盲,主要是由于氧化不充分引起的。另外吸收塔浆液中的CaSO4 ·2H2O饱和会抑
制CaCO3溶解反应。
2.进入FGD系统中的灰粉过高,造成氟化铝致盲
由于电除尘后粉尘含量高或重金属成分高,在吸收塔浆液内形成一个稳定的化合物AlFn(n一般为2~4),附着在石灰石颗粒表面,影响石灰石颗粒的溶解和反应,导致灰石供浆对pH值的调节无效。
3.石灰石粉的质量变差,纯度远低于设计值
石灰石粉中的CaCO3含量降低,意味着其他成分含量增高,如惰性物、MgO等,它们使得石灰石粉的活性大大降低,吸收塔吸收SO2的能力大为降低,即使大量供浆也无济于事。
4.工艺水水质差、烟气中的氯离子浓度含量大
工艺水水质差、烟气中的氯离子浓度含量大等也会对吸收塔浆液造成影响而生石灰石盲区,预防出现石灰石盲区的措施有:
(1)控制进入FGD系统中SO2含量,使之在设计范围内。(2)在每次锅炉负荷或原烟气SO2含量突变时,如需快
速加大石灰石的供给量时,把石灰石供浆调节阀改为手动控制,根据人工计算缓慢加大供浆量,避免由供浆阀自动调节造成迅速加大供浆量,并根据运行参数趋势提前分析和判断,以缩短处理时间。当原烟气SO2含量或烟气量突然增大超出设计范围时,增开1台氧化风机以加强氧化效果,并掌握时机将吸收塔浆液外排脱水。
(3)定期对吸收塔浆液和石灰石浆液取样进行化学分析,掌握吸收塔浆液品质动态变化,根据吸收塔浆液中的CaCO3和CaSO3 ·1/2H2O含量调整pH值;要坚决更换品质差的石
灰石(粉)。
(4)调整电除尘电场运行参数和电场振打运行方式,提高电除尘效率,使进入吸收塔的粉尘量减少,防止粉尘中的氯离子、氧化铝、二氧化硅、氟对CaCO3,溶解产生抑制作用。
(5)做好各运行仪表的维护和校验,使之真实地反映运行状况。如在线pH计要用便携式pH计,并每周一次进行对比,发现偏差大时及时进行标定等。
(6)适当加大废水排放量。当出现严重的石灰石盲区现象时,短时最有效的办法是加强碱(如NaOH)或换浆,即将吸收塔内原品质恶化的浆液暂时外排,更换为新鲜的石膏/石灰石浆液,但这种方式治标不治本。
吸收塔内浆液pH值异常的另一个表现是pH值过高,有的在5.8以上甚至超过6.0。其原因是为了始终保持高的脱硫效率如90%以上而拼命往吸收塔内加石灰石浆液,造成塔内石灰石大量过剩而浪费,很不经济。若只关心脱硫效率,对运行人员考核很重,将致使运行人员只能采取加石灰石浆液的方式,这种做法应当改变。
第十三节 机组投油助燃稳燃问题
部分老机组因掺烧、低负荷燃烧等诸多原因,存在短时投油助燃、稳燃时脱硫不退出运行的情况。其主要会出现以下
问题:
(1)吸收塔起泡,产生虚假液位。(2)脱水滤布沾污油渍而影响脱水。(3)油烟对防腐材料有降解破坏作用。(4)油烟容易导致GGH沾污、积灰、堵塞。(5)影响吸收剂的利用和脱硫效率。
鉴于投油会导致泡沫及脱水不好的问题出现,建议脱硫机组(尤其是无旁路机组)尽可能采用无油点火、等离子和微油点火技术,尽可能避免大量油烟进入脱硫岛,部分老机组亦应尽可能通过改变燃烧方式或技改实现锅炉的稳定燃烧。
第十四节 石膏品质影响因素分析及处理
脱硫石膏的品质取决于脱硫岛入口条件、吸收塔运行控制以及脱水系统设备相关仪表的运行情况。
吸收塔中的石膏浆液通过石膏浆液排出泵送入石膏旋流器进行浓缩分离,浓缩后的石膏浆液含固量为50%左右,流入或泵送到真空皮带脱水机进行脱水处理。经真空皮带脱水机脱水处理后的石膏表面含水率不超过10%为达标。若石膏水分过高,不仅影响脱硫系统和设备的正常运行,而且对石膏的储存、运输及后加工等都会造成一定的困难,因此,应对其加以控制。
影响石膏含水率的因素较多,如石膏晶体的颗粒形状和大小、石膏脱水设备的运行状态及参与反应控制过程的仪表的准确度等。
一、外部输入条件分析及处理
1.脱硫入口烟气条件
与石膏品质相关的条件主要包括烟气参数、石灰石品质、工艺水水质等。
烟尘:对于新、扩、改建机组,脱硫岛入口烟气中的烟尘质量浓度必须控制在100mg/m3以内;对于现有机组的改造工程,必须控制在200mg/m3以下,否则洗涤后烟尘留在石膏浆液中,不仅影响石膏的脱水,也降低了石膏的品质。
HCl、HF含量:氯离子浓度过高除腐蚀系统外,还会降低脱硫效率,因此,需要定期排废水;HF量虽然少,但随着在浆液中积累到一定程度,氟化物会在吸收剂表面形成包覆层,屏蔽吸收剂,降低脱硫效率,降低石膏品质。
2.吸收剂
石灰石的品质对脱硫效率和石膏品质都有直接的影响。石灰石中的杂质(惰性物)在吸收塔内会影响石膏结晶的粒度和纯度,在脱水过程中影响石膏含水率;石灰石的粒径、活性如果不能满足溶解度要求,系统在低pH值下运行,亚硫酸钙比例将增加,致使石膏品质下降。
氧化铝会与进入浆液的F-形成氟化物,影响脱硫效率和石膏产品的黏性,以致脱水困难,石膏含水率高。
Mn、Fe等的盐类会影响石膏色泽,如广东某电厂因石灰石中含一定量的锰,则石膏颜色发红。
图17141为某电厂脱硫现场图片,因吸收剂泥沙含量多,以致石膏板结、脱水困难和含水率高。

图17141 吸收剂泥沙含量多致石膏板结
(a)泥沙杂质多;(b)杂质多的石膏表面
3.工艺水
工艺水水质对石膏的影响主要是其中的氯离子,石膏中氯离子残留量增加则其品质会下降。此时,若要满足市场要求,就必须用大量的电厂工艺水对石膏进行冲洗,这样则又会影响电厂运行的经济性。
二、吸收塔运行控制因素分析及处理
吸收塔浆液密度控制、停留时间、pH值、氧化风的供应量等会影响石膏的结晶,因此,运行时需综合考虑,结合实际,摸索出最佳控制参数。
1.石膏晶体太小
在石膏的生成过程中,如果工艺条件控制不好,往往会生成层状或针状晶体。尤其是针状晶体,形成的石膏颗粒小,黏性大,难以脱水。而理想的石膏晶体(CaSO4 ·2H2O)应是短柱状,比前者颗粒大,易于脱水。因此,控制好吸收塔内化学反应条件和结晶条件,使之生成粗颗粒和短柱状的石膏晶体,同时调整好系统设备的运行状态是石膏正常脱水的保证。
如果生产中发现石膏产品黏性大,含水率高,滤布粘堵等问题,可尝试增开1台氧化风机,提高氧化风量,促使更多粒径细小的亚硫酸盐转化成硫酸盐。
有时,设施重新启动时会出现上述情况,可适当补充石膏晶种,也有利于石膏晶粒涨大。
2.石膏浆液固体含量低
吸收塔内浆液的密度直观地反映塔内反应物的浓度(固体含量)高低,密度值升高,浆液的固体含量随之增加。工艺设计中在石膏排出泵出口管道上安装石膏浆液密度表,运行中根据该密度值的高低自动控制石膏浆液的排放,即密度值低于设定值时,石膏旋流分离器双向分配器转换到吸收塔,也就是不排放石膏。一旦密度超过设定的最大值,将开始排放石膏。
石膏浆液密度设定值根据反应产物石膏的形成和结晶情况来确定,一般要求是形成大颗粒易脱水的石膏晶体,运行过程中根据浆液性质的不同,设定值有所不同,一般控制在
1090~1100kg/m3之间,固体含量在12%左右。
三、脱水设备及仪表问题分析及处理
(一)脱水设备问题
1.旋流站
如果石膏晶粒正常,含水率仍然超标,则要检测旋流子低流浆液密度或含固量是否偏低,进而检查旋流站旋流子提供的压力大小,不同旋流子的压力大小不一样。调整好压力后进行旋流子底流取样化验,检查含固量是否达到50%以上,如果没有,检查石膏旋流站旋流子沉砂嘴口径及其管道内部是否合理或损坏,石膏旋流站旋流子沉砂嘴口径不合理也会导致下溢流含水过多。
定期清理石膏旋流器,保证浆液的浓缩及颗粒分离效果。运行监测中如发现石膏旋流底流固体含量低于40%~45%范围时,及时检查旋流器运行情况,如发现堵塞需及时清理。制定定期清理制度,防止由于堵塞引起的石膏浆液密度、固体含量的降低,影响石膏的后续脱水步骤。
2.脱水机
(1)真空度不够。石膏脱水不好,含水率超标的另外一个原因是脱水机真空度不够,真空密封箱密封不严,包括以下几种情况:
1)真空室对接处脱胶。真空室一般由高分子聚合物制造,这种材料伸缩变形很厉害,如果没有及时固定或是没有固定好,那么就有可能造成脱胶。此种情况下,只有等系统停运后,放下真空室重新补胶并固定每段真空室。
2)真空室下方法兰连接处泄漏,这种情况通常会有吹哨声。解决这种问题时,需要系统停运后放下真空室,检查垫片情况,如果垫片有问题则更换垫片,如果不是垫片问题,那么只需将泄漏处的法兰螺栓拧紧即可。
3)滤液总管泄漏,只需拧紧泄漏处的螺栓,如果是垫片有问题则需要停运装置后更换垫片。预防真空泄漏,需要在系统安装好后、滤布安装前进行真空度测试。这样可以把问题控制在系统投运之前,避免投运后的麻烦。
4)在真空泵入口如果有滤网,滤网堵塞也有可能造成真空度不够。严密监视皮带杌运行参数,控制皮带机真空。皮带机运行中真空的变化,直接反应石膏脱水的效果。真空升高时应关注塔内浆液监测指标是否在正常范围内。特别是当真空超过-0.5bar时,应检查真空升高的原因,并及时调整,联系监测站对石膏水分进行取样分析。
(2)石膏饼厚度调节。在运行过程中,维持真空皮带脱水机上石膏滤饼的厚度是保证石膏含水量不超标的重要条件。当石膏浆液泵排出的浆液流量发生变化时,落到脱水机上的石膏浓浆液量也随之变化。通过真空皮带脱水机变频器来调整和控制其运动速度,可以维持皮带脱水机上稳定的石膏滤饼厚度。
(3)滤饼冲洗。合理调整好石膏饼冲洗水流量及其布置位置也很重要。冲洗水流量过大,会增大脱水难度。冲洗水太少,滤饼中的可溶盐未能被洗涤下来,会降低石膏品质。如果真空度稍微偏高,但是没有到需要停运的地步,脱水率仍然不能达标。这个时候就要分析浆液里面的污泥问题,污泥覆在滤饼上面,形成致密的一层污泥膜,隔绝了石膏滤饼和空气,滤饼中的水分无法排挤出来。对于这种情况,可以通过加装滤饼疏松器对滤饼进行适当的疏松,翻动表面的污泥加以解决。
(4)滤布堵塞。启动前对滤布进行冲洗,检查滤布是否堵塞,滤布冲洗水箱的水位要控制在一定范围内。滤布冲洗水箱的溢流是到滤液水箱,当滤布冲洗水箱水位降低时,采用工业水补充。如果滤布堵塞,可尝试采用一定浓度的稀盐酸浸泡,再用水冲洗。
(二)pH计等测量仪表误差
吸收塔液的pH测量值是参与反应控制的一个重要参数,其输出值与锅炉负荷、脱硫装置入口SO2浓度和新鲜石灰石浆液的密度综合起来,用于确定需要输送到烟气脱硫吸收塔的新鲜反应浆液的流量。pH值升高,新的反应浆液供应量将减少;反之,pH值降低,新的反应浆液供应量将增加。若pH计测量不准,则需要添加的石灰石量就不能准确控制,而过量的石灰石使石膏纯度降低,造成石膏脱水困难。
加强在线检测仪表的维护,减小CRT显示与实际值的偏差。按照吸收塔中反应物计量和生成物品质要求,石灰石浆液的密度、吸收塔pH值与脱硫效率有直接关系。吸收塔浆液密度控制着吸收塔生成物石膏品质。因此,石灰石浆液和石膏浆液密度计以及吸收塔pH计都是参与化学反应和控制的重要仪表,运行中必须加强这些在线仪表的维护,保证其准确性。
四、废水排放及其他因素分析及处理
(一)废水处理排放量
废水排放量减少将导致吸收塔浆液中Cl-浓度的升高及杂质含量的增加。浆液中Cl-浓度及杂质含量升高会改变浆液的理化性质,影响塔内化学反应的正常进行和石膏结晶体的长大,同时杂质夹杂在石膏结晶之间,堵塞游离水在结晶之间的通道,使石膏脱水变得困难。石膏中的水分和杂质主要集中在上层石膏中。
废水处理系统必须正常投入运行,保证废水排放,以降低吸收塔内Cl-浓度及杂质含量,保证塔内化学反应的正常进行及晶体的生成和长大。塔内Cl-浓度应控制在10000mg/L以下,并尽量维持低运行值。
(二)其他
石膏浆液中含杂质太多也会导致含水率超标,杂质太多可能是烟气中的含尘量过大,应及时联系电厂主机系统调整烟气除尘器的运行。
脱硫装置工艺系统复杂,影响石膏含水率的因素也比较多,各因素之间又相互影响。引起石膏含水率超标的根本原因是:废水处理系统设备缺陷多,投入率低,废水排放量少,导致吸收塔浆液Cl-浓度及杂质含量升高,干扰了塔内脱硫化学反应的正常进行,影响了石膏的结晶和生长,使石膏结晶体颗粒大小、形状发生变化,晶体中细颗粒比例增大造成真空皮带机滤布堵塞。另外,吸收塔浆液固体含量低、pH计波动范围大也是影响大颗粒石膏的形成的原因之一。
第十五节“石膏雨”问题分析
在一些FGD系统中,特别是无GGH的湿烟囱,烟囱附近会出现“石膏雨”现象,地面上可显见一层石膏粉。其直接原因是脱硫烟气中携带了大量的石膏,间接原因有以下几方面:
(1)除雾器问题。如除雾效率差,浆液捕捉能力差,除雾器堵塞以致局部流速过高而带浆,除雾器坍塌等。
(2)吸收塔设计流速过高,除雾器带浆多;因此吸收塔的流速设计异常重要。
(3)浆液喷嘴设计选型不当,雾化粒径分布不合理,加之泵的选型不匹配,雾化超细粒径比例偏高,浆液被带出了吸收塔,在后续烟道、烟囱里碰撞聚集后在烟囱附近沉降。
要从根本上消除“石膏雨”,良好的吸收塔设计、除雾器设计、相关设备选型匹配、运行维护等均非常重要。
第十六节 提高石膏质量的运行管理措施
一、对石灰石吸收剂的管理
图17161所示的脱硫石膏组分中,石灰石的酸不溶物和亚硫酸盐等占5.19wt%,一般亚硫酸盐含量不会超过0.3%,因此,石膏中由石灰石酸不溶物带入的杂质所占的比例最大,接近5%。石灰石中的酸不溶物一部分是石灰石矿的伴生物,一部分是采矿时带入的黏土、泥沙。通过冲洗、分筛可以大量减少后一部分。因此,采用较高纯度的石灰石,降低石灰石原材料中夹带的黏土、石英、砂石是提高石膏质量的重要手段。按物料平衡计算,石灰石纯度与石膏纯度的关系大致是石灰石纯度提高1.7个百分点,石膏纯度可上升1%。例如,在某工况下,采用纯度为90%石灰石,可获得纯度为90%的石膏。如果工况不改变,要想通过提高石灰石纯度使石膏纯度提高到93%,那么需采用纯度为95.1%的石灰石。

图17161 FGD装置石灰石纯度与石膏成分的关系
如前所述,石灰石研磨细度对石灰石的反应活性影响很大,当吸收系统的运行条件未发生大的变化,如果出现石膏中CaCO3含量不正常的增加,而循环浆液可溶性亚硫酸盐浓度不高,那么很可能石灰石研磨工序出现了异常,石灰石粒径变粗。因此,定期检测石灰石浆液的粒径和测定石灰石CaCO3和酸不溶物含量是运行管理保证石膏质量的重要措施。
此外,当石灰石浆液浓度波动较大,对于未采用石灰石浆液密度来修正按化学计量确定石灰石供浆流量的系统来说,可能造成供浆量的紊乱,反应罐浆液pH值出现不正常的波动,从而使得浆液中过剩CaCO3浓度大大超过预定值,影响石膏质量。
二、对烟尘的控制
从烟气中脱出的飞灰可以通过“封闭”石灰石的活性来间接影响石膏质量。飞灰的直接影响是飞灰的大部分将进入石膏,通常成为石膏中含量居第三位的杂质成分。烟尘对石膏纯度的影响程度与烟尘浓度和脱除SO2的相对量有关。也就是说,烟尘含量越高,脱除的SO2量越低(或燃煤含硫量越低,或入口SO2浓度越低),烟尘对石膏质量的影响越大。可以根据灰硫比来估算烟尘浓度对石膏质量的影响,现介绍两种估算方法:
一种方法是,标准状态下,根据FGD系统入口烟尘浓度
(mg/m3干基)与SO2脱除量(mg/m3干基)的比值,即灰硫比[灰/SO2(%)]估算石膏副产物中飞灰含量(wt%)
石膏中飞灰含量(wt%)=灰/SO2(%)
3%
另一种方法是根据FGD系统入口烟尘浓度、燃煤含硫量与石膏中飞灰含量的关系(见图17162)来预估。当煤
中含硫量超过1.2%时可按灰(g/m3干基)/S(%)来计算,
此处的灰/S比取无量纲,而灰/S比与石膏中飞灰含量(wt%)的比值为一常数,等于6.9。因此,知道了灰/S比便可估算出石膏中飞灰含量。

图17162 脱硫装置入口烟尘浓度和
石膏中的飞灰含量的关系
现举例说明:某电厂燃煤设计煤种含硫4.02%,燃用设
计煤种 FGD装置入口 SO2浓度为 10000mg/m3 (标态、5.59%H2O、4.94%O2 ),入口烟尘浓度213mg/m3 (标态、5.59%H2O、4.94%O2 ),设计脱硫效率为95%。
按第一种方法:
灰/SO2比=
213(mg/m3)
10000×0.95(mg/m3)×100=2.24%(标准
状态)
所以,石膏中飞灰含量(wt%)=2.324%=0.75%按第二种方法:灰/S=0.213/(1-5.59%)
=0.056
4.02
那么,石膏中飞灰含量(wt%)=0.6.0956×100%=0.81%
上述两种计算方法得出的结果与图17162示出的石膏中飞灰含量值一致或很接近。从上述估算和图17162所示的线性关系可看出,FGD系统入口烟尘浓度增加一倍,石膏中飞灰含量也增加一倍。因此,FGD系统上游侧除尘设备的正常运行是保持FGD装置稳定运行不可忽视的条件之一。
我国大多数电厂中锅炉电除尘器和FGD装置分属不同的部门管理,电除尘器投运情况不能及时为FGD运行人员所知道,石膏中飞灰含量又非常规分析项目,当FGD系统出现石灰石“封闭”现象或石膏纯度下降时,无法及时准确地判断造成的原因。因此在FGD系统入口安装在线烟尘监测仪或通过其他方式让FGD运行人员及时了解电除尘器的运行状况,有利于FGD系统的运行管理。
三、对氧化效率的控制
由于FGD系统无在线检测循环浆液和石膏成分的分析仪,运行操作人员无法及时了解系统氧化效率。为了保证氧化效率,运行人员应根据入口SO2浓度,烟气流量及时合理地调整氧化空气流量,在这种情况下,经验往往起到主要作用。对于可调节流量的氧化鼓风机,当增大氧化风机入口风门开度,风机电流并不随之升高或升高程度偏低,而风机出口风压下降,则有可能是风机入口空气滤网被飞尘堵塞,应及时更换滤网以保证氧化空气流量。反应罐液位和浆液浓度舍影响风机出口风压,但当风机出口风压不正常的增大,同样,当增大风机入口风门开度,电机电流增大不明显时,有可能雾化空气喷嘴部分被堵塞,这种情况对于固定管网式氧化装置尤其易于发生,严重时甚至造成风机疏通喷嘴。
前面已提到,在低pH值下运行有利提高氧化率。因此,在确保脱硫率的前提下应尽量降低运行pH值,避免高pH值运行。
四、对水力旋流分离器的管理
对于水力旋流站,需要运行人员操作的工作不多,除了调整旋流站投入运行的旋流子个数外,还要注意监视旋流器入口浆液压力,当压力下降或波动较大时会影响分离效果。压力波动往往是供浆泵造成的,例如浆泵叶轮磨损、吸入较多的氧化空气气泡、管道部分堵塞等。定期测定底流和溢流浆液的浓度也是检查分离效果的手段。
五、运行pH值的控制
运行pH对石膏纯度有最明显、最直接的影响。当入口烟气条件不变时,降低运行pH值即可降低浆液中过剩CaCO3含量,有利提高石膏纯度,但将以损失脱硫率作代价。过分降低pH值可能对石膏质量产生负面影响,过低pH值将增加浆
液中有害离子浓度,有可能造成“封闭”石灰石活性。因此,一般运行pH值不宜低于5.0。提高pH值,脱硫效率增大,石膏纯度下降。当pH值超过5.7后不仅脱硫效率提高不多,未反应石灰石浓度却增加较多,石膏纯度将明显下降。因此,运行人员合理设定pH值是提高石膏质量的重要保证。
六、反应罐浆液含固浓度的控制
反应罐浆液含固浓度是FGD装置运行控制的重要参数之一。当浆液pH值和固体物浓度一定时,浆液固体物中CaSO3与CaSO4 ·2H2O有一定的质量比,此时生产出来的石膏纯度相对稳定。当浆液浓度下降时,比值增大,石膏副产品中的CaCO3含量将增大。相反,提高浆液固体物浓度则有利提高石膏副产品的质量,但是,在实际运行中通常并不以提高浆液浓度作为提高石膏副产品质量的手段,保持浆液浓度的稳定将有助于稳定石膏副产品质量。
七、运行控制方式对石膏副产品质量的影响
对于FGD系统脱硫效率,通常有三种运行控制方式,采用不同的运行控制方式对石膏纯度的影响不同。图17163示意地表示了三种控制方式时浆液中CaCO3浓度、pH值、脱硫效率以及石膏纯度的变化情况。图中的实线代表恒定控制浆液中CaCO3浓度的运行方式,当FGD装置入口SO2浓度下降时(上升时的情况,读者可以类推)始终维持反应罐浆液中
CaCO3浓度不变[见图17163(a)中的实线]。维持Ca-
CO3浓度恒定的方法是通过调节回路自动设定脱硫效率,使之随入口SO2的下降略高于设计点的脱硫效率[见图1716 3(c)],这是一种按预定程序自动调节的运行方式,这种运行控制方式可以获得居中的脱硫性能,稳定而不低于保证值的石
膏纯度[见图17163(d)]。

图17163 运行控制方式对石膏纯度的影响示意图


恒定控制CaCO3浓度运行方式恒定控制pH值运行方式

恒定控制脱硫效率运行方式
图17163中的虚线表示恒定pH值控制的运行方式,即当入口SO2浓度在设计值范围以内时,pH值取定值运行
方式[见图17163(c)],在这种运行方式下,脱硫率为定值,根据入口SO2浓度和脱硫率自动设定出口SO2浓度设定值,pH值将随入口SO2浓度的下降而下降[见图17
[见图17163(b)],这样随着入口SO2浓度的下降,脱
硫率上升[见图17163(c)],这种运行方式可获得较高的脱硫效率。浆液中CaCO3浓度亦随入口SO2浓度的下降后
16 3(b)],浆液中CaCO3浓度也随pH值下降而下降[见图
17163(a)]。因此,可以获得三种运行方式中最高石膏
上升[见图17163(a)],石膏纯度则下降[见图17 16 3(d)]。
纯度[见图17163(d)]。
图17163中的点划线代表自动控制恒定脱硫率运行
FGD系统实际上采用何种运行控制方式,取决于供应商的设计。第一、第二种方式只要设置合理都能保证石膏纯度不
低于保证值。当操作人员用手动控制方式运行时,则是采取第二种控制运行方式,即只要脱硫率不低于规定值则以固定pH值运行。在这种情况下,当入口SO2浓度变化时,石膏纯度难以得到保证。从提高石膏质量的角度来说,应采用第三种控制运行方式,即恒定脱硫效率控制方式,随着FCO装置入口SO2的下降,石膏纯度提高。
第十七节 脱硫废水处理不达标问题
点,国内学者对此难点的研究明显落后于国外同行。日本火电厂一般采用专用的吸附剂或专用树脂来吸附脱硫废水中的COD,吸附剂或树脂能够再生循环利用,反复进行吸附处理。处理脱硫废水中COD的另外一种方法是酸解,即向脱硫废水中加入无机酸,在酸性条件下加热废水,使其中的连二硫酸、氮硫化合物分解,这种方法已在日本得到应用。日本还研究开发出一种能选择吸附氟离子的吸附剂,并正在研究将其应用于脱硫废水处理。
脱硫装置产生的废水来自石膏旋流站溢流液,经废水旋流站由废水泵送至废水处理系统。在典型的废水处理系统中,废水经加入石灰浆控制pH值范围进行碱化处理,部分重金属以氢氧化物的形式沉淀出来;通过加入有机硫化物,使某些重金属如镉、汞等沉淀出来;通过添加絮凝剂及助凝剂,使固体沉淀物以更易沉降的大粒子絮凝物形式絮凝出来,在澄清浓缩器中将固形物从废水中分离后脱水外运,合格的澄清液外排或回用。在实际运行过程中,澄清液中的一些排放指标达不到设计要求,例如COD、F-以及部分重金属等。
脱硫废水中的氟化物主要来源于煤燃烧后产生的HF,其含量与煤质关系很大。一般采用直接加入石灰的方法对氟离子进行处理,即在调节废水pH值时选用石灰作为碱化剂进行除氟处理。同时,由于脱硫废水含有一定量的镁、铁、铝等金属离子,在碱性条件下生成氢氧化物沉淀。因此,当采用石灰进行碱化处理时,通过以下3个方面将氟离子除去:Ca(OH)2与F-直接反应生成CaF2而沉淀下来;Mg(OH)2絮凝物吸
附F-;氟化物与Al(OH)3、Fe(OH)3沉淀物共沉淀。上述
的反应对pH值有很高的要求,但在实际运行过程中,因各种原因使pH值与设定值的偏差往往过大,造成F-的去除效果不佳而超标,同样使部分重金属的排放不合格。
在脱硫废水中,形成COD的因素不是有机物,而是还原态的无机离子,一般通过氧化降低其含量。氧化剂通常采用空气,系统曝气在废水箱中完成,曝气时间为6~8h,气水比为2∶1。实践表明,脱硫废水经曝气处理后,COD去除率只能达到8%~10%,因此COD经常超标。这源于我国对脱硫废水中的COD处理研究还不够,脱硫废水的COD处理工艺与通常的COD处理工艺不一致,并成为脱硫废水处理中的一个难
另外对脱硫废水的水质进行分析时,人们往往会忽略对其中的氨氮化合物的分析。脱硫废水中的氨氮化合物也是煤燃烧后产生的,氨氮化合物含量也会超过GB8978—2002《污水综合排放标准》中规定的排放指标,需要经过处理后才能排放,但是目前国内还很少有人注意到此问题。